Размер силикатного блока для стен: Размер силикатного блока для стен
Размер газосиликатного блока для стен в средней полосе |
Иногда застройщику требуется дополнительная информация. Например, каков оптимальный размер газосиликатного блока для стен в наших условиях (для стран бывшего СНГ)?
Сразу перейдем к делу и озвучим уже укоренившаяся правила у нас. Для быстрой кладки несущих стенок обычно применяется газосиликатный блок со стандартными размерами 200×300×600 мм.
Это, подчеркиваем, выжимка из коллективного опыта строительства. Однако, не всё так просто.
Очень большое значение при возведении стен из газобетона имеют климатические условия, в которых происходит строительство, а также вид последующих операции по утеплению или отделке.
Вполне понятно, что в регионах с более тёплым и мягким климатом толщину стен можно уменьшить и, наоборот, в холодных районах толщина стен должна быть увеличена. Поговорим об этом чуть более обстоятельно немного ниже, а пока представим размеры газосиликатных блоков для наружных стен от двух популярных производителей.
Почему мы приводим в таблице размеры еще и u-образных и пазогребневых блоков? Потому что в процессе возведения стен строитель неизбежно сталкивается с необходимостью обустройства армопояса и перемычек, а также блокираторов мостиков холода в вертикальных швах.
Рекомендуемые размеры газосиликатных блоков для наружных и внутренних стен
Со стандартными размерами продукции мы познакомились. Но какое конкретно значение выбрать из этих таблиц? И существуют ли определенные строительные нормы на этот счет? Да существует.
Согласно этим нормам минимальная толщина наружной стенки (однородной), возведенной из газосиликатных блоков, должна быть не менее 375 мм при том условии, что кладка ведется с применением клеевой смеси, а толщина шва не превышает 5 мм. Кроме того, такая толщина подразумевает дальнейшую отделку сайдингом или кирпичом. Если же в дальнейшем планируется отделка искусственным камнем, или плиткой, или простой штукатуркой, то ширина кладки должна быть увеличена до 500 мм.
Выпускаются ли отдельно газосиликатные блоки для внутренних стен (перегородок)?
Да, они имеют следующие размеры (они, впрочем, могут варьироваться)
Также в продаже для межкомнатных стен и перегородок можно встретить размер газосиликатного блока, равный 588×285×151 мм.
Egor11Газосиликатные блоки: размеры, ширина, вес
Блоки, выполненные из ячеистого бетона, являются разновидностью стенового материала. Они отличаются минимальной массой, упрощают возведение стен, обеспечивают хорошую теплоизоляцию помещений. Газосиликатные блоки размеры которых установлены нормами ГОСТа, используются для возведения подсобных объектов и жилых домов.
Достоинства и недостатки
Основными преимуществами материала являются:
- Незначительный вес снижает трудоёмкость при укладке.
- Высокая прочность позволяет возводить несущие стены.
- Отличные теплоизоляционные характеристики.
- Звукоизоляция почти в 10 раз выше, чем у кирпича.
- Возможность теплового аккумулирования помогает снизить расходы на отопление.
- Паропроницаемость помогает создать внутри объекта комфортный микроклимат.
- Не опасен для здоровья человека.
- Высокая сопротивляемость огню.
Любой строительный материал имеет недостатки. У газосиликатных блоков выделяют следующие отрицательные моменты:
- чрезмерное влагопоглощение;
- невысокая прочность и морозостойкость;
- усадка, приводящая к образованию трещин и расколов;
- образование грибка в условиях намокания.
Разновидность газосиликата
По назначению блоки условно разделяют на несколько видов:
- Стеновые. Камень используется для выкладывания наружных стен.
- Перегородочные. Кирпич применяется для монтирования стен внутри объекта.
Газосиликатные блоки условных групп различаются габаритами. С технической позиции для монтирования перегородок в помещении выгодно использовать изделия меньших размеров. Ведь это ещё и экономия финансовых вложений.
По форме газосиликатные блоки производят следующих видов:
- прямоугольные, используются для выкладывания несущих стен;
- пазогребневые – с двух сторон выполнены два выступа, при соединении между блоками не образовывается мостик холода;
- U-образные, применяются для выполнения армирующего пояса в верхней части стен и возведения перемычки.
К тому же производители выпускают блоки произвольной формы, со специальными ручками для захвата.
Размеры блоков
Размеры газосиликатных блоков установлены согласно, стандартам. Для строительства дома и других объектов производят изделия следующих габаритов:
- Ширина стенового камня: 200, 250, 300, 350, 375, 400, 500 миллиметров, перегородочного – 100-150 миллиметров.
- Длина – 600, 625 миллиметров.
- Высота газосиликата: 200, 250, 300 мм.
Согласно ГОСТ допускаются отклонения размеров готовых изделий. Они различаются по 1 и 2 категории. При выборе продукции стоит обращать внимание на габариты, вес и плотность. От этих показателей зависит сложность кладки, прочность и теплосохраняющие свойства. Благодаря разным размерам каждый покупатель может выбрать подходящий вариант.
Плотность
Готовые изделия различают по составу, который влияет на эксплуатационные характеристики. Плотность влияет на теплопроводность и прочность газосиликатных блоков.
Чем ниже плотность материала, тем выше морозостойкость и теплопроводность. Оптимальной показателем плотности газосиликата является 500 килограмм на кубический метр. Марка D500 хорошо подойдёт для возведения наружных и внутренних стен.
Следует учитывать: низкая плотность – низкая прочность на сжатие. В таблице приведены технические показатели в зависимости от плотности материала.
Вид газосиликатных блоков | Плотность, кг/м3 | Теплоизоляционные свойства | Применение |
Конструкционные | от 1000 до 1200 | Необходимо дополнительное утепление | Первые этажи
|
Конструкционно-теплоизоляционные | от 500 до 900 | Среднее | Широкая сфера использования |
Теплоизоляционные | от 300 до 500 | Отличное | Не выдерживает большого давления |
Вес блоков
Газосиликатные блоки размером 600х300х200 мм отличаются плотностью. Для возведения строительных объектов используют марки D500, D600, D700, а D300, D400 – для утепления. Вес газосиликатного блока 600х300х200 прямо пропорционально зависит от плотности. В таблице приведены показатели для материала маркировки D500 в зависимости от разных габаритов.
Размеры блока (длинна х толщина х высота), мм | Количество блоков на поддоне, штук | Вес 1 газосиликатного блока марки D500, кг
|
600х200х150 | 100 | 11,7 |
600х200х250 | 60 | 19,5 |
6600х200х300 | 50 | 23,4 |
600х200х400 | 30 | 31,2 |
600х250х100 | 120 | 9,8 |
600х250х150 | 80 | 14,6 |
600х250х250 | 48 | 24,4 |
600х250х300 | 40 | 29,3 |
600х250х375 | 32 | 36,5 |
600х250х400 | 24 | 39 |
600250х500 | 24 | 48,7 |
На вес газосиликата влияет влажность воздуха.
В сырую погоду удельный вес газосиликатных блоков увеличивается, один из недостатков материала – сильно впитывает влагу. Для строительства объекта расчёт веса ведётся в 1 кубическом метре.
Другие параметры
На рынке строительных материалов представлен большой выбор газосиликатных кирпичей. Популярностью пользуется продукция из ячеистого бетона «Забудова» страна производитель Республика Беларусь, «Бонолит» производитель Россия.
При выборе газосиликатного камня следует учитывать прочность. Наиболее востребован материал с показателем прочности: B 1,5, B 2,5, B 3,5. Например, для строительства несущих конструкций пяти этажного дома используются блоки В 3,5, выдерживающие нагрузку 600 килограмм на кубический метр.
Морозоустойчивость — немаловажный показатель для строительного камня. Перепады температур приводят к изнашиванию материала. Необходимо учитывать климатическую зону, в которой будет производиться строительство объекта.
youtube.com/embed/Sy2rFY6eTNU» src=»data:image/gif;base64,R0lGODlhAQABAAAAACH5BAEKAAEALAAAAAABAAEAAAICTAEAOw==»>?
В таблице приведены технические характеристики газосиликата «Забудова».
Марка газосиликатных блоков | Класс бетона по прочности на сжатие | Удельная теплоёмкость, кДж/кгоС | Марка по морозостойкости
| Коэффициент теплопроводности, Вт/моС |
D350 | B 1,0 | 0,84 | F 25 | 0,09 |
D400 | B 1,0-1,5 | 0,84 | F 25 | 0,1 |
D450 | B 1,5 | 0,84 | F 35 | 0,11 |
D500 | B 2,0-2,5 | 0,84 | F 35 | 0,12 |
D600 | B 2,5-3,5 | 0,84 | F 35 | 0,14 |
D700 | B 3,5 | 0,84 | F 50 | 0,18 |
Газосиликатные блоки являются востребованным материалом на строительных площадках. Популярность вызвана высокими эксплуатационными характеристиками.
Калькулятор расчета гасиликатных блоков для дома (стены)
Газосиликатные блоки
Калькулятор газосиликатных блоков: основы и методика расчета
Доставка газоблоков осуществляется поддонами. Чтобы рассчитать примерное количество поддонов, необходимых для заказа, воспользуйтесь калькулятором выше или позвоните по телефону. Менеджеры сделают более точный расчет для Вашего объекта.
Формулы для расчета
При проведении вычислений учитываются следующие характеристики:
- – длина, ширина и высота стен;
- – площадь оконных и дверных проемов;
- – размеры и плотность газоблоков.
Калькулятор количества газоблоков использует простые формулы вычисления объема и массы и учитывает площадь проёмов для окон и дверей.
При расчете используются следующие формулы:
- площадь стены S = P*h, где P – периметр, а h – высота стены;
- площадь оконных и дверных проемов Sпр = w1h2n1+w2h3n2, где w – ширина, h – высота, n – количество;
- действительная площадь стен Sобщ = S – Sпр.
Допуски и погрешность
Погрешность при вычислениях минимальна, так как газосиликатные блоки имеют большие размеры, а при работе опытных каменщиков толщина шва не изменяется. Величина погрешности зависит от количества обрезок, которые остаются после кладки мелких архитектурных деталей, поэтому необходимо оставлять допуски – 3-5 % на блоки и 7-10 % на раствор.
Количество и масса газоблоков в 1 м куб. и на поддоне
При размере 600 х 300 х 100 мм в 1 м куб. помещается 55 газоблоков, на поддоне – 112. Если размер газоблоков составляет 600 х 300 х 200 мм, то в 1 м куб. входит 28 штук, а на поддоне расположатся 56 блоков.
Масса одного блока D500 составляет 17-18 кг. Таким образом, масса 1 куб. м блоков – от 480 до 510 кг, а поддона – от 960 до 1020 кг.
Масса блока D600 – от 21 до 22 кг. В 1 куб. м масса блоков будет составлять от 570 до 600 кг, на поддоне – от 1150 до 1200 кг.
как рассчитать сколько весит 1 штука и 1 м3 материала
Газоблоки относят к легким каменным материалам, по сравнению с монолитным бетоном и кирпичом, при помощи которых возводят стены дома. Основные компоненты — цемент, песок и известь. Один из важных параметров такого материала – его масса. Прежде всего вес газобетонного блока нужно знать для расчета фундамента дома.
От чего зависит масса
- плотность;
- влажность.
Плотность
Значение плотности отображено на маркировке материала и указано в единицах измерения кг/м3.
Марка газобетона | Плотность (кг/м3) | Вес 1 м3 газобетона (кг) |
D300 | 300 | 300 |
D400 | 400 | 400 |
D500 | 500 | 500 |
D600 | 600 | 600 |
Из таблицы следует, что 1 куб газобетона марки D400 весит 400 кг, 1 куб марки D500 весит 500 кг.
Влажность
Что касается влажности, то этот показатель влияет на массу аналогичным образом. Чем больше процент влаги, тем большей будет масса материала.
По технологии производства автоклавные газобетоны подвергаются длительной выдержке в среде насыщенного пара под высоким давлением. Изделия, выходящие с конвейера, содержат 25-30% влаги.
Важно!
Отпускная влажность газобетона составляет 25-30%, что увеличивает вес блоков в 1,25-1,3 раза по сравнению с высохшим материалом.Однако, в течение 3-х лет, если строительство произведено с учетом требований по защите ограждающих конструкций от переувлажнения, материал высыхает и приобретает эксплуатационную равновесную влажность меньше 5%. Причем бóльшая часть влаги уходит в первый год эксплуатации.Расчет массы
Сколько весит блок
Чтобы провести расчеты, необходимо изначально знать габариты материала и плотность.
Расчеты проводят по формуле m=V*p. Обозначения следующие: m – вес блока (кг), V – объем(м3), р – плотность (кг/м3).
Справка
Для того чтобы узнать объем, нужно перемножить все значения.В качестве примера посчитаем вес газосиликатного блока 600х300х200 мм и плотностью D500.Расчет
Дано:- Размер: 200х300х600 мм
- Плотность: 500 кг/м3.
Решение:
- Зная размеры, можно высчитать объем. Для указанного изделия он будет составлять:
V = 200 мм * 300 мм * 600 мм = 36000000 мм3 = 0,036 м3 - Далее, отталкиваясь от марки, на которой указана плотность, определяется вес блока:
m = 0,036 м3 * 500 кг/м3 = 18 кг
Ответ: Вес газобетонного блока 200х300х600 без учета влажности составляет 18 кг.
Закрепим знания и произведем расчет для популярного стенового блока 250х400х600 мм и плотностью D400.
Расчет
Дано:- Размер: 250х400х600 мм
- Плотность: 400 кг/м3.
Решение:
- V = 250 мм * 400 мм * 600 мм = 60000000 мм3 = 0,06 м3
- m = 0,06 м3 * 400 кг/м3 = 24 кг
Ответ: Масса 250х400х600 без учета влажности составляет 24 кг.
Если расчет производится с целью определения нагрузки стен дома на фундамент, то влажность не играет большое значение в определении массы в данном случае. Так как параметр влажности в эксплуатируемых стенах не поднимается выше 5% при любых погодных условиях.
На начальном этапе строительства фундамент будет нагружаться стенами, нагрузка от которых больше расчетной за счет отпускной влажности. Но к моменту установки окон, возведения крыши, внутренней и внешней отделки, установки оборудования и мебели стеновой материал отдаст в окружающую среду значительную часть влаги и примет расчетную массу. Именно поэтому не стоит учитывать влажность при расчете нагрузок.
Некоторые самозастройщики возводят стены из газобетона в одиночку. И не по наслышке проверяют на себе массу блока лишь при кладке первого ряда. В этом случае им стоит понимать, что свежие заводские блоки за счет содержащейся в них влажности будут тяжелее рассчитанных выше значений примерно на 25%. Если толщина стен по проекту составляет 500 мм, то один человек будет не в состоянии поднимать такие тяжелые изделия. Ему придется либо взять помощника, либо купить более легкий материал толщиной 200 мм и 300 мм (и выложить из него двойную стену вразбежку).
Строителю на заметку
Помимо стандартных блоков с прямолинейными гранями некоторые современные заводы выпускают блоки с захватами для рук с обеих сторон.
Такой материал удобно поднимать и переносить.
При этом расход клея не увеличивается, так как по технологии монтажа пустоты заполнять не нужно.Так, в нашем первом примере свежий заводской блок, только сошедший с конвейера, будет тяжелее расчетных значений на 30%. Его вес для нашего первого примера составит:
m = 18 кг * 1,30 = 23,4 кг
Для второго примера предлагаю произвести этот несложный расчет самостоятельно и прикинуть свои возможности по подъему таких блоков на стены в одиночку.Вес поддона с блоками
Эта характеристика пригодится при планировании доставки материала на объект. У каждого грузового автомобиля есть предельные значения грузоподъёмности и объема перевозимых грузов.
Допустим, визуально вам покажется, что в грузовой автомобиль войдет 10 поддонов. Но водитель, узнав массу поддона, скажет, что сможет взять только 8 поддонов. И он будет прав, так как грузоподъемность транспортного средства не должна превышаться.
Определить массу паллеты с газобетоном просто. Зная количество единиц материала в паллете и вес одного газоблока, перемножьте эти значения.
Кстати, многие продавцы отпускают материал со склада целыми поддонами. И в прайс-листе указывают плотность и объём поддона.
Мы уже знаем, что плотность блоков соответствует массе одного кубометра. Соответственно, перемножив плотность на объём получим искомый вес паллеты.
Например, как видно из предложенного прайс-листа, объём поддона с блоками 600х200х300 мм составляет 1,8 м3. Рассчитаем массу поддона для плотности D400.
m = V*p = 1,8 м3 * 400 кг/м3 = 720 кг
Если мы везем газобетон с завода, то сделаем поправку на влажность: 720 кг * 1,25 = 900 кг.
Сколько весит куб газобетона и определение реальной плотности
В начале статьи самой первой таблице приведены эти значения без всякого расчета. Вес кубометра газосиликатного материала соответствует плотности, указанной в маркировке (D400, D500 и т.д.).
Однако, ситуации бывают разные. Возможно, вы захотите проверить соответствие заводского газосиликата заявленным характеристикам. Или вам не хватило поддона блоков, а у соседа остались излишки. При этом ваш сосед не помнит характеристики своего газобетона.
Внимание!
Узнав реальную массу мы можем посчитать реальную плотность.В этом случае нам понадобится взвесить 1 блок и произвести расчет по обратной формуле p=m/V. Где:
- m – вес (кг) — нужно найти весы и взвесить 1 блок;
- V – объем(м3) — его мы считали выше;
- р – плотность (кг/м3).
Не забывайте брать поправки на влажность.
Расчет количества материала в 1м3
Расчет проводят в два действия:
- Изначально у продавца узнают геометрические размеры конкретного стенового материала и вычисляется его объем.
- Далее нужно разделить общий объем (в нашем случае 1 м3) на объем данного блока. В итоге получается 27,778 штук.
Эту характеристику обычно указывают в прайс-листе.
В проектной документации на строительство дома в калькуляции указывается объём необходимого материала, который получают перемножением площади стен с учетом проемов под окна и двери на толщину стен.
Произведя расчет количества материала в кубическом метре, и умножив его на общий объём, мы можем узнать необходимое количество блоков для постройки нашего дома. Кстати, следует помнить при расчете, что над окнами выполняются перемычки. И эти участки в расчет не брать. Но позаботиться о выборе и покупке материала для перемычек.
Размеры и вес
Подводя итоги и учитывая зависимость массы от плотности материала, можно привести следующие параметры веса для каждой марки. Данные представлены одним из производителей.
В заключении напомню, что при выборе марки и размера, нужно учитывать длину, ширину и высоту стен, а также их функциональное назначение.
Полезное видео
Как поднять тяжелый газосиликатный блок на второй этаж, проявив смекалку.
Отличная статья 10
Вес газосиликатного блока
Газосиликатные блоки представляют собой искусственный камень, изготавливаемый из извести, цемента и песка с добавкой порошка алюминия (способствует образованию пор в рассматриваемом материале). Хорошая прочность и малый вес газосиликатных блоков делают его незаменимым материалом для быстрого возведения стен.
Плотность материала определяет его основные свойства и марку. Так марка блоков D500 и выше используется для кладки стен и перегородок, а марки ниже рассматриваемой являются теплоизоляционными материалами.
Вес газосиликатного блока будет зависеть от его номинального размера, плотности и применяемых материалов. Длина блока, зависимо от его формы (параллелепипед или параллелепипед с пазами) – 60 сантиметров или 62,5 сантиметров соответственно, высота таких блоков от 20 сантиметров до 30. Ширина газосиликатного блока зависит от толщины стены (10-20 сантиметров для перегородок и 30-40 для несущих стен). Плотность материала 350-750 килограммов на кубический метр.
Давайте рассмотрим сколько весит газосиликатный блок в зависимости от его размеров и плотности. Исходные размеры: длина – 60 сантиметров, высота – 25 сантиметров.
При ширине в 10 сантиметров и плотности 400 кг/м³ вес газосиликатного блока будет составлять 7,2 килограмма, при плотности 500 – 8,7 килограмма, при плотности 600 кг/м³ – 10,8 килограмма.
Если изменить ширину блока до 20 сантиметров, а плотность оставить той же, то при плотности 400 его вес увеличится вдвое и составит 14,4 килограмма, при плотности 500 – 17,4 килограмма, при плотности 600 – 21,6 килограмма.
Теперь рассмотрим изменение веса газосиликатного блока при его ширине 30 сантиметров. Плотность 400 кг/м³ – вес блока 21,6 килограмма; плотность 500 кг/м³ – вес блока 26,1 килограмма; плотность 600 кг/м³ – вес блока 32,4 килограмма.
Теперь рассмотрим последний вариант изменения веса блока при его ширине 40 сантиметров. Плотность 400 кг/м³ – вес блока 28,8 килограмма; плотность материала 500 кг/м³ – вес блока 34,8 килограмма; плотность 600 кг/м³ – вес блока 43,2 килограмма.
Современный силикатный блок в качестве стенового материала
Поиски надёжного и эффективного, при этом удобного в работе и не отпугивающего своей ценой материала для строительства с переменным успехом велись всегда. Результат налицо — достижения современной строительной науки вдохнули новую жизнь в давно известный материал.
Новый взгляд на силикат
Строительство дома — серьёзный этап, требующий тщательного подхода в выборе надёжного и эффективного строительного материала. Поиски удобного и при этом доступного материала велись всегда. На сегодняшний день достижения современной строительной науки вдохнули новую жизнь в давно известный материал.
Продолжительное соперничество на строительном поприще двух классических конкурентов керамики и силиката до сих пор так и не выявило явного лидера. Силикатные блоки приобрели солидное преимущество за счет более доступной цены и высокой прочности.
Необходимо заметить, что не стоит путать силикатные блоки с газосиликатными. Это два строительных материала с абсолютно несравнимыми характеристиками. Газосиликат представляет собой пористый ячеистый бетон с достаточно низкими прочностными характеристиками.
Силикатный блок — материал с высокой прочностью, в состав которого входят природные компоненты: известь, песок и вода. Силикатный блок по праву можно назвать природным камнем. Высокая марка прочности (М150-200) позволяет использовать силикатный блок для строительства высотных жилых зданий, а так же для сооружения промышленных объектов, выдерживая при этом серьезную нагрузку.
Силикатный кирпич имеет такую же долгую историю создания, как и керамический. Но гораздо более драматическую. Известно, что в поисках более дешёвого и удобного, но столь же надёжного строительного материала, как природный камень, прошли столетия. Из глины в итоге получился керамический кирпич, а из песка и извести при добавлении связующего — силикатный. Первые силикатные кирпичи, хоть и уступали в прочности керамическим, были более дешёвыми в производстве. А потому их считали перспективными, и работа над улучшением характеристик силикатных материалов продолжалась весь XX век.
В малоэтажном строительстве силикатный блок завоевал лидирующие позиции и это вполне обоснованно. При строительстве коттеджей из силикатного блока отпадает необходимость в армопоясе, колоннах и балках, а это существенно экономит средства и время. Идеальная геометрия позволяет обойтись без дополнительного оштукатуривания, а стены из силикатного блока являются несущими. Из этого следует, что рассмотрение строительного материала детально, позволит сделать правильный выбор в строительной индустрии.
Силикатный блок — мировой строительный тренд
На сегодняшний день силикатный блок является одним из самых продаваемых строительных материалов в Европе. Залог такой популярности заключается в экономических, технических и экологических преимуществах. Силикатный блок включает бесспорное преимущество в идеально ровной поверхности, высокой прочности, безусадочности а так же высокой тепло и звукоизоляции.
Обращая внимание на ценовую политику строительных материалов, силикатный блок является доступным для массового потребления. Экономический фактор отвечает новому формату силикатных изделий. Силикатный блок является среднеформатным, весом в 18 кг каждый с системой паз-гребень позволяют резко снизить количество швов, минуя «мостики холода» и серьезно упростив процесс самой кладки.
Безупречные геометрические размеры позволяют производить кладку на специальную клеевую смесь, а не на кладочный раствор. Современная торцовочная система паз-гребень обеспечивает плотное прилегание торцевых поверхностей блоков. Возможные перекосы при строительстве полностью исключаются- стена будет ровная. Без особых усилий с кладкой справится даже начинающий мастер.
Отсутствие необходимости закладки силовых поясов сокращает трудоёмкость работ и экономит время строительства, а значит вносит свою не малую лепту в снижении затрат. Идеальная геометрия как основа строительного материала обеспечивает экономию времени на дополнительное выравнивание стен и экономит затраты о общем бюджете строительства дома.
Всё вышеперечисленное не только экономит затраты на рабочие руки и вспомогательные материалы, но и за счёт размера блоков и толщины клеевого слоя доля кладочных швов в общей площади стен оказывается в пять раз ниже. Из этого следует, что теплопотери такой стены будут существенно ниже. Кладка попросту будет «теплее».
В разряд экономических достоинств необходимо добавить и то, что за счет хороших энергосберегающих характеристик, а значит, и меньшей толщины блока, площадь дома на том же фундаменте будет больше. С фундамента площадью в 100 м2 можно сэкономить порядка 6 м2, а это целая котельная или санузел. За счёт уменьшения толщины стен потребуется и существенно меньший объём блока для строительства.
С экологической стороны блоки преуспевают в своем развитии. При производстве силикатных блоков используются только природные, экологически чистые компоненты. Одна из составляющих силикатного блока — известь придаёт материалу бактерицидные свойства. Такие стены не подвержены губительному воздействию грибков и плесени.
Высокая удельная теплоемкость силикатного блока говорит о том, что стены хорошо аккумулируют тепло и компенсируют резкие перепады температур в помещениях, из-за чего в доме легче настроить оптимальный микроклимат. Иными словами в доме из силикатного блока летом прохладно, а зимой тепло.
Очень важно касательно характеристик, следует добавить, что стены из силикатного блока не дают усадки, чем не могут похвастаться другие строительные материалы. Высокая прочность на врыв анкера позволяет навешивать на стены тяжелые конструкции без всяких сомнений.
Развенчивание мифов о силикатном кирпиче
Силикатные строительные материалы в малоэтажном домостроении давно и успешно применяют во многих странах Западной Европы (Германии, Австрии, Швейцарии, Нидерландах) даже при возведении фундаментов, цоколей, подвалов и санузлов.
Ранее в ряде нормативных документов определялись ограничения на использование силикатного кирпича для кладки наружных стен подвалов или помещений с мокрым режимом эксплуатации. Данные положения отчасти были справедливы в отношении продукции 50-70 годов прошлого века. Сегодня силикатные технологии шагнули далеко вперёд. Усовершенствование технологий производства вызвало столь значительное повышение качества выпускаемых силикатных изделий, что на сегодняшний день такие кирпичи и блоки по своим эксплуатационным свойствам не уступают никакому другому строительному материалу.
Причём для снятия негативного отношения к силикатному кирпичу есть научное подтверждение. Опубликованные и находящиеся в общем доступе результаты испытаний силикатных материалов по стандартной методике исследования строительных материалов показывают, что автоклавный силикатный блок можно назвать водостойким материалом, способным длительное время сохранять при этом важнейшие качества (прочность и внешний вид).
При воздействии попеременных циклов увлажнения-высушивания (по крайней мере до 100 циклов). Из силикатного камня не только не вымывается основной связывающий компонент, гидросиликат кальция, но и происходит усиление взаимодействия песка и извести. Прочность таких блоков практически не меняется.
Проведённые исследования наглядно доказали и достаточную стойкость современных силикатных строительных материалов в горячей воде. Все без исключения испытываемые изделия после длительного (6-месячного) воздействия горячей воды по всем показателям соответствовали ГОСТ 379-2015. Таким образом, опасения по поводу воздействия горячей, ровно как и кипящей воды, абсолютно напрасны. Также подтверждены высокие результаты стойкости материалов к минерализованным грунтовым водам (в агрессивных средах солевых растворов).
Всё это обосновывает применение силикатных блоков при кладке наружных и внутренних стен подвалов, цоколей и фундаментов, в помещениях с влажным и мокрым режимом эксплуатации. Приведённые доводы показывают, что блок из силиката обрёл популярность у застройщиков вполне заслуженно. Настоящий «каменный дом» из такого строительного материала прослужит своим хозяевам многие десятки лет.
Онлайн калькулятор расчета количества строительных блоков
Информация по назначению калькулятора
Онлайн калькулятор строительных блоков предназначен для выполнения расчетов строительных материалов необходимых для постройки стен домов, гаражей, хозяйственных и других помещений. В расчетах могут быть учтены размеры фронтонов постройки, дверные и оконные проемы, а так же сопутствующие материалы, такие как строительный раствор и кладочная сетка. Будьте внимательны при заполнении данных, обращайте особое внимание на единицы измерения.
При заполнении данных, обратите внимание на дополнительную информацию со знаком Дополнительная информация
Технологии не стоят на месте и строительные в том числе. Для строительства стен на смену дереву пришел кирпич, а сегодня его место все чаще занимают строительные блоки, получаемые искусственным путем, и в зависимости от используемого сырья, могут обладать различными характеристиками.
Строительные блоки популярны при возведении малоэтажных зданий, и стен монолитно-каркасных построек. Из них можно не только возводить наружные стены, но так же использовать для внутренних перегородок и межкомнатных стен. Бетонные блоки подойдут и для изготовления сборного фундамента для легких построек.
Преимущества строительных блоков очевидны. С их помощью можно в сжатые сроки построить здание без использования специальной техники. Они обладают хорошей теплоизоляцией и необходимой прочностью. Поэтому средства, потраченные на утепление, будут существенно ниже, чем при строительстве из кирпича. А если сравнивать строительные блоки с деревянными срубами, то это не только меньше дополнительных средств и работ, но и более высокая долговечность постройки.
Блокам не нужна столь сильная пароизоляция, как например, дереву. Учитывая их габариты и легкость, даже фундамент под такой дом будет стоить значительно дешевле по сравнению с кирпичом и железобетоном. Использование специального кладочного клея увеличивает теплоизоляцию стен, и делает их более привлекательными по внешнему виду.
Строительные блоки можно разделить на два вида:
- Искусственные – их получают путем смешивания различных по составу бетонов на заводах, с использованием специальных виброформовочных станков. Получаемый материал, в зависимости от сырья, отличается необходимой прочностью, плотностью и теплоизоляционными свойствами.
- Природные – стоят сравнительно дороже, чем предлагаемые заводом.

К искусственным строительным блокам относятся: газобетонные, пенобетонные, керамзитобетонные, полистиролбетонные, опилкобетонные и многие другие. Каждый вид применяется в зависимости от необходимых качеств, и обладает как рядом преимуществ, так и рядом недостатков. У одного вида хорошие теплоизоляционные показатели, но они несколько уступают по прочности (если сравнивать, например, газобетон и керамзитобетон). В любом случае, здания, построенные с использованием строительных блоков, требуют меньше времени для возведения домов под ключ, по сравнению с теми же деревянными срубами, которым требуется много времени, чтобы окончательно просохнуть и отстояться. И только после этого можно начинать окончательную отделку помещения.
При строительстве из блоков, внутреннюю отделку помещений возможно производить сразу же после окончания строительства.
По конструктивным особенностям строительные блоки различают на:
- Конструкционные Применяются для возведения несущих стен постройки. Обладают высокой прочностью, но так же и высокой теплопроводностью и большим весом. В связи с этим, при постройке жилых помещений, необходимо обязательное дополнительное утепление.
- Конструкционно-теплоизоляционные Применяются для возведения несущих стен малоэтажных строений. Обладают средними характеристиками, как по прочности, так и по теплоизоляционным качествам. Идеально подходят для жилых помещений с сезонным проживанием.
- Теплоизоляционные Применяются для возведения только самонесущих стен, таких как внутренние перегородки и стены каркасных построек, а так же для утепления несущих стен. Обладают низкой теплопроводностью, малым весом, но так же малой прочностью.
К сожалению, на данный момент не существует идеального материала, обладающего высокими показателями сразу всех необходимых характеристик, таких как низкая теплопроводность, высокая прочность, малый вес и стоимость. И в каждом конкретном случае необходимо выбирать именно тот материал, который больше всего подходит для планируемой постройки с учетом необходимых требований.
Стоимость готовых стен приблизительно равна 1/3 стоимости всей постройки.
Далее представлен полный список выполняемых расчетов с кратким описанием каждого пункта. Если вы не нашли ответа на свой вопрос, вы можете связаться с нами по обратной связи находящейся в правом блоке.
Общие сведения по результатам расчетов
- Периметр строения — Общая длина всех стен учтенных в расчетах.
- Общая площадь кладки — Площадь внешней стороны стен. Соответствует площади необходимого утеплителя, если такой предусмотрен проектом.
- Толщина стены — Толщина готовой стены с учетом толщины растворного шва. Может незначительно отличаться от конечного результата в зависимости от вида кладки.
- Количество блоков — Общее количество блоков необходимое для постройки стен по заданным параметрам
- Общий вес блоков — Вес без учета раствора и кладочной сетки.
- Кол-во раствора на всю кладку — Объем строительного раствора, необходимый для кладки всех блоков. Объемный вес раствора может отличаться в зависимости от соотношения компонентов и введенных добавок.
- Кол-во рядов блоков с учетом швов — Зависит от высоты стен, размеров применяемого материала и толщины кладочного раствора. Без учета фронтонов.
- Кол-во кладочной сетки — Необходимое количество кладочной сетки в метрах. Применяется для армирования кладки, увеличивая монолитность и общую прочность конструкции. Обратите внимание на количество армированных рядов, по умолчанию указано армирование каждого ряда.
- Примерный вес готовых стен — Вес готовых стен с учетом всех строительных блоков, раствора и кладочной сетки, но без учета веса утеплителя и облицовки.
- Нагрузка на фундамент от стен — Нагрузка без учета веса кровли и перекрытий. Данный параметр необходим для выбора прочностных характеристик фундамента.


Что бы произвести расчет материала для перегородок, необходимо начать новый расчет и указать длину только всех перегородок, толщину стен в пол блока, а так же другие необходимые параметры.
Изоляционные материалы: блок из силиката кальция и труба
Силикат кальция используется для изоляции высокотемпературных труб и оборудования, а также для обеспечения огнестойкости. Он производится и продается в трех различных формах: предварительно отформованный блок, предварительно отформованная труба и картон. Сегодняшний силикат кальция, производимый в Северной Америке, отличается высокой прочностью на сжатие, антикоррозийными свойствами и структурной целостностью при высоких температурах. Он может выдерживать постоянные температуры до 1200 ° F (тип I для труб и блоков) или 1700 ° F (тип II, огнестойкие плиты).Структурный силикат кальция для применений, требующих более высокой термостойкости и большей прочности, в этой статье не рассматривается.
История
Силикат кальция возник примерно в 1950 году из более ранних теплоизоляционных материалов для высоких температур: 85% карбоната магния и изоляции из чистого асбеста. Сначала изоляция из силиката кальция обычно армировалась асбестовыми волокнами. К концу 1972 года большинство североамериканских производителей перешли на стекловолокно, растительные волокна, хлопковый линт или вискозу.Теперь силикат кальция, производимый в Северной Америке, не содержит асбеста.
Когда в 1970-х годах на промышленных предприятиях начались программы по снижению выбросов асбестовой изоляции, безасбестовый силикат кальция широко использовался в качестве материала для замены трубопроводов и оборудования на нефтеперерабатывающих, нефтехимических заводах, электростанциях, парораспределительных линиях и в других высокотемпературных установках. требующий использования высокопрочного изоляционного материала. Сегодня в Северной Америке существует всего два завода по производству изоляционных материалов из силиката кальция.
Как производится силикат кальция
Силикат кальция изготавливается из аморфного кремнезема, извести, армирующих волокон и других добавок, смешанных с водой в резервуаре периодического действия для образования суспензии. Этот шлам перекачивается в подогреватель, где нагревается до кипения и быстро разливается в формы. Через несколько минут материал удаляется в виде влажного и хрупкого твердого вещества. Эти сформированные детали помещаются в индуктор (своего рода пароварку под давлением) на несколько часов, где происходит химическая реакция с образованием силиката кальция.Затем кусочки помещают в сушильный шкаф. После высыхания кусочки обрезаются, разрезаются на две или более частей и упаковываются. Процесс относительно низкоэнергетический, так как максимальная достигнутая температура составляет всего около 380 ° F.
Формованный отвержденный изоляционный материал по существу представляет собой кристаллическое образование с большим воздушным пространством, чем твердое пространство (более 90 процентов воздуха). Миллионы крошечных воздушных пространств, разделенных кристаллическими стенками с низкой теплопроводностью, придают силикату кальция его изоляционные свойства.Через него может проходить очень мало инфракрасного излучения, поэтому это эффективный высокотемпературный изоляционный материал.
Характеристики продукта
Американское общество испытаний и материалов (ASTM) C533, «Стандартные технические условия на теплоизоляцию блоков из силиката кальция и труб», устанавливает минимально приемлемые стандарты для типов I и II. Тип I рассчитан на максимальную рабочую температуру 1200 ° F и максимальную плотность 15 фунтов на кубический фут (фунт / фут 3 ) или 22 фунта / фут 3 , тогда как тип II рассчитан на 1700 ° F и максимальная плотность 22 фунта / фут 3 .Предел прочности на сжатие в заводских условиях для обоих типов превышает 100 фунтов на квадратный дюйм (фунт / кв. Дюйм) при 5-процентной деформации, что является самым высоким показателем среди любых неструктурных высокотемпературных изоляционных материалов в технических условиях ASTM. Максимальная линейная усадка после воздействия максимальной рабочей температуры составляет всего 2 процента, а прочность на изгиб для обоих типов превышает 50 фунтов на квадратный дюйм. Показатели распространения пламени и образования дыма равны 0 согласно ASTM E84, так как материал не способствует горению.Максимально допустимые значения потери массы в спецификации ASTM составляют 20 процентов и 40 процентов после переворачивания в течение 10 и 20 минут соответственно, что демонстрирует его устойчивость к разрушению.
Не влияет отрицательно на теплопроводность и прочность на сжатие после испытания на максимальную рабочую температуру в соответствии с ASTM C411. Силикат кальция в Северной Америке разработан и изготовлен для предотвращения коррозии под изоляцией (CUI) как нержавеющей, так и углеродистой стали. Этот материал также классифицируется как негорючий согласно ASTM E136.
Изоляция из силиката кальция обычно покрывается защитной оболочкой: обычным алюминиевым листом, листом из нержавеющей стали, листом поливинилхлорида (ПВХ), стеклотканью с мастикой для защиты от атмосферных воздействий или многослойным ламинатом. Чтобы предотвратить проникновение воды, следует нанести валик герметика на перекрытия обшивки из листового металла.
Общие приложения
Силикат кальция обычно наносится на высокотемпературные (выше 250 ° F) трубы и оборудование на промышленных предприятиях, таких как химические заводы, нефтеперерабатывающие заводы и паровые электростанции.Поскольку это жесткий материал с относительно плоской кривой теплопроводности, чрезвычайно высокой прочностью на сжатие, высокой прочностью на изгиб, классом А для распространения пламени / образования дыма и негорючим (ASTM E136), он широко используется в высокопрочных материалах. температура, промышленные применения, подверженные физическому насилию.
Благодаря высокой прочности на сжатие (более 100 фунтов на квадратный дюйм), высокой прочности на изгиб (более 50 фунтов на квадратный дюйм) и устойчивости к повреждениям в результате опрокидывания, а также его способности сохранять эти свойства с течением времени до номинальных значений 1200 ° F, силикат кальция может выдерживать значительные физические нагрузки без потери изоляционной эффективности. Кроме того, силикат кальция может противостоять вибрации, вызванной потоком высокотемпературного пара вокруг внутренних препятствий труб, таких как внутренние детали клапана, измерительные устройства и отверстия для ограничения потока.
Сводка
Силикат кальция обеспечивает структурную целостность при высоких температурах, высокую прочность на сжатие и ингибирует коррозию. Это также может быть важным фактором сохранения. Энергия, используемая для производства линейного фута силиката кальция такого размера, составляет всего около 154 000 британских термических единиц; Соотношение затраченной энергии к прогнозируемой экономии энергии составляет 575: 1 за 1 год и 11 500: 1 за 20 лет.
Читатели, которые хотят узнать больше об изоляционных материалах, представленных здесь, должны посетить каталог продукции MTL или посетить каталог членов NIA, чтобы найти производителя.
Рисунок 1Силикат кальция устанавливается на трубу промышленного объекта.
Рисунок 2 Горизонтальные трубы с изоляцией из силиката кальция могут выдерживать небольшое пешеходное движение без серьезных повреждений.
Microsoft Word — диссертация 15 декабря 2005 г.doc
% PDF-1.5 % 1 0 obj > endobj 7 0 объект > endobj 2 0 obj > endobj 3 0 obj > ручей Acrobat Distiller 6.0 (Windows) 2006-01-20T14: 57: 02 + 01: 00PScript5.dll Версия 5.2.22009-05-29T12: 23: 27 + 02: 002009-05-29T12: 23: 27 + 02: 00uuid: 17662668-d4f8-4a2d-a1db-61d0433a647cuuid: 53828091-10b7-4348-805c-756cded377a4application / pdf
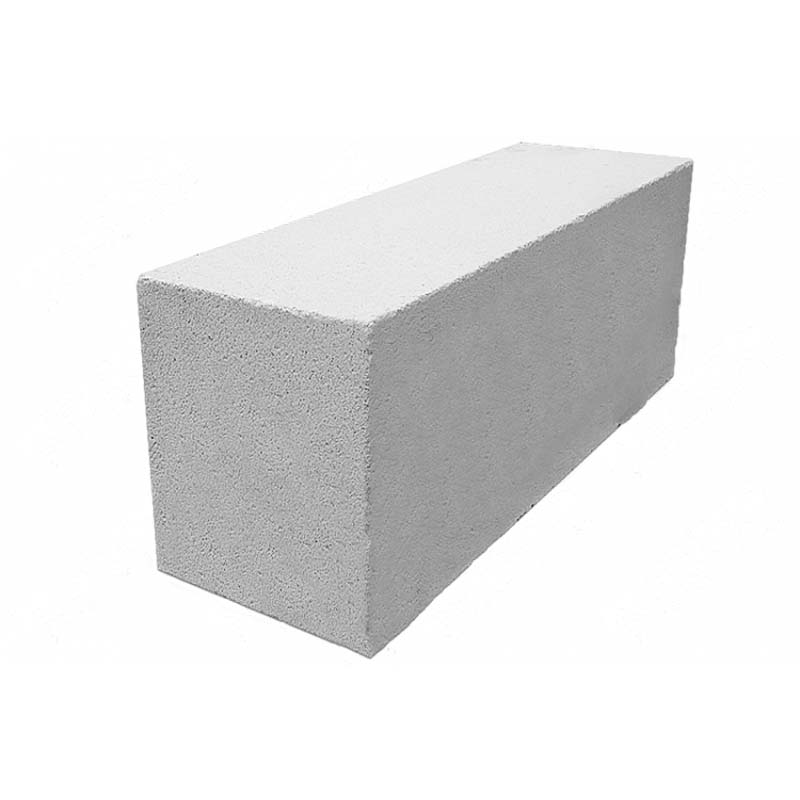
?» J8T) & aw͎Qe! + — «. ad {ȩPDjKqU1E.nwpE «) SqNǤD`p ֽ
Ѿq & i) 3 \ ZIN $ 22: JKR> sN * / H ~ IOF
Trowel Trades Supply — камень из силиката кальция
Камень из силиката кальция
Кладки из силиката кальция (искусственный песчаник) доступны в следующих типах продуктов: 1) Полнослойные блоки (блоки Renaissance Stone), которые очень похожи по внешнему виду и физическим свойствам на известняк и песчаник Индианы, размером 4x4x24, 4х8х24 и 4х12х24; 2) строительный камень («Цитадель», «Старая мельница» и «Лорье») обеспечивает отличную экономию для двух- и трехуровневых моделей тесаного камня; эти блоки строительного камня, уложенные на несущую полку, устанавливаются по цене ниже, чем цена наклеенного камня, с гарантией того, что материал никогда не упадет со здания; и 3) плитка (ArrisTile), ¾-дюймовые блоки Renaissance Stone для внутренних работ, которые можно приклеивать к любому основанию, чтобы придать вид сплошных известняковых блоков, отлично подходящих для проектов реконструкции и модернизации.
Предлагаемое использование
- Дымоходы
- Камины
- За дровяными печами
- Внешние подъезды
- Фасад дома
- Наружные стены
Кладка из газосиликатных блоков.
Как выполняется кладка стен из газосиликатных блоков? Инструкция по укладке газосиликатного блока своими руками
Газобетон — это строительный материал, созданный синтетическим путем. Это сделано в результате температурного воздействия всех составляющих компонентов. Основные преимущества этого материала — простота изготовления, небольшой вес, прочность и теплоизоляция. Однако, несмотря на все его достоинства, многие неквалифицированные рабочие не любят с ним работать. Но профессионалы с удовольствием используют газобетонные блоки.Есть некоторые особенности укладки таких блоков.
Подбор инструмента
Для того, чтобы кладка газобетона была правильной и долговечной, без использования специальных инструментов не обойтись. Для приготовления бетонного раствора вам понадобится промышленный миксер, емкость для смешивания. Для того, чтобы нанести смесь, вам потребуется — несколько мастерков разного размера. Для сборки газобетонных блоков — специальный молоток и мерный уровень. Если предусмотрена обработка газобетонного блока, то неплохо было бы запастись такими инструментами, как разметочная линейка, напильник, затирка, оборудование для формирования бороздок, насадки для дрели, дрели, щетки.
Методы кладки
Приготовление раствора для кладки.Сегодня существует два метода укладки газобетонных изделий своими руками, это укладка газобетонных блоков на цементный раствор и на клеевую смесь. Но, несмотря на выбранный способ укладки, первый ряд необходимо укладывать на цементный раствор. Дозировка компонентов должна быть такой, чтобы полученная кладочная смесь не растекалась, ведь иначе блок не зафиксируется. Если конструкция большого объема, то замешивать раствор гораздо удобнее не своими руками, а с помощью бетономешалки.
Клеевой раствор
Чтобы полученный раствор имел однородную текстуру, для перемешивания лучше использовать оборудование, работающее на малых скоростях. Для смешивания клея из пяти килограммов сухой смеси в емкость набирается литр воды. В емкость медленно наливают сухой клей и сразу взбивают. Дать настояться десять минут, а затем еще раз тщательно взбить. Раствор клея можно считать готовым, когда он станет похож по консистенции на густую сметану … Если клей высох и затвердел, запрещается разбавлять его новой смесью или водой.
Цементно-песчаная смесь
Аналогичный раствор можно использовать для блокировки. Его изготавливают путем смешивания всех ингредиентов и специального связующего. Такие составы отличаются простотой приготовления и надежностью использования.
Состав таких смесей может незначительно отличаться в зависимости от поставленной задачи. Если необходимо получить более пластичную смесь, то в состав добавляют глина.Такая смесь не крошится и не крошится при эксплуатации, что позволяет аккуратно и легко укладывать строительный материал. Использование в цементной смеси для газобетона специальных пластифицирующих компонентов позволяет качественно выполнить монтаж фасадных стен. Такая смесь очень экономична, дает хорошие изоляционные свойства, удобна в использовании и кладке. Благодаря ее достоинствам многие рабочие до сих пор работают с этой смесью чаще, чем с клеем.
Что выбрать?
Использование клея — рациональное, выгодное и правильное решение.
При выполнении строительных работ специалистов интересует не только, как класть газобетон, но и какую смесь выбрать. Ведь и у первого, и у второго варианта масса преимуществ. Следует отметить, что теплопроводность обеих смесей намного выше, чем у блоков. Из этого очевидно, что теплоизоляция всего здания зависит от ширины шва. Если вы используете цементную смесь, ширина шва будет примерно 9 миллиметров. В случае с клеем ширина швов не превышает 3 миллиметра.
Учитывая, что цена на клей выше, изначально можно предположить, что при его использовании значительно возрастут и затраты на монтажные работы. Но, с учетом его минимального расхода, на самом деле затраты растут очень незначительно, и здание выходит намного теплее. Но если использовать более дешевую цементную смесь, становится понятно, что нужно гораздо больше и стоимость монтажа неизбежно возрастет.Из этого сравнения становится понятно, что использование клея при укладке на блоки — более рациональное решение, выгодное и правильное.
Технология укладки
Перед тем, как приступить к монтажным работам своими руками, нужно распаковать блоки и разместить их рядом с кладкой ряда. При выполнении строительных работ по монтажу лучше использовать специальную клеевую смесь. В случае такого выбора вы будете защищены от образования холодных ветров на участках кладки.Не рекомендуется использовать цементную смесь, потому что, несмотря на дешевизну, расход намного выше, а швы выглядят неряшливо и слишком широкими. Также такой выбор ухудшает теплоизоляцию будущего дома.
Перед тем, как приступить к монтажу кладки блоков, стоит установить специальные маячки. Устанавливаются в зонах примыкания, по всему периметру фасада. Они нужны для выравнивания, чтобы с их помощью закрепить специальную проволоку, контролирующую ровность стен и перегородок. Закрепите проволоку оцинкованными гвоздями. Также нельзя забывать, что инструкция по укладке — важный элемент любой строительной операции.
Замешивание смеси
Для приготовления необходимо подготовить специальную емкость и промышленный миксер. Для замеса смеси используйте специальный сухой состав и теплую воду. Взбивание продолжают до тех пор, пока смесь не станет однородной по консистенции. Проработать нужно 20 минут, из-за этого смешиваются малые дозы. В процессе эксплуатации клея его нужно постоянно месить, чтобы он потерял однородность.
Если строительство ведется при низких температурах, необходимо использовать специальный вид кладочной смеси. В его состав входят специальные компоненты, предотвращающие замерзание, что дает ему возможность сохранять свои характеристики даже при низких температурах.
Наценка
Кладка стен осуществляется только после полной разметки строительных изделий. Разметка проводится по осям всех поверхностей будущего фасада. После этого материал забирается, доставляется к месту установки и распределяется по выбранным осям. При выполнении процедуры перевязки используется неполный материал, который будет располагаться по углам.
Отсюда следует, что сначала нужно разрезать продукты. Сделать это несложно, ведь распил производится пилой или ножовкой. Чтобы все конструкции были вырезаны ровно, стоит при разметке использовать специальную линейку. Необходимо заранее подготовить те материалы, которые в будущем будут армированы.
Сначала подготавливаются те блоки, которые необходимы для укладки первого ряда, после чего проделываются пазы стержней для армирования при монтаже фасада.
Укладка и армирование
Процесс установки стен и перегородок будущего здания несложный, но важно все сделать правильно. Только тогда весь процесс пройдет быстро, а конструкция будет качественной. Сначала готовится строительный материал и специальная смесь для работы.Чтобы завершить первый ряд, необходимо выполнить процедуру армирования. После этого на поверхность наносится клей и распределяется специальной гребешкой. Толщина шва не должна превышать 4 миллиметра.
Укладка кладки должна производиться с перевязкой, каждое изделие необходимо сдвинуть на расстояние, равное половине одной конструкции. Если перевязка не производится, то это негативно скажется на свойствах стен. Выступающую из толщины швов смесь нельзя тереть; удалить его можно только шпателем.Для ровности кладки используется специальный шнур. Ровность проделанной работы определяется с помощью строительного уровня и специальной линейки.
При правильном монтаже стен своими руками нельзя не учитывать вопрос гидроизоляции. Для его реализации используется специальная сетка. Обязательно закрепите гидроизоляционную сетку на стенах в зоне соприкосновения с фундаментом. После возведения перегородок их нельзя оставлять беззащитными. Стоит сразу выполнить фасадные и утеплительные работы.В случае, когда сделать это сразу невозможно, ряд стараются накрыть специальной полиэтиленовой сеткой до тех пор, пока не появится возможность все доделать. Армирование планируется еще при подготовке к строительству. Это обязательная операция, если стена слишком длинная или ящик будет находиться под повышенным давлением.
Данной процедуре подлежат все перемычки, длина которых превышает 90 сантиметров. А также все нижние швы проемов. Эта операция может быть применена по двум технологиям — с помощью металлических стержней или специальной сетки. При установке в блоках вырезаются специальные пазы, куда укладываются стержни и заливается клей. Далее следует укладка следующего ряда.
Сетка при строительстве здания требуется для повышения прочности фасада и исключения возникновения трещин в стенах. Металлическая сетка укладывается с интервалом в 3 ряда из газобетонных блоков. Чаще всего для выполнения армирования используются такие материалы: сетка оцинкованная
- ;
- сетка базальтовая;
- Сетка из стекловолокна.
Задумываясь о строительстве дома своими силами, люди стараются выбрать строительный материал, с которым легко работать. На современном строительном рынке можно увидеть большой выбор новых материалов, подходящих для строительства зданий. Газосиликатные блоки занимают одно из первых мест среди популярных у потребителей строительных материалов. Чтобы дом был крепким, надежным, нужно знать, как правильно класть газосиликатные блоки, какой раствор использовать и как рассчитать необходимое количество материала для вашего проекта.
Газосиликатная технология строительства
Построить собственный дом из газосиликатных блоков можно даже при начальных знаниях строительных технологий, но при этом есть трудолюбие и энтузиазм. Для возведения стен вам потребуются следующие инструменты и материалы:
- Для разведения клея понадобится емкость-перфоратор мутовкой.
- Наносить клей можно специальным ведром или зубчатым шпателем.
- Ножовка по металлу с большим зубом поможет разрезать блок на куски нужного размера.
- Неровности можно выровнять с помощью крупного наждака.
- Щетка для метлы.
- Квадрат металлический, уровень.
- Раствор песчано-цементный.
- Газосиликатные блоки марок Д400 или Д500.
- Пароизоляция из минеральной ваты.
- Кладочная сетка из стекловолокна или арматурные стержни.
Расчет необходимого количества блоков
Общее количество газосиликатных блоков можно посчитать, посчитав объем всех стен дома по проекту.
Более точный расчет ведется для каждой стены отдельно. Для этого нужно взять из проекта размеры стены, а габариты газосиликатного блока станут известны при его покупке. Зная ширину блока и длину стены, модно рассчитывать количество блоков в ряду кладки. Если требуется половина блока, она считается за весь блок. Количество рядов кладки рассчитывается аналогично. Количество строк умножается на полученное количество блоков в одной строке.Окончательное число — это количество блоков на стену.
Если в стене есть проемы дверей и окон, также производится приблизительный расчет. Затем, посчитав блоки для каждой стены, сложите все числа.
Кладка
Примечание! От точности и качества кладки первого ряда зависит прочность и надежность всей конструкции здания.
Готовый фундамент необходимо покрыть слоем гидроизоляции, сверху выложить кладочную сетку, а для укладки стартового ряда строительства использовать обычный раствор.Затем нужно проверить углы постройки на разницу в высоте, она должна быть не выше 30 мм. Если углы не находятся на одном уровне, укладку нужно начинать с самого высокого угла.
Первый ряд предназначен для выравнивания погрешностей при заливке фундамента, поэтому толщина раствора в разных местах может отличаться, но не должна быть меньше 20 мм. Далее устанавливаются угловые блоки и соединяются шнуром. Проверяется уровень натянутого шнура; он должен быть строго горизонтальным.Если длина стен больше 10 метров, необходимо укладывать промежуточные блоки, чтобы не допустить провисание шнура.
Используйте резиновый молоток, чтобы исправить вертикальное и горизонтальное положение блоков. Неровности кладки удаляют наждаком. Щетка для веника используется для удаления пыли и грязи. Если вам нужна часть блока, то вырежьте ее электропилой или ручной пилой.
Далее выполняется кладка блоков с помощью клеевого раствора.На строительную площадку доставляется сухая смесь мелкого песка, портландцемента и специальных добавок. Необходимо внимательно ознакомиться с инструкцией по приготовлению качественного раствора необходимой консистенции. Толщина связующего слоя должна быть не более 3 мм.
Примечание! Перед нанесением клея на блоки их необходимо тщательно очистить и смочить водой для обеспечения хорошего сцепления.
Стены кладут в теплое время года.Для строительства в холодную погоду необходимо использовать зимний клей. Клей наносится на блоки зубчатым шпателем по ширине, равной ширине поверхности газосиликатного блока. Слой должен быть однородным как с вертикальной, так и с горизонтальной сторон блока. После нанесения клеевого слоя на поверхность блока следует сделать канавку. Зазоры между карманами захвата и между гребнем и пазом заполнять раствором не нужно.
Второй ряд блоков необходимо укладывать с полусмещением, чтобы между рядами получилась перевязка.Все ряды укладываются угловым блоком. Положение каждого блока необходимо контролировать с помощью уровня и откорректировать молотком. Все стыки необходимо залить клеем во избежание усадочных трещин. Излишки клея удаляем шпателем.
Если использовать блоки паз-гребень для самостоятельного строительства, то вертикальное армирование выполнять не нужно. Для горизонтального армирования на поверхности газосиликатных блоков уложенного ряда по периметру делают продольные пазы и укладывают в них стеклопластиковые стержни или просто кладочную сетку.
Примечание! В верхней части дверных и оконных проемов сначала укладываются металлические уголки, длина которых превышает ширину проема не менее чем на 40 см, а затем продолжается укладка блоков.![]()
Устройство полов
После того, как кладка стен практически завершена и остается сделать только последний ряд, необходимо вместо блоков устраивать монолитный железобетонный пояс. Такой подход поможет равномерно распределить нагрузку от пустотных или ячеистых бетонных плит на все несущие стены.
Газосиликатная отделка стен
Для наружной отделки используйте специальные вентилируемые системы или материалы, отличающиеся высокой паропроницаемостью. Между кирпичной кладкой фасада и стеной из газосиликата оставляется зазор. Соедините две кладки гибкими стяжками. Если вы предпочитаете использовать для фасадных работ краску, шпатлевки или штукатурные смеси, нужно убедиться, что они рассчитаны на работу с газосиликатом.
В интерьере использованы воздухопроницаемые материалы.Стены из газосиликатных блоков можно оклеить обоями или покрасить краской на водной основе. Для ванной, санузла, кухни предварительно необходимо проложить пароизоляцию или пропитать стены специальным раствором. При использовании керамической плитки для отделки ванной комнаты не требуется пароизоляция.
Примечание! Внутренние стены можно шпаклевать не ранее, чем через два месяца после завершения строительства.
Работы на фасаде здания можно начинать только после завершения всех внутренних отделочных процессов.Единственное исключение — вентилируемые системы. Их можно устанавливать сразу после окончания строительства.
Видео
Более подробную информацию об установке газосиликатных блоков можно найти ниже:
Процесс изготовления газосиликатных блоков
Производственный технологический цикл изготовления этого строительного материала начинается с приготовления смеси, для которой используются четыре компонента: портландцемент, кварцевый песок, известь и вода.Эти компоненты тщательно перемешивают с помощью миксера и, доведя смесь до однородной массы, добавляют к ней алюминиевую пудру. Спустя некоторое время, необходимое для завершения процесса перемешивания, раствор переливается в специальные формы, где он должен находиться несколько часов. Это время посвящено химической реакции между элементами алюминиевой пудры и извести, которая приводит к выделению газа. В этом и заключается фокус — выделение газа способствует образованию ячеек в массе материала.
После этого изготовленные блоки нарезаются специальной ниткой до размеров, установленных стандартами, после чего помещаются в автоклав для обработки паром при температуре 190 градусов Цельсия под давлением 10-12 бар. Такой технологический процесс позволяет равномерно распределить созданные ячейки, придав материалу необходимую плотность. В этом случае в автоклаве продолжится процесс химической реакции.
Методы кладки
Газосиликатные блоки можно укладывать двумя способами — цементным и клеевым.Какому варианту лучше отдать предпочтение с точки зрения практической экономии? Прежде всего отметим, что и клей, и цементный раствор обладают высокой теплопроводностью, выше, чем у газобетона. Это говорит о том, что при уменьшении толщины шва между блоками комната способна дольше сохранять тепло в доме. Мы пришли к выводу, что цементный способ укладки газоблоков требует шва не менее 6-10 миллиметров, а толщина клеевого шва будет в пределах 1-3 миллиметров.Из этого следует, что кладка из газобетона на клей сделает дом намного теплее.
Казалось бы, все просто и понятно, а что еще нужно? Если бы не одно — стоимость клеевого раствора дороже цементного. Однако следует учитывать, что расход клеевого раствора в пять раз меньше, чем цементного. Поэтому получается, что клей для газоблоков и практичнее, и экономичнее.
Правда, кладку первого ряда (нижнего) нужно производить на цементном растворе, потому что только он способен справиться с двойной ролью как крепежной составляющей, так и выравнивающего слоя.
Технология кладки
Для монтажа газосиликатных блоков необходим фундамент. К сожалению, его поверхность обычно не неровная, вернее, всегда довольно неровная. Поэтому изначально его следует накрыть гидроизоляционным материалом, например, рубероидом или полиэтиленовой пленкой, уложенной в несколько слоев. Затем на поверхность гидроизоляции необходимо нанести цементный раствор из песка и цемента в соотношении 4: 1.
Можно приступать к укладке блока, только нижняя поверхность каждого блока, которая будет ложиться на раствор необходимо смочить водой.Это уравняет влажность блока и раствора и предотвратит попадание влаги из раствора в блок, который очень гигроскопичен, особенно если это блок ячеистого типа. Благодаря этим мерам цементный раствор не потеряет присущих ему адгезионных качеств.
Начало кладки следует вести от угла фундамента, имеющего наибольшую высоту, которую можно определить с помощью уровня или строительного уровня. Блоки первого ряда следует укладывать в строго горизонтальной плоскости (желательно в вертикальной), добиваясь максимальной ровности общей поверхности.Поэтому за процессом укладки блоков нужно постоянно следить по уровню. Как видите, требование к кладке первого ряда под цементный раствор оправдано, так как им несложно отрегулировать совмещение смонтированных блоков в нужной плоскости.
Равномерно разложив нижний ряд блока, можно проводить дальнейшую укладку с помощью клея.
Вполне возможно, что последний блок в ряду может выступать за фундамент. В этом случае его легко можно будет разрезать, например, ножовкой по металлу.И вообще, этот материал для кладки стен легко обрабатывать различными методами — точить, просверливать, отрезать, обламывать и так далее.
Второй, верхний ряд следует монтировать, начиная с укладки на разрезанный блок, что даст возможность сделать хорошую стяжку между элементами блока, то есть повторить все приемы стандартной кирпичной кладки со смещением.
После укладки четырех рядов газоблоков необходимо выполнить армирование, то есть на поверхности четвертого ряда необходимо сделать пазы, в которые уложить металлическую арматуру диаметром около восьми миллиметров, которую дополнительно засыпают. на цементном растворе.
Строб должен быть сделан достаточно глубоким, чтобы якорь полностью погрузился в него.
Оштукатуривание стен из газоблоков
Если перегородки в квартире выполнены из газосиликатных блоков, то их можно оштукатурить для последующей отделки. Этому процессу присущи свои нюансы, которые отличаются от оштукатуривания других поверхностей, например, из бетонных блоков или кирпича. И самое главное отличие — это сама штукатурная смесь.
По мнению специалистов, не рекомендуется оштукатуривать газосиликатные блоки штукатуркой на цементной основе. Поэтому возникает вполне закономерный вопрос: как правильно оштукатурить поверхность стены из газосиликатных блоков? Все просто, штукатурную смесь готовить совсем не обязательно. Достаточно зайти на строительный рынок или аналогичный магазин и приобрести готовый штукатурный раствор, разработанный специально для оштукатуривания газосиликатных блоков. Их основа — гипс, который имеет столь необходимый нашему варианту высокий уровень паропроницаемости.
Современная гипсовая штукатурка продается в сухом виде. Довести сухую смесь до готового к употреблению гипсового раствора несложно, достаточно следовать инструкции на упаковке продукта. Сразу учтите, что при приготовлении раствора следует неукоснительно соблюдать главное требование — сначала высыпать сухой раствор в емкость, а уже потом вливать в него воду, а не наоборот!
Для приготовления стандартного раствора обычно соблюдается соотношение двести граммов воды на килограмм сухого вещества. Будьте осторожны, так как слишком много воды ухудшится качество штукатурки.
Покрытие стен штукатуркой
На первом этапе оштукатуривания поверхность стен из газосиликатных блоков должна быть тщательно очищена от пятен, подтеков, мусора и пыли.
Второй этап — грунтование поверхности стены. Для этого желательно использовать грунтовку глубокого проникновения.
Третий этап — это установка на поверхность стены армирующей сетки из стекловолокна, которая должна иметь строго определенные свойства: изделие должно иметь высокую степень сопротивления разрыву и растяжению, а также иметь высокую плотность.
Четвертый этап — это сам процесс штукатурки. Оштукатуривание стен, облицованных газоблоками, необходимо производить по специальным направляющим маякам. В качестве маяков можно использовать направляющие планки, которые следует установить вертикально на стене по уровню или отвесу, закрепить, например, тем же раствором, а затем заполнить пространство между маяками штукатурным раствором. В зависимости от необходимости в общем слое штукатурка выполняется единовременно или в несколько приемов. Толщина одного слоя не должна превышать 15 миллиметров, это в том случае, если вы полностью выполняете штукатурку этим слоем.А если раствор нужно наносить в несколько слоев, то толщина каждого последующего слоя не должна превышать восьми-девяти миллиметров.
Установленные планки служат ориентиром для выравнивания штукатурки, а сам процесс выравнивания осуществляется по особому правилу, по которому нанесенный раствор можно перераспределить на недостаточно заполненные места на поверхности или даже удалить их излишки. Дождавшись высыхания штукатурки, ее затирают шпателем.
Каждый слой штукатурки можно наносить только после полного высыхания предыдущего слоя.Оштукатуривание рекомендуется проводить при положительной температуре воздуха в помещении — в пределах 5-30 градусов тепла.
Отделочные работы по стенам из газоблоков
По эксплуатационным характеристикам стены из газосиликатных блоков не хуже аналогов, из которых возводятся поверхности стен. Также они в полной мере характеризуются высокой прочностью, надежностью, а также показателями тепло- и звукоизоляции. Однако, как мы уже отмечали выше, у материала повышенный коэффициент гигроскопичности, что делает нежелательным его использование при необходимости перепланировки туалета или ванной комнаты.Но, повторяем, «нежелательно», потому что сегодня производители отделочных материалов наладили производство отделочных покрытий, способных успешно защитить даже такие гигроскопичные изделия, как газосиликатные блоки, от проявлений повышенной влажности. Например, специальные виды штукатурки.
А во всем остальном посмотрите на строительство из газоблоков как на обычную стену. Поэтому для отделки его поверхности можно в полной мере использовать все известные отделочные материалы, а также применить все способы их укладки на стену.При этом требования к подготовке стены под покраску и оклейку обоями остаются неизменными — поверхность необходимо довести до максимально возможной гладкости и ровности, что можно сделать известными штукатурными или шпатлевочными растворами.
В случае, когда перегородка из газосиликатных блоков предназначена только для разделения помещения на две части, достаточно лишь шпаклевки для ее выравнивания. А если вы решили отдать предпочтение пластиковым или декоративным панелям, то никаких дополнительных работ на стене делать не придется.Просто соорудите на его поверхности деревянный каркас, на который можно легко смонтировать указанные отделочные материалы. Сегодня этот способ отделки считается самым простым и наименее затратным.
В полной мере это касается вагонки, зеркал, деревянных панелей. Керамическую плитку можно укладывать и на газосиликатные блоки, но в этом случае для ее основания придется оштукатурить поверхность. На самом деле, при отделке можно дать волю своей фантазии или следовать рекомендациям опытных дизайнеров, обоснованно полагающих, что отделать поверхность из газосиликатных блоков можно практически любыми отделочными материалами, например фактурной штукатуркой, жидкими обоями, настенный линолеум.Или можно полностью отказаться от отделки, предпочтя украшать стену разнообразными мелочами. Кстати, этот стиль сегодня становится все более популярным и известен под категорией городского индустриального варианта.
Из этого видно, что методов отделки стеновых поверхностей из газосиликатных блоков действительно огромное количество.
Итог
Подходит ли вам материал стен из газосиликатных блоков для перепланировки квартиры, решать только вам.Со своей стороны считаем необходимым отметить, что этот строительный материал имеет ряд положительных преимуществ перед аналогами и с самого начала использования в строительстве зарекомендовал себя только положительно.
Конечно, в случае использования на кухне, туалете, ванной, для отделки стен этим материалом придется потратить определенные силы, деньги и время на защиту газосиликатных блоков от влаги. Но в итоге затраты с лихвой окупятся, ведь изделия из газобетона дешевле такого же кирпича и их намного проще монтировать даже по сравнению с гипсокартоном.
Во время строительных работ рекомендуется снимать с поддонов столько блоков, сколько предполагается уложить в один день. В остальное время соблюдайте правила хранения блоков и размещайте их на ровной площадке, недоступной для влаги.
Различаются технологии кладки первого и последующих рядов стен. Давайте посмотрим на обе технологии по отдельности.
Укладка первого ряда блоков
После установки фундамента здания укладка первого ряда — самый ответственный момент.От первого ряда зависит точность всех последующих рядов стены и устойчивость всей постройки. Поэтому к этому этапу строительных работ нужно подойти особенно ответственно.
Перед кладкой первого ряда производится гидроизоляция по верхнему уровню фундамента, которая защитит между фундаментом и кладкой. Под блоки заливается выравнивающий слой из цементно-песчаного раствора. Сами блоки устанавливаются с помощью полимерных растворов на основе сухих смесей, иногда для монтажа также используются битумные рулонные материалы.
Для того, чтобы выровнять все ряды здания по углам, по высоте каждого ряда кладки кладут рейки с рисками. Через них протягивают причальный шнур, чтобы контролировать ровность кладки каждого последующего ряда.
С помощью уровня необходимо измерить уровень самого высокого угла здания, с которого начинается строительство здания. При этом перепад высоты между углами домика не должен быть более 3 см.
|
Блоки лучше всего класть на клеевую смесь. Для его приготовления требуется вода, ведро для смешивания и строительный миксер. В ведро наливают необходимое количество воды и при постоянном помешивании постепенно добавляют миксером рассчитанное количество сухой смеси. Во время монтажных работ клей необходимо время от времени перемешивать. Это делается для того, чтобы он не затвердел, чтобы постоянно сохранялась его однородность.
В процессе строительства часть газосиликатных блоков необходимо разрезать. Эти материалы режутся просто с помощью обычной ручной пилы. Квадрат используется для точности резки и измерения прямого угла при резке. Такие обрезанные блоки называют дополнительными блоками. Перед установкой следующего дополнительного блока обязательно промажьте вертикальные швы клеевой смесью.
Укладка последующих рядов стены
Укладка следующих рядов также имеет свои особенности.Каждый последующий ряд укладывается только после того, как предыдущий будет полностью схвачен. По времени это примерно 1-2 часа после завершения укладки.
Необходимо четко контролировать кладку каждого блока стены. Ровность рядов проверяют по уровню и швартовному тросу. Финишное выравнивание кладки производится с помощью уровня и резинового молотка.
Смесь наносится на блоки следующим образом. В зависимости от толщины блоков для нанесения смеси подбирается зубчатая каретка или шпатель.Равномерно, без зазоров, клей наносится на поверхность 2-3 блоков. Каретка помогает лучше распределить смесь, не капая по бокам блоков.
Следующие ряды, как и первый, располагаются от угла здания. В этом случае на торцы блоков клеевую смесь не наносят. Материалы укладываются и разравниваются сразу на место, а блоки перевязываются.
В некоторых случаях газосиликатные блоки нуждаются в армировании.
Правильное усиление кладки
Каждый первый и четвертый ряды кладки армированы. Для армирования в середине блоков прорезают пазы ручным или электрическим резцом. Если вы работаете с блоками толщиной 400 мм и более, лучше всего уложить два параллельных ряда арматуры. Попавшая внутрь строительная пыль удаляется веником или феном.
Перед заполнением пазов клеевой смесью и укладкой арматуры рекомендуется их смочить водой.Это делается для улучшения строительных качеств конструкции. Каждая канавка заполняется скрепляющим раствором на половину ее глубины, после чего в нее вставляется стальная арматура.
|
Стальные стержни диаметром 8 мм используются для усиления блоков. При армировании блоков на углах здания пазы просверливаются со скруглением, а стержни загибаются в расчетном месте.Для гибки используется специальное оборудование или ручной инструмент. После этого стержни устанавливаются каждый в свой стробоскоп.
Каждый элемент арматуры погружается в клеевой раствор, затем раствор заливается стробоскоп. Таким образом предотвращается коррозия. После завершения работ остатки смеси удаляют шпателем.
После устройства стен из газосиликатных и газобетонных блоков требуется их облицовка.
Есть несколько основных вариантов облицовки.
Облицовка кирпичом.
Облицовка реле.
Штукатурка отделочная.
- Выбирая этот вид облицовки, важно помнить, что штукатурка не должна быть цементно-песчаной. В зонах повышенных нагрузок, таких как углы зданий, оконные проемы, изломы фасадного профиля, рекомендуется армировать штукатурный слой специальными сетками.
- Во время штукатурных работ необходимо не допускать промерзания, пересыхания штукатурки, а также соблюдать температурный режим.
Выбирайте газоблоки для своего строительства!
Газосиликатные блоки, благодаря своей универсальности, оптимальны для возведения малоэтажных домов в частном строительстве. Основное преимущество этого строительного материала — небольшой вес газоблоков при больших габаритах, что позволяет увеличить скорость возведения стен и укладки легкого фундамента. Большие габариты изделий также означают минимальное количество «мостиков холода» в стенах. Самостоятельная кладка стен из газоблоков не требует профессиональных навыков и опыта — достаточно уметь владеть простейшими строительными инструментами.
Пористая структура газосиликатных изделий обуславливает необходимость учета ее свойств при работе с газобетонными блоками с целью предотвращения отклонений от технологии строительства и обеспечения проектной прочности и надежности конструкции. Наличие воздушных пор обеспечивает несложную доставку изделий на строительную площадку и непосредственно к месту кладки, а также быстрое увеличение высоты стен за счет больших размеров изделий и «шпунт-паз» система, которая автоматически выравнивает строки относительно друг друга.
Но из-за небольшого веса пористого блока он мало давит на раствор, создавая некачественное сцепление между смесью и кирпичом. Поэтому рекомендуется максимально ограничить использование цементно-песчаного раствора и работать со специальным строительным клеем, толщина шва которого минимальна при высокой адгезии к любой поверхности.
В индивидуальном строительстве в первую очередь ценятся такие характеристики газобетона, как размер изделий и плотность строительного материала.Использование клеевого состава в сочетании с большими размерами изделий и небольшим количеством клеевых швов не допускает образования «мостиков холода», которые неизбежно появятся при работе с цементом.
Теплоизоляционные свойства — еще одно несомненное преимущество газосиликатного кирпича. Воздух в порах блоков плохо пропускает через себя тепло, и остается внутри помещения, а холодный воздух извне в дом не проникает. Поэтому никаких дополнительных утеплителей для здания не требуется, за исключением утепления фундамента и крыши.
Гидроизоляционные характеристики газобетона недостаточно высоки, чтобы обойтись без слоев гидроизоляции, поэтому защита от влаги необходима не только для фундамента и кровли, но и для стен как внутри, так и снаружи. Обычно это слой штукатурки с предварительной пропиткой битумом, грунтовкой и другими влагозащитными средствами. В этом случае толщина стены значения не имеет, так как влага будет проникать на всю ширину блоков.
Самостоятельная кладка стен из газосиликатных блоков будет стоить намного дешевле, чем строительные работы с традиционными материалами — кирпичом, бетоном или деревом.Цена определяется дешевизной природных компонентов для производства газосиликата, дешевыми технологиями производства и дешевизной перевозки больших объемов стройматериалов с малым весом. Использование обычных инструментов без привлечения автоматики и специального оборудования, а также высокая скорость укладки делают работы недорогими.
Применение газоблоков — кладка из газосиликатных блоков не только в частном секторе, но и в промышленных масштабах, ограниченная только этажностью построек.Оптимально подобранные размеры блоков, кратные стандартным размерам кирпича, позволяют в короткие сроки выполнить ремонтно-строительные работы любого объема. Кроме того, вы можете заказать у производителя блоки нестандартных размеров, что ускорит укладку или обеспечит быстрое строительство геометрически сложных архитектурных объектов.
Поверхность стен из газосиликата получается практически идеально ровной, поэтому экономия от минимизации отделочных работ очевидна.
Подготовка фундамента перед кладкой стен
Перед тем, как начать кладку газосиликатного блока, необходимо с помощью уровня воды проконтролировать горизонтальность поверхности фундамента — от этого зависит ровность укладки первого и последующих рядов газосиликатного кирпича.Если перепад по краям стены составляет 10-20 мм, фундамент следует выровнять слоем цементно-песчаного раствора. Дальнейшая укладка блоков по системе «паз-гребень» будет намного проще, если первый ряд уложен идеально ровно по горизонтали. Также нужно проверить углы периметра — они должны быть 90 0. Контроль осуществляется измерением диагоналей периметра дома.
Чтобы дождевая или снеговая вода не просочилась под фундамент, необходимо выложить газоблокирующую стену так, чтобы она выступала на 1-2 см по краям фундаментной плиты.Так влага сразу стечет на отмостку и попадет в дренаж. Именно поэтому между стеной и основанием дома необходимо оборудовать два-три слоя гидроизоляции из рубероида, чтобы стены не промокли и не заплесневели. При принятии решения и устройстве гидроизоляции толщина стен из газосиликатных блоков не имеет значения — стены любой толщины необходимо защищать от влаги.
Варианты кладки стен
Стены из газосиликатных блоков возводятся на цементно-песчаном растворе, а также на специальном строительном клее, который готовится из сухой смеси с добавлением обычной воды.Исследования показали, что в толстом слое раствора «мостики холода» возникают гораздо чаще, поэтому склейку и укладку газосиликатного блока следует производить как можно более тонким слоем связующего. Это возможно только при использовании клея. Раствор на цементе дает слой со средней толщиной 9-12 мм, а слой строительного клея — 3-5 мм, поэтому цементный раствор используют только для укладки первого ряда газоблоков, чтобы связать стену и фундамент. . Дальнейшую кладку рекомендуется проводить на клей, а если используются пазогребневые блоки, то использовать цементный раствор просто невозможно из-за точного прилегания элементов — паза и гребня друг к другу — в пространство между ними не поместится раствор.
Стены из газосиликата возводятся с одновременным формированием максимально тонкого слоя вяжущего раствора. И цементно-песчаный, и клеевой раствор можно приготовить самостоятельно.
- Раствор песчано-цементный готовится традиционно, в пропорции 1: 3 (цемент — песок). При строительстве дома зимой нельзя использовать обычный раствор, так как при низких температурах прочность состава нарушается образованием льда.
- Клей изготовлен на основе портландцемента, в который добавлены минеральные добавки и полимеры.Благодаря мелкодисперсному составу клея слой раствора очень тонкий, и в нем не появляются «мостики холода». Но первый ряд блоков нужно только уложить на цементный раствор, а зимой используют несколько методов обогрева участка кладки, в том числе тепловые пушки, палатки и локальное отопление.
А вот стандартный клеевой состав в чистом виде зимой использовать нельзя. Для отрицательных температур выпускаются специальные антифризы, с которыми клей успешно застывает на морозе быстрее.
Инструмент и оборудование для строительства дома из газосиликатных блоков
Правильная и точная геометрия блоков, малый вес газосиликата, упрощенная укладка за счет пазогребневой системы позволяют обойтись без специального оборудования и большой бригады строителей. Для самостоятельного строительства вам понадобится такой инструмент:
- Дрель, шлифовальная машина или лобзик — корректировка размеров блоков для геометрически сложных архитектурных конструкций;
- Уровень, кельмы разной формы и кельмы разной ширины, в том числе зубчатые;
- Молоток резиновый или деревянный;
- Емкость для перемешивания раствора;
- Рубероид, битум, мембранные материалы, арматурная сетка.
Способ укладки газосиликатных блоков
- Первым делом проводится гидроизоляция фундамента и пористых газоблоков. Рубероид необходимо разрезать по ширине фундамента и уложить в два-три слоя в два слоя на чистую и ровную поверхность основания;
- Далее выкладываются углы будущих стен.
Газоблок устанавливается вертикально на фундамент, положение контролируется по уровню и корректируется киянкой;
- Между образованными уголками нужно натянуть шнур, по которому будут выравниваться оставшиеся блоки и ряды;
- Для укладки первого ряда использовать цементно-песчаный раствор минимально возможной толщины.Раствор наносится на нижнюю и боковые стороны блока и фундамента зубчатым шпателем подходящей ширины. Основная задача цементного раствора — выравнивание первого ряда, поэтому допускается увеличение толщины слоя до 20-25 мм;
- После схватывания раствора под первым рядом (1-2 часа) можно приступать к укладке второго и последующих рядов. Последний газоблок подгоняют по размеру с помощью болгарки, ножовки по дереву или лобзика. Межрядную связку осуществляют смещением блоков влево-вправо на 10-12 см.Следующий ряд укладывается после снятия угловых кирпичей и выравнивания поверхности предыдущего ряда путем его шлифовки.
- Клей на следующие ряды наносится сплошным слоем с помощью подходящего шпателя на поверхность нижнего ряда и по бокам блоков; клей следует разровнять зубчатым шпателем до получения толщины 1–5 мм.
Выдавленный клей необходимо удалить после того, как он полностью высохнет на стене;
- При формировании перемычек для окон и дверей используются бетонные или металлические плиты, профили или швеллеры;
- Каждый третий-четвертый ряды необходимо армировать прутьями Ø 10-14 мм или армирующей сеткой из стекловолокна, чтобы не увеличивать толщину шва.При армировании стержнями в блоках закладывают пазы, а в них укладывают стержни на расстоянии не менее 5 см от краев стены;
Особенности зимнего строительства
При строительстве малоэтажного частного дома из газосиликатных блоков температура на улице особо не имеет значения — важен клей и цементный раствор. При отрицательных температурах адгезия растворов ухудшается, и прочность стен заметно теряет качество.Если строительство планируется сплошным, то для зимней кладки газоблоков практикуются следующие проверенные и эффективные приемы:
- Синтетические добавки, обеспечивающие стопроцентную адгезию и твердение клея при температуре окружающей среды до -35 0 С;
- Обогрев кладки — тепловая пушка, электрические обогреватели, обогрев электродами или кабелями, электрические маты или местное палатное оборудование и т.
Д. Важно, чтобы место кладки с клеевым раствором было теплым или имело температуру не ниже 0 0 С.Чаще всего эти методы сочетают или используют кратковременное локальное обогревание места укладки блока.
Газосиликатные блоки — строительный материал, идеально сочетающий в себе высокие технические и эксплуатационные характеристики и доступную цену. Действующие ГОСТ и СНиП позволяют строить дома из газосиликатных блоков высотой до 5-7 этажей. Небольшой вес изделий и несложный монтаж позволяет построить дом своими руками и без использования специальной техники, что существенно сэкономит семейный бюджет.Строителю остается только соблюдать технологию строительства, и в результате он получит теплый, надежный и качественный дом.
Кладка газосиликатных блоков обновлена: 17.01.2017 автор: Артём
Кирпич силикатный
Размер и вес любого строительного материала является исходной величиной для определения набора вспомогательных факторов. Такой же силикатный кирпич необходимо купить, правильно рассчитать, нанять перевозчика с грузчиками и доставить материал на строительную площадку. Все это требует вознаграждения, которое напрямую зависит от веса, размера и количества материала.
Основная учетная работа каменщика состоит из расчета количества штук уложенного материала, реже — в кубометрах кладки. Силикатный кирпич по сравнению с керамическим блоком очень тяжелый, выше физическая нагрузка и затраты на его кладку. Цены могут колебаться и варьироваться в зависимости от марки, средней плотности класса, размера и качества кладки.
Никто не хочет подсчитывать, сколько силикатного кирпича уложено в стену после завершения работ, какой реально использованный материал и сколько бракованного.Так что перед работой следует уточнять размер, марку и вес. Это можно сделать тремя способами:
- Tangenziale путем измерения линейных размеров высоты, ширины и длины строительного материала;
- Доверять информации о силикатных блоках на этикетке или этикетке производителя;
- Взвесьте стандартные кирпичи из силиката кальция на поддон, вычтите вес поддона и рассчитайте вес одного поддона, разделенный на количество штук, указанное в счете или на этикетке.
Таким образом, в современной маркировке строительного материала обязательно указываются его название, марка, марка, средней плотности, морозостойкости, увеличенного размера или единичного размера, информация о наличии специальных пустот, фотографии. Информация о размерах или весе стандартной единичной единицы в маркировке есть, но она может присутствовать как дополнительная информация от производителя вместе с общим весом всего содержимого.
Кроме того, текущие условия предпродажной подготовки товаров требуют упаковки поддона с материалом в толстую прозрачную пластиковую пленку, которую сложно вытянуть пару единиц для измерения или осмотра.
По ГОСТ №379-2015 выделяют две основные размерные группы силикатного кирпича одинарный и крупный, ранее одинарный. Размер как в длину -250 мм, в ширину — 120, в высоту варьируется — увеличенный конструкционный материал -88 мм, одинарный — 65 мм.
Эти размеры имеют все виды лицевых и сырьевых материалов, вне зависимости от наличия пустот или декоративных элементов на лицевой поверхности.
Важно! Не следует путать силикатный кирпич с другими материалами из силикатной массы.Так, если увеличить высоту до 138 мм, то материал 250х120х138 правильнее назвать камнем, а при ширине склеиваемой грани более 130 мм силикатный блок.
Выбор однотонного или увеличенного материала часто делается для обеспечения привлекательного внешнего вида кладки. Единый блок проще, а сцепление часто выглядит эффектно, в то время как одинарный силикатный материал позволяет увеличить скорость возведения стен почти вдвое при небольшом количестве раствора на швах.
Самым сложным и плохо контролируемым параметром силикатного материала является его вес.Известно, что средний вес единичного экземпляра обычного кирпича может варьироваться от 3,2 до 3,7 кг. Среднее тяговое усилие одного экземпляра 4,3–4,8 кг, в зависимости от конструктивных факторов.
Зависит от веса ↑
Если вы запрашиваете и проверяете вес силикатного кирпича, а также вес силикатного кирпича, который не соответствует описанию, вы должны учитывать следующие факторы:
- Стандарт выделяет семь основных классов средней плотности материала, которые могут быть выбраны производителем в зависимости от используемого сырья от 1000 до 2200 кг / м Три ; №
- В пределах одного класса силикатного кирпича плотность может варьироваться на 50 кг на куб материала;
- Разные условия хранения материалы из силиката имеют разную влажность материала и разный вес.
Важно! В ГОСТе не указан вес пустотелого варианта, размеры пустот и их форма определяется производителем, если только толщина наружных стен была не менее 10 мм, а прочность блока силиката соответствовала его. бренд.
Самыми популярными среди вариантов силикатных материалов для частного строительства являются:
- Увеличенный или матовый материал с 20% объема пустот в виде мелких ячеек с классом средней плотности 1.6. Этот прочный, легкий материал с относительно хорошими теплоизоляционными характеристиками. Возведение капитальных стен двухэтажных домов;
- Облицовка класса single option, средней плотности 2,0 с гипсовым компаундом и гидрофобной пропиткой.
Выбор силикатного кирпича по весу ↑
Вес экземпляра материала из силиката и его прочность — вещи абсолютно взаимосвязанные. Прочность во многом определяется степенью помола исходных компонентов и сырья.Чем мельче фракция песка и извести, чем глубже и тщательнее перемешивание, тем плотнее получается силикатная масса кирпича и выше ее вес.
Производство такого материала затруднено, процесс автоклавной обработки требует повышенных затрат для обеспечения необходимой прочности камня, производство занимает больше времени. Но в теле кирпича намного меньше воздушных пор, губительно влияющих на срок службы силикатного материала.
Это связано, в первую очередь, с глубоко влажным материалом.Чем больше пор и полостей в теле силикатного материала, тем больше влаги он может впитать. Необязательно оставлять кирпичи под дождем или погружать в воду. Очень хорошо, почти как губка, материал силикатной массы может впитывать влагу из тумана, конденсата и сырости, особенно из влажной почвы.
Чем больше площадь контакта, тем быстрее происходит намокание. И полиэтиленовые пакеты на поддоне не могут остановить этот процесс. Скорее, он защищает от сильного дождя и сохраняет внешний вид кирпича от загрязнения.Поэтому купленный материал из силиката следует хранить в сухом, проветриваемом месте.
Очень хорошо подходит для гидрофобной пропитки, но держится максимум от трех до четырех лет, чем жарче климат, тем быстрее исчезает репеллентный эффект.
Важно! Благодаря высокой степени уплотнения силикатный кирпич с высокими показателями класса средней плотности намного лучше противостоит намоканию.
Стандарт определяет минимальное поглощение для силикатного кирпича 6%.На практике максимальное водопоглощение составляет 8 — для тяжелого и плотного кирпича до 14% для легкого и пустотелого. Это означает, что половина образца весом 4,3 кг сможет набрать дополнительно 0,5 кг или литр воды. Теоретически, находясь под дождем длительное время, связку нового материала можно выложить не менее 10%.
Соответственно вы увеличиваете транспортные расходы, но, что самое неприятное, вместо толстого тяжелого варианта вы можете купить мокрый легкий силикатный кирпич и даже не догадываться об этом.
Чаще всего вес блока или камня рассчитывается как среднее значение, полученное при взвешивании небольшой партии из десяти штук.
Помимо плотности и водопоглощения, на вес силикатного кирпича влияет количество циклов замораживания и оттаивания «опытного» материала. С каждым новым циклом внешняя лицевая поверхность подвергается отслаиванию и осыпанию. Стандарт требует, чтобы при заданном показателе морозостойкости, например, самом маленьком из имеющихся — F25, за двадцать пять циклов потеря веса материала не превышала 5%.
Вес и размеры силикатного кирпича требуют индивидуального контроля, как минимум, в пределах одной упаковки.Это позволит избежать потерь, связанных с недобросовестными производителями материалов из силикатных масс и тем, что большинство импортирует некачественные или контрафактные товары.
Связанные с контентом
Рынок активного силиката кальциявырастет более чем на 8% к 2024 году: Global Market Insights, Inc.
Селбивилль, Делавэр, 18 сентября 2019 г. (GLOBE NEWSWIRE) —
Активный спрос на рынке силиката кальция в Бразилии на керамическую плитку к 2024 году потребление должно превысить 90 тонн.Повышение осведомленности потребителей о замене обычных полов и стен на эстетичный внешний вид должно стимулировать региональный спрос.
По прогнозам, потребление активного рынка силиката кальция в Китае к 2024 году превысит 15 кг. Сильные индикаторы роста расходов на инфраструктуру аэропортов, автомагистралей, торговых комплексов и эстакад должны стимулировать региональную промышленность. Кроме того, наличие крупных производств, которые включают производство резины, пластмасс, красок и покрытий, должно стимулировать спрос на продукцию для высокотемпературной изоляции.
Рыночная стоимость активного силиката кальция в Германии к 2024 году должна превысить 17 миллионов долларов США. Внедрение правил и положений в отношении стандартов и качества продукции должно стимулировать региональный рост. Растущий спрос на огнезащитную облицовку для предотвращения дыма, пламени и распространения огня должен стимулировать спрос на продукцию.
Запрос на образец этого исследовательского отчета @ https://www.gminsights.com/request-sample/detail/1108
Объем рынка активного силиката кальция от приложений противопожарной защиты должен принести более 135 миллионов долларов США в продажи до 2024 г. Он используется в доменных печах, стенах зданий, нефтеперерабатывающих заводах и в электродуговых печах в виде блоков и плит. Расширение области применения высокотемпературной изоляции в сталелитейной, стекольной и нефтехимической промышленности должно повысить спрос на продукцию.
Сырая нефть сначала нагревается в печи во время процесса экстракции, чтобы поддерживать высокую температуру, возникающую во время процесса. Доменные печи используются в сталелитейной промышленности для преобразования сырой железной руды в сталь путем плавления, а внутренние стенки состоят из кирпичей из активного силиката кальция и штук.
Строгое соблюдение нормативных требований в отношении расходов на инфраструктуру должно стимулировать рост спроса на рынке керамической плитки. Сегмент керамической плитки может принести бизнесу более 150 миллиардов долларов к 2024 году, ожидается прирост в 9%. Они используются в строительстве для полов благодаря высокой прочности и термостойкости. Кроме того, высокоэффективная керамика имеет преимущества в сложных и агрессивных средах благодаря таким характеристикам, как легкий вес, высокая твердость, коррозионная стойкость и высокая температура плавления, что должно стимулировать рост рынка активного силиката кальция.
Сделайте запрос о покупке этого отчета @ https://www.gminsights.com/inquiry-before-buying/1108
Керамические изделия могут стать свидетелями роста более 3,5%, с плиткой, подвесными потолками, штукатуркой Парижа, а также производство крыш. Частое и широкое использование штукатурки парижа и подвесных потолков в строительных проектах будет стимулировать активное проникновение на рынок силиката кальция. Кровля для текстильных и автомобильных заводов также использует этот продукт в значительных количествах.
Доля на мировом рынке активного силиката кальция является конкурентоспособной; с American Elements, Promat International, Skamol, Ramco Industries, HIL Limited и Johns Manville, Bee Chems, BIP Chemicals, Weifang Hong Yuan Chemical, Imerys Filtration Minerals, Anglitemp, 2K Technologies и R. K. Нефтяная промышленность играет ключевую роль.
Компании, работающие на рынке, сосредоточены на производстве и строительстве помещений, с функциями противопожарной защиты и изоляции в качестве ключевых преимуществ, которые могут создать новые возможности для роста.Статистика торговли свидетельствует о сильном экспорте продукции в регионы с дефицитом, такие как Южная Африка, Саудовская Аравия и ОАЭ, которые могут предложить сильное региональное присутствие.
Просмотрите ключевые отраслевые идеи на 150 страницах с 154 таблицами рыночных данных и 12 рисунками и диаграммами из отчета, «Активный рынок силиката кальция по областям применения (изоляция, противопожарная защита, керамика, цемент, краски и покрытия), региональный прогноз, Ценовые тенденции, конкурентная доля рынка и прогноз на 2024 год », а также содержание:
https: // www.gminsights.com/industry-analysis/active-calcium-silicate-market
Оглавление (ToC) отчета:
Глава 3 Активный анализ рынка силиката кальция
3. 1 Глобальная сегментация отрасли
3.2 Размер рынка и перспективы роста, 2013-2024 гг.
3.3 Анализ отраслевой экосистемы
3.3.1 Анализ каналов сбыта
3.3.1.1 Сотрудничество / партнерство
3.3.1.2 Лицензирование технологий
3.3.1.3 Поставка изоляционных плит
3.3.2 Матрица поставщиков
3.4 Торговая статистика
3.5 Расчетная производственная мощность
3.6 Анализ цен
3.7 Динамика производства активных ингредиентов силиката кальция
3.7. 1 Факторы роста
3.7.1.1 Позитивный прогноз роста строительной отрасли
3.7.1.2 Рост керамической промышленности
3.7.2 Отраслевые подводные камни и проблемы
3.7.2.1 Руководящие принципы и правила, касающиеся воздействия продукта
3. 8 Ключевые возможности роста
3.9 Анализ Портера
3.10 Конкурентный ландшафт
3.10.1 Стратегический ландшафт
3.11 Анализ PESTEL
Просмотр полной таблицы of Contents (ToC) @
https://www.gminsights.com/toc/detail/active-calcium-silicate-market
О Global Market Insights
Global Market Insights, Inc.со штаб-квартирой в Делавэре, США, является поставщиком консалтинговых и исследовательских услуг по всему миру; предлагая синдицированные и индивидуальные отчеты об исследованиях вместе с консультационными услугами по развитию. Наши отчеты о бизнес-аналитике и отраслевых исследованиях предлагают клиентам проницательную информацию и практические рыночные данные, специально разработанные и представленные для помощи в принятии стратегических решений. Эти исчерпывающие отчеты разработаны с использованием собственной исследовательской методологии и доступны для ключевых отраслей, таких как химическая промышленность, современные материалы, технологии, возобновляемые источники энергии и биотехнологии.
Свяжитесь с нами: Арун Хегде Корпоративные продажи, США Global Market Insights, Inc. Телефон: 1-302-846-7766 Бесплатный звонок: 1-888-689-0688 Электронная почта: [email protected] Интернет: https://www.gminsights.com
Знакомство с кальциево-силикатным кирпичом
Кальциево-силикатный кирпич: практический пример
Жилой дом, построенный из силикатного кирпича
Некоторое время назад меня попросили исследовать структурные взломать большой жилой комплекс в Уэст-Мидлендсе.
При просмотре схемы и обнаружении трещин на здании у меня возникло сильное подозрение, что здание было построено из силикатного кирпича, но следует отметить, что не существует окончательного теста на месте для определения силикатного кирпича; Положительная идентификация может быть получена только после лабораторного анализа, в частности XRD (дифракции рентгеновских лучей), когда пики в кварците и кальците положительно подтверждают структуру силиката кальция. Однако базовое понимание этих кирпичей и их свойств может в некоторой степени помочь в правильной идентификации сайта.Поскольку мы знаем, что существует ряд известных проблем, связанных со строительством из силикатного силиката, первостепенной важности было определить форму каменной конструкции.
Кирпичи из силиката кальция (песчаная известь и кремневая известь) производятся путем смешивания извести, песка и / или измельченного кремнеземистого или кремневого камня с достаточным количеством воды, позволяющим формовать смесь под высоким давлением. Затем кирпичи автоклавируют с паром, чтобы известь вступила в реакцию с кремнеземом с образованием гидратированных силикатов кальция.Пигменты можно добавлять на стадии смешивания. В естественном состоянии кирпичи из силиката кальция имеют цвет от белого до кремово-кремового, но добавление охры (желтого или кремового цвета), оксидов железа (розового, красного, коричневого или черного) или оксида хрома (зеленого цвета) может позволить очень большое разнообразие цветов.
Тщательный осмотр кирпичей показал, что это были мелкие частицы кремня размером до 3 мм.
Виден врезанный кремень, и кирпичи очень легко царапаются об их поверхность.
Это соответствовало бы силикатному кирпичу, так же как и тот факт, что царапина на поверхности кирпича доказала, что они чрезвычайно мягкие. У них также нет «огненной кожи», как у глиняного кирпича. Их часто путают с бетонными кирпичами, но они намного сложнее и не так легко поцарапать. Наконец, фактором, который изменил баланс вероятности в пользу кирпичей из силиката кальция, была разница в цвете ниже и чуть выше уровня DPC. Кирпичи из силиката кальция имеют склонность ко всем вариантам цвета довольно заметно темнеть во влажном состоянии.Более влажные кирпичи ниже уровня DPC и чуть выше уровня dpc (где dpc был замкнут) заметно темнее.
Необычные явления изменения цвета, часто наблюдаемые в силикатно-кальциевом кирпиче
000000000000 Осмотр- Раствор значительно тверже, чем блоки кладки.
- DPC, перекрытые строительным раствором
- Регулярные и последовательные ступенчатые усадочные трещины по всей схеме
- Указание на деформационные швы в углах здания
- Потеря защиты деформационных швов в углах.
- Изменение цвета кирпичной кладки ниже и чуть выше уровня dpc.
- Переполненная кирпичная кладка на уровне ЦОД.
Регулярное ступенчатое растрескивание и плохой ремонт. Плоскость скольжения ЦОД также должна была быть установлена на уровне первого этажа.
Объяснение дефектов, отмеченных на схеме
- Раствор значительно тверже, чем каменные блоки: сам по себе не дефект, но силикатный кирпич из кальция склонен к усадке или расширению трещин, поэтому раствор должен «уступить» кирпичной кладке.Это невозможно, если использовалась слишком крепкая растворная смесь OPC. В идеале следует использовать известковый раствор, который будет иметь такой же коэффициент расширения, что и кладочные блоки.
Чрезмерно прочная смесь, несомненно, способствовала широко распространенной проблеме трещин от усадки в этой схеме.
- DPC, перекрытый строительным раствором: это, конечно, проблема, которая может привести к будущим проблемам с влажностью, но, что более важно, dpc является очень важной частью строительства из силикатного кирпича. DPC действует как плоскость скольжения для кирпичной кладки наверху и позволяет кирпичной кладке наверху двигаться более контролируемым образом без растрескивания.Направление вокруг стыка dpc служит только для предотвращения движения плоскости скольжения с опасностью возникновения неконтролируемых усадочных трещин в другом месте здания.
- Регулярные и последовательные ступенчатые усадочные трещины по всей схеме: я не считаю, что эти трещины вызывают беспокойство, помимо того факта, что требуется повторная наладка для улучшения эстетики и защиты открытых швов от атмосферных воздействий. Ничего не указывало на то, что эти трещины вызваны чем-либо, кроме усадки / расширения.
- Указание на деформационные швы в углах здания: Деформационные швы по самой своей природе предназначены для смещения, поэтому вы не герметизируете их строительным раствором против элементов, так как он негибкий, треснет и выпадет. Именно это и произошло на этой схеме, и необходимо удалить галтели раствора и заменить эластичной полисульфидной мастикой.
- Потеря защиты деформационных швов в углах: То же, что и в пункте 4, но замена строительного раствора герметиком восстановит защиту деформационных швов от атмосферных воздействий.
- Изменение цвета кирпичной кладки ниже и чуть выше уровня dpc: здесь нет никаких проблем, кроме различного эстетического вида более темной кирпичной кладки. Нет никаких технических проблем, связанных с этим, поскольку силикатные кирпичи имеют хороший уровень защиты от замерзания.
- Избыточная кирпичная кладка на уровне DPC: заслуживает упоминания, но, на мой взгляд, не является дефектом этой конструкции; он просто демонстрирует, что плоскость скольжения на уровне dpc действует в определенных областях так, как задумано.
- Раствор значительно тверже, чем каменные блоки: сам по себе не дефект, но силикатный кирпич из кальция склонен к усадке или расширению трещин, поэтому раствор должен «уступить» кирпичной кладке.Это невозможно, если использовалась слишком крепкая растворная смесь OPC. В идеале следует использовать известковый раствор, который будет иметь такой же коэффициент расширения, что и кладочные блоки.
Деформационный шов из сжимаемого фибрового картона установлен, но не работает должным образом из-за твердого цементного раствора. Стык следует заделать эластичной мастикой.
Диапазон исторических проблем, связанных с кальциево-силикатным кирпичом
- Температурное движение, вероятно, будет примерно в 1,5 раза больше, чем у глиняной кирпичной кладки. Кирпичная кладка из силиката кальция, в отличие от глины, обычно претерпевает первоначальную необратимую усадку при кладке (глиняная кладка имеет тенденцию расширяться), но до тех пор, пока склонность к перемещению понимается и учитывается в проекте, нет причин, по которым кирпичная кладка не должна работать должным образом .Часто этот фактор не учитывается при проектировании, и это приводит к широко распространенному растрескиванию.
- Кирпичи из силиката кальция не следует использовать в сплошных работах с глиняной облицовкой или основой, это связано с тем, что кирпичи склонны к усадке в отличие от расширения глиняной кирпичной кладки.
Если предполагается строительство сплошных стен, следует использовать основы из бетонных кирпичей или блоков, так как они имеют такие же характеристики движения, как и силикатный кирпич. Мы часто видим неправильный выбор материала стенок для внутренней створки, и это создает противодействующие силы из-за дифференциального расширения, что снова приводит к широко распространенному растрескиванию.
- Общие конструктивные детали часто не принимаются во внимание, особенно в отношении обеспечения достаточной гибкости стеновых анкеров, чтобы допускать дифференциальные движения, и допуска разрывов вокруг заглушек для предотвращения растрескивания.
4. Требования к встроенным плоскостям скольжения часто не соблюдаются. Внутри стены из силикатно-кальциевой кирпичной кладки должны быть уложены на гидроизоляционный слой, чтобы действовать как плоскость скольжения и, таким образом, способствовать возникновению продольных движений — это было бы одинаково необходимо на уровнях верхних этажей, деталь, которая была упущена в этой схеме.
5. Контроль движения в ограждении — не единственная проблема — также учитывайте элементы здания, которые могут оказывать сдерживающее влияние. Например, следует избегать бетонных колонн или стен, упирающихся в кирпичи, если не может быть предусмотрена скользящая мембрана. — как и любая конструкция, препятствующая свободному движению. В этой схеме расположение деформационных швов и ДПК обеспечивают это сдерживающее воздействие.
6. Нет ничего необычного в том, чтобы увидеть некоторые формы смещения кирпичей из силиката кальция из-за теплового расширения, например, соскальзывание кирпичной кладки с гидроизоляционного слоя, растрескивание в углах или явное нарушение.Напротив, растрескивание при усадке обычно не вызывает этих проявлений.
DPC направлен вверх, но движение через плоскость скольжения DPC вызвало разрушение строительного раствора и, таким образом, восстановило функцию естественной плоскости скольжения.
Заключение
Кирпич из силиката кальция часто получает плохую репутацию в прессе из-за проблем, освещенных здесь; однако следует сказать, что они являются превосходным строительным материалом, если понятны детали конструкции, необходимые для предотвращения усадки или расширения. К сожалению, чаще всего эта детализация не понимается, и здания обычно строятся так же, как и глиняные кирпичи. По некоторым показателям они превосходят глиняный кирпич, особенно по морозостойкости.
Вопрос для этой конкретной схемы заключается в том, была ли детализация строительства настолько плохой, чтобы вызывать серьезные опасения в отношении долгосрочного будущего или жизнеспособности этих блоков? На мой взгляд, особых опасений не было; блоки структурно прочны, и к трещинам следует относиться как к эстетической детали.Качество предыдущего наведения было довольно низким, и это до некоторой степени повредило блоки некрасивой или несоответствующей работой, и мало что можно сделать, чтобы обратить вспять это повреждение. Направляющая должна быть удалена с dpc, чтобы позволить ему действовать как плоскость скольжения и остановить повышение влажности выше уровня dpc. Кроме того, с вертикальных деформационных швов в углах блоков следует удалить ограничивающую кромку раствора и затем соответствующим образом загерметизировать высококачественной полисульфидной мастикой.