Ячеистые блоки автоклавного твердения: Блоки из ячеистого бетона автоклавного твердения (газобетонные, газосиликатные блоки), ГОСТ 31360-2007
Блоки из ячеистого бетона автоклавного твердения (газобетонные, газосиликатные блоки), ГОСТ 31360-2007
В настоящее время единственным стеновым материалом, который может в практике строительства использоваться без дополнительного утепления, является ячеистый бетон (еще его называют газобетон или газосиликат), представляющий собой уникальную систему, которая универсальным образом обладает основными преимуществами, отвечающими современным требованиям по физико-техническим и теплозащитным свойствам к строительным материалам.
Физико-технические свойства ячеистого бетона обусловлены его структурным строением. Ячеистый бетон следует рассматривать как сложно организованную систему, в которой могут быть выделены макроструктурный и микроструктурный уровни.
Основными физико-техническим свойствами ячеистого бетона являются: плотность, прочность, морозостойкость, огнестойкость, звукопоглощение, теплофизические свойства, обрабатываемость.
Подробно о газобетонных блоках можно ознакомиться в «Методических указаниях по применению изделий из автоклавного газобетона при проектировании и возведении ограждающих конструкций» (Разработаны Центром ячеистых бетонов и Межрегиональной Северо-Западной строительной палатой)
Мы предлагаем блоки из ячеистого бетона с оптимальным сочетанием цена — качество:
ЗАО ЛИСКИ-ГАЗОСИЛИКАТ. Производство газосиликатных блоков на немецкой линии Wehrnhahn (Верхан). Технические характеристики блоков, фото и цены. Cертификаты.
ЗАО ГРАС-Саратов. Производство газосиликатных блоков на немецкой линии Wehrnhahn (Верхан). Технические характеристики блоков, фото и цены. Сертификаты.
ЗАО Клинцовский силикатный завод. Производство газосиликатных блоков на польской линии Solbet (Солбет). Технические характеристики блоков, фото и цены. Сертификаты.
ООО «ЭКО-Золопродукт Рязань». Производство газосиликатных блоков на немецкой линии Wehrnhahn (Верхан). Технические характеристики блоков, фото и цены. Сертификаты.
ОАО «Бонолит — Строительные решения». Производство газобетонных блоков на голландской линии HESS (Хесс). Технические характеристики, фото и цены. Сертификаты.
ООО «Газобетон» г.Иваново. Производство газосиликатных блоков на немецкой линии WKB Systems GmbH. Технические характеристики блоков, фото и цены.
Блоки из ячеистого бетона автоклавного твердения: состав, производство
Для постройки современных теплых строений используются блоки из ячеистого бетона автоклавного твердения, другое название — газобетон или газосиликат. Это универсальное средство, которое вобрало в себя положительные качества различных строительных материалов. Благодаря этим качествам, он применяется при строительстве разных объектов и конструкций, чем снискал большую популярность как среди строительных организаций, так и среди владельцев новостроек.
Состав блоков
Ячеистая структура газобетона обусловлена его составом смеси, из которой он изготовлен: кварцевый песок — 60%, цемент — 20%, известь — 20%, вода. Алюминиевая паста, добавленная в этот вязкий раствор, вызывает вспенивание, а возникшие воздушные пузыри равномерно образуют ячейки по всему объему материала. При добавлении негашеной извести в результате взаимодействия с алюминиевыми частицами образуется водород — так получают газосиликат.
Разновидности
Стеновые блоки из газобетона классифицируются по разным признакам:
- определенный показатель;
- сфера применения;
- особенность состава;
- способ производства.
Разновидности ячеистых автоклавных блоков
Признак классификации | Виды |
Вяжущий компонент | Шлаковые |
Цементные | |
Известковые | |
Зольные | |
Смешанные | |
Вид кремнеземистого компонента | Из кварцевого песка |
С добавлением вторичных продуктов промышленности | |
Сфера применения | Теплоизоляционные (плотность 400 кг/м3) |
Конструкционные (плотность 700 кг/м3) | |
Смешанные (плотность 500—600 кг/м3) | |
Прочность блока | D350 |
D400 | |
D500 | |
D600 | |
Объемная масса | Тяжелые |
Легкие | |
Средние |
Производство автоклавного бетона
Производство автоклавного бетона в домашних условиях невозможно: его делают на промышленной основе в специальном оборудовании.
Производство ячеистого бетона происходит только на промышленной основе на заводских мощностях при значительных финансовых вложениях в оборудование. Изготовить его в домашних условиях невозможно. Поэтому результатом работы такого предприятия будет продукция высокого качества и соответствие параметрам сертификации по ГОСТ 31359–2007.
Производственная линия включает в себя такое оборудование:
- дозатор для распределения компонентов;
- смеситель бетона;
- формы для блоков;
- склады;
- водяной дозатор;
- комплекс для резки;
- автоклав.
Технология заключается в отливке материала в специальных емкостях. Сухую смесь загружают в бетономешалку, где ее перемешивают. Для реакции взаимодействия нужно 5 мин., после чего в сырье добавляют воду и алюминиевую пудру. Все это перемещают в другие сосуды. Формы наполняются раствором наполовину, так как он при застывании увеличивается в объеме. Для ускорения процессов схватывания и затвердения, используют подогретую до +40 С воду. После распределения массы в формы ее оставляют для застывания.
Для придачи строительному материалу уникальных качеств, его после застывания отправляют в специальную автоклавную печь. Там разогревают воздух до +190 С и создают избыточное давление. В таких экстремальных условиях возникает активное газовыделении, кроме того, образуется другое минеральное вещество с особыми характеристиками.
Новый материал очень прочный — через 12 часов после пребывания в автоклаве газобетон выдерживает давление до 5 МПа.
Где применяют?
Благодаря сравнительно небольшому весу и прочности, строительный материал применяется в зонах с сейсмической активностью.Автоклавный газобетон используется при изготовлении армированных плит перекрытия, несущих стен, межкомнатных перегородок, в качестве средства теплоизоляции здания. В районах с повышенной сейсмической активностью этот материал применяется в строительстве — ячеистая, пористая структура обеспечивает устойчивость для сооружений. Сравнительно малый вес и высокая прочность снижают нагрузки, которые испытывают строения под воздействием землетрясения.
Газобетонный материал поддается дополнительной обработке — его можно распилить, при подгонке элементов его строгают, в него с легкостью забиваются гвозди или монтажные скобы. При использовании таких блоков нужно знать, что со временем они становятся более тверже. Благодаря высокому уровню кристаллизации, сооружения из автоклавного бетона дают малую усадку. Срок использования газосиликата — более 100 лет.
Плюсы и минусы
К положительным качествам материала относят:
- Экологическая чистота. Бетон нетоксичен и безопасен.
- Пожаробезопасность. Материал не горит, с него делают огнеупорные перегородки.
- При больших размерах строительные элементы имеют небольшой вес. Они легко перемещаются, дополнительно обрабатываются, шлифуются, строгаются, поэтому ускоряется строительство объектов.
- Твердость и низкая плотность блоков. Такая способность позволяет строить 3-х этажные с допустимыми техническими характеристиками.
- Паропропускаемость материала. Обеспечивает высокий уровень комфортности помещений.
- Теплоизоляционные свойства. Позволяют обеспечить экономию тепловой энергии, кроме того, можно не проводить теплоизоляцию дома.
- Ячеистые блоки представлены в продаже в широкой номенклатуре. Поэтому будущим домовладельцам легко выбрать с такими стройматериалами нужные параметры усадьбы — толщину стен, уровень теплоизоляции.
- Высокая морозостойкость вещества по сравнению с другими материалами. Показатель характеризуется количеством пройденных циклов заморозки и оттаивания, для таких блоков он колеблется в пределах 35—150.
- Антибактериальные свойства. Конструкции не подвержены заражению плесенью, грибком.
- Идеальная геометрия. Благодаря особым условиям производственного процесса блоки изготовлены с особой точностью при минимальных отклонениях.
К отрицательным характеристикам автоклавного бетона относится высокое влагопоглощение. Водяные пары, проникая в ячеистую структуру вещества, кристаллизируются под воздействием низких температур. разрушая материал. Также блоки хрупкие — они колются, ломаются, их трудно транспортировать. Для крепления блоков необходимо использовать специальный анкер — «бабочку».
Ячеистый бетон автоклавного твердения, автоклавный газобетон: что это такое
Ячеистый бетон автоклавного твердения качественный материал имеется массу положительных характеристик, среди которых надежность, достаточная прочность. Благодаря этому данное сырье можно использовать даже для возведения высоких зданий плюс задействовать его в перегородках. В этой статье предлагаем разобраться, что такое автоклавный бетон и с его техническими характеристиками, а также с его возможными видами.
Что представляет собой стройматериал
Материал выпускается в виде объемных фрагментов, которые могут отличаться размером в зависимости от партии. Является материалом, который служит годами без намека на деформацию. Это говорит о том, что качество этого состава проверено временем. С помощью блоков, произведенных по технологии твердения в автоклаве, удается даже сконструировать несущие перегородки.
Газобетонные блоки: плюсы и минусы, сравнение с аналогами
Нужно отметить несколько основных преимуществ материала, которые повлияют на выбор сырья для проведения строительства. Положительными качествами считают:
- Звукоизоляция. Структура, с которой изготавливается данный вид бетона, является отличным средством для удержания звука, как внутри помещения, так и снаружи;
- Пожаробезопасность. Пористость материала помогает остановить воспламенение, предупредить его распространение в другие комнаты;
- Теплоизоляция. Воздух, присутствующий в порах материала играет роль неплохого изолятора, за счет этого температура внутри комнаты всегда будет оптимальной для проживания.
- Экономичность. Материал обходится несколько дешевле, чем камень, соответственно на стройке можно эффективно сэкономить.
- Точные размеры. Несмотря на пористость структуры, блоки имеют идеально ровную поверхность и правильные геометрические формы. Это облегчает дальнейший процесс отделки стен.
- Скорость строительства. Ячеистые блоки очень быстро монтируются, так как их не требуется подгонять.
- Элементарность обработки. При необходимости фрагментировать блоки на части, достаточно использовать обычную ножовку.
Однако это сырье не лишено и недостатков:
- возможность растрескивания;
- высокая степень водопоглащения, именно поэтому обязательно устройство вентиляционных зазоров в таких стенах.
Для строительства сооружений из таких конструкций необходимо применение крепежа-бабочки.
Особенности технологии
Автоклавное твердение — это манипуляция, которая представляет собой конструкцию, состоящую из нескольких компонентов: основы и добавки. Последние выбираются индивидуально в зависимости от того, для какой цели изготавливается материал.Благодаря такому подходу производства строительного материала можно достичь идеального качества, который будет в дальнейшем соответствовать выбранным условиям эксплуатации. Весь процесс формирования блоков происходит под высоким давлением и температурой. Процесс твердения выполняется в течение нескольких часов. Эксперты утверждают, что не обязательно доводить затвердение до максимума. Достаточно всего 70% показателя прочности, после чего можно остановить процесс. Когда материал остынет, он не разрушится и будет соответствовать всем нормативам. В таком виде его и выставляют на продажу.
Какие бывают виды блоков
- Легкий. Такой вариант автоклавного бетона имеет минимальную плотность. Она может варьироваться в пределах от 300 до 1200 кг/метр кубический. Подобное значение получается только, если в составе будут присутствовать многочисленные пузырьки. Минусами этого сырья является то, что он не обладает высокими показателями прочности, соответственно это ограничивает его возможности и сферу использования.
- Ячеистый. Его плотность составляет 1200-1800 килограмм на кубический метр. Такие блоки идеальны для строительства несущих стен, если это малоэтажный частный дом.
Если возводится многоэтажное здание, то такие блоки применяются только в качестве составляющего для ограждающих перегородок.
- Тяжелые. Плотность такого составляет 1800 кг/куб.метр и выше. В этом случае класс сжатия на прочность получает соответствие B7,5-B 35. Показатель варьируется в зависимости от состава и выдержки сырья в автоклаве.
Как правильно армировать бетонную плиту для перекрытия
Показатели прочности устройства зависят строго от того, какая плотность получается у строительного материала на исходе.
Блоки с ячеистой структурой автоклавного твердения для строительства жилого домаИсточник ares-nn-cs2347798.tiu.ruРазновидности бетона со структурой ячейки
Помимо основных видов бетонов, которые производят путем автоклавного твердения, есть еще и дополнительные классификации. К ним относят следующие два вида.
Газосиликат

Когда смесь полностью готова, ее отправляют в специальную форму, в ней уже и происходит процесс твердения в паре с химической реакцией, в результате которой внутри и образуются поры.
Газосиликатный блок автоклавного тверденияИсточник avito.ruГазобетон
Газобетон автоклавного твердения представляет собой ячеистый искусственный камень, в котором по всему объему поры равномерно распределены. Такой бетон производится в промышленных цехах и не содержит в себе никаких добавок, которые могли бы навредить человеческому здоровью в ходе эксплуатации материала.
В состав этого вида блоков входит песок, цемент, известь, вода, гипс, алюминиевая паста. Поры образуются в результате происхождения реакции выделения водорода. Только после того, как прошло затвердение готовый материал делят на блоки нужного размера. Все эти фрагменты имеют идеальную форму и размеры, соответственно в процессе укладки не потребуется выполнять соответствующие подгоны. Также все блоки ложатся максимально ровно, в результате чего не образуются зазоры в швах.
Что собой представляет ячеистый бетон и какие у него технические характеристики
Область применения автоклавных блоков
Автоклавные блоки с пористой структурой могут применяться в различных условиях. Прежде всего за счет присутствия данного типа материала в строительном деле, удается сформировать армированные плиты для бетонных перекрытий, играющих роль перегородок или несущих конструкций.
Газобетонные блоки автоклавного твердения с повышенными свойствами прочности зачастую укладывают в сейсмичной зоне, также используют и в регионах, где часто происходят природные катаклизмы. Также перегородки из этого материала стараются выполнять при необходимости выстроить теплое здание, так как он имеет повышенную теплоизоляцию.
Также данный материал применяют в условиях строительства, где его нужно правильно и оперативно обработать. Например, если требуется подрезать, выровнять, отшлифовать грани, просверлить.
Что касается такой разновидности сырья, как газосиликатный блок — то его в основном используют при строительстве зданий, которые должны прослужить не один десяток лет. Обязательно это сырье требуют для работы там, где совсем не нужна большая нагрузка на фундамент (особенно это касается мест с плавающими грунтами).
Стройка из газобетонных блоков с ячеистой структуройИсточник beton-house.comЧем отличается автоклавный бетон от неавтоклавного
В этом разделе предлагаем разобрать главные характеристики автоклавного бетона и для того, чтобы было наглядно понятно, почему его чаще используют, прилагаем таблицу со сравнительными характеристиками блоков неавтоклавного твердения.
Изначально отмечают стабильно высокое качество газобетона автоклавного твердения и процесс усадки в ходе эксплуатации. Усадка происходит только при испарении лишней влаги, которая содержится в материале. В среднем автоклавные бетонные блоки усаживаются на 0,5 м/мм в течение пяти-десяти лет и это совсем немного в отличие от неавтоклавного: 2-3 мм/м.
Рассмотрим сравнение технических характеристик двух разных блоков в таблице ниже.
Характеристики | Автоклавный бетон | Неавтоклавный бетон |
Класс морозостойкости | F15 0 | F15-F30 |
Плотность, кг/м3 | D400-D700 | D600-D800 |
Теплопроводность, Вт/мС | 0.15 | 0.![]() |
Класс горючести | НГ | НГ |
Прочность | B 2.5-B-5 | В 1.5-В 2.5 |
Долговечность | 150 лет | 50 лет |
Если смотреть по совокупности всех перечисленных характеристик, то можно сделать вывод, что идеальный вариант для строительства жилых зданий — блоки, произведенные с применением технологии автоклавного твердения. В случае, если необходимо выполнить строительство гаража, погреба, ангара или склада, то тогда идеальным будет блок неавтоклавного типа.
Кладка ячеистых блоков автоклавного тверденияИсточник blokshop.ruКаким производителям нужно отдавать предпочтение
Поставщиков, которые изготавливают автоклавный пористый бетон на территории страны большое количество. Но только три из них поставляют действительно качественный продукт и это компании:
- Аэрок;
- Бонолит;
- АэроСтоун.
Что такое железобетон: характеристики и виды
Аэрок является первым и достаточно крупным производителем. Их объем поставок составляет 400 тысяч м3 за последний год. Известно, что еще в 2005 году эта компания ввела в оборот блоки, прочность которых составляет B-2.5, а они стали в дальнейшем стандартом в сфере территорий малоэтажными зданиями. Преимущество покупки блоков именно у этого производителя заключается в том, что он предоставляет блоки всех необходимых типоразмеров, которые только могут использоваться в строительстве.
Как выбрать ячеистый бетон? Обзор.
Заключение
Автоклавные бетонные блоки хоть и обладают не столь высокой плотностью, как неавтоклавные, они все-таки являются более востребованными для создания комфортных жилищных условий. Единственно, что нужно учитывать — покупка у проверенного производителя.
Показатель | Значение показателя для марки по средней плотности | |||
D400 | D500 | D600 | D700 | |
Средняя плотность в сухом состоянии, кг/м3 | 376-425 | 476-525 | 576-625 | 676-725 |
Класс бетона по прочности на сжатие | B2,0 B2,5 | B2,5 B3,5 | B2,5 B3,5 | B3,5 B5,0 |
Прочность на сжатие, МПа, не менее | 2,16 | 2,70 3,78 | 2,70 3,78 | 3,78 5,40 |
Марка по морозостойкости | F100 | F100 | F100 | F100 |
Коэффициент теплопроводности, Вт/(м*С) | 0,10 | 0,12 | 0,14 | 0,18 |
Индекс изоляции воздушного шума стены толщиной 250 мм, дБ | 43 | 44 | 45 | 46 |
Коэффициент паропроницаемости, мг/м*ч*Па, не менее | 0,23 | 0,20 | 0,16 | 0,15 |
Усадка, мм/м, не более | 0,5 | 0,5 | 0,5 | 0,5 |
Отпускная влажность, % по массе, не более | 25 | 25 | 25 | 25 |
Средний вес при отпускной влажности 25%, кг/м3 | 470-530 | 595-655 | 720-780 | 845-905 |
Удельная активность естественных радионуклидов, Бк/кг, не более | 370 | 370 | 370 | 370 |
Предельные отклонения от размеров, мм — по высоте: — по ширине: — по длине: | ± 0,5 | ± 0,5 | ± 0,5 | ± 0,5 |
Показатель | Значение показателя для марки по средней плотности | |||
D500 | ||||
Средняя плотность в сухом состоянии, кг/м3 | 476-525 | |||
Класс бетона по прочности на сжатие | B2,0 | |||
Прочность на сжатие, МПа, не менее | 2,10 | |||
Марка по морозостойкости | F35 | |||
Коэффициент теплопроводности, Вт/(м*С) | 0,12 | |||
Индекс изоляции воздушного шума стены толщиной 250 мм, дБ | 44 | |||
Коэффициент паропроницаемости, мг/м*ч*Па, не менее | 0,20 | |||
Усадка, мм/м, не более | 0,5 | |||
Отпускная влажность, % по массе, не более | 25 | |||
Средний вес при отпускной влажности 25%, кг/м3 | 595-655 | |||
Удельная активность естественных радионуклидов, Бк/кг, не более | 370 | |||
Предельные отклонения от размеров, мм — по высоте: — по ширине: — по длине: | ± 1,0 |
ЯЧЕИСТЫЙ БЕТОН И ПЕНОБЕТОН.
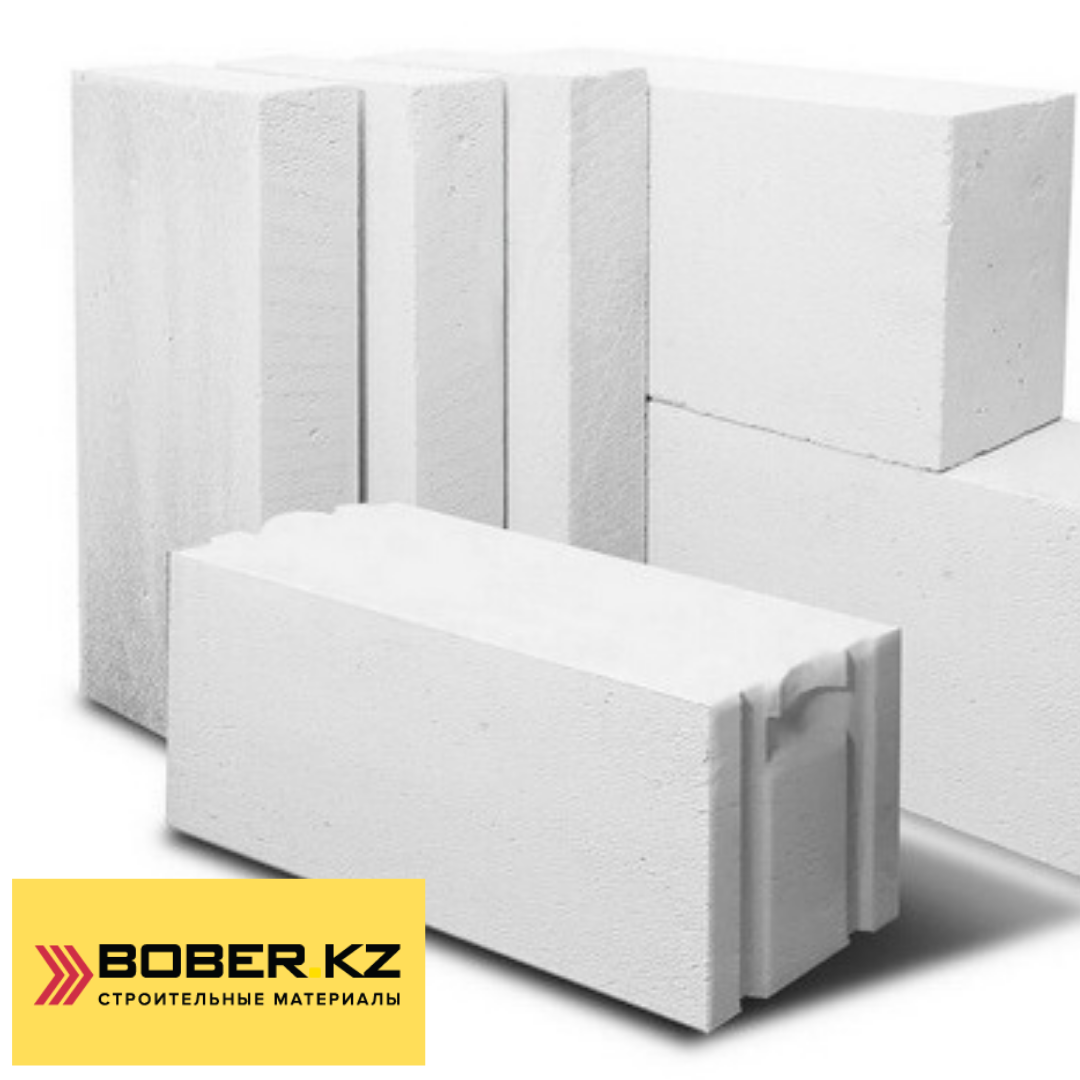
ЯЧЕИСТЫЙ БЕТОН И ПЕНОБЕТОН. СХОДСТВО И РАЗЛИЧИЕ В Лаборатории строительных материалов и конструкций ГБУ «ЦЭИИС» значительную часть испытаний проводят на стеновых блоках из пенобетона и ячеистого бетона, отобранных на строительных объектах г. Москвы. На первый взгляд это идентичные строительные материалы – блоки прямоугольной формы, подразделяются на стеновые и перегородочные. Отличаются размерами (разная ширина, а длина и высота, как правило, одинаковые). Оба вида блоков обладают пористой структурой, понижающей их плотность и массу, достаточной прочностью, низкой теплопроводностью. Однако, есть и различия, формирующие отличительные свойства, которые и являются камнем преткновения между сторонниками и противниками этих материалов. Пеноблоки (фото 1 и 2) используются при устройстве: • несущих стен зданий и сооружений; • внутренних стен для планировки помещений; • заборов, ограждений территорий; • перекрытий с армированием стальным прутом.
Фото 1. Стандартный пеноблок (классический, простой).
Фото 2. Перегородочный пеноблок.
Блоки из ячеистого бетона (фото 3 и 4) в основном применяют для:
· межкомнатных перегородок;
· заполнения пролетов в каркасных зданиях;
· несущих конструкций и стен;
· многоэтажных конструкций и зданий.
Фото 3. Стандартный ячеистый блок.
Фото 4. Кладка из ячеистых блоков.
Чтобы понять, чем отличаются ячеистые бетоны от пенобетонов, нужно разобраться в технологиях, по которым изготавливаются эти строительные материалы.
Пенобетон производится по упрощенной технологии в виде отдельных блоков. В связи с этим разновидность его типоразмеров и видов ограничена. Компонентами для производства являются: цемент, вода, песок, шлак и другие наполнители. Основное вещество, обеспечивающее пористость структуры материала – сульфитный щелок. Пенообразующие добавки и фибра для повышения прочности не превышают 1%. Пенобетон может изготавливаться на небольших предприятиях (мини-заводы, установки, кустарное, частное производство).
Ячеистый бетон изготавливается на промышленных предприятиях со специальным оборудованием. В качестве основных компонентов используются цемент, кварцевый песок и известь, вода. Вспенивающий компонент – алюминиевая паста. Состав схож с тем, что используется для приготовления пенобетона.
Отличие свойств пенобетона от ячеистого бетона объясняется их структурой и видом.
Пористую структуру (фото 5) легко увидеть во время визуального осмотра. Кроме того, изделия имеют разный цвет. Ячеистый бетон (газонаполненный композит), содержащий известь, имеет белый цвет, а пенобетонные блоки – серый.
а) пенобетон б) ячеистый бетон
Фото 5. Структура пор.
Поры ячеистого бетона, сформированные в результате химической реакции алюминиевого порошка, равномерно распределены по объему, имеют открытую форму. Газонаполненный стройматериал, аналогично губке, интенсивно поглощает влагу. Ячеистые блоки впитывают до 50% жидкости с соответствующим увеличением массы. Повышенная гигроскопичность значительно снижает теплоизоляционные свойства, является причиной растрескивания незащищенных блоков при их замерзании.
Пенобетонные изделия отличаются замкнутой формой воздушных пор, которые занимают до 80% общего объема. Воздушные полости диаметром 4–5 мм неравномерно расположены в пенобетонном массиве, что вызвано особенностями распределения пенообразователя. Это снижает прочность материала. Однако замкнутая конфигурация ячеек способствует устойчивости пенобетонного массива к впитыванию влаги. Убедиться в гидрофобных свойствах пенобетонных блоков несложно — материал, погруженный в воду, не тонет (Фото 6).
Фото 6. Блоки из пенобетона и ячеистого бетона в воде.
Если сравнивать физико-технические показатели обеих бетонов, представленных ниже в таблице, то ячеистый бетон имеет лучшие показатели, допускающие его применение для постройки различных зданий и сооружений, в том числе, многоэтажных.
Таблица
Показатели |
Ячеистый бетон |
Пенобетон |
Коэффициент теплопроводности , Вт/ (м•⁰С) |
0,10 – 0,14 |
0,09 – 0,38 |
Объёмный вес (плотность), кг/мᵌ |
400 — 800 |
400 — 1200 |
Марка по плотности |
D350, D400…800 |
D400…800,D1000…1200 |
Класс прочности бетона на сжатие |
В 2,5 при D500 |
В 2,5 при D700 |
Пароприницаемость, мг/мчПа |
0,2 |
0,2 |
Водопоглощение, % от массы |
20 — 25 |
10 — 16 |
Морозостойкость не менее |
50 циклов |
25 циклов |
Кладка, толщина кладочного шва, мм |
Только на клей/2-3 мм |
На клей, раствор/10 мм |
Средняя усадка готовой кладки, мм/м |
0,3 |
2 — 3 |
Средняя толщина однослойной стены, м |
0,4 |
0,63 |
Звукоизоляция |
хуже |
лучше |
Структура пор |
закрытая |
открытая |
Внешний вид |
лучше |
хуже |
Существуют и другие различия технических характеристик:
§ У ячеистого бетона более стабильные показатели теплопроводности, поскольку он имеет равномерную ячеистую структуру. Поры в пенобетоне имеют диаметр 1-3 мм, распределяются они неравномерно, поэтому теплопроводность этого материала нестабильна.
§ Прочность у обработанного ячеистого бетона существенно выше, чем у пенобетона.
§ Промышленное производство позволяет получить ячеистые бетонные блоки с точной геометрией, а изготовленные частным образом пенобетонные блоки такими свойствами не обладают.
§ Штукатурка ложится на оба материала, но правильная геометрия ячеистых бетонных элементов позволяет сэкономить. Также ячеистый бетон обладает лучшей адгезией.
§ У ячеистого бетона лучше морозостойкость, как у автоклавного или термообработанного бетона. Этот показатель у пенобетона достигает 35 циклов заморозки и размораживания, а ячеистый бетон с гидрофобными наполнителями выдерживают до 75 циклов.
Среди плюсов пенобетона отмечают:
· Относительно низкую теплопроводность.
· Сравнительно малую плотность, что позволяет сэкономить на фундаменте, выкладывать стены самостоятельно.
· Высокие показатели звукоизоляции.
· Оптимальный размер блоков и других конструктивных элементов ускоряют строительство.
· Простота подгонки элементов при помощи простой ножовки.
· Экологичность допускает применение для строительства любых жилых помещений.
· Длительная эксплуатация даже в сложных условиях, коррозионная устойчивость.
Но этот материал имеет и недостатки:
— Пористость структуры придает хрупкость, особенно на краях конструкций прочность пенобетона нестабильна.
— Непривлекательная внешняя поверхность, которую лучше оштукатурить.
— При возведении конструкций из пенобетона необходимо армирование на стыках элементов.
— При кустарном производстве качество материала снижается.
— Использование этого материала требует проведения тщательных расчетов прочности конструкции.
— У пеноблоков нет правильной геометрии, поскольку они не производятся в промышленных условиях.
К достоинствам ячеистого бетона относят следующие характеристики:
· Сниженная плотность при повышенной прочности.
· Повышенная влагостойкость автоклавного блока.
· Огнестойкость.
· Морозоустойчивость.
· Устойчивость к биологическим воздействиям и коррозии.
· Долговечность позволяет эксплуатировать здания более 100 лет.
· Отличные показатели тепло- и звукоизоляции.
· Легкость обработки.
· Экономия, поскольку на газобетон требуется минимальный объем цемента.
· Экологическая безопасность.
· Правильная геометрия, поскольку конструктивные элементы изготавливаются на производстве.
При всех достоинствах материала, у него также есть недостатки:
— Повышенная гигроскопичность требует дополнительного оштукатуривания.
— Требуется аккуратность при расчетах нагрузок, поскольку блоки могут дать трещины.
— Стоимость этого материала выше, чем пенобетона.
Таким образом, строительные материалы из ячеистого и пенобетона имеют много общего, но есть отличия, не позволяющие применять их одинаково. Очевидно, что блоки из ячеистого бетона имеют лучшие показатели прочности, по другим характеристикам они схожи. Поэтому учитываются конкретные расчеты, особенности и бюджет работ, в результате чего принимается решение.
Использованная литература:
1. СП 15.13330.2012 «Каменные и армокаменные конструкции».
2. ГОСТ 6133-99 «Камни бетонные стеновые. Технические условия».
3. ГОСТ 25485-2019 «Бетоны ячеистые. Технические условия»
4. ГОСТ 31360-2007 « Изделия стеновые неармированные из ячеистого бетона автоклавного твердения. Технические условия»
5. ГОСТ 5742-76 «Изделия из ячеистых бетонов теплоизоляционные».
6. Материалы сайта https://pobetony.expert/bloki-i-perekrytiya/penoblok-ili-gazoblok
Статью подготовила ведущий инженер лаборатории Измайлова Е.В.
(PDF) ИССЛЕДОВАНИЕ СВОЙСТВ СОТОВЫХ ЗАЗОРОВ НА СДВИГ-СЖАТИЕ ПРИ АВТОКЛАВНОЙ ПЕРЕРАБОТКЕ
3.0. Было замечено, что сдвиговые свойства в направлении W были выше, чем в направлении L
. Кроме того, прочность на сдвиг и модуль снижались при повышении температуры испытаний.
С другой стороны, в то время как прочность на сдвиг в обоих направлениях снижалась при увеличении давления сжатия
, модуль сдвига не проявлял какой-либо особой тенденции при увеличении давления сжатия
. Более конкретно, для образцов, испытанных в направлении L, самые высокие характеристики сдвига
были получены при комнатной температуре и нормальном давлении 0 кПа (модуль сдвига 13,45 МПа
и предел прочности на сдвиг 568,8 кПа) для того же направления испытаний с самым низким сдвигом
Свойствабыли получены при 160 °C при нормальном давлении 345 кПа (модуль сдвига 4,46 МПа и прочность на сдвиг
239,2 кПа). Аналогичным образом, для образцов, испытанных вдоль направления W, самые высокие сдвиговые свойства
были получены при комнатной температуре и нормальном давлении 0 кПа (29.97 МПа
модуль сдвига и прочность на сдвиг 590,2 кПа) для того же направления испытания самые низкие характеристики сдвига
были получены при 160 °C при нормальном давлении 345 кПа (модуль сдвига 1,73 МПа и
289,6 кПа прочности на сдвиг). Вид разрушения для всех образцов был когезионным разрушением при сдвиге
сотового заполнителя, который является приемлемым видом отказа для этого испытания. Полученные свойства материала
можно использовать для определения подходящего давления отверждения и углов наклона сэндвич-панелей
, чтобы избежать разрушения сердцевины во время отверждения.
5. БЛАГОДАРНОСТИ
Авторы выражают благодарность за финансовую поддержку Национальной администрации по аэронавтике и исследованию космического пространства
(Грант № NNX11AM08A).
6. ЛИТЕРАТУРА
1. Yeh, H.-Y., S.V. Нгуен и Х.-Л. Да, анализы отказов сотовых сэндвич-панелей из композита с полимерной матрицей
(PMC). Журнал армированных пластмасс и композитов
, 2004. 23(9): с. 923-939.
2. Шарма Н., Р.Ф. Гибсон и Э.О. Айоринде, Усталость пенопласта и сотового заполнителя
Композитные сэндвич-конструкции: Учебное пособие. Журнал многослойных конструкций и материалов
, 2006. 8 (4): с. 263-319.
3. Сезгин Ф.Е. и др., Механические свойства сотового заполнителя на основе полипропилена
Композитные сэндвич-конструкции. Журнал армированных пластмасс и композитов, 2010.
29(10): с. 1569-1579 гг.
4. Чжан Г. и др. Механическое поведение многослойных конструкций из углепластика с тетраэдрическими
решетчатыми стержнями.Композиты Часть Б: Инженерия, 2012. 43(2): с. 471-476.
5. Xiong, J., et al., Механические характеристики сэндвич-колонн из углеродного волокна с трехмерными сотовыми заполнителями
при сжатии в плоскости. Композиты Часть Б:
Машиностроение, 2014. 60(0): с. 350-358.
6. Shen, S.Y., et al., Механические свойства сопротивления сэндвич-панелей FRP/полиол-изоцианатная пена
. Композитные конструкции, 2013. 99(0): с. 419-432.
7. Лю Дж. и др., Механическое поведение и механизмы разрушения сэндвич-панели из углеродного волокна
с пирамидальным сердечником после термического воздействия. Journal of Materials Science &
Technology, 2013. 29(9): с. 846-854.
8. Hachemane, B., et al., Исследование поведения сэндвич-композитов при ударе и вдавливании.
Композиты Часть Б: Машиностроение, 2013. 51(0): с. 1-10.
9. Hexcel. Атрибуты и свойства сот HexWeb™ Полное руководство по материалам, конфигурациям и механическим свойствам стандартных
сот Hexcel.1999
Сотовая технология | СпрингерЛинк
‘) var buybox = document.querySelector(«[data-id=id_»+ метка времени +»]»).parentNode ;[].slice.call(buybox.querySelectorAll(«.вариант-покупки»)).forEach(initCollapsibles) функция initCollapsibles(подписка, индекс) { var toggle = subscribe.querySelector(«.цена опциона на покупку») подписка.classList.remove(«расширенный») var form = подписка.querySelector(«.форма-варианта-покупки») если (форма) { вар formAction = form.

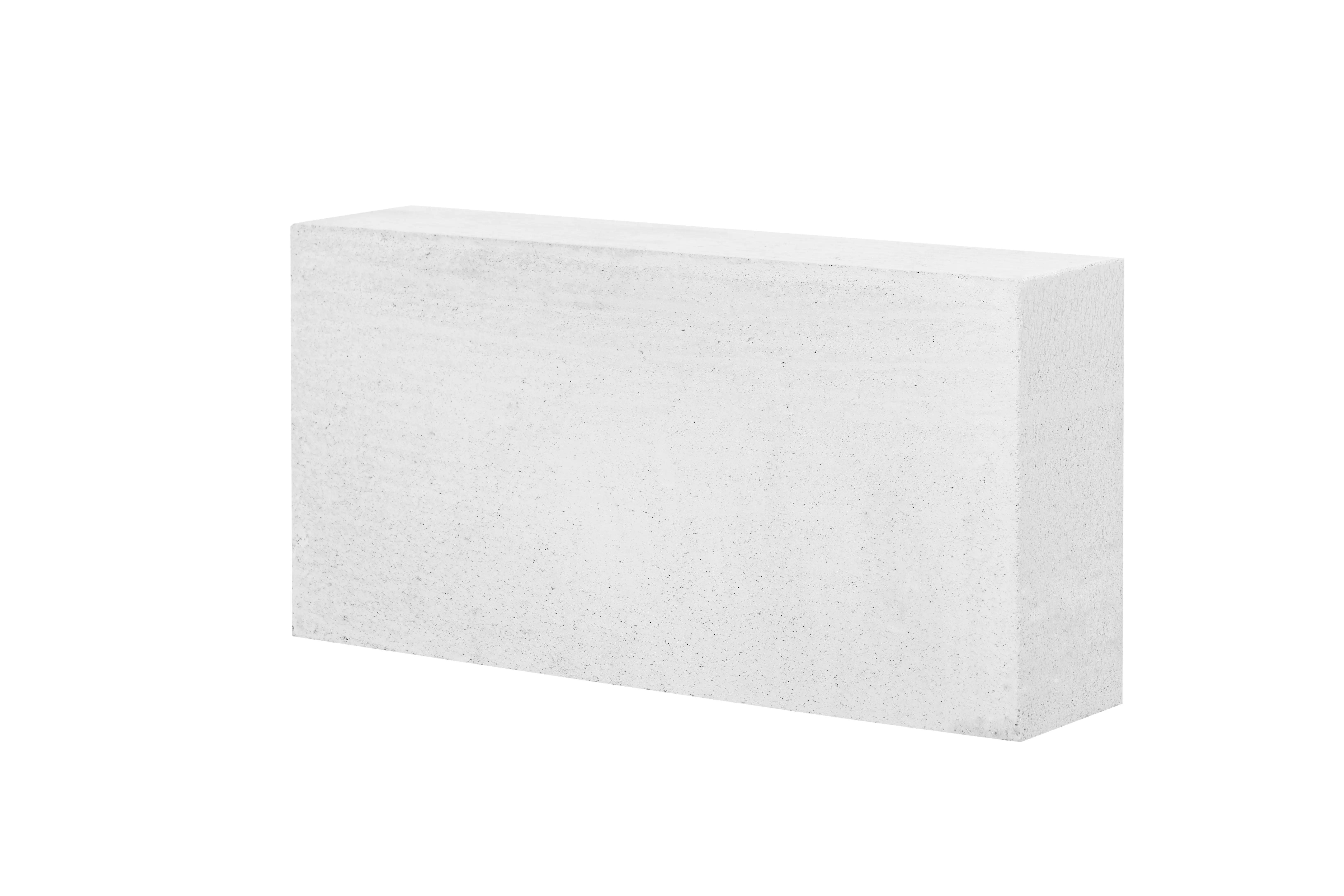


Автоклавные газобетонные блоки | Зурели
Блоки из автоклавного газобетона (AAC) — легкие и прочные строительные изделия. Блоки AAC, впервые концептуализированные и изобретенные шведским архитектором и изобретателем Йоханом Акселем Эрикссоном в 1924 году, особенно известны своими огнестойкими, тепло- и звуконепроницаемыми свойствами. Воздух, являющийся основным компонентом (почти 80-85% по объему), эти строительные изделия обычно легкие, их вес составляет всего треть от более распространенных кирпичей из красной глины.
Как они сделаны?
Общие ингредиенты, используемые в производстве газобетонных блоков, включают известь, цемент, песок, воду, гипс, летучую золу и оксид кальция (обычно известный как негашеная известь).Алюминиевый порошок вступает с ними в химическую реакцию, и к концу процедуры газообразный водород выделяется в воздух. Именно эта химическая реакция придает блокам AAC их отчетливую сотовую структуру, легкость и другие изоляционные свойства.
После необходимого формования и смешивания они подвергаются дальнейшему отверждению в автоклаве (при высокой температуре и давлении), что придает им желаемую прочность и долговечность.
Каковы преимущества использования блоков AAC?
Блоки AAC в среднем в 9 раз больше обычных глиняных кирпичей.Это приводит к превосходной скорости и качеству строительства в сочетании с огромным снижением затрат на штукатурку и раствор на стройплощадке. Важно отметить, что лучшая в своем классе теплоизоляция приводит к увеличению экономии затрат на отопление, вентиляцию и кондиционирование воздуха (HVAC).
Из-за высокой технологичности и гибкости материал AAC широко используется при строительстве жилых домов, медицинских учреждений, школ, гостиниц и других промышленных/коммерческих сооружений.
Сейсмостойкость
Силы землетрясения, воздействующие на конструкцию, пропорциональны весу здания, поэтому легкие блоки обладают отличной устойчивостью к силам землетрясения. В регионах с высокой сейсмической активностью, таких как Япония, используются исключительно блоки летучей золы AAC. Было доказано, что он выдерживает ветровые нагрузки тропических штормов категории 5.
Устойчивость к шумовому загрязнению
Легкие зольные блоки AAC с закрытыми воздушными карманами могут обеспечить очень хорошую звукоизоляцию / звукопоглощение с рейтингом STC (класс звукопередачи) 44.Его также можно использовать в качестве звукоизоляционной стены вдоль дорог с интенсивным движением. Стена AAC имеет превосходный класс звукопередачи (STC) 44. В результате получается практически звуконепроницаемый интерьер.
Водостойкий
Микроскопическая структура легкого блока не допускает капиллярного действия, что делает его непроницаемым для воды. Его гидроизоляционные свойства дополнительно улучшаются за счет добавления добавок на основе силикона.
Теплоизолированный
Самый высокий тепловой класс в отрасли R30!.Его ячеистая структура обеспечивает хорошую изоляцию внутренних помещений, не пропуская теплый воздух летом и холодный зимой. AAC снижает затраты на кондиционирование воздуха до 30%.
производители блоков aac в Махараштре
Высокая прочность
Процесс автоклавирования с паровым отверждением под высоким давлением обеспечивает блокам летучей золы AAC непревзойденное отношение прочности к весу, более высокое, чем даже у бетона M 150, и намного превышающее требования индийских строительных норм и правил.
Огнестойкий
Его уникальная ячеистая структура обеспечивает превосходную огнестойкость.Благодаря такой ячеистой структуре блоки AAC fly ask не разрушаются даже в огне. Это лучший в своем классе показатель огнестойкости 4 часа. температура плавления блоков летучей золы AAC составляет более 1600 градусов по Цельсию, что более чем в два раза превышает типичную температуру в здании 650 градусов по Цельсию.
Бетонный блок AAC
| Автоклавный газобетон
Что такое блок AAC? Блок из автоклавного газобетона (AAC) представляет собой сборный, легкий и изолирующий зеленый строительный продукт, используемый в качестве стенового материала и замены кирпича, блоков CLC и т. Д.Кроме того, благодаря прочной теплоизоляции, блоки AAC также используются в специальных приложениях, таких как брандмауэры, звуковые стены, черепица и т. Д. Блоки Magicrete AAC производят эти продукты на своем современном заводе с последними инновациями в соответствии с передовыми технологиями. в Сурате под торговой маркой «Magicrete AAC Blocks».
AAC используются более 90 лет по всему миру.Здания, построенные более 85 лет назад, стоят до сих пор. Однако для Индии это развивающийся продукт.
Когда был впервые разработан AAC? AAC был разработан в 1924 году в Швеции преподавателем архитектурных наук, который искал альтернативный строительный материал со свойствами, подобными дереву, такими как хорошая теплоизоляция, прочная структура, простота в работе и т. д., а также устойчивость к огню и термитам.
Цемент, летучая зола и известь являются важнейшими ингредиентами для изготовления блоков Magicrete AAC. Их отверждение происходит при отверждении паром, известном как автоклав. Благодаря упаковке из экологически чистых материалов эти продукты сертифицированы по системе зеленого рейтинга и помогают строителям получать кредитные баллы.
Является ли Magicrete AAC Block безопасным для окружающей среды и экологически безопасным продуктом? Да. Блоки Magicrete AAC — экологически чистый строительный материал. Продукты Magicrete AAC Blocks сохраняют и защищают драгоценные природные ресурсы земли, в отличие от кирпичей, которые потребляют верхний слой почвы.Производство блоков Magicrete AAC происходит из летучей золы, промышленных отходов теплоэлектростанции. Во время производства энергия, потребляемая в производственном процессе, составляет лишь небольшую часть по сравнению с производством других материалов. Производственный процесс не выделяет загрязняющих веществ и не создает побочных продуктов или токсичных отходов. При настенном монтаже практически не образуется отходов, и этот продукт потребляет значительно меньше воды. Блоки Magicrete AAC, нетоксичный продукт, не загрязняют воздух, землю или воду во время утилизации.Благодаря эффективному использованию ресурсов и материальной оболочке можно получить много баллов в процессе экологической сертификации, такой как LEED, GRIHA и т. д.
помогают лучше обращаться с блоками и размещать их, что снижает потери и ускоряет выполнение работы. Кроме того, проблемы с языком и канавки обеспечивают автоматическое выравнивание по стене, что устраняет необходимость проверки отвеса. Это также снижает расход раствора и обеспечивает точную стену с экономией времени и денег.
1. Ассортимент продукции ● Первая компания AAC, предлагающая комплексные решения для стен
● Материал класса 1, прочность выше на 33 %
● Маркировка ISI 2.Инфраструктура мирового класса ● 3 крупнейших игрока AAC в Индии с годовой установленной мощностью 800 000 куб.
● Стратегическое расположение в пределах 250 км от крупных городских центров и тепловых электростанций.
● Представлена в 14 штатах, в 30 крупнейших городах Индии через более 2000 торговых точек.
● Вы можете добиться операционного совершенства с помощью TPM в качестве стратегического инструмента и систем, основанных на SOP. 3. Технологии ● SCADAI HMI ((Уровень автоматизации)
● Автоматизированный диспетчерский модуль
● Модуль управления качеством
● CRM 4.Услуги с добавленной стоимостью ● Масонское обучение и аудит
● Отчет об онлайн-тестировании
● Своевременная доставка для улучшения управления цепочкой поставок
● Онлайн-мониторинг статуса заказа с автоматизированной информацией об отправке
● Выделенный колл-центр для жалоб клиентов
Да. Будучи легкими (1/3 веса глиняного кирпича), блоки Magicrete AAC настоятельно рекомендуются для высотных зданий и помогают снизить общую статичную нагрузку конструкции, что напрямую способствует экономии конструкции до 20%.
Имеют ли блоки Magicrete AAC проблемы с прочностью стен, будучи легкими? Прочность блоков Magicrete AAC соответствует стандарту IS: 2185-Part III, который является абсолютно безопасным и достаточно прочным для использования в любых ненесущих стеновых конструкциях.
Прогиб балки, осадка грунта в одну сторону, неравномерная укладка блоков при строительстве – некоторые причины растрескивания стены. Другими причинами являются структурные смещения из-за теплового расширения или изменения содержания влаги или движения влаги. Чтобы избежать такого повреждения, вы должны отложить использование газобетонных блоков до достижения равновесной влажности. Для этого блоки AAC необходимо хранить 10-15 дней до применения.Трещины появляются во всех типах бетона, в том числе и в глиняном кирпиче. Мы можем свести к минимуму эти трещины, используя некоторые методы строительства и надлежащее качество изготовления. Выравнивание блоков должно быть точным и должно проверяться спиртовым уровнем, желательно двухметровой длины. У первого ряда блоков должно быть достаточно времени для застывания, и вы должны выделить для этого не менее 24 часов. Каркасной конструкции должно хватить времени, чтобы вылечиться и осесть, чтобы вы могли заметить любые изменения в конструкции из-за движения конструкции.Через каждые 3 метра от низа до верха стены должен быть контрольный шов 10 мм. Контрольный стык должен быть заполнен упругим материалом или опорным стержнем, которые легче поддаются сжатию. И заклеить герметиком. Компенсационные стяжки необходимо давать после каждого 3-го ряда и размещать между зазорами контрольного шва. Связующая балка должна проходить через каждые 1200 мм по высоте с использованием арматуры из двух стержней MS 8 мм, связанных сталью 6-8 мм с зазором 6″-9″. Минимальную толщину перевязочного бруса следует принимать 3 дюйма с защитным слоем бетона 15-20 мм по бокам.Связующая балка должна быть прерывистой в контрольном стыке. Стальные стержни должны быть заделаны в колонны в 5-6 раз больше их диаметра и закреплены безусадочным высокопрочным раствором.
Возьмите соотношение цемента и песка 1:4 в качестве раствора для заполнения связующей балки. Причина использования связующей балки состоит в том, чтобы придать стене устойчивость и прочность. После каждого 3-го ряда между блоком и бетонной колонной должны быть анкеры.
Вы можете использовать блоки AAC для строительства всех типов стен между двумя колоннами в каркасных конструкциях, таких как перегородки, навесы, балконы и граничные стены.
Как насчет водопоглощения блоков AAC и каков его стандарт? Испытание на водопоглощение при 24-часовом погружении в воду не указано в стандарте блоков AAC IS-2185 Part-3. Теплоизоляционные стеновые элементы, такие как AAC, рекомендуется тестировать на капиллярное водопоглощение. Газобетон лучше всего поглощает капиллярную воду по сравнению с обычным кирпичом.Как и кирпич из красной глины, газобетон не рекомендуется использовать в фундаментах и во влажной среде, поэтому испытание на водопоглощение неприменимо для газобетона.
По разным причинам блоки могут повредиться при транспортировке или обращении на объекте.Это может быть использовано в качестве наполовину вырезанных блоков после размерной резки. Индийский стандарт IS-2185, часть 3, пункт 8.1.1, допускает наличие незначительных трещин и мелких сколов размером не более 25 мм, что не является основанием для отказа.
Каковы размеры блоков AAC? Блоки AAC бывают разных размеров. В длину 650, 600 мм. В высоту 250 240 200 мм и в толщину 75 100 125 150 200 225 мм.
Нет, газобетонные блоки не рекомендуется использовать в фундаменте, а также там, где присутствует повышенная влажность.
В чем его недостаток?Поскольку он очень пористый, его водопоглощение выше, чем у кирпича из красной глины, если его погрузить в воду на 24 часа.Поэтому не рекомендуется использовать его в определенных областях, таких как фундамент, канализационные отверстия и бетонные резервуары для воды.
Говорят, что здание, построенное из газобетона, экономит электроэнергию; как? AAC обладает теплоизоляционными свойствами; его теплопроводность составляет 1/5 глиняного кирпича. Таким образом, AAC сохраняет тепло в течение более длительного периода и экономит затраты на электроэнергию благодаря кондиционированию воздуха или комнатному обогревателю.
Да. IS-2185 Part-3 — это спецификация индийского стандарта для блоков AAC.
Загорается ли AAC и как насчет его рейтинга огнестойкости?Нет, AAC не загорается, а его рейтинг огнестойкости составляет 4 часа для 8-дюймовой стены.
Если мы хотим проверить прочность на сжатие блоков AAC на месте, что требуется? Было бы лучше иметь машину для испытаний на сжатие малой мощности 250 кН и машину для резки. Машины большой мощности 2000-3000 кН использовать не рекомендуется. Вместо этого следуйте рекомендациям по тестированию, указанным в IS-6441, часть 5.
Существует разница между непосредственной плотностью и плотностью после сушки. Блоки AAC имеют определенное содержание влаги в нормальных условиях, поэтому их плотность выше. Тем не менее, для целей испытаний мы сушим образец при 105 °С в течение 4-5 дней до достижения постоянного веса, а затем получаем плотность без влаги или плотность в сухом состоянии.См. IS-6441, часть 1, для проверки плотности в сухом состоянии
. Насколько долговечен газобетон в различных климатических условиях? Автоклавный газобетон отличается высокой прочностью. Он не гниет и не разлагается, как древесина или другие органические материалы. Кроме того, он не ржавеет, как металл. Термиты и другие вредители его не едят.ААС не сгорит. Миллионы крошечных ячеек в зданиях из газобетонных блоков смягчают воздействие значительной силы, предотвращая прогрессирующее разрушение. AAC выдержал землетрясения в Японии, низкие температуры Северной Европы, суровый соленый воздух Французской Риверии и пожары на склонах холмов Сан-Франциско.
№Конструкция AAC представляет собой прочную монолитную стеновую систему с закрытой, несвязанной ячеистой структурой. Наружная отделка дополняет эту структуру, обеспечивая здоровый баланс между влагостойкостью и паропроницаемостью. Кроме того, положительное давление системы кондиционирования воздуха выталкивает водяной пар через стены, предотвращая проникновение влаги снаружи.
Да. Будучи легкими (1/3 веса глиняного кирпича), блоки Magicrete AAC настоятельно рекомендуются для высотных зданий и помогают снизить общую статичную нагрузку конструкции, что напрямую способствует экономии конструкции до 20%.
Блок из ячеистого легкого бетона похож на блок из газобетона? Несмотря на то, что они кажутся похожими, это разные продукты. Параметры прочности CLC составляют 25 кг на кв.см. В то время как прочность газобетонных блоков составляет от 35 до 40 кг на кв. см. CLC нельзя разрезать проволокой, а края не аккуратны и легко повреждаются.CLC отверждается обычными методами, а AAC готов к использованию с достаточной прочностью на этапе постпроизводства благодаря усовершенствованному процессу отверждения в автоклаве. В отличие от блоков AAC, блоки CLC вызывают выделение токсичных газов.
Да.Блоки Magicrete AAC можно использовать для несущих конструкций высотой до 3 этажей.
Должны ли мы замочить и намочить блок перед использованием? Нет. Замачивание и смачивание газобетона не требуется. Достаточно легкого увлажнения.
42 Блоки Magicrete размером 600 X 200 X 200 мм составляют CBM.
Поставляете ли вы или рекомендуете какую-либо уникальную добавку для лучшего склеивания газобетонных блоков?Да, есть. Мы производим и поставляем клей Magicbond для газобетонных блоков.
Какое испытательное оборудование требуется для проверки прочности на сжатие блоков AAC? ● Машина для испытаний на сжатие (CTM) должна позволять считывать предельную нагрузку с максимальной погрешностью (+/-) 2. 0 %.
● Скорость нагрузки должна составлять от 0,5 до 2 кг/кв. см, чтобы отказ произошел в течение 30 секунд.
● Сушильная печь
● Образец должен быть высушен в печи при температуре 105+/-5 градусов Цельсия в течение 4 часов или может быть повторен несколько раз для достижения влажности образца от 8% до 12%. ● Поверхности образцов должны быть равны поверхности давления CTM.● Направление нагрузки должно быть перпендикулярно направлению подъема массы во время производства. ● Скорость нагрузки должна составлять от 0,5 до 2 кг/кв. см, чтобы разрушение произошло в течение 30 секунд.
Каковы стандартные размеры блоков Magicrete AAC?блоков AAC Magicrete: Размеры: Блоки Magicrete AAC доступны в следующих размерах/толщине/длине и высоте: Стандартные размеры блоков: Толщина: 75/100/125/150/200/225 мм Длина: 625/600 мм Высота: 240/200 мм
Сколько блоков нужно на 100 кв.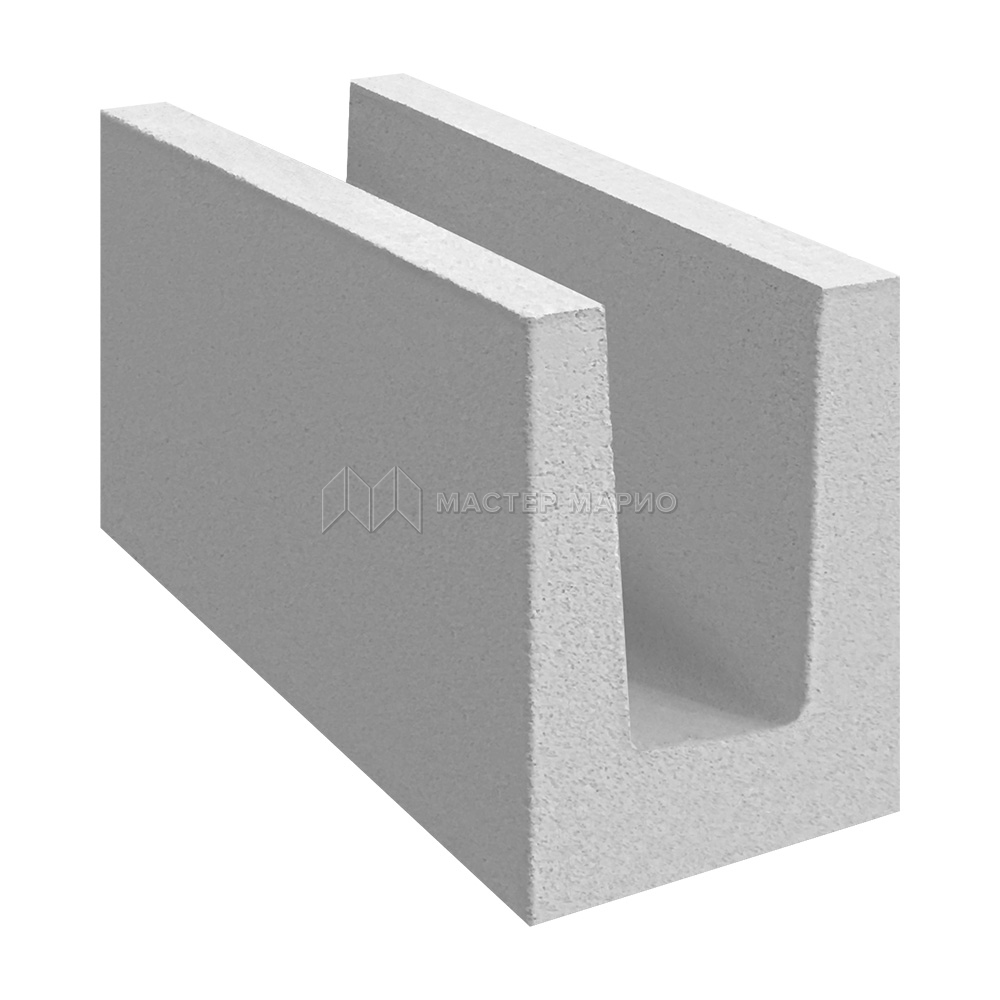
● Для 100 швейцарских футов. (9,29 кв.м) кладочные работы / площадь стены = 63,15, т.е. 63 номера (для блоков высотой 240 мм) ● Для 100 швейцарских футов. (9,29 кв.м) объем кладки / площадь стены = 72,52, т.е. 73 номера (для блоков высотой 200 мм) ● Блоки стандартных размеров предусматриваются с учетом толщины шва на цементном растворе 10 мм.
Каковы преимущества и преимущества блоков Magicrete AAC?● Легкий вес ● Экономичность ● Высокая теплоизоляция ● Огнестойкость ● Звукоизоляция ● Устойчивость к влаге, вредителям и плесени ● Сейсмостойкость ● Экологичность
Блоки
Работа с блоками — это необходимость в здании. Почти все здания будут так или иначе построены из бетонных блоков. По данным Ассоциации производителей бетонных блоков, ежегодно производится 60 миллионов квадратных метров строительных блоков из плотного и легкого бетона.
Существует три основных типа блоков; плотный, легкий и аэрированный. Плотные бетонные блоки с их свойствами долговечности и прочности обычно выбирают для несущих стен. Легкие блоки, которые часто выбирают для заполнения, обеспечивают большую экономию времени и средств, но менее прочны.Газобетонные блоки широко используются в Великобритании с 1960-х годов и обеспечивают как структуру, так и изоляцию. Они производятся путем добавления в смесь алюминиевой пудры, которая позволяет протекать химической реакции, образуя пузырьки воздуха в бетоне.
Стены обычно составляют наибольшую площадь поверхности здания, поэтому важно обеспечить хорошую теплоемкость и низкие значения коэффициента теплопередачи. Использование блоков дает возможность получить большую тепловую массу, особенно если они используются для создания не только внешних стен, но и внутренних перегородок.
уже давно подвергается критике за его воздействие на окружающую среду. Тем не менее, отрасль вносит улучшения; за счет поощрения использования альтернатив цементу снижается воздействие на окружающую среду. Измельченный гранулированный доменный шлак (GGBS) обычно можно использовать для замены до пятидесяти процентов цемента в бетонной смеси. Другой распространенной альтернативой является зола пылевидного топлива, являющаяся отходом сжигания на угольных электростанциях. Для оптимальной прочности он может заменить пятнадцать процентов цемента в стандартных блоках и до пятидесяти процентов в газоблоках.
Существует растущий рынок альтернатив бетону. Начинают использоваться натуральные и возобновляемые материалы. Глиняные сотовые блоки использовались на континенте в течение многих лет, но теперь они становятся все более распространенными в Великобритании. Они имеют ячеистую структуру, которая задерживает воздух, действуя как утеплитель. Конопляные блоки обеспечивают высокий уровень изоляции с воздухопроницаемостью, обеспечивая при этом структуру. Они также очень устойчивы из-за своей способности улавливать углерод, но еще не стали обычным явлением в строительной отрасли Великобритании.
Высокопрочная гладкая поверхность Thermalite Блоки
Hanson’s Thermalite легкие, что означает, что их можно укладывать быстрее. Блоки из газобетона содержат карманы захваченного воздуха, обеспечивающие хорошую прочность на сжатие, высокий уровень теплоизоляции и влагостойкости.
Производитель: Hanson
Применение: стены, перегородки
Материал: пылевидная зола, песок, цемент, известь, алюминий и вода
Возможность вторичной переработки: многоразовый
Переработанный материал: 50 % пылевидной топливной золы перед потребителем
Размеры лицевой стороны: 440 x 215 мм
Ширина блоков: 100 мм и 140 мм
Плотность: 730 кг/м 3
Прочность: 7. 3 Н/мм 2
Теплопроводность: 0,18 Вт/мК
Дистрибьюторская база в Великобритании: Уэст-Мидлендс и Кент
www.heidelbergcement.com
Термалайт Турбо
Блок Thermalite Turbo подходит для всех видов блочных работ, включая использование ниже уровня DPC. Используя блок минимальной ширины 215 мм, Turbo можно использовать во внешних сплошных стенах, где требуются низкие значения коэффициента теплопередачи.
Производитель: Hanson
Применение: наружные стены, перегородки и фундаменты
Материал: пылевидная зола, песок, цемент, известь, алюминий и вода
Возможность вторичной переработки: многоразовый
Переработанный материал: 50 % пылевидной топливной золы перед потребителем
Размеры лицевой стороны: 440 x 215 мм
Ширина блоков: 100 мм, 115 мм, 125 мм, 140 мм, 150 мм, 190 мм, 200 мм, 215 мм, 265 мм и 300 мм
Плотность: 470 кг/м 3
Прочность: 2. 9 Н/мм 2
Теплопроводность: 0,11 Вт/мК
Дистрибьюторская база Великобритании: Кент
www.heidelbergcement.com
Энвироблок облегченный
Enviroblock содержит как минимум 80% переработанных заполнителей. Их можно использовать как внутри, так и снаружи, и они доступны как в стандартной, так и в окрашенной отделке.
Производитель: Aggregate Industries UK
Применение: стены, перегородки
Материал: цемент, фарфоровая глина и вода
Возможность вторичной переработки: повторное использование и переработка
Содержание вторичного сырья: минимум 80%
Размеры лицевой стороны: 440 x 215 мм
Ширина блоков: 100 мм и 140 мм
Плотность: 1450 кг/м 3
Прочность: 7. 3 Н/мм 2
Теплопроводность: 0,84 Вт/мК
Ожидаемая продолжительность жизни: 10 лет
Дистрибьюторская база в Великобритании: Абердин, Лестершир, Уилтшир и Корнуолл
www.aggregate.com
Энвироблок Плотный
Этот блок подходит для использования как выше, так и ниже DPC. Он доступен в лакокрасочном покрытии, которое подходит для использования там, где требуется однородная и плотная текстурированная поверхность.
Производитель: Aggregate Industries UK
Применение: стены, перегородки
Материал: цемент, фарфоровая глина и вода
Возможность вторичной переработки: повторное использование и переработка
Содержание вторичного сырья: минимум 80%
Размеры лицевой стороны: 440 x 215 мм и 290 x 215 мм
Ширина блоков: 100 мм и 140 мм
Плотность: 1950 кг/м 3
Прочность: 10. 4 Н/мм 2
Теплопроводность: 1,37 Вт/мК
Ожидаемая продолжительность жизни: 10 лет
Дистрибьюторская база в Великобритании: Абердин, Лестершир, Уилтшир и Корнуолл
www.aggregate.com
Masterdenz с гладкой поверхностью Solid
Этот блок имеет неизменно высокое качество отделки, что делает его особенно подходящим для облицовки блочной кладки. Он доступен в натуральном желтовато-коричневом или сером цвете, созданном естественным образом, без использования искусственной пигментации .
Производитель: Aggregate Industries UK
Применение: стены, перегородки
Материал: бетон
Возможность вторичной переработки: повторное использование и переработка
Размеры лицевой стороны: 440 x 215 мм
Ширина блоков: 75 мм, 100 мм и 140 мм
Плотность: 1900 кг/м 3
Прочность: 7,3 Н/мм 2
Теплопроводность: 1. 31 Вт/мК
Ожидаемая продолжительность жизни: 10 лет
База дистрибуции в Великобритании: Ланкашир, Уилтшир, Лестершир, Корнуолл и Шотландия
www.aggregate.com
Блоки ThermoplanZiegel
Блок ThermoplanZiegel представляет собой сотовый блок из глины, который обеспечивает высокую изоляцию и низкие значения psi. Система подходит для зданий высотой до четырех этажей.
Производитель: Natural Building Technologies
Применение: наружные стены
Материал: глина
Возможность вторичной переработки: многоразовый
Размеры лицевой стороны: 250 x 250 мм
Ширина блоков: 300 мм, 365 мм и 425 мм
Плотность: 650 кг/м 3
Прочность: 6 Н/мм 2
Теплопроводность: 0. 09Вт/мК
Страна производитель: Германия
Дистрибьюторская база в Великобритании: Лондон и Бакингемшир
www.naturalbuilding.co.uk
Конопляный блок HC
Изготовленный из промышленной конопли блок Hemp HC имеет ряд экологических сертификатов. Они предлагают преимущество связывания углерода, так как конопля поглощает углерод по мере своего роста.
Производитель: Hemp Construct
Применение: Наружные стены и перегородки
Материалы: Конопляная заточка, гашеная известь, гидравлическая известь и вода
Размеры лицевой стороны: 600 x 300 мм
Ширина блока: 300 мм
Плотность: 340 кг/м³
Прочность: 10.8 Н/мм²
Теплопроводность: 0,53 Вт/мК
Дистрибьюторская база Великобритании: Эссекс
www. hempbuildingsystems.com
Стандартные блоки Celcon
Блоки Celcon Standard Grade Blocks можно использовать не только для облицовки стен, но и ниже уровня DPC в качестве заполнения балочных и блочных перекрытий.
Производитель: H+H
Применение: внутренние и наружные стены, перегородки, балочные и блочные перекрытия и фундаменты
Материал: пылевидная зола, заполнители, алюминиевый порошок
Возможность повторного использования: может быть переработан для использования в качестве заполнителя
Переработанный материал: содержит до 80 % переработанного материала
Размеры лицевой стороны: 440 x 215 мм
Ширина блока: 75 мм, 100 мм, 115 мм, 140 мм, 150 мм и 215 мм
Плотность: 600 кг/м 3
Прочность: 3. 6 Н/мм 2
Теплопроводность: 0,15 Вт/мК
Ожидаемая продолжительность жизни: старше 35 лет
Дистрибьюторская база Великобритании: Йоркшир
www.hhcelcon.co.uk
Стандартный фундаментный блок Celcon
Разработанный для использования ниже уровня DPC, этот блок подходит для поддержки полых или сплошных стен, каркасных конструкций или подвесных полов, включая перекрытия из балок и блоков.
Производитель: H+H
Применение: фундамент
Материал: пылевидная зола, заполнители, алюминиевый порошок
Возможность повторного использования: может быть переработан для использования в качестве заполнителя
Переработанный материал: содержит до 80 % переработанного материала
Размеры лицевой стороны: 325 x 215 мм, 440 x 215 мм и 610 x 140 мм
Ширина блоков: 215 мм, 275 мм, 300 мм и 355 мм
Плотность: 600 кг/м 3
Прочность: 3. 6 Н/мм 2
Теплопроводность: 0,25 Вт/мК
Ожидаемая продолжительность жизни: старше 35 лет
Дистрибьюторская база Великобритании: Йоркшир
www.hhcelcon.co.uk
Гигантские блоки
Jumbo Bloks позволяют возводить 1 м 2 стены из шести блоков, что увеличивает скорость и производительность. Эти блоки примерно в два с половиной раза больше, чем традиционные блоки.
Производитель: H+H
Применение: перегородки, внутренние и внешние стены
Материал: пылевидная зола, заполнители, алюминиевый порошок
Возможность повторного использования: может быть переработан для использования в качестве заполнителя
Переработанный материал: содержит до 80 % переработанного материала
Размеры лицевой стороны: 610 x 270 мм
Ширина блоков: 100 мм и 140 мм
Плотность: 600 кг/м 3
Прочность: 3. 6 Н/мм 2
Теплопроводность: 0,15 Вт/мК
Ожидаемая продолжительность жизни: старше 35 лет
Дистрибьюторская база Великобритании: Йоркшир
www.hhcelcon.co.uk
Бетонные блоки с лицевой поверхностью
Эти блоки предназначены для наружной облицовки, обеспечивая как структурную целостность, так и высококачественную отделку. Блок с гладкой поверхностью доступен в девяти различных цветах.
Производитель: Forticrete
Применение: наружная облицовка стен
Материал: бетон
Размеры лицевой стороны: 400 x 215 мм
Ширина блоков: 90 мм, 100 мм, 140 мм и 215 мм
Плотность: 2100 кг/м 3
Прочность: 17,5 Н/мм 2
Теплопроводность: 1,56 Вт/мК
www. forticrete.com.co.uk
Ячеистые блоки из плотного бетона
Эти ячеистые блоки представляют собой легкую альтернативу плотным бетонным блокам. Их можно применять как для внутреннего, так и для наружного листа полых стен высотой до трех этажей.
Производитель: Томас Армстронг
Применение: наружные и внутренние стены
Материал: бетон
Содержание вторичного сырья: до 30%
Размеры лицевой стороны: 440 x 215 мм
Плотность: 2100 кг/м 3
Прочность: 10.4 Н/мм 2
Теплопроводность: 0,92 Вт/мК
www.thomasarmstrong.co.uk
Блоки из легкого бетона Fibotherm Бетонные блоки Fibotherm
обеспечивают высокую скорость строительства благодаря своей легкости. Они обеспечивают высокий уровень изоляции, а поверхность действует как хороший ключ для штукатурки.
Производитель: Стоуэлл Бетон
Применение: наружные и внутренние стены, полые стены и перегородки,
Размеры лицевой стороны: 440 x 215 мм
Ширина блока: 75 мм, 100 мм, 140 мм и 190 мм
Плотность: 850 кг/м 3
Прочность: 3.6 Н/мм 2
Теплопроводность: 0,29 Вт/мК
Дистрибьюторская база в Великобритании: Бристоль, Чеддер и Уэстон Супер Мэр
www.stowellconcrete.co.uk
Дюрисол D365/120 Блоки
Durisol изготавливаются из древесной щепы, связанной цементом. Для устойчивости конструкции в полость, окружающую стальную арматуру, необходимо залить бетон. Они получают рейтинг BRE Green Guide A+.
Производитель: Дюрисол
Применение: наружные стены
Материал: Переработанная и обработанная древесина, цемент и PFA
Переработанный материал: 80 % переработанная древесина
Размеры лицевой стороны: 500 x 250 мм
Ширина блока: 365 мм
Прочность: определяется ядром бетона
Теплопроводность: 0,19 Вт/мК
Дистрибьюторская база Великобритании: Южный Уэльс
www.durisol.net
AAC BLOCK : АВТОКЛАВИРОВАННЫЕ БЕТОННЫЕ БЛОКИ
ААС означает Автоклавный газобетон. (
также известный как автоклавный ячеистый бетон (ACC), автоклавный легкий бетон (ALC), автоклавный бетон,
ячеистый бетон, пористый бетон) Это сверхлегкий бетонный кладочный продукт, обладающий рядом преимуществ в
практичность. В настоящее время он приобретает все большее значение в строительной отрасли, заменяя все традиционные методы. Эта ячеистая структура придает AAC ряд исключительных физических характеристик. Он весит всего 1/5
так же, как обычный бетон, из-за его отчетливой ячеистой структуры, которая имеет миллионы крошечных карманов
захваченный воздух. AAC состоит из основных материалов, которые широко доступны. К ним относятся песок, цемент, известь, летучие
зола, гипс, паста из алюминиевой пудры,
вода и расширительный агент. Кварцевый песок, сырье, используемое в
самый большой объем в AAC, является одним из самых богатых природных ресурсов в мире.Готовый продукт до
пятикратный объем используемого сырья, с содержанием воздуха от 70% до 80% (в зависимости от требуемой
прочность и плотность). В последнее десятилетие в строительной отрасли проводились различные исследования по использованию
легкодоступного сырья в строительстве. Газобетон — один из материалов, способных справиться с
нехватка строительного сырья и может производить легкие, энергоэффективные и экологически чистые
конкретный. Это исследование посвящено введению в процесс автоклавного газобетона и его преимуществам по сравнению с обычным
конкретный .
Блок AAC |
Автоклавный газобетон. не «новый»
инновации. Он существует уже более 80 лет. Изобретен в 1923 году.
AAC широко используется в Европе и Азии. Она составляет более 40% всех
строительство в Соединенном Королевстве
и 60% в Германии и 16% в Индии. С римских времен легкие заполнители
и пенообразователи
применяется для уменьшения веса бетона.Однако, в отличие от этих вспененных или
смеси легких заполнителей, правда
газобетон основан на щелочном вяжущем (известь и цемент), реагирующем с
кислота для выпуска газов, которые остаются
увлекся материалом.
История AAC
AAC
был усовершенствован в середине 1920-х годов шведским архитектором и изобретателем доктором Йоханом
Аксель Эрикссон] работает с профессором
Хенрик Крюгер из Королевского технологического института. Он был запущен в производство в
Швеция в 1929 году на фабрике
в Hällabrottet и быстро стал очень популярным. Сипорекс был основан в
Швеция в 1939 году и в настоящее время лицензии
и владеет заводами в 35 местах по всему миру. В 1940-х годах торговая марка Ytong был представлен и
в Швеции его часто называют «голубым бетоном» из-за его голубоватого цвета.
оттенок. Эта версия Ytong была изготовлена из квасцов.
сланец, содержание горючего углерода в котором делало его выгодным для использования в
производственный процесс.
AAC блокирует индийский сценарий
ААС
состоит из основных материалов, которые широко доступны.К ним относятся песок,
цемент, известь, гипс, вода и наполнитель
агент. Кварцевый песок, сырье, используемое в наибольшем объеме в AAC, является одним из
из самых распространенных в мире
природные ресурсы. В настоящее время в Индии насчитывается 31 производственное предприятие.
работа с сильной концентрацией
недалеко от Сурата. Гуджарат: производственная мощность 2000 м3/день по требованию
3000 м3/сутки (в Сурате есть
3-4 растения). В Ахмадабаде 1 м3 газобетонных блоков стоит рупий. 3200-3500 при 1 м3
глиняные кирпичи будут стоить 2400-2700 рупий.
Несмотря на разницу в цене, строительная промышленность хочет использовать газобетонные блоки.
благодаря присущим преимуществам.Он больше используется в Мумбаи, Банглоре, Ченнаи и Хубли .
Спецификация блоков газобетона
ПАРАМЕТР
| В мм |
Длина | 625 |
Ширина | 240 |
Толщина | 90/100/150/200 |
Допуск | +-1% |
Производство газобетонных блоков
В отличие от
Для большинства других бетонных применений газобетон производится без заполнителя большего размера. чем песок.Кварцевый песок, кальцинированный
в качестве вяжущего используют гипс, известь (минеральную) и/или цемент и воду.
Алюминиевый порошок используется при
нормой 0,05%–0,08% по объему (в зависимости от заранее заданной плотности). В
некоторые страны, например Индия и Китай, летают
зола тепловых электростанций с содержанием кремнезема 50-65%.
используется как агрегат.
Используемое сырье
Старший № | Материал | % доли для газобетонных блоков с Летучая зола/песок |
1 | Летучая зола / песок | 65 – 70 / 55-65 % |
2 | Цемент – 53 Марка OPC | 6-15 / 10-20 % |
3 | Лайм | 18-25 / 20-30 % |
4 | Гипс | 3 – 5 / 2 – 3 % |
5 | Алюминиевая порошковая паста (600 кг/куб) | 8 % |
6 | Вода | 0. |
7 | Литейная система | 36-40°С / 35-38°С |
Когда
Газобетон смешивают и отливают в формы, происходит несколько химических реакций, которые дают
AAC его легкий вес (20% от
вес бетона) и теплофизические свойства. Алюминиевый порошок реагирует с кальцием
гидроксид и вода с образованием
водород. Газообразный водород вспенивается и удваивает объем сырьевой смеси, создавая
пузырьки газа до 3 мм (⅛
дюйм) в диаметре.В конце процесса вспенивания водород уходит в
атмосферу и заменяется
воздух. Когда формы удаляются из материала, он твердый, но все еще мягкий.
Затем его разрезают на блоки или панели,
и помещают в автоклавную камеру на 12 часов. При этом давление пара
процесс закалки, когда температура
достигает 190° по Цельсию (374° по Фаренгейту), а давление достигает от 8 до 12 бар,
кварцевый песок реагирует с кальцием
гидроксид с образованием гидрата силиката кальция, который придает AAC его высокую прочность
и другие уникальные свойства. Так как
блоков AAC с относительно низкой температурой не считаются обожженными
кирпич, а легкий бетон
каменный агрегат. После автоклавирования материал готов к
немедленное использование на строительной площадке.
В зависимости от плотности до 80% объема газобетонных блоков составляет воздух. AAC
низкая плотность также объясняет его
низкая прочность конструкции на сжатие. Он может выдерживать нагрузки до 8 МПа (1160
PSI), примерно 50 %
прочность обычного бетона.
Преимущества Блоки AAC
Легкие экономит затраты и энергию на транспортировку, а также на рабочую силу.(550 кг/м3 — половина масса легкого заполнителя блоков) Больший размер (в 6 раз больше кирпича) приводит к более быстрому строительству и требуется меньше раствора для соединения.
1. Пожар
Стойкость: Это
имеет один из самых высоких часовых рейтингов огнестойкости на дюйм среди всех зданий
материал в настоящее время
используется в жилищном строительстве. Это делает его идеальным выбором для противопожарной защиты вокруг
стальные колонны и 1)
Балки стальные и при возведении стен шахт, лестничных клеток, коридоров
и брандмауэры.
2. Газобетон очень экологически чистый : Процесс производство газобетона использует только натуральные материалы и производит отсутствие загрязняющих веществ или побочных продуктов. AAC полностью не содержит токсичных или вредных вещества. Требуется низкое энергопотребление в производстве, низкий расход сырья, простота использования в строительстве, высокая энергоэффективность, лучше Качество воздуха в помещении и возможность вторичной переработки делают газобетонный газобетон экологически безопасным. дружественный строительный материал и система.
3. Дышащий: It не способствует развитию плесени.
4. Хорошо Звукоизоляционные свойства: Коэффициент шумоподавления более чем в два раза больше, чем стандартная стена из бетонных блоков и более чем в 7 раз больше, чем из обычного бетона.
5. Легко
Рабочий: Это
можно легко обрезать до любой требуемой формы, легко пилить, прибивать гвоздями и сверлить
даже чем дерево.
6. Прочный: Обладает хорошей устойчивостью к сульфатная атака.
7. Привлекательный Отделка: Стены могут оставлять открытыми без гипса.
8. Экономичный: Не требует отверждения, стоимость рабочей силы сохраняется следовательно.
Недостаток AAC
Некоторые
Недостатки блоков и панелей из газобетона заключаются в том, что они содержат портландцемент .
производятся в очень небольшом количестве мест, что означает более высокую стоимость транспортировки и использование газа
Ресурсы. Строители должны научиться
использовать их, так как раствор отличается, некоторые из блоков сделаны для
Европейские стандарты и должны быть
резать. Они пористые, поэтому должны иметь штукатурку или облицовку снаружи, чтобы сохранить
из воды.Для несущей способности газобетон может
необходимо армирование арматурой. В некоторых штатах они еще не приняты в
строительные нормы из-за
отсутствие результатов тестирования.
Что не является зеленым в портландцементе, так это то, что он содержит около 60 процентов
известняк или карбонат кальция и
необходимо сжигать при высоких температурах в печах, используя много энергии и создавая
углекислый газ (CO2), парник
газ связан с глобальным потеплением. Более новый цемент на основе магнезии можно обжигать при
более низкие температуры
используя меньше энергии и создавая меньше CO2.Карбонат магния и кальций
оба карбоната получаются
при добыче полезных ископаемых, но низкощелочной магнезиальный бетон может оставаться прочным при переработке
добавлены материалы
в смесь и может лучше изолировать при добавлении органических материалов. Магнезия
бетон также может поглощать CO2 через
процесс карбонизации во время его производства и использования, что снижает
парниковый газ.
Вакуумный мешок только для приклеивания препрега к сотовому заполнителю из арамида. Часть I. Модель и свойства материала для внутреннего давления во время обработки
Composites: Part A xxx (2015) xxx–xxxСписки содержания доступны по адресу ScienceDirect
Composites: Part A Домашняя страница журнала: www.elsevier.com/locate/compositesa
Вакуумный мешок только для совместного приклеивания препрега к арамидному сотовому заполнителю. Часть I. Модель и свойства материала для давления в сердцевине во время обработки Джеймс Крац, Паскаль Хуберт ⇑ Факультет машиностроения, Университет Макгилла, 817 Шербрук-Стрит. Доступно онлайн xxxx Ключевые слова: A. Сотовый заполнитель B. Поведение при отверждении C. Аналитическое моделирование Воздухопроницаемость препрега
аннотация Была разработана технологическая модель для расчета давления заполнителя сотового заполнителя при производстве сэндвич-панелей.Модель предсказывала приток влаги из клеточных стенок в пространство клеточных полостей по закону Фика, а отток влажного воздуха через кожу со стороны мешка — по закону Дарси. Модель требовала экспериментального измерения влажности сердцевины и воздухопроницаемости сотовой оболочки по толщине. В качестве материала для обшивки в этом исследовании использовали частично пропитанный тканый препрег, изготовленный вне автоклава. Чтобы точно применить закон Дарси во время обработки при повышенной температуре, был предложен метод пошагового измерения температуры для поддержания постоянной толщины кожи во время характеристики воздухопроницаемости. Для подтверждения того, что предлагаемый метод характеризации поддерживает динамику пропитки целевого цикла отверждения, была выполнена микро-КТ. Прогнозы модели с использованием охарактеризованных свойств материала сравниваются с измерениями кернового давления на месте в Части II. Ó 2014 Elsevier Ltd. Все права защищены.
1. Введение Прерывистый характер поверхностей соединения в сотовом заполнителе может привести к исключительно легким многослойным конструкциям, но также является причиной большинства дефектов, вызванных технологическим процессом.В процессах формования мешков перепад давления, воздействующий на сотовую оболочку, определяется внешним давлением на мешок (PExt), уровнем вакуума под мешком (PBag) и давлением внутри сотового заполнителя (PCore). Эти давления показаны на идеализированной схеме сотовой оболочки на рис. 1а. Внешнее давление может быть атмосферным или создаваться автоклавом, но если оно слишком высокое, это может привести к боковому раздавливанию керна, образованию ямочек на коже и образованию подушек [1]. С другой стороны, если уменьшить внешнее давление, чтобы смягчить эти дефекты, могут возникнуть чрезмерные пустоты кожи и отслоение кожи от сердцевины [1].При автоклавной обработке перепад давления можно регулировать для улучшения качества деталей, но при обработке только вакуумным мешком (VBO) внешнее давление зависит от атмосферных условий и уровня вакуума, достигаемого под мешком. Три исследования обработки сот VBO показали, что существует идеальный перепад давления для минимизации пустот и максимизации механических свойств [2–4]. Грув и др. [2] сообщают о лучших механических свойствах при пониженном уровне вакуума от 200 до 220 мбар по сравнению с полным вакуумом.Аналогично, Rion et al. [3] сообщение сокращено ⇑ Автор, ответственный за переписку. Тел.: +1 514 398 6303. Адрес электронной почты: [email protected] (П. Хьюберт).
Вакуум 300 мбар уменьшает волнистость поверхности в тонкостенных сотовых панелях. Напротив, Tavares et al. [4] поддерживали полный вакуум под мешком, но сообщили об оптимальном давлении в ячеистой сердцевине от 400 до 700 мбар для улучшения уплотнения кожи и адгезии кожи к сердцевине. Эти исследования уменьшили перепад давления, воздействующий на сотовую обшивку, и в результате улучшили сцепление между обшивкой и сердцевиной и пористость обшивки.Оптимальный диапазон давления в сотовом заполнителе зависит от изготавливаемой сэндвич-конструкции. Например, для сердечников с большим диаметром ячеек может потребоваться более толстая оболочка, более низкий уровень вакуума в мешке или более высокое внутреннее давление в сердечнике для стабилизации сердечника и уменьшения пористости оболочки. Достижение оптимального давления в сердцевине регулируется поглотителями и источниками давления в производственном процессе. Давление в сердцевине сот будет уменьшаться с учетом воздухопроницаемости кожи и уровня вакуума в мешке и увеличиваться из-за расширения газа, возникающего при повышении температуры и наличии влаги или других летучих веществ.Соответствующие модели и методы измерения, необходимые для прогнозирования давления в сердцевине сот во время обработки, рассматриваются в литературе по моделированию процессов композитов.
Выражения для сохранения массы и импульса, которые были применены для оценки времени заполнения при формовании жидких композитов (LCM) [5], могут быть использованы для оценки удаления воздуха при обработке VBO, если закон Дарси скорректирован для потока сжимаемого газа. Методы измерения сопротивления препрегов воздушному потоку, или, что чаще называют воздухопроницаемостью, опубликованы на сайте
http://dx.doi.org/10.1016/j.compositesa.2014.11.026 1359-835X/Ó 2014 Elsevier Ltd. Все права защищены.
Пожалуйста, цитируйте эту статью в прессе следующим образом: Kratz J, Hubert P. Вакуумный мешок только для совместного склеивания препреговой оболочки с арамидным сотовым заполнителем. Часть I. Модель и свойства материала для давления в керне во время обработки. Композиты: Часть A (2015), http://dx.doi.org/10.1016/j.compositesa.2014.11.026
2
Дж. Крац, П. Хьюберт / Композиты: Часть A xxx (2015) xxx– xxx
был предложен при температуре окружающей среды и повышенных температурах как для препрегов [6–13], так и для сотовых оболочек [14–17]. Подобное явление, наблюдаемое в LCM, также происходит в препрегах, а именно, течение сначала возникает в высокопроницаемых макропорах между пучками волокон, а затем в микропористых жгутах с более низкой проницаемостью [18,19]. В результате можно ожидать, что воздухопроницаемость будет изменяться на протяжении всего производственного процесса. В литературе сообщалось об измерениях воздухопроницаемости через толщину обшивки из препрега OoA порядка 1018 м2, но она может быть увеличена до 1016 м2, если обшивка перфорирована [6,14]. Влияние воздухопроницаемости на давление заполнителя сотового заполнителя при обработке менее распространено в открытой литературе.Было рассмотрено время выдержки вакуума, необходимое для достижения оптимального давления в сердцевине сот для алюминиевых сотовых панелей [4]. Однако, насколько нам известно, влияние неметаллического заполнителя на давление в сотовом заполнителе во время обработки отсутствует в литературе и может привести к тому, что давление в сотовом заполнителе значительно превысит оптимальный диапазон.
Кроме того, бумага из арамидного волокна может поглощать до 10% влаги по весу [20], и было замечено, что эта влага диффундирует из сердцевины в виде пара при повышении температуры отвержденных структур [21].Влияние влаги на давление сотового заполнителя во время обработки невулканизированной и проницаемой оболочки препрега остается неизвестным. Цель этого исследования состояла в том, чтобы разработать модель процесса для давления в сердцевине сот во время обработки при повышенной температуре. Модель связывает параметры процесса (давление в сотовом ядре, уровень вакуумного мешка и температурный профиль) со свойствами материала (воздухопроницаемость кожи и влажность сотового заполнителя). Свойства материала, необходимые для входных данных модели, были измерены для типичной препреговой оболочки OoA и арамидного сотового заполнителя с атмосферными условиями, действующими как внешнее давление в мешке.В части II этого исследования были изготовлены сотовые панели со встроенными миниатюрными датчиками давления для сравнения с предсказаниями модели.
Клейкая пленка
обычно используется для улучшения сцепления кожи с сердцевиной, но она будет препятствовать воздушному потоку через толщину [6,10,17]. В-третьих, анизотропная природа композиционных материалов приводит к разным временам эвакуации воздуха в зависимости от коэффициента сжатия материала [22]. Было установлено, что для аналогичных препрегов OoA отвод воздуха по толщине происходит быстрее, чем отвод воздуха в плоскости для сотовых структур с планарными размерами (длина или ширина) больше 0.4 м [23]. Учитывая, что внеавтоклавная обработка, скорее всего, будет применяться к более крупным интегрированным структурам, которые не подходят для современных автоклавов [24], для этой модели будет учитываться сквозной поток газа. Пустое пространство внутри сотовой ячейки ограничено стенками ячейки, обшивкой со стороны мешка и обшивкой со стороны инструмента. С этими границами был создан контрольный объем для описания повторяющейся сотовой элементарной ячейки, и схема контрольного объема показана на рис. 2. Стенки ячеек поглощают и выделяют влагу в контрольный объем, ограниченный проницаемой оболочкой со стороны мешка и непроницаемая кожа со стороны инструмента.Модель предсказывает давление на основе текущей массы воздуха и водяного пара, mCell, состоящей из притока _ Honeycomb и оттока влажной влаги из стенок ячеек, m _ BagSide. воздуха через проницаемую оболочку со стороны мешка, м Изменение давления в сердцевине сот в контрольном объеме зависит как от пространства, так и от времени и следует закону сохранения массы:
r ðqv Þ =
@q ; @t
ð1Þ
– скорость газа, где q – плотность газа, а v – контрольный объем (или сотовая ячейка).Интегрируя уравнение (1) дает количество вещества, поступающего в контрольный объем V через его границы: объемный интеграл сотовой ячейки в поверхностный интеграл трех ограничивающих поверхностей дает:
2. Разработка модели Использование легких сотовых заполнителей представляет три производственных нюанса по сравнению с монолитными ламинатами. Во-первых, большой объем атмосферного воздуха, в том числе влага из окружающей среды, попадает внутрь сотового заполнителя после укладки.Во-вторых,
вакуумная сумка
T
T
T
EnotComb
@ ¼ @T
qv n ds t qv n ds t qv n ds bag n ds t qv n ds сумка n ds t qv n ds zzz
инструмент для инструментов
q dv;
ð3þ
V
V
Release Poxt
PEXT
Boids
PORES / Voids
PHAM
PEXT ΔH
PHBAGE
RESIBLE
H
клей
PCELL
PCELL
Сим.
Клеточная стенка
(a)
PCell
PCell
Sym.
(б)
Рис. 1. Идеализированные фазы, присутствующие в внеавтоклавной сотовой оболочке: (а) после укладки и (б) в процессе обработки при повышенной температуре. (Для интерпретации ссылок на цвет в легенде к этому рисунку читатель отсылается к веб-версии этой статьи.)
Пожалуйста, цитируйте эту статью в прессе как: Kratz J, Hubert P. Только вакуумный мешок для совместного склеивания препрег-оболочек с арамидным сотовым заполнителем.Часть I. Модель и свойства материала для давления в керне во время обработки. Композиты: Часть A (2015), http://dx.doi.org/10.1016/j.compositesa.2014.11.026
3
Дж. Крац, П. Хьюберт / Композиты: Часть A xxx (2015) xxx– xxx
y
y
ZX
x Проницаемая кожа
M9 HANK Skin
MhoneyComb Mcell MhoneyComb MhoneyComb
контрольный объем непроницаемой кожи
(A)
(B)
Рис. 2. Схема сотового ядра: (а) повторяющийся блок и (б) контрольный объем, используемый для моделирования давления.
, где левая часть уравнения. (3) описывает внешние потоки . Если исходить из контрольного объема через нормали к поверхности, то считать, что преобладает сквозной поток газа через обшивку со стороны мешка, потоком через обшивку со стороны инструмента можно пренебречь, а весь поток наружу происходит через обшивку со стороны мешка. . Преобразование сотового потока во внутренний поток и интегрирование уравнения (3) дал изменение массы во времени, м:
_ Соты м _ Мешок м
Кожа
_ Ячейка : ¼m
ð4Þ
Для прогнозирования давления в сотовой ячейке рассчитывали массу в сотовой ячейке путем дискретизации уравнения.(4) шаг по времени Dt:
_ Соты m _ Мешок m
Кожа
=
mCell;tþDt mCell;t : Dt
ð5Þ
пространство теперь регулируется влагообменом между стенками сотовых ячеек и проникновением влажного воздуха через кожу мешка. Общее давление в сотовых ячейках, PCell, было рассчитано на временном шаге, Dt, с использованием уравнения состояния закона идеального газа и в предположении, что ни молекулы воздуха, ни молекулы воды не смещены во время истечения:
2.1. Истечение массы за счет воздухопроницаемости. Воздухопроницаемость сотовой оболочки (включая клей) по толщине является свойством материала, которое можно охарактеризовать путем измерения давления с обеих сторон оболочки при подаче вакуума под мешок [6]. –8,15,16]. Если перепад давления измеряется на стороне обшивки с сотовым заполнителем, взаимосвязанные поры образуют непрерывные пути через обшивку, и в результате обшивки можно считать пористой средой [25,26]. Препреги имеют очень низкие коэффициенты воздухопроницаемости по толщине, в результате чего текучесть ограничивается низкими числами Рейнольдса, Re 10.Поэтому ламинарное течение сжимаемого газа через пористую среду прогнозировалось путем интегрирования дифференциальной формы закона Дарси при постоянной температуре [26]: универсальная газовая постоянная, T – температура, VCell – пустой объем сотового заполнителя, c – массовая доля воздуха и водяного пара в ячейке, x – молярная масса воздуха и водяного пара. Обмен влагой из стенок ячейки в пространство ячейки и проникновение газа через кожу со стороны мешка были разделены и решены с интервалами в 10 с во время обработки при повышенной температуре, как показано на рис.3.
Р7Р
где Q — объемный расход, K — коэффициент проницаемости, A — площадь поперечного сечения, нормального к потоку, l — вязкость жидкости, PBag — давление вакуумного мешка, PCell — давление в соты, h – толщина обшивки. Объемный расход, описываемый уравнением (7) адаптирован для получения _ Bag Skin : массовый расход через кожу мешка, м 2
_ Bag m _ Honeycomb DtÞ Ru T mAir;i ðmVapor þ m ¼ þ V Cell xAir xVapor cc _ Bag Skin Dt Воздух þ Пар; m
2 2 KA PBag PCell ; l 2PBag h
Кожа
¼
2
qKA PBag PCell ; 2lh PBag
ð8Þ
где q — плотность газа.При повышенных температурах для расчета вязкости воздуха и воды в зависимости от температуры использовался закон Сазерленда, а для расчета вязкости смеси применялась полуэмпирическая формула, предложенная Уилке [27]. При дискретизации каждого шага по времени температура и толщина считались постоянными. Обоснование постоянной толщины обшивки представлено в разделе 4.1. 2.2. Приток массы за счет диффузии влаги. Скорость диффузии массы внутри каждого отдельного компонента сэндвич-панели моделировалась с использованием первого закона диффузии Фика:
Дж = Drc;
ð9Þ
Пожалуйста, ссылайтесь на эту статью в прессе следующим образом: Kratz J, Hubert P. Вакуумный мешок только для приклеивания препрега к арамидному сотовому заполнителю. Часть I. Модель и свойства материала для давления в керне во время обработки. Композиты: Часть A (2015), http://dx.doi.org/10.1016/j.compositesa.2014.11.026
4
Дж. Крац, П. Хьюберт / Композиты: Часть A xxx (2015) xxx– xxx
Рис. 3. Подход к моделированию, используемый для прогнозирования давления в сердцевине сот во время обработки.
где J — поток влаги, D — коэффициент диффузии, c — концентрация.Для учета изменения концентрации влаги во времени использовался второй закон диффузии Фика:
@c = Dr2 c; @t
ð10Þ
в предположении, что концентрация влаги и коэффициент диффузии постоянны на каждом временном шаге. Можно предположить, что на коэффициент диффузии не влияют изменения влажности окружающей среды с минимальной ошибкой, однако изменения температуры будут сильно влиять на коэффициент диффузии [28]. Для процессов с изменением температуры T соотношение Аррениуса описывает коэффициент диффузии:
ED ; D = D0 exp Ru T
ð11Þ
где D0 — предэкспоненциальный множитель, ED — энергия активации, Ru — универсальная газовая постоянная. Для упрощения анализа исследователи использовали процентное содержание влаги М вместо концентрации с при моделировании потока влаги в композиционных материалах [21, 28–30]. В результате уравнения (9) и (10) упрощаются до:
J =
Dq @M ; 100 @x
и
@M @2M ¼D 2 : @t @x
ð12Þ
m mD 100; mD
DA qA
@M @M ¼ DB qB : @x A @x B
M ¼ M U Hb ;
ð16Þ
где MU — процент влажности по массе при 100% относительной влажности, H — относительная влажность в процентах, а b — константа.Экспериментальное исследование коэффициентов диффузии для углеродно-эпоксидных покрытий, эпоксидного клея и арамидного сердечника показало, что b = 1 для всех материалов [29]. Учитывая это, уровень влажности на границе раздела сотовых бумажных стенок и полости ячейки был описан как: Из соотношений (12) и (17) с площадью поверхности стенок ячеек сот, через которые происходит поток влаги, для описания оттока влаги из стенок ячеек сот в пустоты ячеек получено следующее выражение:
_ Соты ¼ DqAS m ð14Þ
ð15Þ
В случае композитного материала, подверженного воздействию влажного воздуха, содержание влаги можно описать формулой [28]:
ð13Þ
где m — текущая масса, mD — сухая масса материала, через который диффундирует влага [28]. Сохранение массы между поверхностями поверхностей структур, состоящих из нескольких материалов, требует, чтобы влага, выходящая из материала A, попадала в материал B [21]. Применяя это к уравнению. (12) результаты:
MPaper M Cell ; MU;Paper M U;Cell
ð18Þ
где AS – площадь поверхности сотовых ячеек. Массовый поток влаги из стенок ячеек в пустое пространство сотовых ячеек _ Honeycomb теперь можно предсказать, если максимальное и мгновенное значение m
Пожалуйста, цитируйте эту статью в прессе следующим образом: Kratz J, Hubert P.Вакуумный мешок только для приклеивания препрега к арамидному сотовому заполнителю. Часть I. Модель и свойства материала для давления в керне во время обработки. Композиты: Часть A (2015), http://dx.doi.org/10.1016/j.compositesa.2014.11.026
5
Дж. Крац, П. Хьюберт / Композиты: Часть A xxx (2015) xxx– xxx
Допущения использовались для упрощения анализа сотовой модели внутреннего давления. Возможное влияние допущений на точность модели обсуждается ниже. 2.3.1. Давление из-за скорости В этой модели пренебрегалось влиянием скорости газа через оболочку сотового заполнителя на давление в сердцевине сотового заполнителя.Число Рейнольдса (Re) оценивалось между 0,01 и 0,6 по формуле:
Re =
qlv ; l
ð19Þ
где q – плотность потока, l – расчетная длина, v – скорость потока, l – вязкость смеси. За референтную длину принимали диаметр волокна [31]. 2.3.2. Идеализация реального газа В формулу внесена ошибка. (6) путем упрощения поведения реального газа, такого как воздух и водяной пар, с помощью уравнения состояния идеального газа. Погрешность зависимости давление–объем–температура возрастает по мере приближения к критическому давлению.Для обработки VBO максимальное давление в керне не может превышать максимальное давление консолидации 1000 мбар. В результате закон идеального газа имеет максимальную ошибку 1,6 % для обработки VBO, которая происходит при 100 °C и 1000 мбар [32]. Выше 100 °С погрешность уменьшается. При более низких давлениях в керне, возникающих при обработке VBO, потенциальная ошибка до 1,6% считалась незначительной и была принята, чтобы избежать использования справочных таблиц пара. 2.3.3. Диффузия в стоячую среду Ошибка вводится в модель с помощью уравнения.(18) для описания массового потока влаги со стенок клетки в пустотное пространство клетки. Линейная зависимость, предложенная Фиком [33], описывает скорость массовой диффузии одного химического вещества в застойную среду другого химического вещества на основе локального градиента концентрации. Среда в пустотном пространстве ячейки не стояла на месте, а двигалась по уравнению. (8), с числом Рейнольдса, оцененным между 0,01 и 0,6 в разделе 2.3.1. Выбор застойной среды в пустом пространстве значительно упростил анализ массопереноса и экспериментальную характеристику.Это допущение следует пересмотреть, если используются сотовые покрытия со значительно большей воздухопроницаемостью по толщине, так как газ в ячейке может не застаиваться. 2.3.4. Коэффициент влагообмена Тонкие арамидные сотовые стенки (75 мкм) были смоделированы с использованием коэффициента обмена в уравнении. (17), поэтому характеристика не является свойством объемного материала.
Для простоты не рассматривался градиент концентрации внутри клеточных стенок или пустот клеточного пространства, вместо этого считалось, что влага равномерно распределяется внутри клеточной стенки толщиной 75 мкм и внутри 3.Пустое пространство диаметром 2 мм. Влагообмен происходил в течение короткого промежутка времени, для более длительных диффузионных процессов толстостенных ядер это следует пересмотреть. 3. Материалы В этом исследовании использовался препрег OoA от Cytec Engineered Materials: Cycom® 5320 T650-35 3K полотняного переплетения с номинальной массой ткани 196 г/м2 и начальным содержанием смолы 36% по массе. Сотовый заполнитель изготовлен из арамидной бумаги
4. Характеристика сотовой оболочки Препреги OoA деформируются в процессе обработки, поскольку представляют собой трехфазные материалы: твердая волокнистая сеть, частично пропитанная высоковязкой несжимаемой смолой, и сжимаемый газ.Закон Дарси можно использовать для характеристики воздухопроницаемости сотовой оболочки, если волокна и высоковязкая смола (включая клейкую пленку) считать жесткой пористой средой, а воздух считать единственной проникающей жидкостью [4,17]. В уравнении (7) предполагалось, что воздух является единственной проникающей жидкостью. На рис. 1 представлена идеализированная схема сотовой оболочки до и после отверждения, и ясно, что воздух не является единственной проникающей жидкостью. Смола и клей растекаются в процессе отверждения, что приводит к уплотнению пор и уменьшению толщины пленки.Следовательно, уравнение (7) считалось действительным только в том случае, если толщина порового пространства оставалась постоянной во время измерений проницаемости. 4.1. Метод пошаговой температурной характеристики Целевой температурный профиль был выбран из таблицы данных производителя: от 1,7 °C/мин до 121 °C [34]. Пример температуры кожи во время обработки показан на рис. 4, а поведение вязкости смолы и клейкой пленки прогнозируется на основе моделей, чтобы показать ключевые параметры процесса, такие как минимальная вязкость и гелеобразование [35].Воздухопроницаемость препрега была охарактеризована путем выполнения в общей сложности тринадцати измерений в течение цикла обработки на рис.
4. Значительные изменения толщины пленки, вероятно, происходили во время изменения температуры на 1,7 °C/мин от температуры окружающей среды до выдержки 121 °C с момента повышения температуры. является основным механизмом снижения вязкости при низких степенях отверждения [35], а меньшая вязкость увеличивает скорость пропитки жгута [36]. При использовании этого цикла отверждения для этого препрега ожидалось полное насыщение жгута или отсутствие дальнейшего уменьшения толщины при температуре около 90 °C [36].Поэтому был предложен профиль приращения температуры до 100 °C, чтобы охарактеризовать воздухопроницаемость сотового покрытия со смолой при постоянной вязкости 11
12
13
1E + 05
100 6
1e + 04 80 5
1E + 03
1E + 03
60
4
1E + 02
40 20
3
Вязкость ( Па·с)
2.3. Предположения и ограничения модели
Толщина 20 мм, диаметр ячейки 3,2 мм, плотность 96 кг/м3. Для сравнения также использовался алюминиевый сотовый заполнитель с идентичными размерами и плотностью. Клейкая пленка представляла собой AF 163-2K от 3M и имела плотность 294 г/м2. Сотовые покрытия состояли из четырех слоев препрега, уложенных друг на друга под углом 0°, и одного слоя клея. Разделительная пленка с перфорацией 0,38 мм, расположенной в шахматном порядке на 6,35 мм в виде квадрата, была помещена между обшивкой со стороны мешка и полиэстеровым дышащим материалом плотностью 340 г/м2.
Температура (C)
Известно содержание влаги в стенах и можно ли рассчитать давление насыщения водяного пара.
1E + 01 1
0 -16 Lay-Up
2
1e + 00 0
1E + 00 0
Температура кожи
1
2
3
2
4
3
5
4
5
Время (H) вязкость
Вязкость смолы
Рис. 4. Целевой цикл обработки при повышенной температуре с указанием мест измерения воздухопроницаемости, профилей смолы и вязкости.
Пожалуйста, цитируйте эту статью в прессе следующим образом: Kratz J, Hubert P. Вакуумный мешок только для совместного склеивания препреговой оболочки с арамидным сотовым заполнителем. Часть I. Модель и свойства материала для давления в керне во время обработки. Композиты: Часть A (2015), http://dx.doi.org/10.1016/j.compositesa.2014.11.026
6
Дж. Крац, П. Хьюберт / Композиты: Часть A xxx (2015) xxx– xxx
ограничение изменения толщины при постоянной температуре. Предлагаемый добавочный температурный профиль кожи показан на рис.5. Первое измерение воздухопроницаемости началось при первоначальном запуске вакуумного насоса для вакуумной выдержки предварительного отверждения, в момент времени t = 16 ч; производитель рекомендует проводить предварительную обработку в вакууме в течение 16 ± 0,5 ч при комнатной температуре перед любой обработкой при повышенной температуре [34]. Второе измерение воздухопроницаемости было проведено за 30 минут до обработки при повышенной температуре, чтобы оценить любые изменения воздухопроницаемости во время вакуумной выдержки. Последующие измерения проводились при повышенных температурах с интервалом 20 °С, вплоть до 100 °С. Последнее измерение инкрементной проницаемости было проведено при 100 °C, поскольку клей превратился в гель, а вязкость смолы увеличивалась в сторону гелеобразования. Следовательно, любые дальнейшие измерения этих образцов при 121 °C должны были выполняться со смолой и клеем в условиях, отличных от температурного профиля, показанного на рис. 4. В результате измерения проницаемости с седьмого по тринадцатое были выполнены непосредственно при 121 °C. C с использованием профиля, показанного на рис. 4.
4.2. Микро-КТ-изображение сотовой оболочки Ступенчатое увеличение температуры дало возможность прервать эксперимент, когда должно было быть выполнено измерение проницаемости.Метки X на рис. 5 показывают, когда кожа подвергалась закалке для анализа микроструктуры и измерения толщины кожи. Система Skyscan 1172 High-Resolution Micro-CT использовалась для сканирования образца при каждом измерении проницаемости на рис. 4 [38]. Закалку при отверждении выполняли путем извлечения приспособления для испытаний из печи и помещения алюминиевого блока с температурой 10 °C поверх вакуумного мешка при поддержании вакуума. Температура кожи падала ниже температуры окружающей среды в течение 2–3 мин, что приводило к остановке потока смолы. Образец размером 18 мм 18 мм вырезали из центра испытательной панели и сканировали.Репрезентативные микро-КТ-изображения сотовой оболочки показаны на рис. 6. На каждом изображении показаны четыре слоя препрега, слой клея и часть сотового заполнителя. На сканах видны насыщенные смолой области (бледно-серые), сухие волокна (темно-серые эллипсы), захваченные летучие вещества или макропоры (черные области) и клейкая пленка (светлые области). Снимки микро-КТ показали, как поры кожи изменялись в процессе обработки. Видимые макропустоты между слоями уменьшились, что свидетельствует об эвакуации воздуха из кожи, а пропитка жгутом наблюдалась по уменьшению видимых участков сухих волокон.Захваченный воздух, присутствующий после 1 часа вакуума (рис. 6а), в основном исчезает через 16 часов (рис. 6b) и полностью исчезает при 40 ° C (рис. 6c). При температуре до 60 °C (рис. 6d) хорошо видны жгуты сухих волокон, что указывает лишь на незначительное течение смолы.
Адгезивная пленка начинает затекать в кожу и формирует галтели на границе кожи и сердцевины. При 80 °C (рис. 6e) текучесть смолы увеличила насыщение жгута до 75–100 %, а клей образовал галтели. На рис. 6д видны некоторые межслоевые пустоты. Они, вероятно, образовались во время предыдущих измерений воздухопроницаемости при более низких температурах и указывают на возможность образования межламинарных пустот, если поток газа происходит одновременно с потоком смолы [37].Жгуты волокон полностью насыщаются при 100 °C, и в клеевой пленке не наблюдается никаких изменений (рис. 6f). Процент липкой пленки в коже измеряли непосредственно с помощью функции трехмерного анализа программного обеспечения Skyscan CTAn. Граница кожи определялась как центр жгутов в препреге, примыкающий к клеевому слою на рис. 6. Вязкость клея была достаточно высокой, чтобы предотвратить проникновение в кожу до 60 °C. Однако при 80 °С содержание клея в коже удваивалось и оставалось постоянным до 100 °С.Результаты микро-КТ приведены в таблице 1.
Наиболее значительное изменение толщины произошло при температуре около 80 °C, так как толщина кожи изменилась на 11%. Учитывая, что все другие измерения показывают менее 4% возможного изменения между температурами, они считались постоянными во время характеристики проницаемости. При расчете проницаемости при температуре 80 °C возможна некоторая ошибка из-за изменения толщины, однако этот подход был наилучшим возможным вариантом для измерения проницаемости во время линейного изменения температуры.Поток смолы в коже при каждом ступенчатом измерении воздухопроницаемости определяли количественно путем измерения степени пропитки по данным микро-КТ. Степень пропитки b рассчитывали, наблюдая за уменьшением видимой площади жгута сухого волокна на последовательных микро-КТ: ATow
ð20Þ
1E+06
, где AVisible — видимая площадь сухого жгута, а ATow — общая площадь жгута волокна. Измеренная степень пропитки по данным микро-КТ представлена в таблице 1 и сравнивается с предсказаниями модели в соответствии с циклом отверждения, представленным на рис. 4. Предсказанная степень пропитки была рассчитана с использованием модели, представленной Centea и Hubert [36] для того же материала препрега полотняного переплетения Cycom® 5320, который использовался в этом исследовании. Близость измеренных и рассчитанных значений подтвердила, что пошаговый подход к расчету воздухопроницаемости во время линейного изменения не изменил динамику пропитки целевого цикла отверждения.
1E+05
4.3. Измерения воздушной проницаемости толщины толщины
120
6
6
5
1e + 04
80 1e + 03
80 1e + 03
80 1E + 03
60 4
1E + 02
40
Вязкость (PA ens a}
C)
100
3
1E + 01
20 1
0 -16
2
1E + 00 0
1E + 00 0
1
2
3
4
3
5
4
6
Время (ч) Температура кожи
Вязкость смолы
Воздухопроницаемость сотовой кожи была охарактеризована с использованием экспериментальной установки, основанной на работе Tavares et al. [4,6,14–16]. Схема установки показана на рис. 7. Ячеистая обшивка была 200 мм × 200 мм, а сердцевина — 150 мм × 150 мм × 60 мм. Прибор измерял градиент давления на коже: давление в вакуумном мешке, PBag, с одной стороны, и давление в ячеистой сердцевине, PCell, с другой стороны. Если давление в сердцевине сот уменьшалось при применении вакуума, это было результатом потока через кожу. Поскольку объем воздуха, проходящего через кожу, пропорционален уменьшению давления в сердцевине сот, объемный расход выражался как:
Вязкость клея
Рис.5. Предлагаемые дополнительные измерения температурной проницаемости для участка технологического цикла при уменьшении толщины корки.
Q =
dP V Ячейка: dt PCell
ð21Þ
Пожалуйста, цитируйте эту статью в прессе следующим образом: Kratz J, Hubert P. Вакуумный мешок только для приклеивания препрега к арамидному сотовому заполнителю. Часть I. Модель и свойства материала для давления в керне во время обработки. Композиты: часть A (2015 г. ), http://dx.doi.org/10.1016/j.compositesa.2014.11.026
7
J.Kratz, P. Hubert / Composites: Part A xxx (2015) xxx–xxx
Рис. 6. Микро-КТ-изображения сотовой оболочки для первых шести измерений проницаемости на рис. 4: (a) 1 ч в вакуумной выдержке , (b) 16 ч в вакуумной выдержке, (c) 40 °C, (d) 60 °C, (e) 80 °C и (f) 100 °C.
Таблица 1 Микро-КТ характеристика дополнительных измерений проницаемости. Измерение проницаемости
Измерено b
Прогнозировано b с использованием модели из [36]
Измерено содержание адгезива (%)
Толщина кожи (мм)
Изменение толщины (%)
Изображение микро-КТ на рис.6
1 2 3 4 5 6
1 2 3 4 5 6
0,05 ± 0,012 0,11 ± 0,013 0,012 0,027 0,32 ± 0,019 0,82 ± 0,011 1,00 ± 0,05 0,82 ± 0,011 0,05 0,05 0,10
0,05 0,05 0,10 0,30 0,87 1.00
1.1 2.5 2.4 2.8 6.1 5,9
1.28 1.25 1.25 1,20 1,08 1,05
Номинальная 2 0 4 11 3
(a) (b) (c) (d) (e) (f)
Подставляя уравнение (21) в уравнение. (7) для закона Дарси дает:
KA dPCell 2 ¼ : HLV Cell dt P2Bag P2Cell
ð22Þ
Интегрируя уравнение. (22) как функция времени от 0 до t дает:
ln
ðP Bag þ PCell;i ÞðP Bag PCell Þ KAPBag t; ¼ ðP Bag PCell;i ÞðP Bag þ PCell Þ Ячейка HLV
ð23Þ
где t – время, PCell,i – начальное давление в сердцевине соты.Левая часть уравнения. (23) линейно зависит от времени t, и по этой причине при построении графика зависимости от времени наклон прямой линии представляет собой воздухопроницаемость [39]. В течение 16 ч вакуумной выдержки перед обработкой давление в сердцевине сот снижалось до уровня вакуума в мешке, как показано на рис. 8. Время до начала снижения давления варьировалось от 1 до 7 ч. Это недарсианское поведение наблюдалось ранее [14, 17] и может быть связано со временем, необходимым градиенту давления между сердцевиной и мешочком кожи, чтобы деформировать смолу и создать каналы для потока через кожу. особенно клейкая пленка.Задержка в падении давления
указывает на то, что никакая взаимосвязанная поровая сеть не была доступна для потока, когда первоначально применялся вакуум. Во время длительной вакуумной выдержки градиент давления формирует новые каналы потока, а давление в сотах уменьшается до тех пор, пока давление консолидации вакуумного мешка не превысит градиент давления и не закроет канал. В результате на рис. 8 показано изменение начала падения давления и конечного давления в керне. Восстановить эти каналы было проще во время обработки при повышенной температуре, поскольку наблюдалась минимальная задержка в ответе на давление сердцевины сот во время последующих измерений воздухопроницаемости при повышенной температуре.После предварительной вакуумной выдержки в полость активной зоны через клапан снова вводился атмосферный воздух и проводились дальнейшие измерения проницаемости. Данные о давлении в сотовом заполнителе, использованные для расчета воздухопроницаемости по толщине, показаны на рис. 9. Резкое падение давления в сотовом заполнителе на ранних этапах измерений при температуре 80–121 °C произошло из-за высокой подвижности смолы. Внезапное увеличение давления в керне вызвало смещение смолы до того, как наблюдалось стационарное поведение давления.
Аналогичный ответ наблюдали Tavares et al. [6]
Пожалуйста, цитируйте эту статью в прессе как: Kratz J, Hubert P. Вакуумный мешок только для совместного склеивания препреговой оболочки с арамидным сотовым заполнителем. Часть I. Модель и свойства материала для давления в керне во время обработки. Композиты: Часть A (2015 г.), http://dx.doi.org/10.1016/j.compositesa.2014.11.026
8
Дж. Крац, П. Хьюберт / Композиты: Часть A xxx (2015) xxx– XXX
Датчик давления давления
Вакуумный насос
вакуумный насос Вакуумная сумка герметичная лента резетят пленка
PHAM
PCELL
капиллярная трубка
Датчик давления давления
Уплотнение диафрагмы
Клапан конвекции
.7. Схема измерительного приспособления, используемого для измерения давления в сердцевине сотового заполнителя во время обработки. (Для интерпретации ссылок на цвет в подписи к этому рисунку читатель отсылается к веб-версии этой статьи).
0
0
4
8
12
16
между этими измерениями считались существенно разными и не вычислялись (обозначены –) в таблице 2.Повышение температуры от комнатной до 100 °C оказывает статистически значимое влияние на проницаемость сотового покрытия. Наиболее значительное изменение проницаемости кожи произошло при воздействии тепла от 40 до 80 °C (увеличение проницаемости). Другие статистически значимые увеличения проницаемости включали измерения между 40 и 60 °C и 40–100 °C. Также было измерено статистически значимое снижение проницаемости между измерениями в условиях окружающей среды и нагреванием до 40 °C, а также изменение состояния смолы с жидкого на гелеобразное (снижение проницаемости).Несмотря на то, что была обнаружена значительная разница между измерениями проницаемости как в окружающей среде, так и при 40 °C, измерения проницаемости до и после 16-часовой вакуумной выдержки существенно не отличаются. Вероятность ошибиться и сделать вывод о значимой разнице превышает 5 %.
Время, ч
при повторном вводе воздуха в активную зону. Они наблюдали более высокую воздухопроницаемость при использовании более высоких уровней внутреннего давления.В результате мы пренебрегаем резким падением давления в первые минуты после начала измерения проницаемости при повышенной температуре и рассчитываем только сквозную воздухопроницаемость из стационарного диапазона данных, указанного на рис. 9. Весь воздух Измерения проницаемости и среднее значение приведены на рис. 10 для целевого цикла отверждения с рис. 4. Ключевые события в производственном процессе показаны на рис. 10: A – окончание предварительной отверждения в вакууме в момент времени t = 0,5 ч, B – сухие жгуты полностью пропитаны, С – гели адгезивной пленки, Г – гели смолы.4.3.1. Дисперсионный анализ (ANOVA) данных теста проницаемости Непараметрический однофакторный дисперсионный анализ Крускала-Уоллиса по рангам был выполнен с использованием SigmaPlot 12.3. Результаты нисходящей разности рангов между измерениями проницаемости представлены в Таблице 2. Стьюдентизированный диапазон и P-значения также были рассчитаны, чтобы определить, была ли разница между измерениями статистически значимой. Порог P-значения был установлен на уровне 5%, чтобы сделать вывод о значительной разнице между двумя измерениями.Если разница в суммах рангов двух измерений была менее 5%, то P-значения измерений в
4.3.2. Интерпретация измерений проницаемости После 16-часовой вакуумной выдержки наблюдалось снижение средней воздухопроницаемости, хотя между измерениями не наблюдалось статистически значимой разницы. Повторное рассмотрение тепловых свойств на рис. 4 и изображений микро-КТ на рис. 6 может дать некоторое качественное представление. Вязкость оставалась постоянной, но на рис.6а и б показано, что за это время кожа была уплотнена за счет сочетания перераспределения волокон и потока смолы в макропустоты вокруг жгутов. В результате поровое пространство уменьшилось, и ожидалось, что воздух в сердцевине будет испытывать большее сопротивление потоку. При повышении температуры до 40 °С вязкость смолы и клея уменьшалась на порядок (рис. 4), но заметного увеличения степени пропитки жгута не наблюдалось (рис. 6в) и не измерялось (табл. 1) от изображения микро-КТ.Тем не менее, статистически значимое снижение воздухопроницаемости по толщине наблюдалось при обоих измерениях окружающей среды. Аналогичное поведение наблюдали Tavares et al. [6], и они предполагают, что снижение воздухопроницаемости было вызвано тем, что смола заполнила небольшие воздушные пути. Измеренные данные в текущем исследовании подтверждают эту точку зрения. Смола и клей становятся более липкими при 40 °C и препятствуют образованию каналов для тока через кожу. При 60 °C вязкость смолы и клея снова уменьшилась примерно на порядок (рис.4). Уменьшение вязкости смолы вызвало растекание (рис. 6d) и увеличение жгута. Часть I. Модель и свойства материала для давления в керне во время обработки. Композиты: Часть A (2015), http://dx.doi.org/10.1016/j.compositesa.2014.11.026
9
Дж. Крац, П. Хьюберт / Композиты: Часть A xxx (2015) xxx– xxx
1000 800 Данные
600 400 Данные
200
200
~ 21 ° C Начальный вакуумный удержание
40 ° C
Соточное давление сот (мбар)
0 1000
Данные
800 600
Данные
400 200 60 ° C
400 200 60 ° C
80 ° C
0 1000 ° C
0 1000
Данные
Данные
800 600 400 200 100 ° C
120 ° C
0 0
5
10
15
20
25
25
30
0
0
5
10
15 20002 10
15
20
25
30
Время (мин) Рис. 9. Данные о давлении в сотовом керне во время предварительной обработки и измерений проницаемости при повышенной температуре. Для каждой температуры указан диапазон данных, используемых для расчета сквозной воздухопроницаемости.
125
125
100 1.0e-17 75
50 1.0e-18
50 1.0e-18
Температура (C)
Проницаемость, K (M 2)
1.0e-16
25 A
B
C
D
1.0e-19
0
0
-16 Укладки
0
0
Измеренный K
1
2
3
Время (H) Средняя температура K
Рис.10. Изменение воздухопроницаемости кожи при обработке при повышенной температуре. пропитка
(табл. 1). Несмотря на то, что микропористость внутри оболочки препрега уменьшилась, воздухопроницаемость увеличилась статистически значимым образом. Это снова наблюдалось при 80 °C, вызывая наибольший рост степени пропитки (таблица 1) и пик воздухопроницаемости по толщине (рис. 10). Повышение воздухопроницаемости связывали с подвижностью смолы с меньшей вязкостью при
более высоких температурах [6].При меньшей вязкости смола находится в благоприятном состоянии для формирования каналов течения через кожу, однако, когда степень пропитки достигает единицы при 100 и 121 °С, воздухопроницаемость по толщине снижается (рис. 10). ), но не было статистически значимым по сравнению с измерениями при 80 °C. 4.3.3. Эффекты Клинкенберга (скольжение) Поток газа при низком давлении газа или среде с низкой проницаемостью может завышать скорость потока из-за явления скольжения, известного как эффект Клинкенберга [40].Скольжение Клинкенберга наблюдалось при использовании газа для измерения проницаемости сухих тканей [41], где проницаемость на 4–5 порядков выше, чем у препрегов ОоА. Зависимостью кажущейся проницаемости от градиента давления пренебрегали, поскольку измерения воздухопроницаемости не использовались для собственной проницаемости ткани; измерения воздухопроницаемости проводились в условиях, соответствующих реальному производственному процессу, который мы моделируем. 5. Характеристика арамидного сердечника Как арамидные, так и алюминиевые сердечники кондиционировались при температуре окружающей среды 21 ± 2 °C и четырех уровнях влажности: 12 %, 30 %, 70 %,
Пожалуйста, цитируйте эту статью в прессе следующим образом: Kratz J, Hubert П.Вакуумный мешок только для приклеивания препрега к арамидному сотовому заполнителю. Часть I. Модель и свойства материала для давления в керне во время обработки. Композиты: Часть A (2015), http://dx.doi.org/10.1016/j.compositesa.2014.11.026
10
Дж. Крац, П. Хьюберт / Композиты: Часть A xxx (2015) xxx– xxx
Таблица 2 Дисперсионный анализ данных проницаемости (ANOVA).
7 P
5 против 3 5 против 10 1 против 3 5 против 2 4 против 3 6 против 3 5 против 8 5 против 9 1 против 10 4 против 10 5 против 7 6 против 10 1 против 2 7 против 3 4 против 2 1 против 8 6 против 2 1 против 9 4 против 8 6 против 8 4 против 9 6 против 9 9 против 3 8 против 3 1 против 7 5 против 6 7 против 10 5 против 4 2 против 3 4 против 7 6 против 7 5 против 1 7 против 2 10 против 3 9 против 10 7 против 8 8 против 10 7 против 9 9 против 2 2 против 10 1 против 6 8 против 2 1 против 4 9 против 8 4 против 6
58. 1880 46.5630 45,4170 42,1880 42,0500 41,2500 38,5210 37,6040 33,7920 30,4250 30,1380 29,6250 29,4170 28,0500 26,0500 25,7500 25,2500 24,8330 22,3830 21,5830 21,4670 20,6670 20,5830 19,6670 17,3670 16,9380 16,4250 16,1380 16,0000 14,0000 13,2000 12,7710 12,0500 11,6250 8,9580 8,3830 8,0420 7,4670 4,5830 4,3750 4,1670 3,6670 3,3670 0,9170 0,8000
5,2790 3,2720 4,5650 17890 1.5990 1.7150 1.6390 1.4040 1.4080 1.0540 1.4640 1.6080 1.1000 0.9700 1.2970 0.9740 0.9760 0.5970 0.5960 0.5360 0.5310 0.3940 0.3260 0.3770 0.3160 0.3380 0.0683 0.0699
Да Да Да Да Да Да Нет — Нет — — — — Нет — — — — — — — — — — Нет — — — — — — — — — — Нет — — — — — — — — — — Нет — — — — — — — — — — Нет — — — — — — — — — — Нет » – – – – – – – – – – – – – – – – – – – –
TAокр. = 21 ± 2 °C
6 5 4
y = 0,057x + 0,41 R² = 0,99
3 2 1 0 0
20
40
60
80
100
Относительная влажность окружающей среды (%) Арамидный сердечник
Алюминиевый сердечник Рис. 11. Равновесная влажность арамидных и алюминиевых сотовых заполнителей.
125 1000 3,45 мас.% 100
800
600
2,34 мас.%
400
1,28 мас.%
75
75
50
Температура (C)
Учебный диапазон
Содержание влаги (мас.%)
Разница в рангах
Сотовое давление сота (MBAR)
Измерение (см. Рис. 4)
25
200 0,2 мас.% 0
0 0
1
2
3
4
5
Время (ч) Арамидный сердечник
Подходит для модели
Алюминиевый сердечник
Температура
Рис.12. Измерено давление заполнителя сотового заполнителя в герметичном объеме при обработке при повышенной температуре.
и относительной влажности 99%. Шесть образцов сот первоначально были высушены в конвекционной печи при 180 °С до изменения веса менее 0,01 мас.%. После сушки образцы ежедневно взвешивали до изменения влажности менее 0,05 мас.%. Предельное содержание влаги в сердечнике и его стандартное отклонение представлены на рис. 11. Содержание влаги, поглощаемое арамидными сердечниками, увеличивалось линейно с влажностью окружающей среды, что указывает на то, что арамидное сердечник, использованный в этом исследовании, имело диффузионное поведение Фика.Алюминиевые сердечники поглощали 0,2% влаги по весу при всех уровнях влажности, показывая, что они нечувствительны к влажности окружающей среды. Константы для коэффициентов диффузии Аррениуса влажности ядра (DO и ED), необходимые для уравнения. (11) были получены путем кондиционирования отдельных образцов керна при трех уровнях влажности и нагревания кондиционированных влагой образцов в полости приспособления
, показанного на рис. 7. вместо проницаемой оболочки препрега._ Bag Skin = 0, и единственный неизвестный член, необходимый для В результате, m предсказывает PCell в уравнении. (6) был коэффициент диффузии из уравнения. (18). Прогнозируемое давление в сотовой ячейке нанесено на график вместе с измеренной реакцией давления на рис. 12 с использованием констант аппроксимации кривой DO = 7,2 · 101 м2/с и ED = 3,8 · 104 кДж/кг с подгонкой R2 > 0,99. В результате модель давления в сердцевине может предсказать давление в ячейке на 6 % при самом низком испытанном уровне влажности и на 1 % при самом высоком уровне влажности. Кривая давления в алюминиевом сердечнике построена для справки, подтверждая, что рост давления, наблюдаемый с арамидными сердечниками, действительно исходит от сердечника и не является артефактом испытаний.
Таблица 3 Параметры материала и процесса, влияющие на давление заполнителя сотового заполнителя. Параметр
Тип
Значение
KD PBag MPPaper PExt
Свойство материала Свойство материала Условие процесса Условие процесса Условие процесса
Снижает Pcore, пропуская газ через оболочку со стороны мешка PCore в начале обработки при повышенной температуре на основе K и времени.Влияет на массу водяного пара, вводимого в пустое пространство ячейки. Применяет давление консолидации к сотовому заполнителю. Часть I. Модель и свойства материала для давления в керне во время обработки. Композиты: часть A (2015 г.), http://dx.doi.org/10.1016/j.compositesa.2014.11.026
J. Kratz, P. Hubert / Composites: Part A xxx (2015) xxx–xxx
Сердечники кондиционировали только до уровня влажности 3.45 мас.%, поскольку более высокие уровни превышают давление уплотнения (1000 мбар), обеспечиваемое вакуумным мешком. Содержание влаги в сердцевине 3,45 мас. % было поглощено при относительной влажности 55 % и температуре 22 °C, и большинство промышленных складских помещений настроены примерно на этот уровень, от 30 % до 70 % относительной влажности. Это подчеркивает, сколько влаги может быть поглощено арамидными сердцевинами, и последующее повышение давления, которое может произойти во время обработки. 6. Резюме Модель процесса была разработана для прогнозирования давления в сотовом заполнителе во время совместного соединения препрегов вне автоклава (OoA) с сотовыми заполнителями с использованием только вакуумного мешка (VBO).В модели предполагалось, что поток в пространство ячейки представляет собой влагу, диффундирующую из сотового заполнителя, а поток из пространства ячейки определяется воздухопроницаемостью стенки мешка по толщине. Свойства материала и параметры процесса, влияющие на давление внутри сотового заполнителя, можно определить по уравнениям. (8) и (18), и они перечислены в таблице 3. Было представлено экспериментальное исследование, чтобы охарактеризовать свойства материала, необходимые для модели. Прибор для измерения давления был использован для характеристики воздухопроницаемости (K) обшивки сотового заполнителя по толщине и коэффициента влагообмена сердцевины (D).Арамидные сердцевины были кондиционированы для измерения равновесного содержания влаги (MPaper) и продемонстрировали зависимость диффузии Фика. Во второй части этой работы прогнозы с использованием модели и свойств материалов, представленных здесь, сравниваются с измерениями давления на месте в репрезентативных сэндвич-панелях во время производства. Условия процесса, представленные в таблице 3, варьируются, чтобы определить, являются ли допущения модели и характеристика свойств материала оболочки со стороны мешка реалистичной методикой определения характеристик многослойных сотовых структур, имеющих оболочки как со стороны инструмента, так и со стороны мешка.
Благодарности Эта работа была выполнена в рамках проекта COMP-1 Консорциума исследований и инноваций в аэрокосмической отрасли Квебека (CRIAQ). Дополнительную финансовую поддержку оказали Канадский совет по естественным наукам и инженерным исследованиям (NSERC) и промышленные партнеры Bell Helicopter Textron Canada, Bombardier Aerospace и Delastek. Мы признательны Timotei Centea за помощь в микро-КТ, а также Meysam Rahmat и Arthur Levy за содержательные обсуждения моделирования. Ссылки [1] Кэмпбелл ФК.Технология изготовления аэрокосмических конструкционных материалов. Нью-Йорк: Эльзевир; 2006. [2] Гроув С.М., Пофэм Э., Майлз М.Э. Исследование связи между оболочкой и сердцевиной в многослойных сотовых конструкциях с использованием методов статистического эксперимента. Compos A: Appl Sci Manuf 2006; 37 (5): 804–12. [3] Рион Дж., Штутц С., Летерье Ю., Мэнсон Дж.-А.Е. Влияние технологического давления на локальную неустойчивость лицевого листа для сверхлегких многослойных конструкций. J Sandwich Struct Mater 2009; 11 (4): 293–311.
[4] Tavares SS, Caillet-Bois N, Michaud V, Manson JAE.Вакуумная обработка сэндвич-конструкций: влияние уровня давления сот на адгезию обшивки к заполнителю и качество обшивки. Compos Sci Technol 2010;70(5):797–803. [5] Адвани С.Г., Брушке М.В., Парнас Р. Трансферное формование смолы. В: Адвани С.Г., редактор. Течение и реология в производстве полимерных композитов. Амстердам: Эльзевир; 1994. с. 465–516. [6] Tavares SS, Michaud V, Månson JAE. Воздухопроницаемость препрегов по толщине при отверждении. Compos A: Appl Sci Manuf 2009; 40 (10): 1587–96. [7] Патнэм Дж.В., Сеферис Дж.К.Газопроницаемость препрега в зависимости от ориентации волокон и времени старения. J Adv Mater 1995; 26 (3): 35–41. [8] Шим С.Б., Сеферис Дж.К. Тепловые и воздухопроницаемые свойства препрега на основе углеродного волокна/упрочненной эпоксидной смолы. J Appl Polym Sci 1997; 65 (1): 5–16. [9] Нам Д.Д., Сеферис Д.К. Газопроницаемость и вязкоупругая деформация препрегов в процессах производства композитов. Полим Компос 1995;16(5):370–7.
11
[10] Альтенедер А.В., Ренн Д.Дж., Сеферис Дж.К., Карран Р.Н. Обработка и исследование характеристик сотовых композитных конструкций.Доклад, представленный на 38-м международном симпозиуме и выставке SAMPE, Анахайм, Калифорния, США; 1993. [11] Arafath ARA, Fernlund G, Poursartip A. Транспорт газа в препрегах: модель и эксперименты по проницаемости. В кн.: 17-я Международная конференция по композиционным материалам. Эдинбург, Великобритания; 2009. [12] Louis BM, Hsiao K, Fernlund G. Измерения газопроницаемости внеавтоклавного препрега MTM45-1/CF2426A. В: Конференция и выставка SAMPE 2010, Сиэтл, Вашингтон; 2010. [13] Xin C, Li M, Gu Y, Li Y, Zhang Z. Измерение и анализ воздухопроницаемости в плоскости и по толщине препрега из волокна/смолы.J Reinf Plast Compos 2011;30(17):1467–79. [14] Tavares SS, Caillet-Bois N, Michaud V, Manson JAE. Неавтоклавная обработка сотовых многослойных конструкций: Воздухопроницаемость кожи по толщине при отверждении. Compos A: Appl Sci Manuf 2010; 41 (5): 646–52. [15] Таварес С.С., Мишо В., Мансон JAE. Оценка полупропитанных тканей в многослойных сотовых конструкциях. Compos A: Appl Sci Manuf 2010; 41 (1): 8–15. [16] Sequeira Tavares S, Roulin Y, Michaud V, Månson JAE. Гибридная обработка толстых обшивок для сотовых многослойных конструкций.Compos Sci Technol 2011;71(2):183–9. [17] Kratz J, Hubert P. Анизотропная воздухопроницаемость в препрегах вне автоклава: влияние на эвакуацию сотовых панелей до отверждения. Compos A: Appl Sci Manuf 2013; 49: 179–91. [18] Кюнцер Н., Симачек П., Адвани С.Г., Уолш С. Характеристика проницаемости двухуровневой волокнистой пористой среды. Compos A: Appl Sci Manuf 2006; 37 (11): 2057–68. [19] Сендер Т.А., Симачек П., Адвани С.Г. Пропитка пленкой смолы в тканевых препрегах с проницаемостью по двойной шкале длины. Compos A: Appl Sci Manuf 2013; 53: 118–28.[20] Е.И. Дюпон де Немур и компания. Информация о воздействии влаги и обработке арамидной бумаги. Технический бюллетень H-52744; 2002. [21] Zigrang DJ, Bergmann HW.
Реакция сэндвич-панелей из графита/эпоксидной смолы на воздействие влаги и температурных переходных процессов. J Spacecraft Rockets 1980; 17: 219–25. [22] Симачек П., Адвани С.Г. Желательные функции моделирования заполнения форм для процессов литья жидких композитов. ПолимКомпос 2004;25(4):355–67. [23] Леви А., Крац Дж., Хьюберт П. Откачка воздуха во время обработки препрега сотовых сэндвич-структур только вакуумным мешком: отвод воздуха в плоскости перед отверждением.Compos A: Appl Sci Manuf 2015; 68: 365–76. [24] Bond GG, Hahn GL, Jost KM, Storage T. Неавтоклавная технология производства препрега: обзор программы и средства совместного отверждения для разрушительного, повсеместного использования. SAMPE J 2012;48(5):8–15. [25] Беар Дж. Динамика жидкостей в пористых средах. Нью-Йорк: американский паб Elsevier. Ко; 1972. [26] Дюллиен ФАЛ. Пористые среды: перенос жидкости и структура пор. Нью-Йорк: Академическая пресса; 1979. [27] Уилке К.Р. Уравнение вязкости газовых смесей. J Chem Phys 1950;18(4):517–9.
[28] Shen C-H, Springer GS. Влагопоглощение и десорбция композиционных материалов. J Compos Mater 1976; 10 (1): 2–20. [29] Гаррет Р.А., Болманн Р.Э., Дерби Э.А. Анализ и испытание сэндвич-панелей из графита/эпоксидной смолы, подвергающихся внутреннему давлению из-за поглощенной влаги. В: Винсон Дж. Р., редактор. Усовершенствованные композитные материалы – воздействие на окружающую среду. Филадельфия (Пенсильвания): Американское общество тестирования материалов; 1978. с. 234–53. [30] Таттл М.Е. Диффузия влаги в сэндвич-композитах с сотовым заполнителем.В кн.: 17-я Международная конференция по композиционным материалам. Эдинбург, Великобритания; 2009. [31] Померой Р., Гроув С., Саммерскейлс Дж., Ван Ю., Харпер А. Измерение проницаемости стекловолоконного армирующего мата из непрерывных нитей при насыщенном радиальном воздушном потоке. Compos A: Appl Sci Manuf 2007; 38 (5): 1439–43. [32] Ченгель Ю.А. Тепломассоперенос: практический подход. Бостон: Макгроу-Хилл; 2007. [33] Фик А.В. О диффузии жидкости.
Philos Mag Ser 4 1855; 10 (63): 30–9. [34] Специально разработанные материалы Cytec. Упрочненная эпоксидная смола CYCOM 5320 для структурных применений, производство вне автоклава.Информационный лист редакция 1.3 – 18.03.09. [35] Kratz J, Hsiao K, Fernlund G, Hubert P. Тепловые модели для MTM45-1 и Cycom 5320 смол препрега вне автоклава. J Compos Mater 2013; 47 (3): 341–52. [36] Сентеа Т., Хьюберт П. Моделирование влияния свойств материала и параметров процесса на пропитку жгута в препрегах вне автоклава. Compos A: Appl Sci Manuf 2012; 43 (9): 1505–13. [37] Cender T, Gangloff Jr J, Simacek P, Advani S. Сокращение пустот во время обработки термореактивного препрега вне автоклава.SAMPE tech 2014. Сиэтл, Вашингтон; 2014. [38] Centea T, Hubert P. Измерение пропитки препрега вне автоклава с помощью микро-КТ. Compos Sci Technol 2011;71(5):593–9. [39] Li H, Jiao JJ, Luk M. Метод падающего давления для измерения воздухопроницаемости асфальта в лаборатории. Дж. Гидрол 2004; 286 (1–4): 69–77. [40] Ву Ю.