Температура плавления базальта: горная порода, характеристика, температура плавления, структура
горная порода, характеристика, температура плавления, структура
БАЗАЛЬТ (лат. basaltes, basanites, от греч. basanos — пробный камень; по другой версии, от эфиоп. basal — железосодержащий камень * англ. basalt, basaltic rocks; нем. Basalt; франц. basalte; испанс. basalto) — излившаяся кайнотипная основная порода, эффузивный аналог Габбро. Окраска базальта тёмная до чёрной. Состоит главным образом из основного плагиоклаза, моноклинного пироксена, оливина, вулканического стекла и акцессорных минералов — магнетита, ильменита, апатита и др. Структуры базальта — интерсертальная, афировая, реже гиалопилитовая, текстуры — массивная либо пористая, миндалекаменная. B зависимости от крупности зерна различают: наиболее крупнозернистый — Долерит, мелкозернистый — анамезит, тонкозернистый — собственно базальт. Палеотипные аналоги базальта — Диабазы.
Химический состав базальта
Средний химический состав базальта по P. Дэли (%): SiO2 — 49,06; TiO2 — 1,36; Аl2O3 — 15,70; Fe2O3 — 5,38; FeO — 6,37; MgO — 6,17; CaO — 8,95; Na Cодержание SiO2 в базальте колеблется от 44 до 53,5%. По химическому и минеральному составу выделяют оливиновые ненасыщенные кремнезёмом (SiO2 около 45%) базальты и безоливиновые или c незначительным содержанием оливина слабо пресыщенные кремнезёмом (SiO2 около 50%) толеитовые базальты.
Физические свойства базальта
Физико-механические свойства базальта весьма различны, что объясняется разной пористостью. Базальтовые магмы, обладая низкой вязкостью, легко подвижны и характеризуются разнообразием форм залегания (покровы, потоки, дайки, пластовые залежи). Для базальта характерна столбчатая, реже шаровидная отдельность. Оливиновые базальты известны на дне океанов, океанических островах (Гавайи) и широко развиты в складчатых поясах. Толеитовые базальты занимают обширные площади на платформах (трапповые формации Сибири, Южной Америки, Индии). C породами трапповой формации связаны месторождения руд железа, никеля, платины, исландского шпата (Сибирь).
Плотность базальта
Плотность базальта 2520-2970 кг/м³. Коэффициент пористости 0,6-19%, водопоглощение 0,15-10,2%, сопротивление сжатию 60-400 Мпа, истираемость 1-20 кг/м², температура плавления 1100-1250°C, иногда до 1450°C, удельная теплоёмкость 0,84 Дж/кг•К при 0°C, модуль Юнга (6,2-11,3)•104 Мпa, модуль сдвига (2,75-3,46)•104 Мпa, коэффициент Пуассона 0,20-0,25. Высокая прочность базальта и относительно низкая температура плавления обусловили применение его в качестве строительного камня и сырья для Каменного литья и минеральной ваты.
Применение базальта
Применение базальта — базальт широко используется для получения щебня, дорожного (бортового и брусчатки) и облицовочного камней, кислотоупорного и щелочестойкого материала. Требования промышленности к качеству базальта как сырью для щебня такие же, как и к другим изверженным породам.
B CCCP на щебень разведано 50 месторождений c промышленными запасами 40 млн. м³. Два месторождения базальта c промышленными запасами 6,5 млн. м³ разведаны на облицовочный камень (Армянская CCP, Грузинская CCP). Годовая добыча базальта свыше 3 млн. м³. B CCCP месторождения базальта сосредоточены в основном в Армении, Восточной Сибири и на Дальнем Востоке. Базальтовые покровы в восточных районах США образуют крупные месторождения в штатах Нью-Йорк, Нью-Джерси, Пенсильвания, Коннектикут (самые крупные карьеры и камнедробильные заводы).
Page not found — Сайт b-utepliteli!
Главным преимуществом базальтового волокна можно отметить следующие позиции:
1. Низкая теплопроводность, это позволяет достичь поставленных задач по теплопроводности в условиях низких температур северных регионов.
2. Базальтовая вата отличается длительным сроком службы. Производители отмечают ее срок эксплуатации в 40-50 лет, это – намного больше, если сравнивать Базальтовую вату с другими теплоизоляционными материалами.
3. Базальтовая вата или на профессиональном языке Базальтовый утеплитель или Базальтовое волокно не подвержена образованию плесени, грибка, гниению, и отличается высокой устойчивостью к воздействию ультрафиолета.
4. Базальтовый утеплитель (базальтовое волокно) не разрушается доже в условиях повышенной вибрации, что нельзя сказать про другие теплоизолирующие материалы.
5. Базальтовый утеплитель (волокно) обладает повышенным звукоизолирующими характеристиками.
6. Базальтовое волокно известно очень низкой плотностью, это свидетельствует о высоких теплозвукоизоляционных ее свойствах.
7. Базальт отличается химической устойчивостью.
8. Базальтовый утеплитель отличается высоким показателем устойчивости к открытому огню, а значит Базальтовый утеплитель отвечает пожаробезопасностью при его использовании. Взрывобезопасность ровна нулю.
9. Базальтовый утеплитель не теряет своих технических свойств и под воздействием температурных перепадов. Базальт легко переносит нагрев, и охлаждение.
10. Базальт отличает высокая температура своего применения. Если прочие минерал ватные материалы можно применять только до температуры до 400 градусов по Цельсию,
то изделия на основе базальтового волокна можно применять до 700 градусов, а краткосрочно — и до 1100 градусов.
11. Базальт в Мире известен как самый экологически чистотой продукт. Он не содержит в себе ни органических веществ, ни горючих, ни канцерогенных. Химическая формула Базальта совпадает с формулой натурального камня — базальта.
Свойства базальта — характеристики, преимущества и применение
Материал, получаемый из базальтового камня, активно используется в современном строительстве. Основные сферы применения базальта – это обеспечение теплоизоляции и защита от возгораний. В зависимости от условий эксплуатации могут быть использованы различные виды защиты, разработанные на основе этого материала.
Изготовление базальтового материала
По сути, базальт – это горная порода, которая образуется в местах извержения вулканов. При застывании базальтовая лава превращается в прочный камень, который затем идёт на переработку.
Производство непрерывного базальтового волокна осуществляется с использованием однофазной технологии, которая позволила достичь себестоимости столь же незначительной, как и стоимость изготовления стекловолокна. В процессе изготовления базальтовая порода измельчается до фракции 5-20 мм и расплавляется в печах при температуре 1400–1600 °С.
Свойства базальта
Подробнее характеристики базальта и изделий из него рассмотрены в таблице:
Свойства и преимущества |
Нет вредных выделений при нагреве |
Пожаробезопасность (температура плавления +1114 °С) |
Хорошая паропроницаемость (0,3 – 0,6 мг/м*ч*Па) |
Стойкость к вибрациям и кислотно-щелочным средам |
Большое разнообразие по плотности |
Отсутствие усадки |
Прочность до 80 кПа с коэффициентом деформации при сжатии не более 10% |
Хорошие показатели теплоизоляции (0,034 – 0,048 Вт/м*С) |
Высокая степень звуконепроницаемости |
Небольшая толщина и масса |
Гибкость и пластичность |
Большое значение имеет сфера эксплуатации материалов на основе волокна из базальта. Например, при возведении зданий по СНиПам необходимо использовать паронепроницаемый материал. С другой стороны, если речь идёт о строительстве сооружений из дерева, газо- и пеноблоков, кирпича, то паропроницаемость утеплителя должна быть больше такой же характеристики стен.
Сфера применения
Основные свойства базальтовых материалов — повышенные показатели звуко- и теплоизоляции, огнезащиты. Они отлично подходят для защиты всех типов зданий, как промышленных, так и жилых. Есть и другие сферы использования:
- теплоизоляция жарочных шкафов и прочего кухонного оборудования;
- в качестве утеплителя навесных фасадов;
- обустройство противопожарного пояса внутри и снаружи объекта;
- защита отдельных элементов инженерных систем (в первую очередь речь о вентиляции).
Отдельно нужно рассказать о вентиляционных системах. При возникновении пожара огонь и дым перемещаются по воздуховодам, а потому без должной защиты есть высокий риск быстрого распространения пламени. Базальтовые материалы дают возможность предотвратить разгерметизацию вентиляционных каналов, остановить возгорание и не дать огню шанса перекинуться на соседние помещения.
Виды базальтовых утеплителей
В зависимости от предназначения, есть несколько видов базальтовых теплоизоляционных изделий:
- Мягкие. Имеют пористую структуру, а потому и повышенный коэффициент теплоизоляции. Однако не приспособлены к механическим нагрузкам.
- Средней прочности. Применение — защита воздуховодов, звукоизоляция, утепление вентилируемых фасадов. Хорошие показатели теплоизоляции, однако стоимость выше, чем у предыдущего варианта.
- Жёсткие плиты. Используются при фасадных работах, для утепления пола и каркасных перегородок. Не боятся большой нагрузки, при этом не теряют эксплуатационные характеристики.
- Фольгированные материалы. Отражают часть тепловой энергии обратно в помещение. Фольга может быть нанесена на одну или обе стороны. Есть фольгирована только одна сторона, то она должна смотреть внутрь помещения (для отражения части тепла).
Самый высокий показатель теплоэффективности среди всех аналогов.
Инновационным решением являются материалы из непрерывного базальтового волокна Basfiber, изготовленные по запатентованной технологии. Данные изделия включают в себя все преимущества базальта и, в то же время, минимизируют его недостатки. В частности, они полностью экологичны, не содержат связывающих формальдегидных смол и других вредных соединений, безопасны для человека. Ознакомиться с продукцией Basfiber вы можете на официальном сайте производителя – ООО «Базкорд».
Технология непрерывного базальтового волокна
УДК 666.189.2 : 666.193
к. т. н. А.Г. Новицкий, д-р тех. наук М.В. Ефремов
ЗАО МИНЕРАЛ 7 (Украина)
Некоторые аспекты технологического процесса получения базальтового непрерывного волокна (НБВ)
Производство непрерывного базальтового волокна
основано на плавлении в плавильном агрегате измельченного базальта, с
последующим вытягиванием из полученного расплава элементарных нитей. Формирование нитей осуществляется через отверстия в фильерных пластинах. При
этом, несмотря на многообразие физических процессов, происходящих в узле
формирования волокна, определяющим является процесс плавления базальта с
получением расплава.
Процесс получения базальтового расплава принято рассматривать как процесс плавления гетерогенной системы, которая состоит из нескольких физически однородных минеральных соединений силикатов, которые представлены в виде кристаллов и стекла. В общем виде расплав базальта представляет собой расплав темного стекла, в связи с чем к процессам формирования базальтового расплава могут быть применены теории и гипотезы формирования расплава стекла.
За последние 100 лет выдвинуто ряд гипотез о строении
стекла. Так по кристаллитной гипотезе А. А. Лебеденва [1]строение стекла
представляется в виде каркаса из
беспорядочно расположенных атомов или ионов,
составляющего основную массу стекла и содержащего участки, степень
упорядоченности которых постепенно возрастает,
образуя так называемые кристаллиты. Н. В. Белов [2] показал, что в структурном отношении, между стеклом и
соответствующими кристаллическими соединениями имеется
далеко идущая аналогия
(сохраняется тип связей, координационные числа
структурных элементов и т. д.).
По структурно-координационной гипотезе Дитцель, Аппен [3] свойства стекла
определяются главным образом
степенью связности основного каркаса, образуемого
стеклообразователями и координационным состоянием катионов-модификаторов. По
агрегативной гипотезе О. К. Ботвинкина [4] в структуре стекла сохраняются
химические соединения или
составляющие их ионы, которые проявляются при
кристаллизации стекла в виде кристаллов определенного состава. По В. В. Тарасову
[5] неорганические стекла по
своему строению являются
непрерывными разветвленными каркасами, состоящими из цепочек, образованных
кремнекислородными
анионами, находящимися в электрическом поле катионов
металла. Тарасов считает, что эти стекла от органических стекол
отличаются
только тем, что их каркас (полимер) имеет характер поливалентного ионного
радикала, а катионы мономеры.
Таким образом, все гипотезы допускают наличие в стекле высокополимерного, апериодического, но, тем не менее, не лишенного отдельных упорядоченных микрообластей каркаса. Этот каркас образован структурными многогранниками в виде бесконечных анионных радикалов стеклообразователя, находящихся в силовом электрическом поле катионов модификаторов.
Гипотеза о кристаллитном строении стекла с момента ее возникновения и до настоящего времени претерпела некоторые изменения. Изучение строения различных стекол отчетливо обнаруживает микронеоднородности их структуры. Из этого следует, что реальные стекла состоят из упорядоченной части кристаллитов и не упорядоченного аморфного вещества. Большинство ученых согласны с тем, что структура стекла является аморфно-кристаллитной.
На упорядоченность структуры расплава влияют
температура плавления, время выдержки расплава при температурах выше температуры
кристаллизации, наличие в составе катионов щелочных металлов, воздействие
электромагнитного поля, наличие сильных Вандервальсовых связей.
На основе исследования стекол из расплава
базальта, полученного в разных температурных условиях, установлено, что при
уменьшении скорости охлаждения стекла его химическая стойкость увеличивалась, а
прочность уменьшались. При повышении температуры приготовления расплава
получена обратная зависимость. При увеличении времени выдержки расплава при
определенной температуре выше температуры кристаллизации зависимость сохраняется.
Так же существенным фактором влияющим на свойства получаемых стекол является
электромагнитная обработка расплава, которая позволяет закрепить эффект
разрушения минеральной памяти и получить высокую прочность стекла. Важным
фактором при работе со стеклом из горных пород является то, что из расплава с
неразрушенной минеральной памятью возможно восстановление структурного
минералогического состава кристаллического тела, если процесс охлаждения вести с
малой скоростью и выдержкой при определенных температурах. А это говорит о
частичном подтверждении кристаллитной гипотезы.
Процесс формирования расплава базальта происходит в интервале температур от 1720 до 15350К, при температуре верхней границы кристаллизации в районе 15300К. Причем эти температуры разные для разных видов базальтового сырья, поступающего на переработку. В этой связи установление интервалов температурного режима является одним из основных элементов управления технологическим процессом получения расплава и производства базальтового непрерывного волокна с заданными свойствами.
Важным этапом получения качественного расплава является процесс дегазации, который заключается в удалении находящихся в расплаве газов. Этот процесс происходит при выдержке расплава при температурах более 17200К. Продолжительность выдержки составляет около двух часов. Вязкость расплава при этом составляет около 150 Па с.
Процесс формирования волокна из расплава через
фильеры определяется вязкостью стекла и характером ее изменения в зависимости от
температуры, величиной верхней границы кристаллизации, её скоростью, а так же
поверхностным натяжением. Базальтовые расплавы, пригодные для получения
непрерывного волокна, должны характеризоваться малой скоростью
кристаллизации[6]. Если склонность расплава к кристаллизации большая, процесс
приходится вести при более высокой температуре, чем температура, которая
отвечает необходимой вязкости, что приводит к возникновению дополнительных
технических трудностей. Если стекло имеет низкую скорость кристаллизации, то из
него можно формировать волокна и в том случае, если температура выработки
отвечает температуре кристаллизации или даже ниже ее.
Технологически базальтовое стекло должно
иметь сравнительно широкий интервал выработки, то есть температурный интервал, в
котором технологические свойства стекла, главным образом вязкость, имеют
определенные значения и не поддаются резкому изменению. Базальтовое стекло,
имеющее широкий интервал выработки, не требует тщательного регулирования
температуры, и процесс выработки более устойчив. Для стабильного
технологического процесса необходимо чтобы разница между конечной и начальной
температурами выработки составляла приблизительно 1000К.
Воздействие на стеклообразующие составляющие высоких температур приводит к их модификации, созданию новых связей и формированию структуры стекла. Эти факторы существенно влияют на характеристики расплава. Изменяя интервал температур плавления, время выдержки расплава в среде высоких температур и режим охлаждения расплава в процессе получения непрерывного волокна, можно эффективно управлять качеством конечного продукта.
Кроме управляемого температурного воздействия на сырье важным фактором получения качественного волокна является также выбор самого сырья. Его химический состав предопределяет температурные режимы получения расплава, его характеристики и в конечном итоге качество получаемой продукции[7].
Как указывалось выше, в основу получения
непрерывного базальтового волокна заложена технология механической вытяжки
нитей из расплава. Эта технология реализуется в настоящее время двумя способами,
которые отличаются только аппаратурным оформлением процесса. Первый способ
предопределяет использование небольших печных агрегатов модульного типа, (модульная
технология) с возможностью установления на печном агрегате одного, двух щелевых
фильерных питателей или пластин. Второй способ предопределяет использование
многопостовых (многопостовая технология) печных агрегатов с установкой струйных
и фильерных питателей в количестве от 6 до 12 штук. Основные производители
базальтового непрерывного волокна развивают свое производство по этим двум
направлениям. В таблице 1. приведены некоторые характеристики производимого
базальтового волокна различными производителями, как модульной, так много
постовой технологией.
Модульная технология характеризуется
относительно малыми начальными капитальными вложениями, возможностью быстрого
введения производства в эксплуатацию и плавного наращивания производственных
мощностей. Основным преимуществом, на наш взгляд, есть то, что модульные печи
можно выводить на режим поочередно и прекращать работу каждой конкретной печи
отдельно не оказывая существенного влияния на технологический процесс в других
печах, и на объемы выпускаемой продукции. Запуск и вывод на режим модульного
печного агрегата происходит в течении 3-4 х дней.
К недостаткам модульной технологии относится сравнительно низкое качество получаемого волокна. Это объясняется малой площадью ванной печи, что значительно снижает время прохождения расплавом этапа дегазации и гомогенизации. Волокно, полученное по такой технологии не намного лучше стекловолокна на основе Е-стекла. Кроме того, количество отходов при этой технологии составляет около 40%.
Главными преимуществами многопостовой технологии
является стабильность технологического процесса получения базальтового волокна,
которое по своим характеристикам приближается к качественным характеристикам
волокна, полученного из S-стекла. Это достигается прежде всего значительными
размерами ванной печи, которые обеспечивают максимальную аморфность расплава,
что достигается увеличением времени выдержка расплава при определенной
температуре и практически полной ликвидации кристаллов. Кроме того, применяемые
в технологическом процессе струйные питатели способствуют увеличению
пластичности расплава, нейтрализуя действием электрического поля ионные связи
катионов и анионов. На рис.1 показано влияние на структуру стекла
электромагнитного поля посредством его воздействия на связи между отдельными
образованиями, составляющими расплав. В верхней части рисунка показано
стекло без обработки расплава электромагнитным полем. Оно имеет крупные
кристаллические включения. В нижней части тоже стекло, после магнитной
обработки расплава. Как видно на рисунке, размер кристаллов значительно
уменьшился и в расплаве появилась неупорядоченность распределения составляющих
элементов. При этом установлено, что прочность волокна, полученного из такого расплава,
на 20% выше прочности волокна, полученного из необработанного.
Рис. 1. Структура стекла базальтового волокна до и после воздействия на расплав электромагнитного поля.
Время выдержки расплава в многопостовом печном
агрегате (в зависимости от технологического процесса, время прохождения
базальта от загрузки в печь до выработки волокна составляет от 14 до 18 часов)
что позволяет практически полностью уменьшить влияние лминеральной памяти╗
базальта на процесс формования волокна. По результатам исследований получена
зависимость (рис. 2.) прочности базальтового волокна от времени выдержки
расплава при температуре 17200К.
Рис. 2. Зависимость прочности базальтового волокна от выдержки расплава при температуре 17200К.
Прочность волокна определялась по ГОСТу 6943.10-79 с небольшими изменениями. При выдержке от 4 до 8 часов происходит растворение магнетита и
других рудных минералов, а также турмалина и слюды. Более труднее растворяются
Ц кварц, пироксен и др. Причем пироксен распадается на кристаллы кремнезема и
оливина. Оливин частично состоит из форстерита, температура плавления которого
21700К, но под действием плавней в расплаве с течением времени он
растворяется. Наиболее интенсивное растворение кристаллов идет в течение 14
часов. В дальнейшем система постепенно приходит в состояние равновесия. Что
подтверждается относительно одинаковой прочностью полученного волокна при
выдержке расплава от 14 до 24 часов. Наглядную картину дает структура стекол
полученных при разном времени выдержки (рис. 3.). В верхней части рисунка
представлено базальтовое стекло с выдержкой расплава в течение 2 часов при
температуре 17200К. Тут отчетливо видны крупные кристаллы, которые не
растворились. В нижней части рисунка представлено стекло, полученное из расплава,
выдержанного в течении 14 часов. Как видно из рисунка, размеры частиц заметно
уменьшились.
Рис. 3. Структура стекла из расплава базальта после выдержки при температуре 17200К. Верхняя часть 2 часа, нижняя часть 14 часов.
Волокна полученные из расплава приготовленного по модульной технологии имеют как крупные кристаллы, так и кристаллиты рис. 4.
а б
Рис. 4. Кристаллы и кристаллиты в базальтовом непрерывном волокне:
а- кристаллиты; б — кристалл
При исследовании под микроскопом среза волокна
изготовленного с малой выдержкой расплава видно, что сечение волокна имеет
множество разных плоскостей рис 5а.
Рис. 5. Сечение волокна.
Волокно, полученное при выдержке расплава более 14 часов на сечении имеет всего несколько плоскостей, т.е. разрыв идет согласно флуктуационной теории прочности стекла [8] (рис. 5б). Это является еще одним подтверждением преимущества многопостовой технологии. Следующим ее преимуществом является то, что при соответствующем аппаратурном оформлении и квалифицированном обслуживающем персонале процесс получения непрерывных нитей идет практически без сбоев. Нет сбоев и при замене узлов выработки волокна. Конструкция печного агрегата позволяет работать три года, без капитального ремонта футеровки. Время запуска печного агрегата и вывода на режим составляет около семи суток. Количество отходов при работе данной технологии составляет менее 5%.
Результаты исследований доказывают перспективность
развития производства БНВ по многопостовой технологии, в отличии от выводов
сделанных другими авторами [9].
Выводы:
1. Несмотря на обилие гипотез образования стекла, многие авторы согласны с тем, что структура стекла является аморфно-кристаллитной.
2. Воздействие на стеклообразующие составляющие высоких температур и электромагнитного поля приводит к их модификации, созданию новых связей и формированию структуры стекла, что существенно влияет на характеристики расплава.
3. Изменяя интервал температур плавления, время выдержки расплава в среде высоких температур и режим охлаждения расплава в процессе получения непрерывного волокна, можно эффективно управлять качеством конечного продукта.
4. На основе проведенного анализа произведено сравнение двух способов производства базальтового волокна. Показано, что получение высококачественного базальтового волокна возможно только при использовании так называемой многопостовой технологии.
Литература:
1.
Лебедев А. А. Труды совещания по
строению стекла лСтроение стекла╗. М.; Л.: Издательство АН СССР. 1955 С.
360Ч362.
2. Белов Н. В. Структура ионных кристаллов и металлических фаз. М., 1947 с. 235.
3. Бут Ю.М., Дудеров Г.Н., Матвеев М.А. Общая технология силикатов ннЦ М.: Госстройиздат, 1962. Ц с. 299.
4. Ботвинкин О. К. Стеклообразное состояние. Ч М.; Л.: Изд. АН СССР, 1965.
5. В.В. Тарасов. Проблемы физики стекла Ц М.: Госстройиздат, 1979.Ц с.256.
6. Новицкий А.Г., Ефремов М.В. Особенности получения непрерывного химически стойкого базальтового волокна.// Хімічна промисловість України. 2003. №1;
7. Новицкий А.Г. Базальтовое сырьё. Технология выбора для производства волокон различного назначения.// Хімічна промисловість України. 2003. №2;
8. Бартенев Г.М. Строение и механические свойства неорганических стекол. стекла Ц М.: Госстройиздат, 1966.Ц с.216.
9. Громков Б.К., Трофимов А.Н., Чебряков
С.Г., Орешко С. М. Аналитический обзор по развитию технологии выработки
непрерывных базальтовых нитей в России и Украине.//
Glass Russia.
2009. № 8.
В Пермском университете создали гидропонную систему на базальте
Ученые ПГНИУ создали фитостену на непрерывном базальтовом волокне – экологически безопасном и долговечном материале, разработанном в университете. «Базальтовая грядка» заняла свое место в ботаническом саду ПГНИУ.
Корневая система растений при выращивании их способом гидропоники развивается на твердых субстратах. Обычно для этого используются керамзит, вермикулит, щебень, однако эти материалы имеют минусы – они подвержены гниению и разрушению. Ученые ПГНИУ предлагают использовать вместо них непрерывное базальтовое волокно – нитевидный материал, который получают из расплавленной и преобразованной магматической вулканической горной породы.
«Непрерывные базальтовые волокна, каждое из которых имеет средний диаметр 20 микрон, удерживают корни растений, как фундамент. В отличие от предшественников, этот материал имеет большую проницаемость, корни в нем «дышат». Поверхностная энергия волокна удерживает на своей поверхности 30% воды, позволяя рассчитать правильный цикл полива», – рассказывает руководитель «Лаборатории базальтового стекла» Рауль Ергалиев.
Базальтовое волокно не гниет, не растворяется и не пахнет. Стеклянная, гладкая поверхность волокон не позволяет микроорганизмам жить и развиваться на них. Волокно также подвергается рециклу – повторному использованию. Легкость материала позволяет создавать вертикальные грядки и экономить площади.
Ранее базальт, если и применялся в сельском хозяйстве, то в другом виде – дискретный (штапельный) базальт короткой длины прессовали в пласты, а потом связывали между собой смолами, которые при утилизации оказывают негативное воздействие на окружающую среду. У нового формата, благодаря непрерывной волоконной структуре, основным преимуществом стала экологичность и безвредность при утилизации – спустя миллионы лет использованное волокно кристаллизуется в камень.
«Лаборатория базальтового стекла» начала свою работу в начале 2017 года. Кроме сельского хозяйства, базальтовые волокна, созданные сотрудниками лаборатории, могут применяться при производстве утеплителей, базальтопластиков, фильтрующих материалов, специальных видов цементов и бетонов повышенной прочности.
В ближайшее время благодаря изобретению лаборатории в Пермском крае запустится крупное производство зеленого фуражного корма для животных. Сейчас ученые планируют разработать технологию, с помощью которой можно будет создавать управляемые соотношения оксидов в базальте, чтобы контролировать конечные качества волокна, а также создание высокопористой структуры из базальта, которая может найти свое применение не только в машинном, но и в аграрном хозяйстве.
Инновационный центр «Мозгово»,
Пресс-служба
Горит ли минвата и при какой температуре
Теплоизоляционные материалы нового поколения из мин. ваты отвечают главным требованиям в отношении способности держать тепло, а еще поглощать звуки и справляться с влиянием влаги и пара. Немного тяжелее обстоит дело с огнеустойчивостью. Изоляторы на самом деле показывают устойчивость к огню, расплавляясь при очень больших температурах, но лишь в конкретных случаях.
Какие изоляторы относят к категории минеральных ват?
Чтобы узнать горит или нет теплоизолятор и при какой температуре, важно знать о его характеристиках и свойствах.
Согласно ГОСТу к классу утеплителей из мин. ваты можно отнести:
- шлаковату;
- вату на основе стекловолокна;
- базальтовую вату.
Эти все теплоизоляторы выделяются между собой не только толщиной и длиной волокон, однако и их размещением. Естественно, разными являются подобные характеристики, как проводимость тепла, водоустойчивость, шумопоглощение и горение.
Вата на основе стекловолокна — горит или нет
Такой вид теплоизолятора из минеральной ваты считается очень доступным, а благодаря этому и нередко применяемым в процессе устройства тепловой изоляции. Основное отличие материала от каменной и шлаковой ваты — особенная структура с колючими волокнами. Работать с ней тяжело и страшно.
Толщина волокон стекловаты может составлять от 5 до 15 микрон, длина может колебаться в границах 15-50 миллиметров. Именно за счёт них теплоизолятор получается таким прочным, эластичным и гибким. Работают со стекловатой в первую очередь в защитной одежде, в респираторе и перчатках.
При минимальном коэффициенте теплопроводимости, теплоизолятор может гореть при температуре от +500 градусов Цельсия, но производственники советуют не дозволять нагрева выше 450 градусов.
Шлаковата — горючий или негорючий теплоизолятор
Чтобы иметь представление о горючести шлаковаты, следует иметь в виду, что теплоизолятор это результат смешивания белитовых шламов со связующими элементами. Волокна материала толщиной от 4 до 12 микрон, длина 16 миллиметров. Специфика материала — конечная кислотность, естественно и способность вступать в реакцию с поверхностями металла под влиянием сырости.
Теплоизоляторы из шлаковаты неустойчивы к проявлениям влаги так, как иные более люксовые материалы из мин. ваты, благодаря этому не используют для наружной изоляции стен фасадов. Из-за этой причины теплоизолятор не подойдет для устройства тепловой изоляции труб из металла и пластика. Непрочный материал, требует конкретной осторожности во время монтажного процесса и эксплуатации.
Показатель теплопроводимости у шлаковаты больше, чем у предыдущего изолятора. стекловолокна. В отношении горючести материал тяжело назвать не уязвимым. Теплоизолятор начинает плавится при температуре от 250 градусов Цельсия. Как только температура может достигать критичной метки, волокна =плавятся, а одновременно с ними теряется и функционал.
Базальтовая вата — подходящий утеплитель
Среди всех указанных разновидностей минеральные ваты, базальтовая вата считается самой неопасной в том числе и в отношении горючести. Волокна материала по размеру сходственны волокнам шлаковаты, однако в отличие от первых совсем не опасные, не просят специализированной защиты во время монтажных работ.
Показатель теплопроводимости у базальтовой ваты очень маленький, а температура плавления может достигать 600 градусов Цельсия.
Усовершенствованной версией базальтовой ваты считается утеплитель из базальтовой ваты из габбро или диабаза. В отличии от каменной, базальтовая дополнительно включает белитовые шламы и минеральные элементы:
- доломит;
- глину;
- известняк.
За счёт примесей, теплоизолятор показывает довольно большие показатели текучести. Стоит еще сказать что в базальтовой минвате практически нет формальдегидной смолы, что уменьшает риск испарения фенола, пускай и на фоне снижения способности сопротивляться действию влаги.
Так как в базальтовой минвате практически нет нестабильных к большим температурам элементов, материал может хранить функционал при нагреве до 1000 градусов Цельсия.
Как из камня минвата, так и базальтовая при заявленных изготовителем температурах плавления не поддаются возгоранию, а исключительно плавятся, чего не скажешь о стекло- и шлаковате.
Что оказывает воздействие на устойчивость к горению каменных теплоизоляторов
Необходимо понимать, что ключевую долю риска собой представляют теплоизоляторы из мин. ваты с содержанием добавок из синтетики. Непосредственно они первыми начинают гореть, нарушая функционал теплоизолятора и подвергая риску цельность всей конструкции.
В процессе изготовления ваты из базальта искусственные клеящие вещества почти что не применяются. Их подменяют компоненты природы, например песок или глина.
Негорючая минвата: в каких формах выпускается
Теплоизоляторы из мин. ваты, которые не поддаются возгоранию, доступны в нескольких формах выпуска с хорошими свойствами. Сюда можно отнести:
- мягкие;
- полужесткие;
- жёсткие.
Мягкие плиты из минеральной ваты не поддаются возгоранию, имеют средние плотностные показатели, не очень большой показатель теплопроводимости. Подойдут для применения в конструкциях, не предполагающих большие нагрузки.
Полужесткие плиты из мин. ваты также не поддаются возгоранию, владеют плотностью вдвое превышающей плотность мягких плит, подходят для теплоизоляции вертикальных конструкций.
Жёсткие плиты также, как и предыдущие варианты не поддаются возгоранию, владеют самыми большими показателями плотности. Применяются для утепления конструкций разного типа, весьма популярны для изолирования систем кровли без стяжки из бетона.
Плиты минераловатные из категории негорючих считаются довольно востребованным теплоизолятором. Следом за ними следуют акустические маты также со способностью сопротивляться огню. Основным отличием плит от матов считается структура — прошитые специализированной нитью волокна, образующие собой полотнище, подобное стеганому одеялу. Толщина и длина матов отличаются в зависимости от марки. Положительным качеством матов считается слой защиты из фольги или сетки.
Как плиты, так и маты из категории негорючих ценны для теплоизоляции огнеопасных конструкций. Это могут быть деревянные дома, веранды, бани и др. Благодаря теплоизоляторам из мин. ваты с температурой плавления от 600 градусов Цельсия, возникает возможность обезопасить сооружения и конструкции от повреждения огнём, сделать больше показатели звукопоглощения и сбережения тепла.
Марки невоспламеняющейся
мин.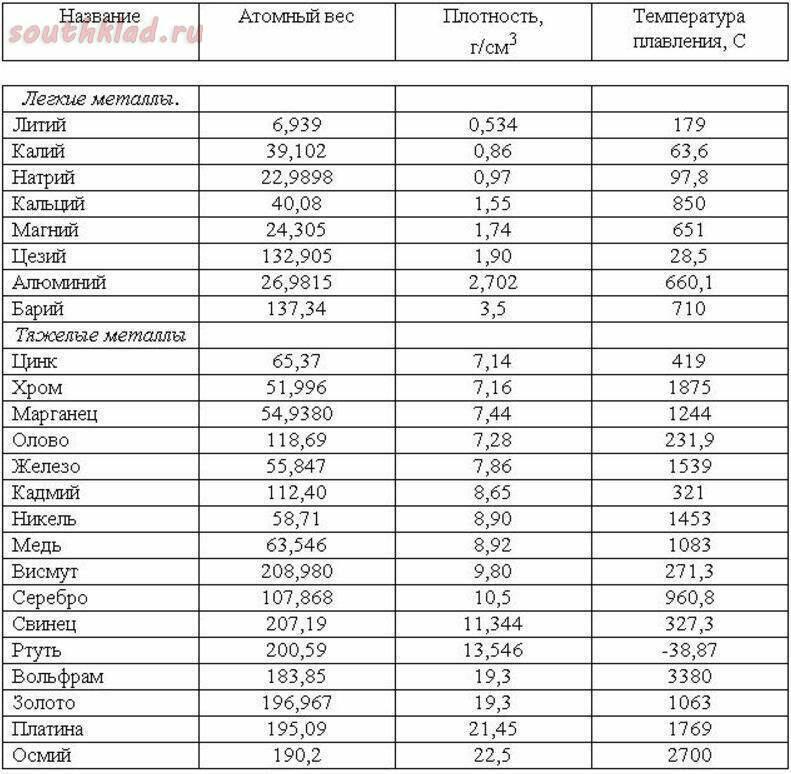
Теплоизоляторы на основе мин. ваты, которые не поддаются возгоранию, на рынке есть продукций некоторых наиболее известных торговых марок как нашего, так и заграничного происхождения.
Одной из очень востребованных считается продукция датской компании Rockwool. Изготовитель практикует изготовление утеплителей из базальтовой ваты с температурой плавления от 1000 градусов для увеличения пожарной безопасности и устройства хорошей тепловой изоляции. Плиты изготовителя негорючие, удобные и комфортные в работе.
Для изолирования кровли нередко применяют минеральный негорючий теплоизолятор общего испано-немецкого производства от компании URSA — М-15. Речь идет о качественной стекловолоконной продукции из категории НГ.
Стойкие к большими температурам плиты выпускают и изготовители из нашей страны Технониколь и Изорок, а еще европейские — Knauf и ISOVER.
Стоимость минерального теплоизолятора будет зависеть не только от плотности, но и от показателей горючести, в особенности важного для устройства неопасной тепловой изоляции. Собственно благодаря этому следует быть аккуратными в покупке материалов с необоснованно невысокой ценой. Быстрее всего основная часть их состава — искусственные элементы, не способны сопротивляться очень маленьким температурам, повышающие риск возгорания и распространения огня в помещении.
Какой утеплитель лучше. Тест на пожаробезопасность
ООО «Фирма «Рось-Базальт». Базальтовое волокно из холодного тигля
Посмотреть и скачать изображение в большом размере можно на Яндекс.Диске: https://yadi.sk/a/YzrRhCmdX9QJRw
Написать директору ООО «Фирма «Рось-Базальт» Сергею Павловичу Лескову: [email protected]
Технология и оборудование для производства базальтового штапельного волокна
Работы по высокочастотному (ВЧ) плавлению горных пород с целью получения базальтового волокна мы начали 30 лет назад. К этому времени относится начало научно-исследовательских работ по изучению процесса плавления базальта с помощью ВЧ генераторов в холодном тигле: определение технологических и конструктивных параметров холодных тиглей, условия выдачи расплава базальта в виде непрерывной струи, а также возможность получения базальтового супертонкого волокна (БСТВ) при условии раздува струи сжатым воздухом. Технология плавления горных пород токами высокой частоты с последующим раздувом струи расплава сжатым воздухом в супертонкое волокно создавалась как альтернатива дуплекс-процессу с целью получения БСТВ без использования драгоценных металлов и газа. В то время многие регионы Сибири и Дальнего Востока остро нуждались в эффективной теплоизоляции, но не были подключены к газопроводам с природным газом. За прошедшие годы было запущено более 20 производств изготовления теплоизоляции в виде ковра из базальтового штапельного волокна и прошивных матов.
Основным элементом технологических линий по производству базальтового волокна является комплекс плавильный, от которого зависит производительность процесса и его экономическая эффективность. Комплекс плавильный состоит из индукционной печи, высокочастотного генератора и дозатора шихты. В качестве источника энергии для плавления горной породы (шихты) в холодном тигле использовались выпускаемые промышленностью ламповые генераторы, предназначенные для индукционной плазмы. В середине двухтысячных годов нами были разработаны специализированные высокочастотные генераторы мощностью 160 и 250 кВт, предназначенные для плавления горных пород. Технологические линии по производству базальтового штапельного волокна (ваты) с плавильными комплексами, оснащенные специализированными генераторами, запущены нами в России, Казахстане, Украине, Узбекистане и Таджикистане. Подобные линии быстро монтируются и не требуют больших капиталовложений.
На рис. 1 показана линия ВМ–100 для производства базальтового волокна, а на рис. 2 – выход базальтового ковра с этой линии. На технологических линиях ВМ с плавлением базальта в холодном тигле индукционной печи изготавливают базальтовое волокно диаметром до 3 мкм.
Рис. 3 отражает момент монтажа холодного тигля индукционной печи. Стенки тигля выполнены из медных секций, охлаждаемых водой.
На рис. 4 показан непрерывный слив двух струй расплава базальта из холодного тигля. Индукционная печь с холодным тиглем полностью снимает проблему взаимодействия расплава с плавильным агрегатом, так как при плавлении породы стенки тигля, охлаждаемые водой, покрываются коркой застывшего базальтового стекла и образуют слой гарнисажа, предохраняющего его от высокотемпературного расплава.
Проведенные научно-исследовательские и проектно-конструкторские работы по высокочастотному плавлению горных пород и многолетний опыт по внедрению и эксплуатации технологических линий изготовления базальтового волокна определили возможности и указали на перспективу этого способа.
Преимущества индукционного способа плавления нерудных горных пород в водоохлаждаемом тигле
Плавление нерудных горных пород в холодном тигле высокочастотной индукционной печи имеет ряд преимуществ перед плавлением газом или жидким топливом:
– плавление базальта происходит при температуре свыше 2000 °С, что позволяет быстро и эффективно осуществлять процесс перевода шихты в расплав, обеспечивая высокую химическую однородность, более полную дегазацию и гомогенизацию расплава с разрушением всевозможных тугоплавких микрокристаллических включений;
– при индукционной плавке происходит интенсивное перемешивание расплава без использования специальных средств. Создается сильное принудительное перемешивание расплава вследствие электродинамического взаимодействия токов, индуктированных в расплаве, с током индуктора. Также создаются условия для конвективного перемешивания и получения равномерной температуры по объему;
– используя электродинамическое перемешивание, расплав можно перегреть во всем объеме тигля. Предел перегрева определяется только мощностью источника тока и устойчивостью расплава при высоких температурах. Для плавления некоторых видов окислов, например, диоксида циркония, температура в холодном тигле поддерживается 3200 °С, и медные стенки тигля прекрасно выдерживают эту температуру;
– индукционная печь является наименее требовательной к перерабатываемому сырью по химическому составу, что позволяет расширить сырьевую базу за счёт использования базальтов, которые не могут быть переработаны в газовых печах;
– процесс индукционного плавления горных пород надежен и устойчив, а подаваемую мощность можно легко регулировать в широких пределах;
– расплавленный базальт не контактирует ни с электродами, ни с газовым факелом, ни с материалом, из которого изготовлен тигель;
– технология плавки имеет в сотни раз меньшие выбросы побочных отводимых газов, не требующих дожигания;
– при индукционном способе плавления имеется возможность подшихтовки горных пород в целях получения расплава требуемого химического состава и волокон, устойчивых в кислых и щелочных средах;
– время от момента включения ВЧ генератора до наведения ванны расплава с температурой 2000 °С и выдачи струи расплава из тигля составляет 60–90 минут.
Модифицирование исходного состава базальта
Технологические возможности индукционных печей позволяют использовать их для получения модифицированных базальтовых стекол, а создание фактического алгоритма целенаправленной модификации горных пород имеет цель повысить устойчивость базальтового волокна к щелочам, кислотам и их огнестойкость, например, для производства высокопрочных базальтобетонов и специальных композитов. Применение волокон, обладающих высокой стойкостью в щелочной среде, является одним из важных условий долговечности композитной арматуры в бетоне.
Если влияние оксидов металлов на свойства стекол достаточно хорошо изучены, то работ по модификации горных пород оксидами металлов явно недостаточно.
В ООО «Фирма «Рось-Базальт» проведена работа по исследованию модификации горной породы диоксидом циркония. Работа проводилась на промышленном оборудовании плавильного комплекса «Базальт–10». Использовали порфирит Тягунского месторождения Алтайского края (Мк = 4,5) и порошок цирконового концентрата производства Туганский ГОК «Ильменит». Для плавления подготавливалась шихта из порфирита и цирконового концентрата с содержанием диоксида циркония 10 % масс. Шихта порфирита в смеси с цирконововым концентратом плавилась в холодном тигле индукционной печи, и струя расплава, непрерывно истекающая из тигля, раздувалась сжатым воздухом эжекционной головкой в штапельное волокно. Средний диаметр полученного волокна составлял 2,8 мкм. Химическую стойкость образцов полученной ваты оценивали по сохранению массы после воздействия на них различных агрессивных сред: дистиллированной воды, растворов кислоты (2N HCl) и щелочи (2N NaOH). Экспериментально было установлено, что химическая стойкость в дистиллированной воде не изменилась, химическая стойкость при воздействии на вату щелочи возросла на 16 %, а в растворе кислоты химическая стойкость ваты увеличилась на 48 %. Термостойкость ваты с содержанием диоксида циркония по сравнению с базальтовой ватой практически не изменилась.
Базальтовое непрерывное волокно
Специалисты по непрерывному базальтовому волокну выражают желание выполнять плавление горной породы при более высокой температуре, чем температура в действующих печах, при непрерывном перемешивании расплава. Особенно наглядно это отражается в патентах. Например:
– патент РФ 2118949, «…температуру в плавильной печи устанавливают 1705–2000 °С, а вытягивание волокна производят со скоростью 5505–6500 м/мин.»;
– патент РФ 2 233 810, «…породу нагревают до температуры 2105–2200 °С до получения расплава со степенью аморфности не менее 96 % и выделения из расплава непроплавившихся кварцитов, последующую гомогенизацию и стабилизацию расплава производят при температуре 1420–1710 °С до получения расплава с вязкостью не менее 130 П, а вытягивание волокон осуществляют из зоны расплава, которая расположена ниже поверхностного слоя»;
– патент РФ 2 421 408, «…загрузку базальта осуществляют в зону максимальных температур 1450–2000 °С пламени горелки-загрузчика, плавление, дегазацию и гомогенизацию расплава производят на плавильной площадке при низких уровнях расплава 5–70 мм с последующим увеличением уровня расплава до 80–300 мм в ванне печи»;
– патент РФ 2 180 892, «…барботаж расплава осуществляют путем подачи кислородсодержащего газового агента через сопла, установленные в донной части зоны плавления. ..».
Технология плавления минерального сырья в холодном тигле индукционной печи обеспечивает высокую температуру плавления и интенсивное электродинамическое перемешивание расплава, позволяет технологически и конструктивно реализовать процессы активного плавления базальтовых пород и перехода их в аморфное состояние, гомогенизации и дегазации расплава. Также позволяет снизить энергопотребление, повысить производительность и обеспечить производство непрерывных волокон с высокими характеристиками по прочности, эластичности, химической стойкостью; получать базальтовое непрерывное волокно меньшего диаметра. Технология плавления горной породы в холодном тигле является оптимальной для получения расплава при производстве базальтового непрерывного волокна.
Удельный расход электроэнергии для плавления 1 кг горной породы в холодном тигле индукционной печи с температурой 2000 °С – 2,3–2,5 кВт•час.
Исследование влияния температурно-временных условий плавления на склонность расплавов к волокнообразованию и на прочность непрерывных волокон, выполненные в Институте проблем химико-энергетических технологий (ИПХЭТ) СО РАН, подтвердили перспективность применения индукционного способа при их производстве. Экспериментальные данные, полученные сотрудниками ИПХЭТ СО РАН, показывают преимущество индукционного способа плавления горных пород при получении тонких непрерывных волокон, так как повышение температуры значительно сокращает общее время стекловарения, обеспечивает химическую однородность расплава и, как следствие, более широкий температурный интервал выработки и лучшее качество волокон. Волокна из высокотемпературных гомогенных расплавов (2000 °С) не содержат не расплавившихся частиц шихты, кварцевых включений и пузырьков газа, и имеют практически бездефектную поверхность [1].
При индукционном способе плавления базальта платинородиевые фильеры эксплуатируются в более щадящем режиме, что позитивно сказывается на стабильности процесса выработки волокна. Уменьшается процесс выноса драгметаллов фильеры, увеличивается межремонтный срок ее эксплуатации. Использование расплавов базальта высокого качества позволяет перейти на работу с фильерами, содержащими повышенное число отверстий. Имеется возможность подшихтовки горных пород в целях обеспечения необходимых выработочных свойств расплавов и получения непрерывных волокон с высокими прочностными характеристиками, устойчивых в кислых и щелочных средах. При плавлении горных пород в газовых печах такие технологические приемы неосуществимы.
Плавление горной породы индукционным способом при изготовлении базальтовой нити может выполняться и как составная часть непрерывного технологического процесса, и как отдельная операция подготовки плавленой шихты с последующим ее дроблением до требуемой фракции.
Нами разработаны проектные предложения для создания производства изготовления базальтового непрерывного волокна (БНВ) разной мощности.
Рис. 5. Одностадийная схема производства БНВ: 1 – плавильный комплекс «Базальт»; 2 – фидер; 3 – фильерный питатель; 4 – устройство замасливания; 5 – наматывающее устройство; 6 – тростильное оборудование; 7 – камера полимеризации Рис. 6. Двухстадийная схема производства БНВ с однопостовыми плавильными агрегатами: 1 – плавильный комплекс «Базальт»; 2 – устройство изготовления гранул; 3 – плавильный агрегат; 4 – фильерный питатель; 5 – устройство замасливания; 6 – наматывающее устройство
Посмотреть и скачать схемы в большом размере можно на Яндекс. Диске: https://yadi.sk/a/YzrRhCmdX9QJRw
Производство базальтового непрерывного волокна может быть организовано как по одностадийной схеме (рис. 5), так и по двухстадийной схеме с однопостовыми плавильными агрегатами (рис. 6), или с многопостовым плавильным агрегатом.
Двухстадийная технология производства БНВ предусматривает изготовление гранул из расплава базальта непрерывной струей, истекающей из тигля индукционной печи, транспортировку гранул в дозатор плавильного агрегата, плавление гранул в этом агрегате и выработку непрерывного волокна.
Однопостовые плавильные агрегаты изготовления БНВ из гранул базальта позволяют выводить их на режим поочередно и прекращать работу отдельно, не оказывая влияния на технологический процесс в остальных модулях. При вводе в эксплуатацию первого плавильного агрегата с минимальными затратами решаются вопросы отработки технологического процесса и обучения производственного персонала. Энергоносителем в плавильных агрегатах может быть электроэнергия, газ или жидкое топливо. Изготовление БНВ по двухстадийной схеме может быть реализовано при модернизации действующих производств.
При одностадийной схеме исключается операции изготовления гранул. Расплав базальта в виде струи подается в фидер, в котором стабилизируется по температуре и распределяется по фильерным питателям. Не требуется изготовление гранул из расплава и вторичное плавление этих гранул, что сокращает расход энергоносителей.
Посмотреть и скачать схему в большом размере можно на Яндекс.Диске: https://yadi.sk/a/YzrRhCmdX9QJRw
На рис. 7 показана установка НВ–1200 (проектное предложение). Установка НВ–1200 предназначена для изготовления непрерывного базальтового волокна (базальтового ровинга) по инновационной технологии на основе индукционного способа плавления базальта.
Основные технические характеристики установки НВ–1200
1. Назначение: производство базальтового ровинга, диаметр монофиламента, мкм – 13–17.
2. Производительность, т/год – до 1200.
3. Сырье, базальт с размером фракции, мм – 0,63–2,5.
4. Потребляемая мощность, кВт – 630.
5. Вспомогательные ресурсы:
– вода (водооборотная система охлаждения), м3/час – 25;– сжатый воздух (0,4 МПа), м3/час – 4.
Разработаны предложения по созданию опытно-промышленной установки, которая позволяет:
– проводить исследования разных месторождений базальта для производства БНВ;
– исследовать подшихтовку базальта минеральными составами для получения БНВ с требуемыми свойствами;
– проводить опытно-организационные работы по переходу на работу с фильерами, содержащими повышенное число отверстий;
– разрабатывать технологии изготовления непрерывного базальтового волокна диаметром 5–7 мкм;
– обучать персонал навыкам работы на производствах БНВ;
– использовать в качестве демонстрационного оборудования для потенциальных покупателей технологии и оборудования изготовления БНВ.
Базальтовая микрофибра и микрошарики
Базальтовая микрофибра предназначена для армирования композиционных материалов. Применяется в качестве замены асбеста для тормозных дисков и колодок. Микрофибра может применяться при производстве базальтопластиков с улучшенными параметрами, армирующим наполнителем для создания защитных покрытий и шпаклевок. Диаметр элементарного волокна микрофибры меньше, чем волокна базальтового ровинга с диаметром 13–15 мкм. Это обеспечивает существенное увеличение площади удельной поверхности микрофибры и положительно отражается на сцеплении волокна и материала матрицы.
Базальтовую микрофибру изготавливали из штапельного базальтового волокна диаметром 1–3 мкм, полученного на технологической линии ВМ методом индукционного плавления базальта с последующим раздувом струи расплава сжатым воздухом в эжекционной головке. Структура волокна получилась полностью аморфной. Полученное волокно механически измельчали, сепарировали на виброситах, отделяя волокна от не волокнистых включений: крупных сферических частиц и достаточно мелких – порядка 20–80 мкм. Благодаря сферичности микрошарики могут применяться, например, в сухих смесях или как наполнители в специальные виды резинотехнических изделий для повышения их эксплуатационных характеристик.
На рис. 8 показано волокно, а также не волокнистые включения после вибросита. На рис. 9 показаны не волокнистые включения в виде базальтовых микрошариков. Дальнейшее разделение микрошариков в зависимости от диаметра проводилось на вибросите, одновременно отделялись элементы, имеющие другую форму, чем шарики. Волокно, после отделения не волокнистых включений, подвергали тонкому измельчению, и сепарировали на массклассификаторе. На рис. 10 показано волокно (увеличение х1000) после сепарации на вибросите, а на рис. 11 – это же волокно после вибросита и обработки на одном из режимов массклассификатора. Микрофибра большой длины, отсеянная массклассификатором, повторно возвращается на оборудование для повторного тонкого измельчения.
Результаты предварительных экспериментов позволили определить направление дальнейших работ, разработать аппаратурно-технологическую схему производства базальтовой микрофибры, осуществить подбор оборудования для создания опытно-промышленной установки.
Базальтовая микрофибра уже находит применение в различных отраслях промышленности в качестве наполнителя в композиционных материалах. Проводятся исследования по применению микрофибры в различных видах пластмасс.
Один из примеров исследования: образцы полиэтилена высокого давления с наполнителем из базальтовой микрофибры (10 % по массе) показали увеличение характеристик по сравнению с эталоном. Сопротивление на изгиб возросло на 40 %, на разрыв – 22 %. Ударная вязкость возросла на 23 %.
Выводы
1. Технология плавления горной породы в холодном тигле высокочастотной индукционной печи является оптимальной для получения расплава при производстве базальтового непрерывного волокна.
2. Производство базальтового непрерывного волокна может быть организовано как по одностадийной схеме производства, так и по двухстадийной. Изготовление базальтового непрерывного волокна по двухстадийной схеме может быть реализовано при модернизации действующих производств.
3. Разработаны предложения по созданию опытно-промышленной установки.
4. Разработана аппаратурно-технологическая схема производства базальтовой микрофибры и микрошариков, в основе которой лежит метод индукционного плавления горных пород токами высокой частоты с последующим раздувом расплава сжатым воздухом.
Литература
1. Ходакова Н.Н., Татаринцева О.С., Самойленко В.В. Влияние условий получения базальтовых стекол на их структуру и свойства // Ползуновский вестник. 2014. Т 2, № 4. С. 148–153.Источник: Огарышев С.И.
%PDF-1.3 % 5147 0 объект > эндообъект внешняя ссылка 5147 125 0000000016 00000 н 0000002856 00000 н 0000003017 00000 н 0000003075 00000 н 0000003108 00000 н 0000003167 00000 н 0000003956 00000 н 0000004254 00000 н 0000004324 00000 н 0000004423 00000 н 0000004675 00000 н 0000004825 00000 н 0000004936 00000 н 0000005052 00000 н 0000005103 00000 н 0000005163 00000 н 0000005260 00000 н 0000005352 00000 н 0000005485 00000 н 0000005552 00000 н 0000005678 00000 н 0000005805 00000 н 0000005956 00000 н 0000006026 00000 н 0000006213 00000 н 0000006400 00000 н 0000006510 00000 н 0000006625 00000 н 0000006732 00000 н 0000006886 00000 н 0000007006 00000 н 0000007144 00000 н 0000007256 00000 н 0000007461 00000 н 0000007664 00000 н 0000007871 00000 н 0000008078 00000 н 0000008289 00000 н 0000008500 00000 н 0000008703 00000 н 0000008908 00000 н 0000009113 00000 н 0000009258 00000 н 0000009402 00000 н 0000009548 00000 н 0000009698 00000 н 0000009846 00000 н 0000009897 00000 н 0000009957 00000 н 0000009990 00000 н 0000010130 00000 н 0000010231 00000 н 0000010350 00000 н 0000010470 00000 н 0000010571 00000 н 0000010689 00000 н 0000010808 00000 н 0000010925 00000 н 0000011043 00000 н 0000011162 00000 н 0000011278 00000 н 0000011394 00000 н 0000011513 00000 н 0000011631 00000 н 0000011750 00000 н 0000011870 00000 н 0000011989 00000 н 0000012107 00000 н 0000012227 00000 н 0000012344 00000 н 0000012463 00000 н 0000012582 00000 н 0000012699 00000 н 0000012817 00000 н 0000012936 00000 н 0000013055 00000 н 0000013172 00000 н 0000013290 00000 н 0000013410 00000 н 0000013528 00000 н 0000013647 00000 н 0000013765 00000 н 0000013884 00000 н 0000014002 00000 н 0000014122 00000 н 0000014240 00000 н 0000014359 00000 н 0000014477 00000 н 0000014595 00000 н 0000014713 00000 н 0000014833 00000 н 0000014951 00000 н 0000015069 00000 н 0000015188 00000 н 0000015306 00000 н 0000015425 00000 н 0000015544 00000 н 0000015692 00000 н 0000015801 00000 н 0000015908 00000 н 0000016016 00000 н 0000016040 00000 н 0000017831 00000 н 0000017855 00000 н 0000019367 00000 н 0000019391 00000 н 0000019697 00000 н 0000019813 00000 н 0000019903 00000 н 0000021668 00000 н 0000021692 00000 н 0000023324 00000 н 0000023348 00000 н 0000025058 00000 н 0000025082 00000 н 0000026815 00000 н 0000026839 00000 н 0000028569 00000 н 0000028593 00000 н 0000029019 00000 н 0000029703 00000 н 0000029837 00000 н 0000031217 00000 н 0000003210 00000 н 0000003933 00000 н трейлер ] >> startxref 0 %%EOF 5148 0 объект > эндообъект 5149 0 объект > эндообъект 5150 0 объект [ 5151 0 Р ] эндообъект 5151 0 объект > /Ф 5197 0 Р >> эндообъект 5152 0 объект > эндообъект 5270 0 объект > ручей Hc«f`b`g` À
Магматические породы образуются в результате кристаллизации магмы. Схема, показанная выше, когда разные виды минералов кристаллизуются при разных температурах, получила дальнейшее развитие в серии реакций Боуэна. Температуры кристаллизации играют большую роль в развитии различных видов изверженных пород при остывании магмы. Различные минералы, находящиеся вместе в одной и той же породе, плавятся при гораздо более низких температурах, чем отдельные минералы. Температуры кристаллизации в этой таблице характерны для среды горных пород, содержащих эти минералы, как и для магмы под поверхностью Земли. Температуры плавления чистых минералов могут быть совершенно разными. Например, в серии реакций Боуэна кварц кристаллизуется при температуре около 650°С, но чистый кварц при давлении в одну атмосферу не плавится до примерно 1700°С. Спасибо д-ру Декстеру Перкинсу, профессору геологии и инженерной геологии Университета Северной Дакоты, за комментарии по поводу температур сухого плавления минералов:
| INDEX IGNEY ROCK Concepts Ссылка Marshak |
Глыбовые породы
навязчивые / плутонные магистральные породы
Неглубокие интрузии, такие как дайки и силлы, обычно мелкозернистые, а иногда и порфритовые, поскольку скорость охлаждения аналогична скорости остывания экструзивных пород. Классификация аналогична классификации вулканических/экструзивных пород. К крупнозернистым породам, образовавшимся на более глубоких уровнях земли, относятся габбро, диориты и граниты. Обратите внимание, что они химически эквивалентны базальтам, андезитам и риолитам, но могут иметь другие минералы или другие пропорции минералов, потому что их история кристаллизации не прерывается, как это может быть для экструзивных пород (см. рис. 6.13 в вашем тексте).
Пегматиты — очень крупнозернистые магматические породы, состоящие в основном из кварца и полевого шпата, а также некоторых более экзотических минералов, таких как турмалин, лепидолит, мусковит.Обычно они образуют дайки, связанные с гранитными плутонами.
Распространение вулканической активности
Магматическая активность в настоящее время имеет место, как и в прошлом, в различных тектонических условиях. К ним относятся расходящиеся и сходящиеся границы плит, горячие точки и рифтовые долины.
Расходящиеся границы пластин
На океанических хребтах магматическая активность связана с извержением потоков базальтовой лавы, образующих подушечную лаву на океанических хребтах, и внедрением даек и плутонов под хребтами.Лавовые потоки и дайки базальтовые, а массивы преимущественно габброобразные. Эти процессы формируют основную массу океанической коры в результате спрединга морского дна. Магмы образуются в результате декомпрессионного плавления по мере подъема и частичного плавления горячей твердой астеносферы.
Конвергентные границы пластин
Субдукция на границах конвергентных плит вводит воду в мантию над субдукцией и вызывает плавление мантии с образованием базальтовых магм.Они поднимаются к поверхности, дифференцируясь путем ассимиляции и фракционирования кристаллов с образованием андезитовых и риолитовых магм. Магмы, которые достигают поверхности, образуют островные дуги и вулканические дуги континентальной окраины, состоящие из потоков базальтовой, андезитовой и риолитовой лавы и пирокластического материала. Магмы, внедряющиеся под эти дуги, могут вызвать плавление земной коры и сформировать плутоны и батолиты из диорита и гранита
Горячие точки
Как обсуждалось ранее, горячие точки — это места, где горячая мантия поднимается к поверхности в виде шлейфов раскаленных пород.Декомпрессионное таяние в этих восходящих шлейфах приводит к образованию магмы, которая извергается, образуя вулкан на поверхности или на морском дне, в конечном итоге образуя вулканический остров. По мере того, как доминирующая плита перемещается над горячей точкой, вулкан удаляется от горячей точки, и над горячей точкой формируется новый вулкан. Это создает трек горячей точки, состоящий из линий потухших вулканов, ведущих к действующему вулкану в горячей точке. Горячая точка, расположенная под континентом, может привести к теплообменному плавлению континентальной коры с образованием крупных риолитовых вулканических центров и плутонических гранитных плутонов ниже.Хорошим примером континентальной горячей точки является Йеллоустон на западе США. Иногда горячая точка совпадает с океаническим хребтом. В таком случае горячая точка производит большие объемы магмы, чем обычно происходит на хребте, и, таким образом, образует вулканический остров на хребте. Так обстоит дело с Исландией, расположенной на вершине Срединно-Атлантического хребта.
Рифтовые долины
Подъем мантии под континентом может привести к трещинам растяжения в континентальной коре с образованием рифтовой долины.Когда мантия поднимается, она подвергается частичному плавлению в результате декомпрессии, что приводит к образованию базальтовых магм, которые могут извергаться в виде базальтов на поверхности. Расплавы, попавшие в кору, могут выделять тепло, что приводит к плавлению коры с образованием риолитовой магмы, которая также может извергаться на поверхность в рифтовой долине. Отличным примером континентальной рифтовой долины является Восточно-Африканский рифт.
Крупные магматические провинции
В прошлом большие объемы преимущественно базальтовой магмы изливались на морское дно, образуя большие вулканические плато, такие как плато Онтонг Ява в восточной части Тихого океана. Такие крупномасштабные извержения могут оказывать влияние на океаны, поскольку они изменяют форму океанского дна и вызывают повышение уровня моря, что иногда приводит к затоплению континентов. Плато образуют препятствия, которые могут резко изменить океанские течения. Эти изменения в океане наряду с огромным количеством газа, выделяемого магмой, могут изменить климат и оказать радикальное влияние на жизнь на планете.
%PDF-1.3 %verypdf.com 331 0 объект > эндообъект внешняя ссылка 331 59 0000000022 00000 н 0000355553 00000 н 0000355697 00000 н 0000356001 00000 н 0000356145 00000 н 0000356450 00000 н 0000357071 00000 н 0000357756 00000 н 0000358468 00000 н 0000359172 00000 н 0000359931 00000 н 0000360636 00000 н 0000361384 00000 н 0000362059 00000 н 0000362288 00000 н 0000362347 00000 н 0000363329 00000 н 0000363368 00000 н 0000366045 00000 н 0000366164 00000 н 0000366480 00000 н 0000366665 00000 н 0000369998 00000 н 0000370918 00000 н 0000371127 00000 н 0000382283 00000 н 0000382462 00000 н 0000382532 00000 н 0000382728 00000 н 0000387587 00000 н 0000387874 00000 н 0000388571 00000 н 0000388693 00000 н 0000388898 00000 н 0000401077 00000 н 0000401386 00000 н 0000401700 00000 н 0000401782 00000 н 0000401987 00000 н 0000415822 00000 н 0000416109 00000 н 0000416286 00000 н 0000416350 00000 н 0000416554 00000 н 0000424049 00000 н 0000424339 00000 н 0000425262 00000 н 0000425471 00000 н 0000435428 00000 н 0000436348 00000 н 0000436557 00000 н 0000446635 00000 н 0000446771 00000 н 0000446908 00000 н 0000447045 00000 н 0000447181 00000 н 0000447317 00000 н 0000447822 00000 н 0000447875 00000 н трейлер ] >> startxref 0 %%EOF 1 0 объект > эндообъект 2 0 объект > эндообъект 3 0 объект > эндообъект 4 0 объект > эндообъект 5 0 объект > эндообъект 6 0 объект > эндообъект 7 0 объект > эндообъект 8 0 объект > эндообъект 9 0 объект > эндообъект 10 0 объект > эндообъект 11 0 объект > эндообъект 12 0 объект > эндообъект 13 0 объект > эндообъект 14 0 объект > эндообъект 15 0 объект > эндообъект 16 0 объект > эндообъект 17 0 объект > эндообъект 18 0 объект > эндообъект 19 0 объект > эндообъект 20 0 объект > эндообъект 21 0 объект > эндообъект 22 0 объект > эндообъект 23 0 объект > эндообъект 24 0 объект > эндообъект 25 0 объект > эндообъект 26 0 объект > эндообъект 27 0 объект > эндообъект 28 0 объект > эндообъект 29 0 объект > эндообъект 30 0 объект > эндообъект 31 0 объект > эндообъект 32 0 объект > эндообъект 33 0 объект > /ProcSet [/PDF/Текст ] /ExtGState > /Цветное пространство > >> эндообъект 34 0 объект > ручей HW]s}#ͱ»Arm&t5Iw
Плавление сухого перидотита при высоких давлениях и базальтовый магмогенез | Американский минералог
Солидус шпинелевого лерцолита (HK66) определен в сухих условиях в диапазоне давлений от 1 атм до 30 кбар . Установлено, что солидус состоит из трех кривых, соответствующих субсолидусным минеральным ассоциациям с выступами около 11 и 26 кбар. Для определения состава расплава, сосуществующего с перидотитом, тонкий слой базальта помещали между прессованными блоками порошкообразных минералов перидотита, а затем уравновешивали его вмещающей средой при температурах плавления. Временные исследования при 15 кбар и 1300°С (на 25°С выше солидуса) показали, что базальтовый расплав, внедренный в перидотит, полностью гомогенизировался с частичным расплавом в перидотитовой матрице в течение 24 часов.Состав расплава, образующегося по солидусу перидотита, представляет собой кварцевый толеит при 5 кбар, оливиновый толеит, близкий к базальту срединно-океанических хребтов (morb) при 8 и 10 кбар, щелочно-оливиновый базальт при 15 и 20 кбар и щелочной пикрит выше 25 кбар. Специально исследовали роль K 2 O в плавлении путем добавления 20 мас. % калиевого полевого шпата в исходный перидотит. Солидус богатого калием перидотита на 70° и 150°С ниже, чем у исходного перидотита при 20 и 30 кбар соответственно.
Его продолжение может пересекаться с обычной океанической геотермой при давлении от 30 до 50 кбар. Расплавы имеют лейцитовый фонолитовый характер в солидусе богатого калием перидотита и постепенно переходят в состав щелочного пикрита в солидусе исходного перидотита. В пользу гипотезы малоглубинного происхождения морбов говорит тот факт, что состав расплава, образовавшегося вблизи солидуса при 8 кбар (16 мас. % Al 2 O 3 , 11 мас. % CaO, 9 мас. % MgO ) графики в середине патологического кластера в нормативных проекциях.Коэффициент распределения оливин-жидкость Fe/Mg, K D = (Fe/Mg) ol / (Fe/Mg) liq равен K D = 0,30 + 0,002 (кбар) в диапазоне давлений от 1 атм до 35 кбар. Судя по значениям K D , составы большинства стекол, о которых сообщалось ранее в экспериментах по плавлению перидотита, значительно изменены эффектом зарастания остаточными твердыми частицами.
(PDF) Термохимия и свойства плавления базальта
энтальпия стеклования определена в этой статье.
Результаты равны –112,2 и –98,5 кДж/моль соответственно.
Благодарности Мы благодарим C. Te
´qui за помощь в измерениях капельной
калориметрии; А. Уиттингтону за полезные комментарии
; и Р. Ланге и анонимному рецензенту за вдумчивые
рецензии на эту статью. В этой работе использован проект ЕС
ENV4-CT98-0713 «Параметризация и моделирование
лавовых потоков». Кроме того, МАБ и АН выражают благодарность
за поддержку грантов НКРЭ №.NER/A/S/2003/00378 и EAR
0229332 соответственно.
Ссылки
Asimow PD, Hirschmann MM, Stolper EM (2001) Расчет
частичного плавления перидодита по термодинамическим моделям
минералов и расплавов, IV. Адиабатическая декомпрессия, состав
и средние свойства базальтов Срединно-океанического хребта
. J Petrol 42:963–998
Bacon CR (1977) Высокотемпературное теплосодержание и теплоемкость
силикатных стекол: экспериментальное определение и модель
для расчета. Am J Sci 277:109–135
Barus C (1893) Константы плавления магматических пород. III.
Теплоемкость магматических пород, рассматриваемая в связи с
отношением температуры плавления к давлению. Phil Mag 35:296–307
Berman RG, Brown TH (1985) Теплоемкость минералов в системе
Na
2
O–K
2
O–CaO–MgO–FeO–
2
O
30002 O
3
-AL
2
O
3
O
-Sio
2
—
2
TIO
2
-H
2
O-CO
2
: представление, оценка и высокотемпературная
экстраполяция.Contrib Mineral Petrol 89:168–183
Бухифд М.А., Кортиал П., Рише П. (1998) Конфигурационные тепловые
емкости: щелочные и щелочноземельные алюмосиликатные жидкости. J
Noncrystal Solids 231:169–177
Бухифд М.А., Рише П., Бессон П., Роскош М., Ингрин Дж. (2004)
Окислительно-восстановительное состояние, микроструктура и вязкость частично
закристаллизованного базальтового расплава. Earth Planet Sci Lett 218:31–44
Bowen NL (1913) Явления плавления плагиоклаза
полевых шпатов, Am J Sci 35:577–599
Brown NE, Navrotsky A (1994) Гематит–ильменит (Fe
) 2
O
3
–
FeTiO
3
) твердые растворы: влияние катионного упорядочения на
термодинамику смешения.Am Mineral 79:485–496
Burchfield JD (1990) Лорд Кельвин и возраст Земли. 2-е изд.
. Издательство Чикагского университета, Чикаго
Куртиал П., Рише П. (1993) Теплоемкость алюмосиликатных расплавов магния
. Geochim Cosmochim Acta 57:1267–
1275
DeYoreo JJ, Lange RA, Navrotsky A (1995) Сканирование калориметрических определений содержания тепла в системах
, богатых диопсидом, во время плавления и кристаллизации.Geochim Cos-
mochim Acta 59:2701–2707
Fukuyama H (1985) Теплота плавления базальтовой магмы. Earth
Planet Sci Lett 73:407–414
Ghiorso MS, Sack RO (1995) Химический массоперенос в
магматических процессах IV. Пересмотренная и внутренне непротиворечивая
термодинамическая модель для интерполяции и экстраполяции
равновесия жидкость-твердое тело в магматических системах при
повышенных температурах и давлениях. Contrib Mineral
Petrol 119:197–212
Gillet P, Richet P, Guyot F, Fiquet G (1991) Высокотемпературные
термодинамические свойства форстерита.J Geophy Res
96:11805–11816
Holland TJB, Powell R (1998) Внутренне согласованный термо-
набор динамических данных для фаз, представляющих интерес для петрологии. J
Metamorphic Geol 16:309–343
King C (1893) Возраст Земли. Am J Sci 45:1–20
Kilinc A, Carmichael ISE, Rivers ML, Sack RO (1983) Соотношение железа и железа
в природных силикатных жидкостях, уравновешенных в
воздухе. Contrib Mineral Petrol 83:136–140
Kojitani H, Akaogi M (1995) Измерение теплоты плавления базальта модели
в системе диопсид–форстерит–анортит.
Geophys RES Lett 22: 2329-2332
Kojitani h, akaogi m (1997) плавящиеся энтальпии мантии
Перидотит: калориметрические определения в системе CaO-
MgO-Al
2
O
3
–SiO
2
и применение к магмообразованию.
Earth Planet Sci Lett 153:209–222
Kress VC, Carmichael ISE (1988) Стехиометрия реакции окисления железа
в силикатных расплавах.Am Mineral 73:1267–1274
Ланге Р.А., Навроцкий А. (1992) Теплоемкость Fe
2
O
3
—
несущие силикатные жидкости. Contrib Mineral Petrol 110:311–320
Lange RA, DeYoreo JJ, Navrotsky A (1991) Сканирование теплоемкости при неконгруэнтном
плавлении диопсида. Am Mineral 76:904–912
Ланге Р.А., Кэшман К.В., Навроцкий А. (1994) Прямые измерения скрытой теплоты при кристаллизации и плавлении
угандита и оливинового базальта.Contrib Mineral Petrol
118:169–181
Lindroth DP, Krawza WG (1971) Теплоемкость и удельная теплоемкость
шести типов горных пород при температурах до 1000°C. Rept Inv, 7503,
Горное бюро США, Вашингтон, 24 стр.
Навроцкий А. (1995) Энергетика силикатных расплавов. В: Stebbins JF,
McMillan PF, Dingwell DB (eds) Структура, динамика и
свойства силикатных расплавов. Rev Mineral 32:121–143
Навроцкий А. (1997) Новый взгляд на прогресс и новые направления в высокотемпературной калориметрии.Phys Chem Mineral
24:222–241
Navrotsky A, Ziegler D, Oestrike R, Maniar P (1989) Калориметрия силикатных расплавов при 1773 K: измерения
энтальпий плавления и смешения в системы диоп-
сайд-анортит-альбит и анортит-форстерит. Contrib Min-
eral Petrol 101:122–130
Naylor BF, Cook OA (1946) Высокотемпературное теплосодержание
метатитанатов кальция, железа и магния. J Am
Chem Soc 68:1003–1005
Osborn EF, Tait DB (1952) Система диопсид–форстерит–
анортит.Am J Sci Bowen ***vol, стр. 413–433
Richet P (1987) Теплоемкость силикатных стекол. Chem Geol
62:111–124
Richet P, Bottinga Y (1984a) Анортит, андезин, диопсид,
волластонит, кордиерит и пироп: термодинамика
плавления, стеклования и свойства аморфного
. Земля планета SCI Lett 67: 415-432
Richet P, Bottinga Y (1984B) Стеклянные переходы и термодинг-
NAMIC Свойства Naalsino
2N + 2
и KALLI
3
O
8
.Geochim
Cosmochim Acta 48:453–470
Richet P, Bottinga Y (1985) Теплоемкость не содержащих алюминия
жидких силикатов. Geochim Cosmochim Acta 49:471–486
Richet P, Bottinga Y (1986) Термохимические свойства
силикатных стекол и жидкостей: обзор. Rev Geophys 24:1–25
Richet P, Bottinga Y, Denielou L, Petitet JP, Te
´qui C (1982)
Термодинамические свойства кварца, кристобалита и аморфного
phous SiO
2 2 : калориметрические измерения падения от 1000
до 1800 К и обзор от 0 до 2000 К. Geochim
Cosmochim Acta 46:2639–2658
Richet P, Gillet P, Fiquet G (1992) Термодинамические свойства
минералов: макроскопический и микроскопический подходы. In:
Saxena SK (ed) Adv Phys Geochem Springer, Heidelberg
10:98–131
Richet P, Fiquet G (1991) Высокотемпературная теплоемкость и
предварительное плавление минералов в системе CaO–MgO– Al
2
O
3
–
SiO
2
.J Geophys Res 96:445–456
Contrib Mineral Petrol (2007) 153:689–698 697
123
Введение в программу физической геологии
Магматическая дифференциация : Итак, все эти источники опираются на плавление мантийных пород, которое должно быть довольно однородным. Почему мы видим такое разнообразие состава магм?Дробная плавка :
Породы мантии, такие как перидотит, состоят из нескольких различных минералов, каждый из которых имеет свою температуру плавления. Когда горная порода нагревается, декомпрессируется или насыщается водой, минералы с самой низкой температурой плавления сначала плавятся и начинают удаляться от материнской породы, поэтому магма всегда несколько более кислая, чем ее источник. Учтите, что магма, извергающаяся на срединно-океанических хребтах, переместилась, может быть, всего на десять километров от своего источника, но если этот источник был ультрамафическим перидотитом, то магма просто базальтовая.
Фракционная кристаллизация . Обратный процесс фракционной плавки.Самые мафические минералы в расплаве (т. е. те, у которых самая высокая температура плавления) будут кристаллизоваться первыми, оставляя все более кислую магму.
Последовательность, в которой минералы кристаллизуются из магмы, была разработана Н. Л. Боуэном в начале 20 века: серия реакций Боуэна .
Ассимиляция :
Подавляющее большинство интрузивов, которые мы видим на континентах, кислые, как гранит. Фракционная кристаллизация не может объяснить это.Помните, что в целом континентальная кора гораздо более кислая, чем океаническая. Когда ультраосновные магмы сталкиваются с кислыми породами континентальной коры, они вызывают плавление большинства кислых минералов в этих кислых породах (имеющих самую низкую температуру плавления). Таким образом, кислый материал добавляется к магме по мере того, как основной материал теряется в результате фракционной кристаллизации. В результате магмы, прошедшие через толстые слои континентальной коры, представляют собой 90 487 высокоочищенных 90 488 концентраций кислых материалов.
Остается загадкой, почему риолитовая и базальтовая магмы могут извергаться рядом друг с другом на континентах. Четвертый параметр – размер магматической камеры. Крупный может пробиться к поверхности и, несмотря на то, что он ассимилировал континентальную кору, сохранить кое-что из своего первоначального состава, тогда как меньший будет значительно изменен при прохождении через ту же толщу коры.
Но реальный мир сложен.Рассмотрим Палисейдс в Нью-Джерси
Стратификация отражает последовательность, в которой однородная базальтовая магма кристаллизовалась после введения в стык между двумя слоями осадочной породы.
- Магма, находящаяся в непосредственном контакте с вмещающей породой, немедленно замерзла, образовав охлажденную зону , химический состав которой соответствует общему химическому составу магмы.
- В оставшейся жидкой магме образовались кристаллы наиболее тугоплавкого вещества, оливина, которые упали на дно, образовав слой оливина
- По мере охлаждения магмы минералы с более низкой температурой плавления, такие как пироксен и богатый кальцием плагиоклаз, начали кристаллизоваться и по очереди падать на дно.
- В конце концов, единственная оставшаяся жидкость кристаллизовалась с образованием более богатого натрием слоя плагиоклаза, примыкающего к верхней зоне охлаждения.
Изверженные формы рельефа
Теперь обратимся к тому, как выглядят магматические породы, когда вы видите их в реальном мире. Для начала, вот общий совет: в поперечном сечении магматические тела, остывшие под землей, как правило, имеют столбчатую трещиноватость , т. е. они пересекаются вертикальными трещинами, которые придают им столбчатый вид.На изображении ниже изображен национальный монумент Devil’s Postpile в Калифорнии, особенно красивый пример.
Даже в менее совершенных формах столбчатая трещиноватость — хороший способ обнаружить магматические породы на расстоянии.
Интрузии и их геометрические формы: Интрузия — это любая плутоническая порода, образовавшаяся из магмы, проникшей в другую породу. Различные термины применяются к типам плутонов в зависимости от их размера и геометрии.
- Плутон : Общий синоним вторжения.
- Батолит : Очень большие массивы плутонических пород — не менее 100 км2 на карте. Сьерра-Невада, Кламат и прибрежные хребты Британской Колумбии представляют собой батолиты, подвергшиеся эрозии.
- Stock : Вторжение среднего размера, менее 100 км2, но в целом поддающееся картированию.
- Силл : Небольшая интрузия, в которой магма была введена между двумя ранее существовавшими слоями породы. Например: Палисады Нью-Джерси и Нью-Йорка.
- Лакколит : В основном надутый порог — ситуация, в которой магма впрыскивается между двумя слоями с достаточной силой, чтобы вынудить вышележащую породу куполом вверх.
- Дайка : Небольшое вторжение, в результате которого магма попала в трещину, в результате чего образовался пласт изверженной породы, пересекающий соседние слои. Дайки часто встречаются в виде роев вблизи вулканов.
- Вулканический перешеек : Если дамба или порог пересекают поверхность, магма устремляется наружу, образуя вулкан. Как только это начинается, канал на поверхность расширяется в трубу. Когда извержение прекращается, магма, все еще находящаяся в трубе, затвердевает, образуя вулканическую шею. Часто от них расходятся дайки.
Вулканические интрузии : Все эти формы, вероятно, состоят из плутонических пород, однако более мелкие, по существу двумерные, имеют высокое отношение площади поверхности к объему. Они, вероятно, будут показывать зону охлаждения в месте их контакта с окружающей породой, которая будет вулканической, потому что она быстро охлаждается. Если дайка или силл достаточно тонкие, зона охлаждения — это все, что есть, что приводит к полностью вулканической дайке или силлу.
Вулканические отложения :
- Основные принципы:
- Чем более кислая магма, тем более вязкая лава.
- Чем влажнее магма, тем взрывоопаснее извержение.
- Когда жидкая магма извергается взрывом, образуется фонтан комков размером с пепел. Вязкая магма не может течь достаточно быстро, чтобы образовать капли, поэтому она выдавливается медленно или рассыпается на тефру (=вулканический пепел).
- Основные лавы :
- Общие характеристики:
- Извержение при 1000 до 1200 град. C ( Hot — примерно температура астеносферы.)
- Fluid
- Характерные текстуры
- Общие характеристики:
- Полезные и средние лавы :
- Общие характеристики:
- извержение 904 C ( Прохладный сравнительно)
- до 10 раз вязче базальта
- Высоковязкая лава
- Характерные текстуры
- Тефра также известная как зола : Мелкие фрагменты менее 2 мм.
в диаметре.
- Сварной туф : Горная порода, образующаяся при осаждении и слипании горячих (и, следовательно, слегка липких) частиц тефры.
- Вулканическая брекчия : Горная порода, состоящая из более крупных фрагментов ранее существовавших пород, разрушенных извержением.
- Тефра также известная как зола : Мелкие фрагменты менее 2 мм.
- Общие характеристики:
Дополнительная информация .
Ключевые понятия и словарный запас:
- Дробная плавка
- Фракционная кристаллизация
- Серия реакций Боуэна
- Ассимиляция
- Новая майка Палисейдс
- Изверженные формы рельефа:
- Плутон
- Батолит
- На складе
- Порог
- Лакколит
- Дайке
- Вулканическая горловина
- Поведение магмы:
- Mafic более жидкий, felsic более вязкий
- Влажная магма (с летучими в растворе) извергается со взрывом
- Тефра
- Основные характеристики извержения:
- Более высокая температура
- Жидкость
- Пахохо
- Аа
- Подушечные базальты
- Базальт везикулярный
- Пепел
- Характеристики извержения среднего кислого состава:
- Более низкая температура
- Вязкий
- Туф сварной
- Вулканическая брекчия
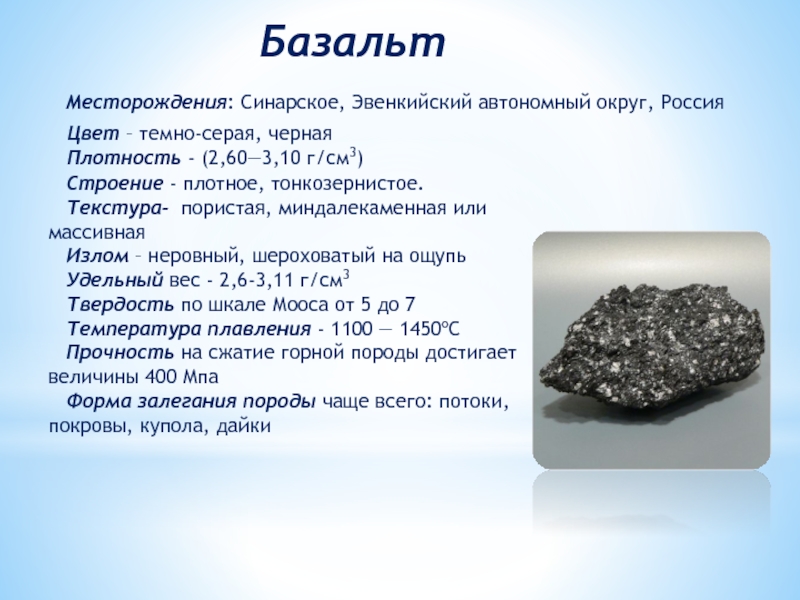