Состав газобетона – Компоненты в составе газобетона по ГОСТу
Состав газобетона на 1 м3, пропорции, изготовление в домашних условиях
Газобетонные блоки относятся к востребованным изделиям, успешно сочетающим теплоизоляционные и конструкционные свойства. При соблюдении пропорций и простых правил замеса они без проблем изготавливаются дома, при наличии подходящего оборудования и проведения автоклавной обработки выпуск продукции организовывается в промышленных масштабах. Итоговые характеристики зависят от качества сырья, тщательности его подготовки и последовательности соединений при замесе, правильный материал имеет однородную закрыто-ячеистую структуру.
Виды и состав газоблоков, соотношение
В зависимости от вида и соотношений используемого вяжущего выделяют следующие разновидности:
- Цементные, с долей ПЦ с маркой прочности от М300 и выше, достигающей 50 % от общей массы.
- Известковые, на основе негашеной помолотой кипелки (до 50 %), гипса, шлака, цемента или их смесей (до 15 %).
- Шлаковые, полученные путем вспенивания молотых отходов металлургии с другими видами вяжущего.
- Зольные, содержащие до 50 % продуктов уноса.
- Смешанные, получаемые путем соединения всех вышеперечисленных видов вяжущего, с долей ПЦ от 15 % и выше.
В качестве инертного заполнителя применяется кварцевый и другие виды песка и вторичные отходы металлургии и теплоэнергетики: зола уноса и гидроудаления, ферросплавные шлаки, продукты обогащения рудных материалов. Все они вводятся после тщательного размола, доля в общем составе варьируется от 20 до 40 %. Поризация обычного и автоклавного газобетона достигается за счет ввода алюминиевой пудры и хлорида кальция, для затворения смеси используется вода с минимальным содержанием солей. К улучшающим свойства добавкам относят упрочнители, полиамидные пластмассы и аналогичные вещества, снижающие усадку, их соотношение в общей массе очень низкое.
Ориентировочные пропорции сырья для газобетона без автоклавной обработки:
Наименование | Доля в общей массе, % | ||
Портландцемент | 15-50 | 51-71 | 35,3-49,4 |
Наполнитель | Кварцевый песок: 31-42 | Молотый микрокремнезем: 0,6-3,5 | Молотый известняк до удельной поверхности 300-700 м2/кг: 12,4-26,5 |
Алюминиевая пудра | 0,1-1 | 0,01-0,15 | 0,06-0,1 |
Известь | — | 0,04-0,7 | 2,6-2,65 |
Полуводный гипс | — | 0,1-0,4 | — |
Другие добавки | Каустическая сода: 0,05-0,45 | Хлористый кальций: 0,5-3 | Хлорид кальция: 0,18-0,25 |
Вода для затворения | Все остальное |
Приведенные пропорции также подходят для автоклавного производства газобетона, в перерасчете на вес на приготовление 1 м
Особые требования выдвигаются к порообразователю: для достижения равномерной ячеистой структуры материала применяется алюминиевая сухая пудра с долей активного металла в пределах 90-95 % или суспензии – до 93. Их ввод требует осторожности: при снижении доли менее 0,06 % блоки не достигают заданной пористости, при засыпке более 0,1 – выделяется избыток водорода, приводящий к образованию чересчур крупных ячеек, вырыванию из них газа и усадке изделий.
Существует четкая связь между качеством используемого наполнителя и прочностными характеристиками: чем тоньше будет его помол, тем лучше. Водоцементное соотношение подбирают опытным путем, доля затворяемой жидкости достигает 45-75% от общего веса сухих составляющих и в идеале сводится к минимуму.
Лучшие результаты при изготовлении неавтоклавного газобетона наблюдаются при В/Ц=0,4, повышение этого показателя приводит к снижению прочности материала.
Технология получения газоблоков в домашних условиях
Для кладочных изделий помимо сырья и емкостей для замеса потребуются формы – заводские металлические или самоделки из фанеры и дерева. Их размеры зависят от назначения блоков: чем больше будет ячеек, тем быстрее пойдет процесс выпуска. Внутренние стороны форм выполняются из ламинированной фанеры или других влагостойких материалов, принимаются меры по исключения протеканию воды, с целью упрощения выемки стенки смазывают составами на основе воды и технического масла в соотношении 3:1, эту процедуру повторяют каждый раз перед заполнением.
Этап замеса считается самым сложным в домашнем производстве, без дозаторов и оборудования для подготовки компонентов пропорции подбираются только опытным путем. Любое изменение степени активности вяжущего, температурных условий или чистоты воды оказывает прямое влияние на процесс поризации и итоговое качество. Важную роль играет последовательность соединения ингредиентов: вяжущее, песок или другие сухие заполнители перемешиваются и затворяются водой порционно, вплоть до получения однородной консистенции (но не более 5 мин, в противном случае цемент начнет схватываться), далее в нее вводят хлористый кальций или каустическую соду (при наличии их в выбранном составе), и в последнюю очередь – алюминиевую пудру или суспензию. После засыпки порообразователя смесь перемешивается со всей возможной тщательностью не более, чем 1 минуту и заливается в предварительно подготовленные формы.
При изготовлении газобетонных блоков в домашних условиях раствором заполняется только половина ячейки. Реагирование ингредиентов начинается незамедлительно, объем массы нарастает в течение первых 5-10 минут, после чего она слегка усаживается. Полученную «горбушку» срезают струной, формы оставляют в теплом помещении на сутки. Элементы вынимают с максимальной аккуратностью и размещают на стеллажах или поддонах до окончательного набора прочности.
Для получения автоклавных изделий они проходят обработку горячим паром под избыточным давление в специальных камерах, в домашних условиях этот этап пропускается. Это вместе с отсутствием возможности строгого контроля за составом и геометрической точностью форм объясняет уступку качества кустарных элементов заводским. С целью его улучшения принимается ряд мер:
- Площадка или помещение защищаются от сквозняков и холодной температуры. В идеале работы проводятся в теплое время года.
- Формы слегка прогревают перед смазыванием. После выемки изделий оценивается состояние стенок и проводится их тщательная чистка.
- Сухие компоненты перед затворением водой просеиваются сквозь сито и вводятся малыми порциями.
stroitel-lab.ru
Газобетон неавтоклавный — состав и производство
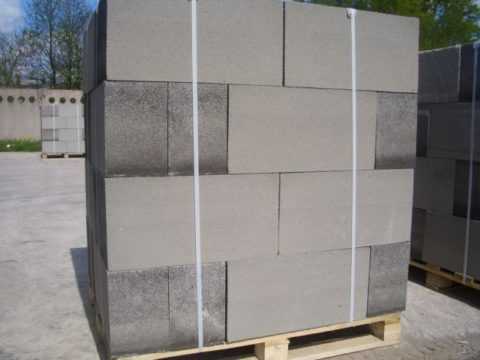
Неавтоклавный газобетон
Выбор строительного материала для стен является наиболее сложным, ведь от этого зависит не только скорость строительства, но и в будущем — долговечность конструкции, ее прочность и комфортность пребывания. Газобетон неавтоклавный уже давно не является новинкой на рынке, производится он на протяжении длительного времени и, не смотря на появление более современных изделий, по-прежнему, не теряет популярность.
Содержание статьи
Обзор основных качеств материала
Рассмотрим основные свойства и качество газобетонного блока неавтоклавного твердения, опираясь на требования ГОСТ, СНиП и результаты испытаний продукции. Проанализируем технологию производства и выясним: будет ли правильным выбор данных изделий в качестве основного материала для возведения стен.
Что такое газоблок неавтоклавного твердения и его сфера применения
Неавтоклавный блок сделан из того же вспененного бетона, но при условии естественного твердения.
Сфера применения у него достаточно широкая:
- Изделия используют при малоэтажном строительстве для возведения несущих стен и перегородок;
- Также применяют в качестве заполнителя каркаса из железобетона при формировании высотных зданий;
- Использование неавтоклавного газобетона актуально при теплоизоляции и армировании.

Возведение стены из неавтоклавного газобетона, фото
Состав газобетона неавтоклавного характеризуется наличием следующих компонентов:
- Цемент;
- Песок;
- Гипс, зола или мел;
- Вода;
- Алюминиевая пудра в качестве порообразователя;
- Химические добавки, ускоряющие процессы газообразования и твердения.
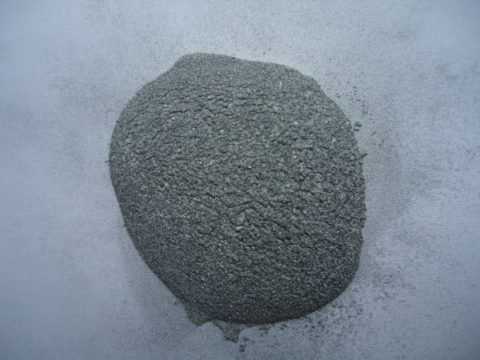
Алюминиевая пудра
Газобетон, в зависимости от плотности, различают:
- Теплоизоляционный;
- Теплоизоляционно-конструкционный;
- Конструкционный.
Рассмотрим, как плотность блока влияет на его основные показатели.

Кварцевый песок
Таблица 1. Характеристики неавтоклавного газобетона в зависимости от плотности:
Наименование показателя | Значение для неавтоклавного теплоизоляционного газобетона | Значение для неавтоклавного конструкционного газобетона |
Теплопроводность ккал/м. ч. Гр. | 0,07-0,16 | 0,17-0,33 |
Паропроницаемость | — | 0,16-0,25 |
Водопоглощение | — | 8,5-9 % |
Усадка | — | 0,033 % |
Прочность на сжатие кг/см2 | 10-29 | 30-70 |
Огнестойкость | ||
Масса в сухом состоянии кг/м3 | 350-590 | 600-1600 |
Преимущества и недостатки строений, возведенных из неавтоклавного газобетона
- Малый вес изделий, в сочетании в достаточно неплохим показателем прочности.
- Низкий коэффициент теплопроводности, способен гарантировать высокий уровень сохранения температуры в здании.
- Простота в обработке, облегчит задачу возведения стен, и повысит скорость строительства. Изделия легко поддаются резке любым пригодным для этого инструментом. Дом из неавтоклавного газобетона, под силу построить практически каждому.
- Материал экологически чистый, не горит и обладает устойчивостью к биологическому воздействию.
- Еще одним достоинством является возможность изготовления блока своими руками. Технология производства достаточна проста и не требует приобретения дорогостоящего оборудования.
- Показатели значений паропроницаемости и звукоизоляции, также находятся на должном уровне.
- Морозостойкость достигает 50-70 циклов, что, несомненно, неплохой результат.
Относительно невысокая цена на продукцию. Данный факт также можно отнести к плюсам изделий.

Неавтоклавный газобетон
Отрицательные стороны представлены также в немалом количестве, их гораздо больше, нежели у автоклавного газобетона и сводятся они к следующему:
- Материал достаточно хрупкий, и крошится от механических воздействий
- Требуемая толщина стены – от 65 см, что не позволит сэкономить на строительстве, а, скорее, наоборот (блоки придется укладывать в два ряда).
- Повышенный уровень усадки, составляющий от 1 до 2-х мм. Следствием может стать нарушение не только внешних характеристик, но и эксплуатационных качеств здания и свойств материала.
- Широкое распространение мелких кустарных производств, также следует отнести к минусам. В связи с этим, шансы на приобретение некачественной продукции значительно возрастают.
- Наличие геометрических отклонений в силу несовершенства оборудования и влияния человеческого фактора во время изготовления.
Обратите внимание! Вышеуказанный факт может существенно отразиться на расходе клеевого состава при укладке блока и скорости строительства в целом
Высокий уровень влагопоглощения губительно сказывается на изделиях, разрушая их структуру и снижая показатели качества свойств.
Усложненность отделки, в основном, за счет вышеуказанного недостатка и пониженной адгезии основания стены из газобетона с отделочными материалами. В результате, у строителей возникают дополнительные расходы, например, на составы грунтовки, специализированные дорогостоящие смеси, армирование.
Сравнение изделий с другими, схожими по свойствам, материалами
Автоклавный газобетон – особенный материал, однако во многом он имеет сходства с другими изделиями, предназначенными для возведения стен. Рассмотрим подробнее при помощи таблицы.
Таблица 2. Сравнение неавтоклавного газобетона:
Наименование материала | Теплопроводность | Морозостойкость, циклов | Усадка | Прочность | Водополощение | Толщина стены (минимальная) |
Газобетонные блоки неавтоклавные | До 0,2 | 35-75 | 1-2 мм/м2 | 25-45 | До 20% | 0,6 метра |
Пенобетон | 0,14-0,22 | От 35 | 0,4 мм/м2 | 15-25 | 10-16% | Минимум – 0,6 м |
Кирпич | 0,5 | 100 | 6-13% | 100-200 | 12-15 % | Минимум 1,2 м |
Полистиролбетон | 0,1-0,2 | От 35 | 0,33 мм/м2 | 20-30 | 10-15% | От 0,5 м |
Керамзитобетон | 0,4-0,8 | От 50 | 0,3-0,5 мм/м2 | 25-35 | 10-15% | От 0,5 м |
Дерево | 0,14 | От 30 | Около 10% | — | 20-25% | Минимум – 0,5 м |
Внешнее отличие газобетона от других стеновых материалов
Отличительные особенности неавтоклавного газобетона от блоков автоклавного твердения
Автоклавный газобетон и неавтоклавный: отличия
А теперь давайте разберемся: в чем же заключается отличие автоклавного газобетона от неавтоклавного?
Одним из основных является, разумеется, сам способ твердения. Дело в том, что два этих типа блока подвергаются сушке при различных условиях, что, как следствие, влияет на числовой показатель свойств и характеристик.
Газобетон синтезного метода твердения, на последнем этапе производства помещают в автоклав, где он находится под воздействием высокой температуры и давления. В свою очередь, неавтоклавный газобетон твердеет при естественных условиях.
Следствием данного различия и некоторых нюансов производства, является несовпадение многих показателей, однако частично свойства все же схожи:
- Морозостойкость автоклавного бетона может достигать 100, а иногда и 150 циклов, в тоже время неавтоклав, таким высоким значение похвастаться не может — максимальный, обещанный производителями, порог достигает 70 циклов замораживания и оттаивания.
- Газобетон гидратационного твердения (неавтоклавного) больше подвержен усадке. Следствием этого, может стать появление трещин на кладке и поверхности, покрытой штукатуркой. Процесс этот объясним особой обработкой автоклава, во время которой он начинает набирать прочность прямо на стадии изготовления.
- В числовом выражении, усадка неавтоклавного газобетона составляет до 1,5 мм/м2, а автоклавного всего 0,3 мм.
- Коэффициент теплопроводности хорош у обоих типов. Однако толщина стены при одинаковых показателях двух блоков будет разной и отличаться примерно на 20-25 см, не в пользу неавтоклавного изделия.
- Звукоизоляционные характеристики также схожи, как и способность к паропроницанию.
- Оба материала могут стойко противостоять огню, и находиться под воздействием разрушительно воздействия высокой температуры до 2-х часов.
- Также, являясь изделиями экологически чистыми, они не наносят никакого вреда окружающей среде.
- Стоит обратить внимание на то, что геометрия автоклавного блока значительно выигрывает. Максимально допустимые отклонения, в соответствии с ГОСТ, не должны превышать 3 мм по длине, 2 – по ширине и 1 мм – по высоте. У неавтоклавного блока, данные показатели достигают в числовом выражении следующих значений: 5 мм – по длине, 4 мм – по ширине и 2 – по высоте.
В следствие этого, толщина кладочного слоя раствора или клея будет отличаться, как и скорость строительства.
- Изделия имеют и внешние отличия, основное из которых заключается в цвете: блок гидратационного твердения – серый, а автоклав – белый.
- Одним из важнейших различий, является прочностная характеристика. При плотности блока равной Д500, марка автоклавного газобетона, по требованию ГОСТ, должна соответствовать показателю 3,5. У неавтоклава это значение едва достигает половины.
- Завершим сравнение указанием на факт различия в основном вяжущем компоненте: для неавтоклавного газобетона это всегда – цемент, а путем автоклавирования получают известь содержащие газосиликатные блоки.
Требования технической документации к последнему, разумеется, ниже. И это касается не только прочности, но и других качеств. А теперь, для наглядности, проанализируем вышеперечисленные свойства в виде таблицы:
Таблица 3. Сравнение: автоклавный газобетон и неавтоклавный газобетон:
Наименование свойства | Значение у автоклава | Значение у неавтоклава |
Морозостойкость, циклов | 50-100 (иногда до 150) | 25-75 |
Теплопроводность | 0,1-0,14 | До 0,12 |
Усадка | 0,3 мм/м2 | 1-2 мм/ м2 |
Толщина стена | Минимум 40 см | Минимум 65 см |
Защитная отделка | Нуждается | нуждается |
Марка прочности | 1,5-3,5 | 1-2,5 |
Стоимость за м3 | Дороже | Дешевле автоклавного газобетона |
Выбор среди ведущих производителей | Достаточно широк | Не так распространен, более характерен для кустарногои домашнего производства |
Сложность производства | При наличии автоматизированной линии или конвейера, сложностей не возникает, участие человека минимизировано | Процесс отнимает немало времени, нуждается в трудозатратах |
Проанализировав вышеуказанное, наверняка, становится риторическим вопрос: что лучше автоклавный или неавтоклавный газобетон.
Анализ технологического процесса
Теперь рассмотрим, что представляет собой производственная технология неавтоклавного газобетона? Какие материалы и оборудование используются при изготовлении, и как влияют технологически верные пропорции сырья на конечный результат качества изделий.
Необходимое оборудование и материалы
Сразу стоит обратить внимание на то, что изготовление неавтоклавного газобетона, не смотря на большую популярность автоклавного, по-прежнему, производится на некоторых предприятиях. Соответственно, набор оборудования для домашнего использования и для заводского, будет разниться.
Для полноценного производства понадобится наличие следующих машин и станков:
- Газобетоносмеситель;
- Форма для блока;
- Станок для резки блочного массива;
- Ручной дозатор;
- Мерная емкость;
- Поддоны для блоков.
При объемном производстве, могут понадобиться также средства транспортировки. Рецептура на неавтоклавный газобетон содержит перечень определенного набора материалов.
Содержание его следующее:
- Вода — она должна соответствовать ГОСТ 23732-79 «Вода для бетонов и растворов». Обычно используется простая водопроводная.
- Цемент, соответствующий требованию ГОСТ 10178-85. Марка должна быть не менее 400
- Требования к песку определены ГОСТ 8736-93. В большинстве случаев используют кварцевый.
- Наполнители могут быть следующими: мука известковая ГОСТ 26826-86, мука доломитовая ГОСТ 14050-93, золошлаковая смесь ГОСТ 25592-91, зола с тепловых станций ГОСТ 25818-91, шлакигранулированные ГОСТ 3476-74 ,минеральный порошок ГОСТ Р 52129-2003.
- Газообразователь – алюминиевая пудра ГОСТ 5494-95.
- Применяются также поверхностно-активные вещества в виде: стирального порошка, сульфонола или обычного хозяйственного мыла.
- Для ускорения твердения и порообразования, применяют каустическую соду, или едкий натриевые, схожие по свойствам, добавки.
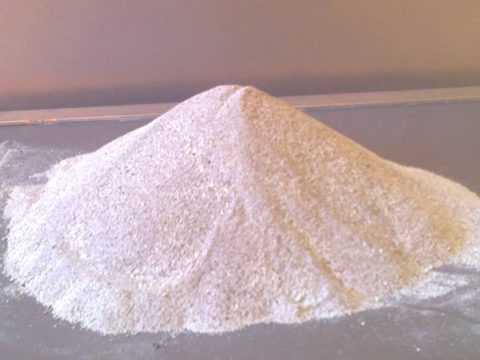
Мука известковая
Поэтапное описание хода работ при изготовлении
Классическая технология производства газобетона неавтоклавного содержит в себе следующие этапы:
- Первым делом производится подготовка форм: смазка их специализированной эмульсией для облегчения выемки изделий. Замешивается раствор в соответствии со всеми требованиями к пропорциям.
- Готовая смесь заливается в формы и выстаивается.
- Далее осуществляют удаление излишков и резку блочного массива.
- Блоки выдерживают до состояния, пригодного для распалубки, после чего изделия перемещают на деревянные поддоны.
Теперь рассмотрим подробно каждый из этапов при помощи таблицы.
Таблица 4. Производство газобетона неавтоклавного: поэтапная инструкция процесса изготовления.
Подача цемента | Осуществляется в дозирующий бункер вручную. Доза цемента контролируется при помощи датчиков. По достижению нужного количества, бункер опрокидывается и цемент попадает в скиповый подъемник, а точнее в его банку. |
Подача песка | Происходит по аналогии с цементом |
Подача воды | Жидкость нагревается до 40 градусов и отправляется в промежуточный дозатор. Он содержит достаточно широкую горловину, которая позволяет быстро переливаться воде в основной смеситель для смешивания с остальными компонентами. |
Добавление порообразователя | Чаще всего используют алюминиевую пудру. Дозирование производят при помощи мерного сосуда. |
Смешивание компонентов | Первой в смеситель попадает вода. Предварительно его включают для образования воронки. Следом, туда отправляются сыпучие ингредиенты, а последними – химические добавки. После смешивания, смеситель передвигается ближе к формам. |
Заливка в форму | Полученным раствором заполняют форму для блоков |
Газообразование и первый этап твердения | Смесь выдерживают в форме до окончания процесса своеобразного брожения. После его завершения раствор начинает набирать прочность. |
Корректировка и резка | По истечении нескольких часов, излишки раствора удаляются, а массив разрезается на блоки. Для этого используют ручной резательный аппарат, погрешность которого составляет 3 мм, гост неавтоклавного газобетона это позволяет. |
Заключительный этап | Изделия накрывают теплоизоляционным материалом, и выжидают 6-8 часов. После этого, блоки перемещаются на деревянные поддоны, где остаются набирать техническую прочность в течение еще как минимум 3-х суток – летом и 7-ми – зимой. |
Обратите внимание! При домашнем производстве порядок работ остается тем же. Взвешивание компонентов производят вручную при помощи весов, а раствор разливают в формы определенного размера, после извлечения из которых, получается готовый блок. То есть резательный аппарат, с целью снижения затрат, не используется.
Видео в этой статье расскажет о процессе производства более подробно.
Основные итоги
Неавтоклавный газобетон достаточно популярный материал в строительной сфере. Однако при этом, по некоторым показателям, он значительно уступает газобетону синтезного твердения. В первую очередь, это заключается в более низком уровне морозостойкости, прочности и повышенной способности к усадке.
Производство данных изделий не вызывает значительных трудностей. Но при домашнем изготовлении процесс выпуска требует особой внимательности и отчасти — опыта. Так как неисполнение технологии и неправильное дозирование компонентов, может привести к отрицательным последствиям, в первую очередь, в отношении характеристик изделия и свойств.
Газобетон автоклавный и неавтоклавный имеют некоторые отличия. Это обосновано различным способом твердения и составом компонентов. Проанализировав основные свойства данных видов блока, сложно не согласиться с рекомендациями специалистов, советующими отдавать предпочтение именно автоклавным изделиям.
beton-house.com
Автоклавный газобетон: характеристика, технология, производство
Первостепенная задача каждого застройщика заключается в правильном выборе строительного материала. Из всего разнообразия, представленного на рынке, хорошо зарекомендовал себя искусственный камень — автоклавный газобетон, который является разновидностью ячеистых бетонов (пенобетона, газопенобетона). Учитывая то, что материал набирает популярности в частном строительстве, стоит разобраться, что это такое, и какими свойствами обладает. Также, необходимо знать, чем отличается неавтоклавный газобетон.
Характеристики
Блоки из ячеистого бетона имеют пористую структуру, которая образуется за счет наличия сферических пор. Размеры воздушных частиц составляют от 1 до 3 мм. Качество строительного материала напрямую зависит от равномерности распределения пор по всему объему камня и их закрытости.
Сырьевой состав газобетонов, производимых автоклавным и неавтоклавным способами, полностью идентичный. Смесь содержит следующие компоненты:
- Вяжущие вещества — портланд цемент М300-М400, негашеная известь, гранулированный доменный шлак, зола.
- Твердые компоненты — кварцевый песок мелкой фракции, зола-унос.
- Порообразователи — алюминиевая пудра ПАП-1/ПАП-2 или паста, содержащие активный металл 90-95%.
- Вода очищенная, без наличия солей (ГОСТ 23732).
- Модификаторы и присадки (не являются обязательными компонентами, и добавляются для улучшения эксплуатационных характеристик материала).
Реакция по образования пор происходит не на этапе смешивания, а непосредственно в формах. Водород, выделяющийся в результате химической реакции, пронизывает всю залитую массу и обеспечивает формирование воздушных частиц практически одинаковой величины с равномерным их распределением. Несмотря на идентичность компонентов, присутствует разница: физико-химический состав искусственного камня меняется под воздействием высокого давления и влажности. Внутри камня происходят глобальные изменения по прочности. При затвердевании в естественных условиях прочность блоков значительно ниже.
Виды и сфера применения
Блоки из ячеистого бетона подразделяется на 3 категории:
- Теплоизоляционный,
- Конструкционный.
- Конструкционно-теплоизоляционный.
Автоклавный газоблок плотностью до 400 кг/м2 является теплоизоляционным и применяется для строительства малоэтажных домов в районах с очень холодным климатом. Искусственный камень плотностью 700 кг/м2 относится к конструкционному типу и предназначен для создания несущих конструкций и зданий высотой не выше 3-х этажей. Такой материал требует дополнительной теплоизоляции. Конструкционно-теплоизоляционные блоки плотностью 500 кг/м2 универсальные: обладают достаточно высокой прочностью и хорошей теплоизоляцией.
Благодаря малому весу строительные блоки выпускаются в увеличенных размерах. Длина составляет 625 мм, высота — 200, 250 мм, ширина — 100-400 мм. Большие параметры способствуют значительному ускорению возведения зданий, и упрощают кладку стен.
Отличия
В чем же заключаются основные отличия двух видов газобетонных блоков? Сравнивать материалы удобнее всего с помощью таблицы.
Характеристики автоклавного газобетона | Характеристики неавтоклавного газобетона |
Искусственный синтезированный камень. | Застывший раствор с порами естественным путем или с применением пара при нормальном атмосферном давлении. |
Структура готового блока одинакова по характеристикам и свойствам в любой точке. | Свойства и характеристики отличаются в пределах одной партии. |
Полностью отсутствуют усадочные деформации. Необходимая прочность достигается на этапе производства и автоклавирования. Показатель усадки не превышает 0,4 мм/м. | Показатель усадки в 10 раз больше — составляет до 5 мм/м. |
Нарезка на блоки осуществляется на специализированном оборудовании с помощью струн. В результате такой механической обработки получаются стеновой материал идеальной геометрической формы. Размеры регламентированы ГОСТ. Допустимые отклонения составляют по длине — до 3 мм, по ширине — до 2 мм, по толщине — до 1 мм. Укладка искусственного камня осуществляется на клеевой раствор, который создает более тонкий слой, по сравнению с цементно-песчаным вариантом. Клеевой состав придает строению монолитности, повышает теплоизоляционные свойства и исключает образование «мостиков холода». Минимальный показатель отклонений способствует экономии кладочного клеевого состава. | Для изготовления блоков применяется разборная опалубка с ограниченными циклами использования. Допускаются значительные отклонения геометрических размеров — по толщине до 5 мм (ГОСТ 1989 года). Из-за большого разбега в геометрии:
|
Блоки толщиной всего 40 см и плотностью D400-D500 обладают необходимыми требованиями по теплозащите и прочности. | Для обеспечения необходимой теплоизоляции без использования утеплителя толщина камня должна составлять около 65-70 см. Плотность ячеистого бетона минимум D700. |
Морозостойкость, (циклы) — F20 | Показатель морозостойкости — F15 –F35 |
Период эксплуатации — 200 лет. | Эксплуатационный период — 50 лет. |
Прочность по ГОСТ — B2,5-B5 | Прочность по ГОСТ — B1,5-B2,5 |
Высокие показатели экологичности. | Экологически чистый материал. |
Благодаря автоклавной обработке газобетон обладает улучшенными физико-техническими свойствами и внешним видом.
Технология
Высокое качество строительного материала может гарантировать только предприятие, имеющее специализированное оборудование, где производство проходит в строгом соблюдении технологических процессов на всех этапах. Технология производства автоклавированием предусматривает применение герметической камеры, где застывший раствор с порами придается термической обработке под высоким давлением. Такая технология позволяет получать строительный материал с улучшенными свойствами и характеристиками, которых невозможно добиться в обычных условиях. Изменения в структуре искусственного камня выполняются на молекулярном уровне. На современных заводах автоклавного газобетона продукция соответствует европейским стандартам качества.
Пропорции неавтоклавного и автоклавного продукта регламентированы и рекомендованы в следующем соотношении компонентов:
- Портландцемент — от 35 до 49%.
- Известь негашеная — от 12 до 26%.
- Силикаты кальция — примерно 2,6%.
- Хлорид кальция — от 0,18 до 0,25%.
- Пудра алюминиевая — от 0,06 до 0,1%.
- Вода несоленая, до получения 100% объема.
Процентное соотношение компонентов и состава устанавливается опытным путем. В зависимости от прочности и условий затвердевания, показатели варьируют в широком диапазоне. При использовании автоклавирования из продукта выводятся излишки влаги, и завершается процесс твердения.
Производство
Производство автоклавного газобетона проходит в определенной последовательности:
- Песок и вода соединяются, после чего частицы измельчаются в песчаный шлам.
- Далее поэтапно вводятся остальные компоненты — цемент, известь, поваренная соль. Время смешивания длится 5 минут и готовый раствор заливается в подготовленную опалубку, поверхность которой смазывается маслом.
- В форме происходит основной цикл химической реакции с участием высокодисперсного алюминия. В результате водородной реакции образуются пузырьки, вспенивающие раствор и создающие пористую структуру, занимающую до 80% всего объема. Бетонная масса увеличивается в объем, заполняя всю форму.
- Время дозревания и отвердения длится примерно 2—3 часа.
- Застывшая масса разрезается промышленными струнами на блоки соответствующих размеров.
- Финальная стадия обработки включает пропаривание заготовок в автоклаве при температуре 180—200° и под давлением не выше 1,2 МПа. Процесс кристаллизации продолжается на протяжении 12 часов.
Для того чтобы изготовить неавтоклавный газоблок в домашних условиях обязательно потребуется бетономешалка. Перед приготовлением компоненты взвешиваются в отдельных емкостях: на одну часть пудры алюминиевой берется 50 частей воды и добавляется стиральный порошок. Получившаяся смесь тщательно перемешивается до тех пор, пока на поверхности не останется металлических частиц. При заполнении форм следует учитывать особенности геометрии неавтоклавного бетона. Когда внутри продукта начинается процесс пенообразования, поверхности, не ограниченные опалубкой, вздымаются. Поэтому в верхней плоскости образуется так называемая «горбушка», размеры которой могут достигать 7% от общего объема блока. Такое вздутие обязательно удаляется.
Повышенный спрос на искусственный камень привел к образованию национальной ассоциации производителей автоклавного газобетона. На профессиональном уровне решаются проблемы отрасли, связанные с производством газобетона. Разрабатываются современные требования к качеству строительного материала.
Преимущества
Основные преимущества автоклавного газобетона заключаются в:
- экологичности — в составе нет вредных примесей;
- повышенной огнеупорности и способности удерживать процесс горения на протяжении 7 часов и более;
- низкой теплопроводности;
- точной и стабильной геометрии блоков, что позволяет создавать ровные и гладкие поверхности граней, оформлять наружные и внутренние углы;
- повышенной паро- и воздухопроницаемости, за счет чего стены зданий «дышат» и исключается образование конденсата;
- легком весе — как результат низкой плотности;
- устойчивости к влаге, воздействиям микроорганизмов и процессов гниения;
- обеспечении оптимального микроклимата в помещениях независимо от сезона.
К достоинствам газобетона автоклавного твердения относится наличие в составе минерального образования — тоберморита. Под воздействием высокой температуры и давления камень приобретает повышенную механическую прочность и безусадочность. Благодаря созданным условиям значительно ускоряется затвердение массы, что является важным моментом при крупномасштабном производстве.
Крепление в стенах навесного оборудования, мебели осуществляется при помощи специальных анкеров, выдерживающих до 350 кг.
Применение
Производство автоклавным способом значительно расширило область применения продукции из ячеистого бетона. Повышенным спросом пользуется материал у индивидуальных застройщиков. Возводятся коттеджи и малоэтажные дома из автоклавного газобетона, здания промышленного и коммерческого назначения.
Отзывы
Зная, чем отличаются материалы автоклавного и естественного отвердевания, проще делать выбор. Застройщики отметили такие особенности автоклавного газобетона:
- Простота обработки присутствует при возведении дома с арочными внутренними перегородками. Для выпиливания проемов на месте применялась обычная ручная пила, при этом края не осыпаются и на работу не уходит много времени. Недостатком является потребность в армировании.
- Отсутствуют проблемы при кладке и распиле. Для контроля уровня применяется обычный шнур. Из-за неправильного хранения блоки намокли даже от несильного дождя, но восстановили свой вес через 4 дня. Очень важно подготавливать площадку правильно.
- Проживание в доме из газобетонных блоков с толщиной стен в 600 мм достаточно уютно и комфортно. Очень тепло, что снижает расходы на обогрев помещений. В наружном утеплении отсутствует необходимость.
- Высокая цена материла и доставки. Но затраты компенсируется, за счет быстроты строительства, небольшого количества кладочного раствора и отсутствия дополнительной теплоизоляции.
Даже несколько отзывов позволяют понять, что лучше использовать автоклавные блоки, которые обладают улучшенными характеристиками.
betonov.com
характеристики и марки газобетонных блоков
Этот строительный материал считается разновидностью ячеистых бетонов. Камень искусственного происхождения, имеющий пористую структуру, состоит из цементного материала, песка кварцевого, пудры алюминиевой, извести и чистой воды. Технологический процесс газобетонного материала считается уникальным, но встречаются умельцы, способные неавтоклавным методом изготавливать блоки, используя самодельное оборудование. Из истории известно, что впервые материал был изготовлен более ста лет тому назад в чешской столице. Удивительно то, что рецептура приготовления газоблочного материала до настоящего времени не изменилась. Сегодня рассмотрим, какие виды газобетона бывают.
Состав блока
Основные ингредиенты, используемые в производственном процессе, уже вспоминались выше. Кроме них в состав могут добавляться гипсовый материал, шлак, зола и иные отходы промышленного производства.
Газообразование достигается за счет алюминиевой пудры, взаимодействующей с негашеной известью и выделяющей водород, от которого остаются многочисленные пустотные участки. Как только газобетонная масса затвердевает, ее можно резать на камни необходимых размеров, после чего блоки подвергаются повторному твердению.
Характеристики материала
Газобетонный блок обладает следующими показателями:
- значение прочности – варьируется от 10 до 40 кгс на квадратный сантиметр. Параметр зависит от обработки в автоклаве;
- объемная масса – от 400 до 600 кг в кубическом метре;
- тепловая проводимость – 0.12 Вт;
- устойчивость к температурным перепадам – F100;
- усадка – от 0.2 до 5 мм на метр кладки;
- влагопоглощение – не более двадцати процентов;
- уровень паропроницаемости – высокий;
- устойчивость к воздействию открытого пламени – не менее семи часов;
- шумонепроницаемость – 50 Дб;
- максимальное строительство – не более трех уровней в высоту.
Газоблок имеет характеристики и по маркам. Чем больше данное значение, тем выше показатель плотности растворной массы.
Строительный рынок представляет следующие марки:
- d600 – материал применяется при строительстве объектов с навесными вентилируемыми фасадами, отличается хорошей прочностью;
- d500 – применяют блок данной марки для возведения стен монолитных сооружений;
- d400 – специалисты рекомендуют применять такие блоки при теплоизоляции, устраивать из них проемы для дверных конструкций;
- d350 – применяют их при утеплении стен. Материал отличается хрупкостью, в продаже встречается достаточно редко.
От марки газоблока зависит значение прочности материала.
Основные виды
Их всего три:
- конструкционный – блок с высоким показателем прочности, используется при возведении стен наружного типа и перегородок. Теплопроводность материала низкая, дополнительного утепления не требуется;
- теплоизоляционный – материал с низким показателем тепловой проводимости. Данная категория блоков отличается способностью сохранять тепло внутри помещения, но плохой прочностью. Материал рекомендован для утепления зданий, устройства внутренних перегородок. С его помощью можно создать дополнительную защищенность в холодный сезон; конструкционно-теплоизоляционный – прочность такого материала дает возможность возводить трехэтажные сооружения, не утепляя стены. Такой стройматериал считается популярным, так как из него можно построить частный дом с высоким теплоизоляционным показателем.
Классификация по формам
Разделяют строительный материал по его формам. По такому признаку бывают следующие разновидности газоблоков:
- прямоугольные – из такого материала возводят несущие стены и перегородки;
- армированные – нужны для обустройства потолков;
- Т-образные – из таких блоков монтируют перекрытия. U-образные – используются при обустройстве оконных и дверных проемов. С применением таких материалов значительно сокращаются денежные расходы, ускоряется рабочий процесс;
- дугообразные блоки.
Разделение материала по процессу изготовления
На основании производственного процесса различают следующие виды газоблоков:
- Неавтоклавный – такие блоки не подвергаются специальной обработке в печи. Твердение и высыхание материала происходит в простых условиях.
- Автоклавный – блок проходит обработку в специальной печи. Температурный режим при этом равен двести градусов, давление – двенадцати барам. Данный вид материала считается наиболее предпочтительным при строительстве, потому что за счет производственных технологий получает высокий уровень прочности и способность сохранять тепло внутри помещения. За счет автоклавной печи пористые участки внутри блока распределяются равномерно.
Виды блока по вяжущему компоненту
По данному признаку выделяют следующие разновидности газоблоков:
- известковые – в общей массе материала содержится не менее пятидесяти процентов извести. Сюда же добавляют гипс, шлак или цементный состав, но не более пятнадцати процентов от общего количества сырья;
- цементные – половину сырья составляет портландцемент;
- шлаковые – основу составляют шлак и гипс, который можно заменить известью или щелочью;
- зольные – основа блока – зола;
- смешанные – состоят из шлака и извести, добавляется цемент в количестве пятнадцати – пятидесяти процентов от общего веса сырья.
Виды газобетонных блоков определяются типом кремнеземистых компонентов.
Принято различать:
- произведенные на основе природного песка. Зачастую при этом используют песок кварцевый, иногда применяются и другие типы;
- изготовленные с применением вторичного сырья производственной деятельности. К ним следует отнести золу с ТЭС, вторсырье, полученное после обогащения различных видов руд.
Размеры газобетонных блоков
Исходя из параметров, материал разделяется на стеновой и перегородочный. Блок, толщина которого равна 7.5 – 20 см, считается материалом для устройства перегородок.
Блочные камни с более высокими значениями по ширине используются для строительства стен.
Достоинства и недостатки материала
Какие бывают блоки, мы выяснили. Теперь рассмотрим их несомненные качества, которыми газобетон выделяется от других строительных материалов:
- блок легче простого кирпича в три – пять раз, что дает возможность изготавливать их со значительными параметрами. Такая особенность позволяет увеличить скорость строительных работ;
- небольшой показатель тепловой проводимости зависит от количества пустотных участков;
- камень легко обрабатывается ручными инструментами. По такому признаку его можно сравнить с древесиной. Он без проблем распиливается, сверлится и строгается;
- показатель паропроницаемости позволяет стенам «дышать», за счет чего внутри помещения всегда поддерживается комфортный микроклимат;
- экологическая чистота материала.
Имеются в материале и негативные моменты:
- из него строят здания, высота которых не превышает трех этажей. Обусловлено это ограниченными возможностями газобетонного блока к сжатию;
- из-за того, что газоблок способен напитываться влагой, его внешние поверхности необходимо отделывать облицовочным материалом;
- материал неавтоклавного изготовления дает существенную усадку, оказывая негативное воздействие на прочность стен.
Область применения и особенности транспортировки блоков
Из газобетона возводят стены частных объектов с максимальной высотой в три этажа. Кроме того, строят технологические здания и помещения для офисов. В наше время материал часто применяется для наращивания этажности старых объектов, потому что он отличается небольшим весом и не создает большую нагрузку на существующую фундаментную основу и старые стены.
При перевозке таких блоков их следует укладывать на поддоны из деревянного материала, упаковывать термоусадочным полиэтиленом. Разрешается перевозить блоки открытыми платформами для транспортировки грузов. Доставку газобетона осуществляют различными видами транспорта – водным, железнодорожным, автомобильным.
Заключение
Как следует из отзывов, строительство объектов из такого материала следует поручать опытным специалистам, которые все работы выполнят оперативно и с хорошим качественным уровнем.
Кстати, при возведении кладки рекомендуется применять специальный клеевой состав, нанося его на блочную поверхность кельмами.
betonov.com
что это такое, характеристики, отзывы
В строительной сфере быстро приобретает популярность газобетонный материал. Блоки постоянно лидируют по продажам благодаря тому, что большинство застройщиков стремятся для своего загородного дома приобрести именно их. Применение такого материала дает возможность значительно ускорить темп строительных работ. Существенно уменьшаются денежные расходы, связанные со строительством стен и внутренних перегородок. Но кроме достоинств газобетонные блоки отличаются и негативными моментами, про которые забывать не следует. Необходимо отметить, что при определенном внимании некоторые проблемы, связанные с материалом, возможно легко и надежно нивелировать.
Что это
Итак, газобетонные блоки – что это такое? Под данным названием понимают искусственно изготовленный камень из бетонного раствора с ячеистой структурой. При этом не следует его путать с пеноблоком.
В газобетоне пустотные участки создаются в процессе химической активности, происходящей в бетонной массе в момент затвердевания. А в варианте с пеноблоками поры образуются за счет добавления в растворную массу заблаговременно подготовленной пены.
Случается, что газобетонный материал путают с газосиликатными блоками. По факту второй вариант считается подвидом газобетона. Исходное базовое сырье в любом случае применяется одно. Отличие состоит в пропорциональных отношениях и технологии затвердевания бетонного раствора. Отсюда и возникают отличия материалов по данным прочности, тепловой проводимости и плотности.
Состав
В смесь для газобетонных блоков включены определенные компоненты:
- цементный состав;
- песок речной;
- известь негашеная;
- чистая вода;
- алюминиевая пудра, используемая в виде газообразователя.
Технические характеристики
Газобетонный блок – это строительный камень, обладающий следующими характеристиками:
- Прочность газобетонных блоков – значение максимальное, несмотря на относительную легкость камня. Блок считается идеальным вариантом, сочетающим в себе прочность, небольшой вес и хорошую теплоизоляцию. Прочность на сжатие будет зависеть от марки бетона и варьироваться в пределах от 1.5 до 3.5 кгс на квадратный сантиметр.
- Легкость обработки – еще одно неоспоримое отличие от остальных материалов. Блок без особых усилий режется и пилится ручными инструментами, чтобы получились элементы с нестандартными размерами и формами. Кроме того, никогда не возникнет вопрос, чем сверлить блок – подойдет даже ручная дрель.
- Теплоизоляционные качества – блоки марки d500 и d600 считаются теплоизоляционным и конструкционным материалом, отличающимся хорошей морозостойкостью. Это дает возможность стенам сохранять тепло внутри помещения даже в зимнее время. В летний сезон объект из газобетонного материала сильно не нагревается. Микроклимат в помещении всегда отличается комфортностью.
- Шумоизоляционные качества – блок может гасить посторонние звуки, и способность эта зависит от марки раствора и его густоты, ширины стен и способа их кладки.
- Предел огнестойкости – блок относится к негорючим стройматериалам. Объекты из газобетона имеют I и II степень по пожарной безопасности.
- Экологичность – радиоактивность материала гораздо ниже допустимых значений. Во время эксплуатационного периода блоки не образуют токсинов. По уровню экологичности камень не уступит материалам природного происхождения.
- Вес газобетонного блока – камень стандартных габаритов, равных 62.5 х 10 х 25 см, весит не более восьми килограмм, имея при этом средний показатель плотности, равный 500 кг на кубический метр. Это дает возможность существенно снизить расходование кладочной смеси и сократить сроки выполнения работ.
- Биологическая устойчивость – материал представляет собой неблагоприятную массу для образования плесени, бактерий и грибка. По данному показателю блок превосходит древесину, не нуждается в обработке антисептическими средствами.
Виды газобетонных блоков
Параметры газобетонных блоков установлены ГОСТом 31360 2007 и другими документами, зависят от предназначения изделия и технологических особенностей затвердевания бетона.
Но довольно часто в реализации находятся газобетонные блоки от производителя, в которых параметры длины, ширины и высоты предусматриваются определенными техническими условиями. Плюс в том, что блок режется простой пилой, и подогнать камень под необходимые габариты несложно.
По ГОСТу формы для газобетонных блоков должны отличаться следующими размерами:
- толщина (ширина) – от 10 до 50 см;
- длина – 60 (62.5) см;
- высота – 20 – 30 см.
От показателя плотности блочного материала будет зависеть его прочность и вес. Но чем материал плотнее, тем пустот в нем содержится меньше, что оказывает положительное влияние на показатель тепловой проводимости.
Блоки разделяют на три вида:
- теплоизоляционный – d300 – d500, применяется при утеплении стен и строительстве тонких перегородок в помещениях;
- конструкционно-теплоизоляционный – d600 – d800, используется для внутренних перегородок в домах;
- конструкционный – d900 – d1 200, из такого материала возводят стены несущего и внешнего типа.
Независимо от марки газобетонных блоков и их предназначения, камни изготавливаются в форме параллелепипеда с прямыми углами и плоскими гранями. Но всегда можно найти варианты со специальными вырезами, облегчающими захват, с пазо-гребневой системой, дугообразные газобетонные блоки, внутренняя часть которых заполняется бетоном.
Технология производства
Из чего делают газобетонные блоки, мы выяснили. Теперь рассмотрим технологических процесс.
В момент смешивания негашеной извести, алюминиевого порошка и воды начинает образовываться водород, формируя в застывающей массе огромное количество пор, которые в некоторых марках камня занимают не менее восьмидесяти процентов от общего объема.
Чем больше пустотных участков, тем меньше вес газобетона и ниже его прочность. Кроме того, понижается тепловая проводимость камня.
Приготовленный состав газобетонного блока разливается по формам необходимых размеров, и его затвердевание происходит либо на складе, либо в автоклавной установке. Применение автоклава создающего давление от 10 Атм и температурный режим до 200 градусов, позволяет изготовить прочный материал.
Данную технологию используют на предприятиях, изготавливающих газоблоки для строительных работ.
Области использования
Теперь понятно, как делают газобетонные блоки. Предлагается разобраться с их применением.
Блоки считаются прекрасным конструкционным и теплоизоляционным материалом для строительной сферы. Из них строят жилые объекты и постройки сельскохозяйственного предназначения. Кроме этого, блоки используют при обустройстве общественных, административных и промышленных зданий, строительстве больничных и учебных заведений.
По своим свойствам материал считается лучшим для строительства стен и перегородок. Очередное предназначение – перестройка и реставрация старых объектов.
Благодаря своим вентиляционным качествам, блоки из газобетона используются для обустройства подвалов и фундаментных основ. Но данная сфера использования требует дополнительных проверок на надежность и продолжительность срока службы газобетонных блоков.
Достоинства и недостатки
Вес и хорошая прочность значительно выделяют газобетон среди остальных стройматериалов, из которых возводят стены. Потребителя привлекает ряд качеств, связанных с сохранностью тепла, защитой от посторонних шумов и способностью противостоять открытому огню.
Блоки изготавливают по различным размерам, что дает возможность подобрать необходимые параметры и формы, чтобы соорудить любую конфигурацию, заданную проектом.
Еще один аргумент – сокращение строительных сроков. Если мы строим из газобетонных блоков, то значительно уменьшается время для проведения работ, снижается потребность в кладочном растворе. При правильной перевязке газобетонных блоков за короткий срок может получиться достаточно прочная стена.
Мы помним, из чего сделан блочный материал. Это дает право уверенно заявлять, что блоки относятся к экологически чистому стройматериалу, не оказывающему негативного воздействия на организм человека.
Кроме того, стоимость газобетонного блока достаточно приемлема для большинства потребителей. С таким материалом никогда не возникнет проблем в плане «на что сажать» камни или «чем покрасить изнутри» стены.
Вспоминая все о газобетонных блоках, необходимо сказать про отрицательные моменты. Структура материала такова, что он способен «дышать». За весь эксплуатационный период в порах накапливается влага, что приводит к разрушению целостности камня.
Объекты, возведенные из такого материла, подразумевают выполнение внутренней и внешней отделки. Данная мера значительно увеличит их срок службы.
Отзывы
Как следует из отзывов владельцев, газобетонные блоки отличаются гигроскопичностью. Если не устроить гидроизоляционный слой, то стены довольно быстро напитаются водой и начнут разрушаться. Кроме того, необходимо следить, чтобы не было промерзаний. Лучше всего регулярно жить в данном помещении, чтобы внутри комнат поддерживался необходимый температурный режим.
От опытных строителей всегда можно узнать, как сделать газобетонные блоки своими руками, для чего используется гидрофобизатор.
betonov.com
виды, изготовление в домашних условиях, видео
Газобетон – это искусственный камень, который используют для возведения стен в индивидуальном строительстве. Он подходит для сооружения несущих конструкций, внутренних перегородок и заполнения межкаркасных пространств. Газоблоки не дают большой нагрузки на фундамент, поскольку имеют ячеистую структуру и малый вес. Это экономичный стройматериал, обладающий высокими теплоизоляционными свойствами.
Оглавление:
- Особенности и виды стройматериала
- Пропорции компонентов
- Методика производства своими руками
Состав и способ получения газобетона
Существует несколько типов классификации ячеистого бетона: в зависимости от назначения, формы, технологии производства и состава.
1. По способу обработки различают автоклавный и неавтоклавный газобетон.
2. По назначению газоблоки могут быть теплоизоляционным, конструкционным или конструкционно-теплоизоляционным. Они имеют определенную маркировку, например, газобетон d500 относится к классу конструкционно-теплоизоляционных блоков.
3. По форм-фактору делятся на U-образные, прямые и паз-гребневые.
Газоблоки изготавливают из песка, цемента, извести, воды, гипса и алюминиевой пудры. Также в производстве могут использоваться вторичные и побочные промышленные материалы, такие как шлак и зола. В зависимости от состава газобетона, его классифицируют на:
- цементный;
- шлаковый;
- известковый;
- зольный;
- смешанный.
В искусственно синтезированный камень строительная смесь преобразуется лишь при определенных условиях. Для его получения используют технологию автоклавного затвердения. В этом случае состав застывает под влиянием насыщенного пара и высокого давления, меняя свою структуру. В смеси образуется минерал тоберморит, который придает материалу прочность. Таким образом получают автоклавный газобетон.
Бетон, затвердевающий в естественных условиях, называют неавтоклавным. Он имеет ячеистую структуру, но отличается по своим свойствам от газоблоков, изготовленных по специальной технологии. Этот стройматериал больше подвержен усадке при эксплуатации, поэтому его целесообразно применять в случае небольших нагрузок. Чтобы увеличить прочностные характеристики неавтоклавных блоков, в исходный состав добавляют различные армирующие вещества и наполнители. Снизить усадочную деформацию позволяет применение полиамидных пластмасс при армировании.
Производство неавтоклавных блоков не требует дорогостоящего оборудования, поэтому их можно сделать самому.
Газобетон своими руками
Процесс производства состоит из нескольких этапов:
- подбор и смешивание компонентов;
- заполнение форм раствором;
- выдержка состава для набора прочности;
- извлечение из форм.
В универсальном составе для получения газобетона содержится цемент, песок, известь, алюминиевая пудра. Исходные добавки и их пропорции могут меняться, в зависимости от наличия сырья и требований к готовому стройматериалу. Например, в автоклавном производстве песок иногда заменяют золой или шлаком. А для получения стройматериала с меньшей плотностью можно делать газобетоны на основе смол ТЭС.
При изготовлении газобетона в домашних условиях необходимо правильно рассчитать соотношение расходных материалов и учесть особенности укладки и погрешности замеров. Но существуют и стандартные рецепты смеси для газоблоков, в которых указаны следующие пропорции:
- Цемент – 50-70 %;
- Вода – 0,25-0,8 %;
- Газообразователь – 0,04-0,09 %;
- Известь – 1-5 %;
- Песок – 20-40 %.
Данные вещества используются и при автоклавном производстве. Ориентируясь на приведенное в рецептуре соотношение, можно рассчитать приблизительное количество компонентов, которые войдут в состав на 1 м3 газобетона:
- Портландцемент – 90 кг;
- Вода – 300 л;
- Газообразователь – 0,5 кг;
- Известь – 35 кг;
- Песок – 375 кг.
Однако идеального состава в домашних условиях можно добиться лишь опытным путем, поскольку многое зависит от качества исходных компонентов. Повлиять на течение химической реакции может как температура воды, так и марка цемента.
Инструкция по самостоятельному изготовлению неавтоклавного газобетона
Для получения газоблока дома не потребуются сложная аппаратура и инструменты. Главное – четко следовать пунктам приведенного ниже пошагового руководства и использовать компоненты в определенном соотношении, а не «на глаз».
1. Исходя из указанных пропорций вычислить необходимое количество ингредиентов.
2. В первую очередь, необходимо смешать портландцемент с предварительно просеянным песком.
3. В полученную смесь влить воду и все тщательно перемешать.
4. Добавить в раствор другие компоненты. Алюминиевая пудра всыпается в последнюю очередь. В приготовлении как неавтоклавного, так и автоклавного газобетона одинаково важен процесс смешивания ингредиентов. Для равномерного распределения воздушных пузырьков лучше использовать бетономешалку.
5. Полученный раствор разливается в специальные формы, которые изготавливаются из металлических листов или деревянных досок. Чтобы застывший газобетон было легче достать, лучше использовать разборные конструкции. Кроме того, форму рекомендуют смазывать машинным маслом, разведенным с водой.
6. Заливать смесь нужно наполовину, поскольку она в процессе химической реакции расширяется практически вдвое. Этот процесс занимает около шести часов, после чего можно выравнивать блоки, срезая выступившую массу.
Формирование в этом случае длится дольше, чем для автоклавного газобетона – требуется не менее 12 часов, чтобы смесь затвердела. Для ускорения процесса застывания состава рекомендуют добавить растворимые соединения натрия (соду) на этапе приготовления раствора. Марочную прочность материал набирает после 28 дней выдержки. Готовый неавтоклавный газоблок, приготовленный своими руками, подходит для малоэтажного строительства, например, для возведения одноэтажного дома или гаража.
stroitel-list.ru
Все о газобетонных блоках: характеристики и особенности работ
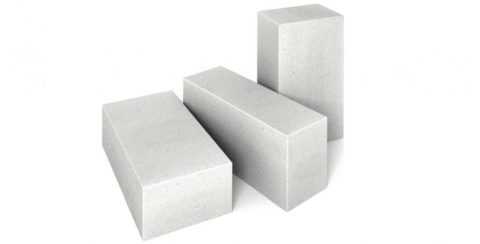
Блоки из газобетона
Газобетонные блоки приобрели широкую популярность среди будущих владельцев строений. Объясняется это тем, что материал отвечает практически всем основным требованиям, предъявляемым к изделиям, предназначенным для строительства.
Это касается, в первую очередь, набора свойств и эксплуатационных показателей. Не менее важным фактором также является низкая стоимость блока, привлекающая все большее количество потребителей.
Данная статья посвящена обзору этого материала, и мы постараемся в ней рассказать все о газобетонных блоках.
Содержание статьи
Характеристика газоблока
Газоблок – особенный материал, и в первую очередь, мы обратим внимание на его состав, виды, основные свойства, а так же дадим ответ на вопрос: что такое газобетонный блок?
Состав и технические свойства материала
Газобетонный блок является изделием, изготавливаемым из материала-представителя ячеистых бетонов. Основное его отличие заключается в наличии пористой структуры, которая определяет во многом основной набор характеристик изделий.
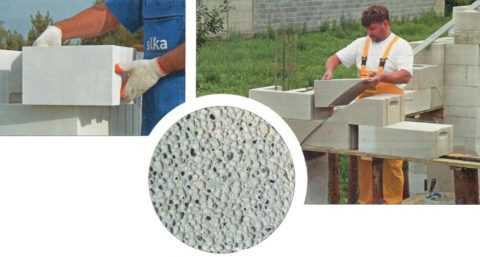
Структура газобетонного блока
Из чего состоит газобетонный блок? Материал представляет собой смесь извести негашеной, воды, цемента, песка (чаще кварцевого), и газообразователя. В соответствии с рекомендацией ГОСТ, последний используется в виде алюминиевой пудры либо пасты на ее основе.

Состав блоков из газобетона
Во время изготовления, между негашеной известью и алюминиевой пудрой происходит химическая реакция, которая провоцирует образование ячеек. Количество последних определяет вес, плотность и теплопроводность изделий и, как следствие, сферу их применения.
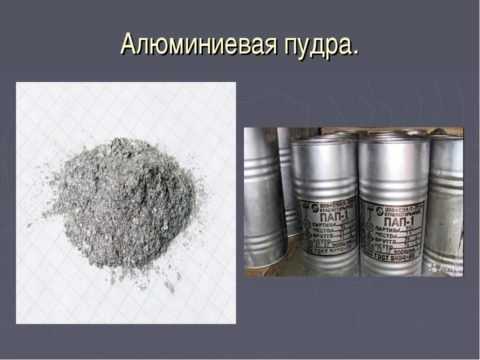
Алюминиевая пудра
Рассмотрим более подробно свойства газобетонных блоков:
- Материал отличается низким коэффициентом теплопроводности. Значение находится в промежутке между 0,09 и 0,34 Вт*мС. Это означает, что здание будет не только теплым, но и экономичным в отношении обогрева помещения в зимнее время года.
При возведении дома, застройщикам, использующим блок газобетонный в качестве основного материала, удастся снизить затраты на утепление — в особенности, если при кладке будет применяться специализированный клеевой состав.

Толщина стены из газобетона в соответствии с теплопроводностью и сравнение с другими материалами
- Изделия характеризуются плотностью в 300-1200 (кг/м3). На данный показатель оказывает влияние концентрация цемента в растворе. Чем его больше, тем будущие изделия плотнее.
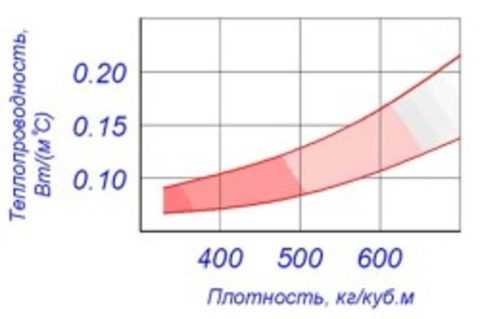
Соотношение плотности и теплопроводности газоблока
- Блок из газобетона отличается высокой маркой по морозостойкости. Достигать она может значения в 150 циклов. Оно указывает на то, какое количество циклов заморозки и оттаивания может выдержать газоблок.
На заметку! Если сравнивать материал с его конкурентами среди представителей легких бетонов, то большим показателем могут похвастаться не многие. Выделить можно керамзитобетон.
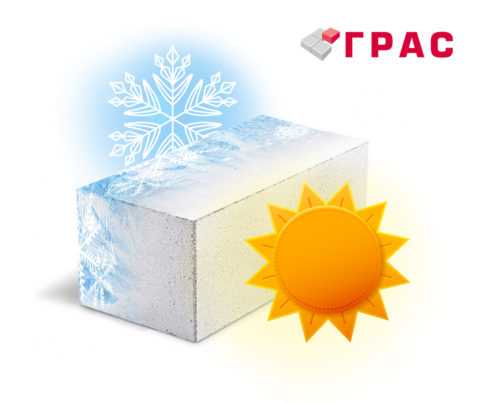
Газобетон — морозостойкий материал
- Долговечность газобетонных блоков также высока. Если в процессе строительства и отделки не допущено технических ошибок, то строение способно простоять длительный срок.

Долговечность позволяет использовать блок при строительстве многоквартирных домов
- Прочностные марки газобетонных блоков варьируются в промежутке от 1,5 до 15, и находятся в прямой зависимости от средней плотности материала.
Соответствие плотности и прочности
- Стоит отметить экологичность изделий, которая не оставляет сомнений. Из чего состоит газобетонный блок, мы уже разобрались и выяснили, что ни один из компонентов сырья не является опасным ни для человека, ни для окружающей среды.
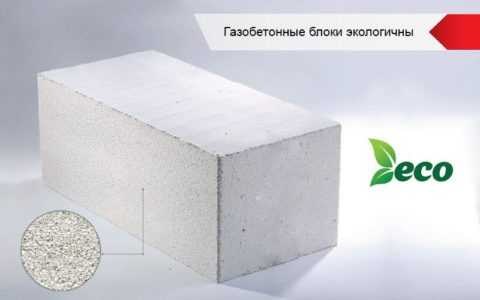
Газоблок — экологичен
- Влагопоглощение изделий по-настоящему высокое. Они гигроскопичны и нуждаются в защите в обязательном порядке. В противном случае, начнется процесс разрушения материала.

Газобетонный блок: водопоглощение приводит к разрушению
Видео в этой статье: «Газобетонный блок во влажных помещениях», содержит информацию об особенностях применения изделий при строительстве зданий, в которых будет преобладать влажность.
- Огнестойкость газобетонных блоков — налицо. В соответствии со стандартом качества, материал является негорючим.

Устойчив к воздействию высокой температуры
- Биологическая устойчивость – весомый плюс. Изделиям не свойственно образование грибка и плесени.
- Звукоизоляция газобетонного блока достаточно хороша. То же самое можно сказать и про паропроницание.
Все вышеуказанные свойства говорят не только о практичности использования материала, но и о высоких эксплуатационных характеристиках. Срок службы газобетонных блоков может достигать 200-300 лет.
Разновидности и сфера их применения
Теперь стоит обратить внимание на виды газобетонных блоков. Их классификация довольно обширна, и основывается на тех или иных показателях и факторах.
Изделия, как уже говорилось, могут обладать разными показателями средней плотности, что положило основу для их классификации, которая определяет область применения газобетонных блоков:
- Материал, характеризующийся плотностью в 300-400 (кг/м3) называется теплоизоляционным. Нагрузок он, разумеется, выдержать не может, а вот в качестве теплоизоляционного материала вполне подойдет.
- Конструкционно-теплоизоляционный вид более распространен среди потребителей. Он имеет плотность 500-900 (кг/м3). Такой показатель предполагает использование газобетонного блока при возведении перегородок и стен строений.
- Плотность в 1000-1200 кг/м3 характерна для конструкционного вида изделий. Они достаточно прочны для использования при сооружении несущих иных конструкций, на которые оказывается значительная нагрузка.

Блоки с разным показателем средней плотности, фото
Еще одна разновидность газобетонных блоков основана на методе твердения, который используется при изготовлении изделий:
- Материал может достигать марочной прочности в условиях обработки его в автоклавах. В таких условиях на блоки оказывается воздействие высоких температур и давления выше атмосферного. Своими руками такой блок изготовить не получится. Производство его возможно только лишь в заводских условиях.
- Неавтоклавный блок твердеет в естественных условиях. Изделия также могут быть подвергнуты тепловлажностной обработке с целью ускорения процесса твердения и повышения показателей некоторых свойств.
Обратите внимание! Автоклавный блок, как правило, несколько превосходит в показателях неавтоклав. Долговечность газобетонных блоков синтезного твердения значительно выше. Также их плюсом является лучшая геометрия, прочность, плотность и морозостойкость.
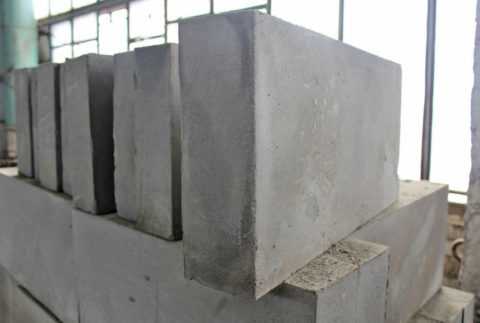
Неавтоклавное изделие
Геометрия газобетонного блока также устанавливает следующие его виды:
- Изделия первой категории обладают наилучшей геометрией. К ним в данном отношении предъявляются высокие требования. Отклонения не должны превышать более 1,5 мм по размеру.
Укладка таких блоков производится на клей с минимально возможной толщиной шва.
- Вторая категория — точность изделия характеризуется большими допустимыми отклонениями от линейного размера – до 2- х мм. Также допускаются сколы на углах и гранях не более 2-х штук на изделии. Укладку производят как на клей, так и на раствор.
- Третья категория чаще всего применяется для строительства хозяйственных помещений. Отклонения могут достигать 0,7 мм по размеру.
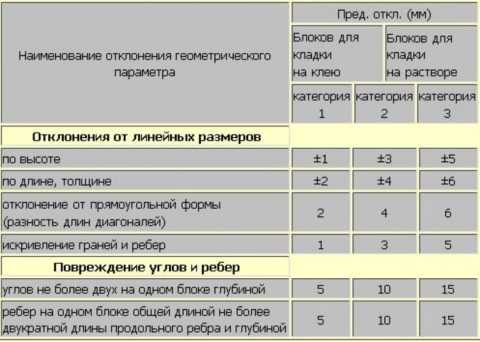
Геометрические отклонения по ГОСТ
На что ложится газобетонный блок третьей категории? Разумеется, на раствор. Толщина шва будет не маленькой, а, следовательно, и мостики холода увеличатся, поэтому строение требует серьезного утепления. Во многом, это объясняет применение газобетонных блоков с подобными отклонениями, указанное выше.
При изготовлении изделий, а, точнее, смеси для них, может быть использован разный тип вяжущего. В качестве него может выступать: цемент, шлак, известь, зола. Также вяжущее может быть смешанным.
Тип кремнеземистого компонента во многом влияет на некоторые показатели. Это касается соотношения плотности и теплопроводности изделий в сухом состоянии.
Компонентом может быть:
- Песок;
- Зола высокоосновная;
- Вторичные продукты промышленности.
В соответствии с назначением, блоки могут быть:
- Перегородочными. Как следует из названия, они применяются при возведении перегородок. Вот какой толщины может быть перегородочный газобетонный блок: 75 мм, 100 мм, 120 мм, 150 мм.
- Стеновыми. Габариты газобетонного блока, предназначенного для возведения стен, могут быть следующими: 625(600) *250(200) *300(400).
- Газобетонные u-образные блоки применяются зачастую при создании несъемной опалубки — например, при устройстве армопояса. Также их используют при монтаже перемычек.
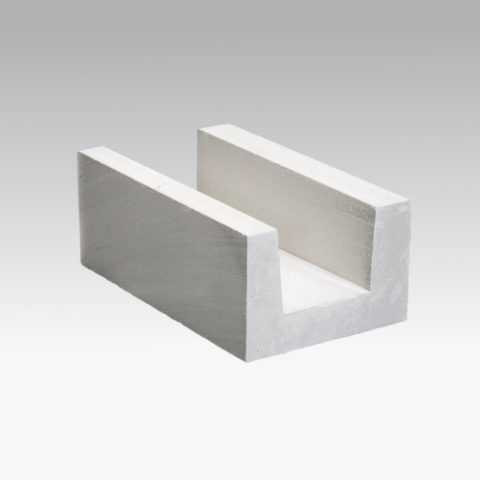
u образный газобетонный блок
Стоит отметить, что изделия могут иметь специализированные выемки и впадины, носящие названия паз и гребень. Их наличие помогает сделать кладку максимально ровной. Захват для блоков газобетона изготавливается с целью упрощения процесса работ для удобства каменщика.

Гладкий газоблок и изделие, имеющее паз-гребень
Положительные и отрицательные стороны изделий
Преимущества и недостатки газобетонных блоков характеризуются довольно обширным списком. Причём, достоинства значительно превышают минусы, однако рассмотреть стоит все качества. Сразу отметим, что многие из недостатков могут быть нивелированы при помощи технических приемов, о которых также будет сказано.
Итак, преимущества газобетонных блоков сводятся к следующему:
- Хорошая способность к сохранению температур.
- Морозостойкость изделия действительно на высоте.
- Прочностные и характеристики, и значения средней плотности позволяют применять блок при строительстве домов, высотой в несколько этажей.
- Предел огнестойкости газобетонных блоков достаточно высок. Материал относится по этому показателю к первому классу. Перегородка толщиной 20 см выстоит не менее 2,5 часов при одностороннем воздействии огня. При этом с обратной стороны температура поверхности не превысит +220 градусов по Цельсию.
- Экологичность обоснована составом изделий.
- Габариты газобетонных блоков позволяют значительно сократить процесс строительства.
- Легкость веса предполагает снижение нагрузки на основание строения. В случае, если предполагается, что дом будет легковесным и небольшим, фундамент может быть и облегченным.
- Большой выбор среди изготовителей и разнообразие размеров.
- Невысокая цена на изделия.
- Возможность самостоятельного производства газоблока гидратационного твердения. Инструкция приведена ниже.
- Толщина газобетонных блоков в 400 мм вполне достаточна для стены здания, расположенного в среднем регионе России. Для сравнения, это значение для других материалов может достигать и 60, и 70 мм.
- Произвести отделку стен из газоблока можно с использованием практически любых материалов. Главное, соблюдать технические требования.
- Материал легко поддается обработке. Его можно распилить, разрезать, придать желаемую форму.
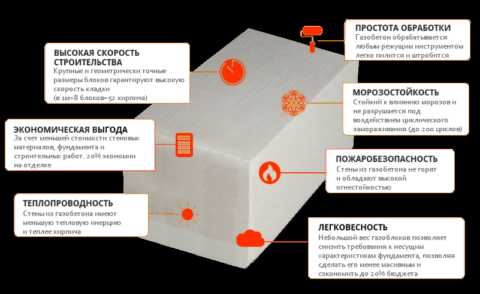
Преимущества газоблока
Теперь озвучим недостатки:
- Газобетонный блок склонен к усадке.
- Изделия очень гигроскопичны и впитывают влагу буквально как губка.
- Адгезию материала придется повышать, а это – дополнительные затраты денег и времени.
- Необходимо учитывать, что применение любых метизов для фиксации предметов к газобетонным стенам – недопустимо. Придется приобретать специальные.
- Блоки хрупкие, легко подвергаются механическим повреждениям.
- Пористая структура – это не только плюс, но и существенный минус. Если влага сумеет попасть в поры и кристаллизироваться, то структура блока будет со временем разрушена.
Особенности изготовления блока из газобетона
Раз уж мы решили рассказать обо всем, что касается газобетонного блока, давайте кратко рассмотрим процесс изготовления изделий. Для начала, изучим необходимый набор оборудования и дадим дельные советы при выборе сырья и поставщика его.
Оборудование и сырье
Оборудование может быть различным. Если говорить про автоклавные изделия, то оно может быть использовано 2-х типов: стационарное и конвейерное.
Последний вариант полностью автоматизирован. Процесс происходит достаточно быстро, объемы могут быть весьма впечатляющими. Минус – очень высокая стоимость комплекта.
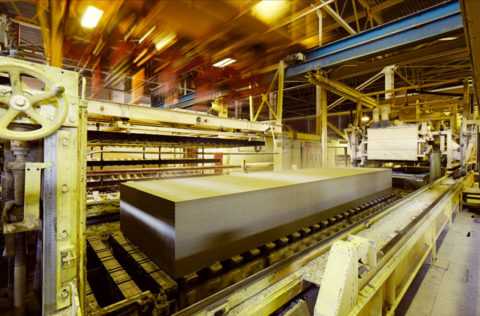
Фрагмент оборудование конвейерного типа
Стационарный тип характеризуется частичной автоматизацией. Участие человека необходимо проведении того или иного производственного этапа. Это уже зависит от комплектации. Объем выпуска может достигать 80 м3 в сутки. Это, согласитесь, тоже неплохой результат.
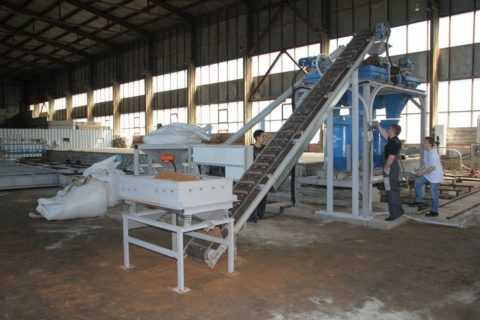
Стационарное оборудование
В случае, если решено производить неавтоклавный газоблок, то, помимо вышеуказанных типов, может быть применено и более простое оборудование: мобильная установка или просто комплект в виде бетономешалки и форм.
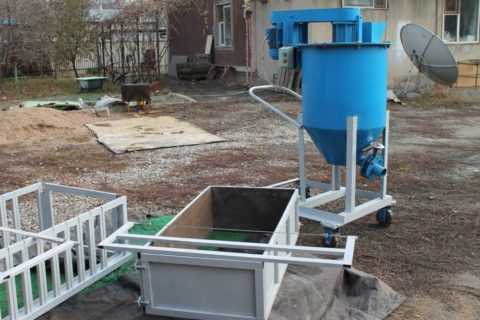
Мобильная установка для газобетона
Выбирая сырье, учитывайте следующее:
- Использование цемента марки ниже 400 не рекомендуется. В этом случае, изделия не будут обладать высокой плотностью, и будут более хрупкими.
- Материалы не должны быть просроченными.
- Цемент должен характеризоваться однородностью и быть без комков.
- Песок лучше использовать кварцевый.
- Внимательно изучите рынок строительных материалов перед покупкой. Стоимость сырья прямым образом влияет на себестоимость продукции.
Пропорции компонентов для изготовления газобетона
Описание технологического процесса
Как уже говорилось, отличие автоклава от неавтоклава заключается лишь в последней стадии обработки, технологический процесс крайне схож, поэтому мы рассмотрим этапы изготовления на примере выпуска блока синтезного твердения.
- Дозаторы подают компоненты в нужном объеме. В случае самостоятельного производства или за отсутствием приборов, измерять придется при помощи весов.
- Сырье попадает в смеситель, где происходит тщательное смешивание.
- Далее раствор попадает в формы, которые заполняются примерно на 1/3. Это необходимо с целью предотвращения вытекания излишков во время вспучивания смеси.
- Излишки удаляются, блоки выдерживаются несколько часов.
- Если залит единый пласт, то необходимо произвести резку. На производстве для этого применяется специальная машина – резательный комплекс. Оператор задает нужные параметры газобетонных блоков в отношении размера, а оборудование – режет.
- Последним этапом станет автоклавирование в течение, примерно, 12-ти часов.
- Впоследствии блоки отправляют на склад, предварительно запаковав.
Приемка и маркировка изделий
Приемка изделий осуществляется после проведения испытаний:
- Теплопроводность испытывается не реже одного раза в год.
- Морозостойкость и усадка – не реже 1 раза в 6 месяцев.
- Плотность, прочность и морозостойкость контролируется для каждой партии товара.
- За партию принимается количество блоков, произведенное по одной технологии, за одну смену, и имеющим одинаковый состав.
- В случае, если изделия изготавливаются малыми партиями, их могут объединить для проверки, однако все изделия должны соответствовать вышеуказанным требованиям.
- Контроль приемки ведется по ГОСТ 13015.1
Маркировка газобетонных блоков:
- Партии изделий, которые отличаются показателем прочности и плотности, маркируются несмываемыми красками.
- Маркировка наносится минимум на 2 изделия с противоположных сторон упаковки.
- Если плотность блоков равна значению от Д500 до Д900, то наносят только первую цифру. Если – Д1000-Д1200, то наносятся 2 цифры.
- Марка прочности указывается полностью. Например, если изделие имеет марку В3,5, то на блоках пишут: 3,5.
- Обязательным является нанесение предупреждения: «Боится влаги».
Приведем еще несколько примеров: газобетонный блок д 600, прочностью В 3,0 маркируется – 6-3,0. Газобетонный блок д700, прочностью В5 маркируется – 7-5.
Краткий обзор популярных производителей
А теперь давайте взглянем на перечень наиболее популярных брендов газобетонного блока.
Воспользуемся таблицей. Таблица 1. Газобетонные блоки разных производителей.
Наименование | На что делает основной упор производитель? |
![]() Газобетонные блоки «Грас» | Все специалисты организации проходят обучение в Германии и владеют знаниями о современных европейских методиках изготовления. Газобетонные блоки Грас производятся в виде стеновых, перегородочных и у-образных блоков. |
![]() Газобетонный блок aeroc | Производитель заявляет о сочетании повышенной плотности и прочности, и максимально низком коэффициентом теплопроводности. Газобетонный блок aeroc element является обозначением перегородочного блока. |
![]() Газобетонный блок teform | Компания гарантирует высокие показатели, и идеальную геометрию изделий в связи с использованием современного модернизированного оборудования. |
![]() Газобетонный блок биктон | Организация также оказывает строительные услуги. Указывает на высокое качество изделий. Предлагает проведение работ по возведению стен с использованием их продукции со скидкой. |
![]() Газобетонный блок вармит | Продукция отличается достаточно конкурентной ценой. Большой выбор размеров и широкая география доставки на выгодных условиях. |
![]() Газобетонный блок вкб | Упор делают на теплопроводность, отличную геометрию. |
Калькулятор Веса Дома
beton-house.com