Плита из опилок как называется: OSB – материал из стружки и прессованных опилок
OSB – материал из стружки и прессованных опилок
В наше время постоянного развития стройматериалов все так же остается востребованным хороший отделочный материал. Конечно же, в этом плане лидирует дерево, которое, скорее всего, уже никто не заставит сойти с пьедестала. Но есть и обратная сторона медали – древесина становится дефицитным материалом, поэтому и цена на нее увеличивается в геометрической прогрессии. Из-за этого производители все чаще создают отделочный материал, грубо говоря, из отходов деревообрабатывающей промышленности – опилок и обломков. Казалось бы, отходы, которые годны только на растопку печей, но из этих никому не нужных опилок получается один из самых востребованных отделочных материалов на Земле – плиты OSB. Данная фанера из стружки постепенно захватывает рынки всех стран, став уже незаменимой в любом строительном проекте.
Способ создания материала из прессованных опилок
Плиты ОСБ (или ОСП) на самом деле создаются из прессованных опилок.
Фанера из стружки после всех данных процедур становится чрезвычайно крепкой и красивой, поэтому ее применяют для отделки как внутренних, так и внешних стен. Кроме того, ОСБ используются для выравнивания полов и создания домов из сэндвич-панелей. Также именно ОСП плиты используются дизайнерами всего мира для внутренней отделки, так как их природная фактура и раскраска украсят любое жилище.
Достоинства фанеры из стружки
В народе ОСБ плиты называют «совершенной древесиной» из-за богатства вариантов применения данного чудесного материала. Можно выделить такие его преимущества:
прочность. Плиты ОСП чрезвычайно прочны, что обусловлено спецификой их создания и обработки. Данное качество позволяет использовать материал в особо опасных производствах, где наблюдается повышенный риск физических и механических воздействий.
пожаробезопасность. Во время создания конструкторы обрабатывают фанеры из прессованных опилок специальным нейтральным составом, который предохраняет материал от возгорания.
устойчивость к паразитам. Ни короеды, ни мыши, ни плесень, которые часто становятся настоящей проблемой хозяев дома из настоящего дерева, не могут повредить ОСП, так как данный материал имеет специальную защиту от подобных атак.
сплошную структуру. Многие строители жалуются на природный брак древесины — сучки и пустоты, которые образовываются из-за впадения веточек. Фанера из стружек обладает цельной структурой, так как все ее основание заполнено непрерывным потоком опилок.
звуко/теплоизоляция. ОСП плиты будут сохранять тепло, которое вырабатывается нагревательными приборами, внутри жилища. С той же эффективностью материал блокирует идущие снаружи холод и звуки, не пропуская их в дом.
простота монтажа. Монтировать фанеру из прессованных опилок может один человек с минимальным количеством инструментов и отсутствием строительного опыта.
длительный срок эксплуатации. Простая древесина имеет небольшой срок эксплуатации, ограниченный несколькими десятками лет. Плиты ОСП имеют намного более развитую защиту, поэтому период их использования практически неограничен.
Данный список преимуществ перевешивает те невеликие недостатки, которые имеет данный чудесный материал.
Недостатки фанеры из стружек
Как и любой материал, ОСП плиты имеют некоторые недостатки. Особенно мастера-строители отмечают вред от материала. Самой уязвимой точкой ОСП плит является тот факт, что они могут негативно влиять на здоровье человека. Данный эффект вызывается высоким содержанием фенола, который выделяет в воздух канцерогенные вещества. Стоит заметить, что существует несколько типов ОСП плит, а среди них есть марка материала GREEN – полностью безопасного для человека. Поэтому нужно попросту во время покупки ОСП внимательно смотреть на сертификат – если там указан класс Е0, значит материал безопасен для человека.
Важная информация: чтобы обезопасить свою семью от вредного формальдегида, для внутренних работ нужно применять только экологически чистые виды ОСП. Если же учесть это правило не получается, то стоит заложить ОСП плиты утепляющим слоем из пенопласта и настроить качественную вентиляцию помещения.
Также нельзя забывать о том, что разные производители создают различные по качеству плиты. Так, например американские фирмы выпускают фанеры из прессованных стружек только высокого экологического качества. Отечественные производители также постепенно выходят на достойный уровень, но при покупке таких материалов стоит все же сверяться с сертификатами. А вот китайский ОСП является самым некачественным типом материала, поэтому покупать его для внутренних отделок помещения крайне неразумно, даже если сертификаты утверждают обратное.
Обзор утеплителей из опилок — как выбрать
Современные и эффективные утеплители не смогли полностью вытеснить с рынка экологически чистые и испытанные поколениями материалы. Для теплоизоляции дома не редко используются универсальные и доступные по цене древесные опилки. Экономия средств и снижение себестоимости строительства — основные факторы, заставляющие сделать выбор в пользу такого теплоизолятора. Чтобы сделать объективные выводы о целесообразности использовать опилки как утеплитель, необходимо рассмотреть их плюсы и минусы.
Характеристики, особенности и виды утеплителей из опилок
Отходами пиления и переработки древесины являются стружки различного размера, который зависит от параметров оборудования. Предпочтение стоит отдать средней фракции, с пылью сложно работать, а крупные частицы увеличивают теплопроводность. Эти остатки получили широкое применение в хозяйственных целях: подстилки для животных, мульчирующий материал, теплоизоляция домов. Опилки в чистом виде имеют существенные недостатки и не применяются для теплоизоляции. Перед использованием их обрабатывают составами от гниения и возгорания, перемешивают с различными веществами: песком, известью, медным купоросом.
Тепло и звукоизоляционные свойства древесной стружки сопоставимы с минеральной ватой, материалы укладываются одинаковым по толщине слоем. Кроме насыпного способа ее применяют при изготовлении строительных материалов.
Дерево-блок — смесь опилок, обработанных медным купоросом, и цемента. Вещества соединяются в пропорции 1:8 и засыпаются между стен, укрытых гидроизоляционным полотном. Влага, выделяемая из древесины при утрамбовывании, способствует связыванию состава.
Опилкобетон — блоки из раствора стружки, песка, цемента и воды.
Сухие составляющие смешиваются, и постепенно добавляется вода. Из раствора формируются огнестойкие блоки с низкой теплопроводностью.
Арболит — легкий бетон, 90% состава которого занимают отходы деревообработки. Из материала изготавливают плиты и блоки, отличающиеся прочностью и стойкостью к горению. Арболит чувствителен к влаге, поэтому требует гидроизоляции.
Преимущества использования природного теплоизолятора
- Экологическая безопасность — это одно из основных преимуществ продукта. Опилки как утеплитель сохраняют все полезные свойства дерева и не представляют опасности для здоровья человека.
- Экономическая выгода — отходы деревообработки имеют низкую стоимость, некоторые предприятия отдают их даром при условии самовывоза.
- Надежность — практика использования стружки для теплоизоляции дома насчитывает сотни лет.
Такой срок свидетельствует о качестве материла, которому не нашли достойной альтернативы.
Универсальность — опилками утепляют стены, чердачные перекрытия и пол здания.
Недостатки натурального утеплителя:
- высокая горючесть;
- использование грызунами в качестве жилища.
Минусы древесной стружки известны давно, поэтому с ними научились справляться. В качестве защиты от крыс и мышей добавляются различные вещества: гашеная известь в пропорции до 10% общего объема, табак — 10-15% смеси, борная кислота.
Для обеспечения пожарной безопасности опилки обрабатываются антипиренами или включаются в состав негорючих веществ.
Способы утепления потолка
Для теплоизоляции перекрытий используются опилки мелкой и крупной фракции, смешанные с известью, медным купоросом или бурой. Работа начинается с настилания подложки, препятствующей просыпанию мелкой трухи. Распространенным вариантом является сухой картон, его раскладывают с нахлестом в 15 см и закрепляют скобами. Подложка должна пропускать пар, чтобы не образовывался конденсат, вызывающий рост плесени.
Утеплитель из опилок формируется несколькими способами: сухим, с добавлением цемента, в смеси с глиной.
Сухой вариант предполагает засыпку в два слоя. Первой укладывается крупная фракция, на слой в 15 см насыпается мелкая труха и утрамбовывается. Для лучшей усадки допускается увлажнение, общий слой теплоизоляции достигает 25-30 см. Защитить опилки можно покрытием из глины, шлака или песка.
Смесь стружек и цемента создает прочное и надежное покрытие для изоляции потолка. Вещества перемешиваются в соотношении 20:2 и увлажняются. Перед раскладыванием утеплителя насыпается песчаная подушка высотой 3-4 см. Раствор опилок и цемента утрамбовывают до толщины 10 см. После его застывания поверхность накрывают настилом из досок или фанеры.
При изготовлении смеси с глиной, она перемешивается, и растворятся в воде, а после засыпаются опилки. Готовый состав не должен растекаться, его наносят на потолочное перекрытие слоем в 10 см. Каждый участок утрамбовывается и разглаживается, трещины после высыхания замазывают глиной.
Особенности теплоизоляции пола
Использовать опилки как утеплитель пола экономически выгодно и безопасно. Материал обязательно проходит предварительную обработку антисептиками, для отпугивания грызунов добавляется гашения известь, битое стекло и медный купорос. Засыпка одной стружкой со временем дает усадку, поэтому при изоляции пола всегда добавляются вещества, способствующие затвердению утеплителя.
Опилки смешивают с известью гипсом или цементом, при необходимости добавляется вода. Раствор должен при сжатии сохранять форму. Смесь с гипсом очень быстро твердеет, поэтому готовится небольшими порциями.
Перед выполнением теплоизоляции на перекрытия наносится влагостойкая грунтовка и настилается пароизоляционная пленка. На подложку выкладывается состав и тщательно трамбуется. После застывания смеси укладывается напольное покрытие.
Предотвратить промерзание пола можно составом с применением глины. Получаемый раствор имеет жидкую консистенцию, поэтому требует настилания в основание гидроизоляционной пленки. Смесь глины и опилок готовится в бетономешалке, на поверхность наносится слоем до 10 см и разравнивается доской. Для сушки раствору потребуется 1-2 недели. Готовый утеплитель покрывается мастикой от влаги и закрывается финишным деревянным настилом.
Как выполнить утепление стен опилками
Создание надежной теплоизоляции из натурального древесного материала между каркасными стенами достаточно сложный процесс. Используется стружка большого размера, смешанная с известью и гипсом. Между перегородкой и утеплением размещается гидроизоляционное полотно. Смесь увлажняется и закладывается вручную слоями по 25-30 см, обязательно хорошо трамбуется. Из-за проседания могут образоваться пустоты, пропускающие внутрь холод. Теплоизоляция должна заполнить все пространство каркаса, ее толщина составляет от 15 до 30 см. До полного затвердения состава потребуется около 1 месяца.
Рекомендации по выбору и использованию опилок:
- При выборе стружки оценивается ее внешний вид, не стоит приобретать материал с большим количеством посторонних предметов. Имеющийся мусор выбирают вручную или просеивают.
- При использовании древесных отходов необходимо ответственно подходить к обеспечению пожарной безопасности. В местах прохождения печных труб устанавливают защиту из негорючих материалов, электропроводку размещают в специальных коробах.
- Стружку обрабатывают антисептиком от гниения и насекомых, антипиреном и гидрофобизаторами. Эти составы должны быть совместимы друг с другом, лучший вариант — продукция одного изготовителя.
- Для создания утепляющей смеси лучше использовать не свежие опилки, а полежавшие 2-3 месяца. За это время из древесины выветрятся вещества, препятствующие прочному связыванию раствора, и потребуется меньшее количество цемента. Если нет возможности приобрести продукцию нужной кондиции или подождать, можно улучшить свойства смеси добавлением жидкого стекла.
- Теплоизоляцию рекомендуется выполнять в летний период, когда есть возможность хорошо просушить состав, предотвратив развитие плесени в процессе эксплуатации.
- Перед добавлением медного купороса или другого химического вещества, необходимо надеть средства защиты.
- Стружка различных пород древесины отличается своими свойствами. Хвойные отходы содержат смолу, отпугивающую насекомых, поэтому их используют для изоляции дома. Лиственные стружки идут на утепление хозяйственных построек.
Из чего делают мебель?
Мебель могжет быть выполнена из различных материалов, которые обладают любыми свойствами. Материалы бывают натуральными, не натуральными. Можно встретить изделия из массива дерева, а так же из прессованных опилок. Разберёмся подробнее в вопросе о том, из чего производят мебель и как это может сказываться на ее эксплуатации.
Древесные плиты
Большинство наших предметов мебели изготовлены именно из дерева, а точнее — из частиц дерева. Поэтому сейчас пойдёт речь о перечне материалов, которые используют для производства прессованных заготовок для производства мебели.
Компания «Аист» продаёт детские коляски оптом российского и польского производства. Купите детскую коляску по выгодной цене в Интернет-магазине. Доставка товара по Москве и регионы России.
МФД
Этот материал производится из древесных опилок. Частицы очень малы, это практически древесная мука. Её прессуют горячим методом, для наилучшего сцепления частиц используют связующие материалы. К таковым относятся парафин и лигнин. Особенностью этого материала считается его высокая экологичность, так как связующие элементы совершенно натуральны, поэтому они полностью безвредны для человека.
Мебель из МДФ обладает хорошими техническимихарактеристиками, материал очень плотный. Его плотность практически приближена к плотности массива дерева, поэтому на нем позволительно вырезать различные узоры. Резные украшения мебельных изделий выполняются именно на этом материале. Он довольно качественный, но не выдерживает некоторых внешних воздействий. Для него губительны высокая температура, его нельзя использовать вблизи нагревательных приборов. Если температура будет выше 70 градусов, то материал может разбухнуть. А вот влаги он не боится, так происходит за счёт наличия в нем парафина. Он обладает влагостойкими свойствами. Стоит этот материал не дёшево, многим может быть не по карману. Довольно часто можно встретить мебельные изделия, которые только на некоторую часть выполнены из этого материала. Он не вызывает аллергии, хорошо подходит для детской комнаты.
ДСП
Этот материал производится из древесных стружек и опилок, в ход могут идти как отдельные заготовки, так и отходы производства. Связующим элементом являются смолы. Смолы обычно используются феноловые и формальдегидные. Это не самым лучшим образом сказывается на качестве изделия, оно не очень экологично. Прессованные опилки обычно снаружи прикрываются декоративными элементами. Для этого может быть использован ламинат, шпон, меламин.
ДСП делится на три категории, каждая из которых имеет определенный уровень качества. Этот сорт производится из более качественных материалов. Поверхность готового изделия гладкая и ровная. Такая плита может покрываться декоративным слоем, быть покрашена. Этот материал может иметь различные внешние дефекты, обычно это трещины и сколы. Материал может быть с декоративным покрытием, а может и нет. Такой сорт характеризуется наличием большого количества дефектов. Обычно используется как черновой материал. Любой ДСП боится воды, поэтому стоит избегать попадания на него жидкостей. Так же этот материал очень хрупкий.
ЛДСП
Этот материал представляет собой прессованную древесную плиту, которая покрыта специальным покрытием. Из ЛДСП производят ламинат и предметы мебели. Устройство материала напоминает собой заламинированную бумагу. Древесная плита покрывается пленкой, подобно бумаге при ламинировании. Поверхность образует защитный и декоративный слой. Такой материал может быть устойчив к воздействию внешней среды. Так же для этого материала характерен приятный внешний вид.
Используется материал для изготовления ламинат, а так же подходит для производства мебели. Такую мебель можно встретить практически в каждом доме. Из ЛДСП можно изготовить как бюджетную, и экономную мебель, так и мебель премиум класса. Материал имеет недостаток — низкий уровень экологичности. При производстве материала используют формальдегиды, смолы. А они, как известно, очень токсичны и могут сказываться на здоровье человека не лучшим образом.
ДВП
Это материал, который не отличается высокой прочностью. Он производится из прессованных опилок, щепок и древесной крошки. Материал довольно долговечен, но он имеет значительные недостатки. Его технические свойства таковы, что он очень гибок и мягок. Его не используют для производства мебели, его применяют в виде панели для закрытия задней стенки шкафов. В народе этот материал называют деревянным картоном, если оценивать его качества с технической точки зрения, то он и вправду напоминает картон.
Материалов для производства мебели очень много, мы рассмотрели самые основные, наиболее распространённые варианты. Учитываете характеристики материалов при выборе мебели, от этого будет зависеть срок и качество эксплуатации, а так же воздействие мебели на ваш организм.
Листовые материалы на основе древесины
Производство мягкой мебели не обходится без листовых (плитных) материалов на основе древесины. Это ДВП, ДСП, фанера и другие материалы. Все это с добавлением деревянных брусков используется для изготовления каркасов диванов и кресел — основного элемента конструкции, на котором закрепляются все остальные части.
В компании «Эгида» вы можете приобрести следующие листовые (плитные) материалы:
Древесноволокнистая плита (сокращенно ДВП)
Древесноволокнистые плиты — листовой материал, изготовляемый в процессе горячего прессования массы из древесных волокон, сформированных в виде ковра. Эти волокна получают путём пропарки и размола древесного сырья. Они представляют собой отдельные клетки тканей, их обрывки или группы клеток древесины. Сырьём служат отходы лесопиления и деревообработки, технологическая щепа и дровяная древесина.
Лицевая и оборотная стороны панелей ДВП
Для улучшения эксплуатационных свойств в массу добавляют упрочняющие вещества (например, синтетические смолы), гидрофобизаторы (парафин, церезин), антисептики и др. Из ДВП изготавливают конструкционные элементы мебели, задние стенки и полки шкафов и тумб, нижние полки у диванов, выдвижные ящики, спинки кроватей, перегородки. В практике твёрдые ДВП иногда называют оргалитом (т.е. «органическим камнем»), но вряд ли такой термин приемлем, учитывая способность твёрдых ДВП при погружении в воду разбухать и поглощать за сутки до 20-30% воды.
Древесностружечная плита (сокращенно ДСП)
ДСП — сокращенное наименование древесностружечной плиты, которая изготавливается из прессованных древесных опилок и стружек, пропитанных связывающим веществом, а именно — формальдегидными смолами различных типов. ДСП — это листовой материал, получаемый путем горячего прессования крупнодисперсионной стружки.
Древесностружечные плиты изготавливают из различных видов древесины (неделовая древесина, отходы лесопиления, деревообработки, фанерного производства, технологической щепы, полученной из отходов лесозаготовок).
В качестве связующих веществ в нашей стране используются при горячем прессовании плит преимущественно карбамидоформальдегидные смолы. ДСП плоского прессования характеризуются плотностью 550…850 кг/м3. Для применения в мебельном производстве ДСП имеет также декоративное покрытие из пленок, шпона, бумажно-слоистого пластика (ламината) и лака. Часто, внешние слои — более плотные из мелкодисперсной стружки. Водостойкая ДСП на срезе имеет характерный зеленоватый цвет. Так как связующее вещество содержит фенол, для обеспечения безопасности в изделиях из ДСП не допускаются открытые торцы плит, они должны быть окрашены, оклеены или загерметизированы любым другим способом.
Ламинированная древесностружечная плита (сокращенно ЛДСП)
ЛДСП — трехслойные плиты, получаемые в результате облицовывания ДСП пленками на основе бумаг, пропитанных синтетическими смолами.
Из высушенной и покрытой клеем стружки сухим методом формируется «ковер», который подвергается плоскому прессованию, в процессе которого клей затвердевает, связывая плиту. Ламинированная ДСП благодаря своим свойствам (устойчивостью к истиранию, царапинам, воздействию температуры и химических веществ), а также широкой гамме цветов и структур поверхности, находит широкое применение в мебельной промышленности, а также в строительных, отделочных и столярных работах. Для ламинирования ДСП используются пленки на основе термореактивных полимеров, оригинальных отечественных и западных текстурных бумаг, пропитанных меламиновыми смолами.
Фанера
- Размеры 1525*1525(квадратная) 1220*2440 (длинная).
- Толщина: 3.5, 4, 7, 9, 12, 15 (мм).
Основным плитным конструкционным материалом является фанера. Это многослойный материал, изготовленный из березового или древесины хвойных пород, шпона, в котором все слои склеены между собой в горячем прессе под давлением с применением клея на основе карбамидоформальдегидной смолы.
Количество слоёв шпона обычно нечётное, от 3 и более. Для повышения прочности фанеры слои шпона накладываются так, чтобы волокна древесины были строго перпендикулярны предыдущему листу.
Березовая фанера благодаря своей прочности широко используется в мебельном производстве. Мебель из березовой фанеры отличается элегантным внешним видом и хорошими эксплуатационными характеристиками. Именно элегантность внешнего вида, а так же хорошая сопротивляемость механическим повреждениям делают березовую фанеру практически незаменимым материалом для внутренней отделки помещений.
Хвойная фанера отличается высокой прочностью, хорошо переносит повышенную влажность, и практически не подвержена грибковым заболеваниям. Эти свойства ей придает высокое содержание смол в древесине. Поэтому фанера хвойная часто используется в малоэтажном домостроении в качестве материала для наружных и внутренних отделочных работ. Дом, обшитый хвойной фанерой, отличается долговечностью.
Фанера хвойная как материал также прочно вошла в мебельное производство. Это произошло благодаря хорошим эстетическим свойствам. Хвойная фанера не только отлично смотрится, она легкая и долговечная.
Офисная мебель. Состав материала, для изготовления мебели
Чаще других материалов используется плита ДСП – состоит из прессованной стружки, из различных пород дерева ,которая достигается путём горячего прессования с карбамидоформальдегидными смолами. Благодаря этому веществу, прочность ДСП высока. Плиты ДСП покрывают краской или специальной плёнкой , это исключает испарение смол и по оценке экологии не уступает другим материалам.
Следующий более дорогой материал — МДФ. Это тоже плита, и в состав её входит очень мелкая стружка, как пыль, из отходов и опилок разнообразных пород дерева. Плита МДФ не такая плотная, этот материал изготавливается методом как сухой пресс, без смол. Благодаря такой технологии МДФ можно ставить на ступень выше по экологии, чем ДСП. При изготовлении плит МДФ, используют метод, который связывает мелкую стружку. Путём нагревание древесины, выделяется лигин. Он является натуральным материалом, который выполняет роль связующего звена. Благодаря такому процессу МДФ становится самым безопасным материалом, который проходит все экологические нормы и стандарты. Для повышения прочности МДФ облицовывают в плёнку.
Самый прочный и крепкий материал ДВП. Принцип изготовления этого материала похож на предыдущие, только прессование происходит горячим методом. Его изготовляют в виде листов, в состав входит древесная стружка и волокна от разных пород деревьев. Так как листы имеют не большую форму, они крепче и надёжней. У ДВП есть название «оргалит». При горячем прессовании стружки и волокон используют смолы. Этот материал проходит герметизацию, то есть покрывают краской, плёнкой и т. п., естественно для здоровья нет какого- либо вреда человеку.
Все представленные материалы довольно крепкие и прочные для офисной мебели, по качеству не ниже, чем натуральная целиковая древесная плита. Как показывает практика при использовании, мебель из этих материалов очень проста в уходе, при любых температурах сохраняет свою форму, и не боится каких либо механических повреждений.
При изготовлении мебели, при распилах этих плит на детали, где видны все горизонтальные части и торцы, как правило эти места обрабатывают кромкой, чтоб смотрелось эстетично, и выполняло функцию прочности. Кромка для облицовки изготовляют из разного материала. Искусственные — это ламинат, меламин, и т.п., но есть и натуральная облицовка — это шпон , который выполняется из среза натурального древесного листа, по толщине могут быть различные.
Что такое ламинат? Это такой материал, в состав которого входит бумага специального изготовления. Она прессуется, и пропитывается смолой из полимера, благодаря этому этот материал становится очень прочный. Бумага, которая создает основу для ламината, может быть любого цвета, структуры, даже с рисунком . Кромочный материал , с такой фактурой, создаст для мебели красивый , гармоничный вид , защитит мебель от каких либо ударов и повреждений, температурных воздействий и выделение вредных смол для здоровья. Что такое меламин? В состав изготовления этого материала, тоже входит натуральная бумага, пропитывается смолой, которая называется меламиновая . Кромочный материал из меламина более тонкий, чем ламинат. Меламин могут производить любого цвета, структуры. Он тоже прекрасно защитит мебель от повреждений, вредных выделяемых смол и придаст красивый вид. Эту кромку в основном используют, когда мебель изготовляется из ДСП.
Перечисленные материалы прекрасно подходят, и используются для изготовления офисной мебели. Они придадут такой мебели привлекательный, стильный, модный вид.
Опалубка из древесностружечных плит — информационная статья от компании Новатор
Опалубкой называют каркас из дерева (досок, фанеры, ДСП, ОСБ), металла (алюминия, стали), пенополистирола (пенопластовых листов), цементно-стружечных плит и других стройматериалов. Подготовленную форму заливают цементом или бетоном. Такое сооружение делают для возведения монолитных секций на строительной площадке. Конструкцию для создания формы различают съемную и несъемную, а также классифицируют по назначению. Ее используют для построения стен, лифтовых шахт, перекрытий, колонн, ступеней, фундамента, оград и других сооружений.
Что представляет собой несъемная форма из ДСП
Опалубка из ДСП производится из габаритных листовых элементов, которые соединяются при помощи креплений из металла. Как правило, данную систему применяют при возведении стен, перегородок и обустройства потолка. Плиты из прессованных стружек не снимают после затвердевания цементного или бетонного раствора. Они не являются утеплителем, как опалубка из пенополистирола, и требуют дополнительного утепления при необходимости. Но, несмотря на это, каркас из данного материала имеет ряд преимуществ:
- простая и быстрая сборка;
- небольшая масса листов, что облегчает монтаж и делает возможным бетонировать форму даже одному человеку;
- исключение демонтажа, а это значительно сокращает объем строительных работ;
- идеально ровная поверхность, не требующая дополнительного выравнивания;
- конструкция готова к финишной отделке, покраске, побелке и других видов фасадных работ.
Как изготовить такую опалубку самостоятельно?
Форму для бетонных элементов можно изготовить без особой трудности. Для этой цели следует использовать древесностружечные плиты толщиной не менее 18 мм. Исходя из получения желаемой высоты бетонных элементов, нужно предварительно распилить листы по размерам. Также надлежит позаботиться о наличии брусьев со сторонами 30 и 40 мм, саморезов длиной не менее 60 мм, гвоздей 80 мм, целлофановой плотной пленки (от 0,2 мм), арматуры, вязальной проволоки. Также совсем нелишними будут шуроповерт и строительный степлер со скобами.
Приготовленные по размеру секции будущей формы обертывают пленкой, которую закрепляют скобами на внутренней стороне. Этот шаг необходим для обеспечения влагоизоляции, которая повлияет на время застывания смеси, что в будущем скажется на качестве сооружения.
Основу, на которой будет производиться строительство, также необходимо изолировать от влаги (обычно кладут ленту из рубероида). Теперь пришло время к порезке вязальной проволоки. Требуется высчитать периметр всей формы и учесть ее высоту, а затем нарезать проволоку так, чтобы ее отрезки можно было разложить поперек рубероидной ленты по всей ее длине на расстоянии 1,2-1,5 м. Это понадобится для дополнительного стягивания щитов.
Из имеющихся брусьев сооружается рама, размер которой равен необходимой бетонной постройки. Подготовленные плиты стягиваются между собой с помощью саморезов с внешней стороны. Если применяются гвозди, то ими закрепляют ДСП изнутри. Сбитые щиты устанавливают поверх проволоки, а внутрь ставится рама из брусьев, которая послужит ограничителем ширины. Теперь концы проволоки хорошо связываются сверху над опалубкой. В качестве распорки следует вставить и закрепить гвоздями поперечный брусок. Внутренняя рама аккуратно передвигается, и процесс повторяется, пока не будет собрана вся форма для заливки.
Такую опалубку можно разбирать и использовать неоднократно. Однако проволока из-под готовой бетонной конструкции не вытягивается, а отрезается для исключения образования пустот. Этот вариант используют для возведения фундамента или основы для ограды высотой не выше 300 мм. Если стенку опалубки необходимо сделать выше, то используют арматуру для укрепления бетонного сооружения. На каждые дополнительные 250 мм используется один прут диаметром 18 мм.
Преимуществом такой формы является ее цена, которая ниже всех остальных материалов, а также возможность неоднократного использования, благодаря ее защищенности пленкой.
Чем и как пилить ОСБ-плиту?
Ориентированно-стружечная плита является довольно популярным материалом, используемым в строительстве. Материал этот сокращенно называют ОСП или ОСБ. Такой крупноформатный лист нуждается в подгонке по нужным размерам, поэтому мастерам приходится производить подобные действия непосредственно в процессе работы. В статье дана подробная информация о том, как просто и качественно произвести распил ОСБ-плиты.
Основные правила
ОСБ-плиты являются одними из наиболее популярных материалов, используемых для отделки помещений. С их помощью можно создавать несущие элементы зданий, выбирать в качестве разных видов обшивок. Используются подобные материалы при сборке корпусной мебели, лестниц и прочих конструкций.
Выбирая это изделие для работы, следует ознакомиться с принципом изготовления данного материала. ОСП представляют собой материал, имеющий 3 или больше слоев. Состоит каждый из них из размолотой щепы, смешанной со смолой. Длина и толщина щепы может быть самой разной, при этом ориентированы они в противоположные стороны. Чтобы плита была более прочной, все слои расположены в четком направлении, при этом расположение стружки в каждом слое происходит перпендикулярно предыдущему и следующему слоям.
В составе листовых древесных материалов имеются смола и клей для скрепления шпона, щепок и опилок. Благодаря этому плиты получаются упругими и довольно плотными.
Хотя по определенным показателям подобные материалы превосходят цельные изделия, работать с ними иногда бывает сложней. В основном это касается их распиливания.
Для качественного проведения распила ОСБ-листов следует использовать специальные инструменты, а также придерживаться некоторых правил.
-
Производят распил листов сначала поперек волокна, а затем вдоль него. Это позволит уберечь материал от деформации и расщепления.
-
Важным фактором является правильный подбор инструментов. Для распиливания на внутренней стороне больше подойдет пила (ручная или ленточная). При работе на обратной стороне чаще используется контурная или дисковая плита.
-
При использовании циркулярной пилы необходимо поддерживать скорость оборотов на довольно высоком уровне.
-
Материал следует подавать плавно, без рывков, иначе есть вероятность его порчи.
Выбор подходящих для данного материала инструментов позволит провести работу без заломов и иных дефектов.
Обзор инструментов
При не очень большом объеме работы произвести распил плиты в домашних условиях можно даже ручной пилой или ножом. Но качественно проделать это в данном случае вряд ли получится. Ручная ножовка не самый удачный инструмент, позволяющий пилить ОСБ-плиту. Даже опытные мастера редко могут сделать такую работу на должном уровне. При неимении иных, более подходящих инструментов резать плиту лучше пилой с мелкими зубьями, ведя инструмент полого. Нож также менее всего подходит для работы с OSB-листами, его чаще используют только для разметки.
Вот перечень подходящих инструментов, используемых при распиливании листовых материалов.
-
Электролобзик. Этот инструмент больше подходит при необходимости делать криволинейный рез. Кроить же лобзиком листы по прямой довольно сложно. В процессе работы могут возникать дефекты в виде сколов и ворса на одной из сторон изделия, поэтому правильный выбор пилки в данном случае очень важен.
- Ручной электрический фрезер.
Использование этого инструмента позволит отрезать плиту чисто и ровно. Но при этом нередко приходится делать несколько проходов при большой толщине плиты.
- Наиболее удачным вариантом для раскроя подобных материалов считается циркулярка. При использовании дисковой пилы рез получается очень качественный. Мотор обладает достаточной мощностью для распила даже довольно толстых листов. Работа с подобным инструментом позволит получить при распиле кромку, перпендикулярную лицевой поверхности листа. Изменение наклона позволит сделать кромку под углом 45 градуса. Для получения лучшего результата стоит использовать диски с большим количеством зубьев.
ОСП-плиты обычно имеют большие размеры, поэтому предпочтительней производить распил их на полу. Если необходимо произвести распиливание большого количества таких листов, целесообразно делать это на специальных подмостках.
Независимо от выбора инструмента, необходимо плиту немного приподнять, используя небольшие бруски из дерева. Работая с лобзиком или ножовкой, их располагают вдоль реза.
Используя циркулярную пилу, бруски нужно положить поперек. Удачное же расположение подкладочных брусков не позволит материалу сломаться.
Рекомендации по раскрою
Используя советы опытных мастеров по резке подобных материалов, можно распилить OSB-листы быстро и без дефектов.
-
В процессе работы скорость вращения прибора должна быть максимальной.
В том случае, когда пила начнет идти с усилием, или при «подгорании» заготовки – необходимо уменьшить скорость вращения инструмента. При этом нужно обеспечить минимальную скорость его подачи.
-
Перед тем как отрезать лист, необходимо произвести пробный срез, выбрав ненужный кусок материала. Это позволит убедиться в хорошей видимости разметки, а также подобрать наиболее подходящую скорость, оценить качество работы, определиться с размером готового изделия.
-
Основным правилом при распиливании листов является непрерывное и плавное ведение инструмента, так как при остановке часто остаются следы. Многие новички, стараясь избежать сколов в конце, начинают дорезать плиту с двух сторон, что неверно.
-
Необходимо убедиться в доступе к разметке, удобно распределить кабель рабочего инструмента.
-
Пилить необходимо не по линии разметки, а рядом с ней.
-
Производя разметку, необходимо учесть толщину пропила.
-
Перед началом работы следует убедиться, что инструмент работает на полную мощность. Это обезопасит от «обратного удара».
-
Завершив работу, необходимо подождать, пока диск полностью не остановится, а затем вынимать его из листа.
Основной задачей мастеров при фиксации плит является исключение вероятности заклиниваний оснастки в листе в процессе работы. А также необходимо исключить излишнюю вибрацию. Для защиты лицевой поверхности от поднятий ворса и от сколов используют подходящие для этого инструменты, а также выбирают нужные режимы их работы. Некоторые специалисты советуют наклеить по линии реза малярный скотч, сделав разметку прямо сверху него – это позволит получить качественный рез.
Многие рекомендуют производить разметку с помощью острого ножа. В этом случае лезвие ножа будет прорезать волокна в верхних слоях, снижая вероятность возникновения сколов. Для получения четкой линии реза желательно выбрать «направляющую» в виде обрезной доски, бруска, обрезка материала с ровными краями или правила из алюминия. Направляющую закрепляют на плите с помощью саморезов.
Правильно подобрав инструмент и подготовив его к работе, можно обеспечить желаемый результат без лишних затрат сил и времени.
Смотрите видео о том, чем распилить ОСБ-плиту.
КЛАССЫ КАЧЕСТВА ДСП – Фанера
КЛАССЫ КАЧЕСТВА ДСП
Древесностружечные плиты подразделяются на семь различных классов в зависимости от их свойств. Свойства классов стружечных плит определяются в соответствии с общеевропейским стандартом SFS-EN 312. Классы древесностружечных плит обозначаются буквой «P» и числом.
не устанавливают требований к качеству поверхности плиты, но производители классифицируют плиту по качеству A- и B в зависимости от ее внешнего вида.При определении качества поверхности необходимо учитывать такие факторы, как качество отделки, гладкость и чистота поверхности и дефекты на краях.
Класс | Применение | Класс пользователя |
---|---|---|
Р1 | Строительные плиты для внутренних работ | 1 |
Р2 | Мебельные щиты для внутренних работ | 1 |
Р3 | Ненесущая плита, плита, которая лучше сопротивляется влаге, чем стандартная древесно-стружечная плита | 2 |
Р4 | Плиты, выдерживающие нагрузку, для внутренних работ | 1 |
Р5 | Для приложений, которые должны выдерживать нагрузки, плита, которая лучше противостоит влаге, чем стандартная древесно-стружечная плита | 2 |
Р6 | Половые доски, способные выдерживать большие нагрузки, для внутренних работ | 1 |
Р7 | Для приложений, которые должны выдерживать сильные нагрузки, плита, которая лучше противостоит влаге, чем стандартная древесно-стружечная плита | 2 |
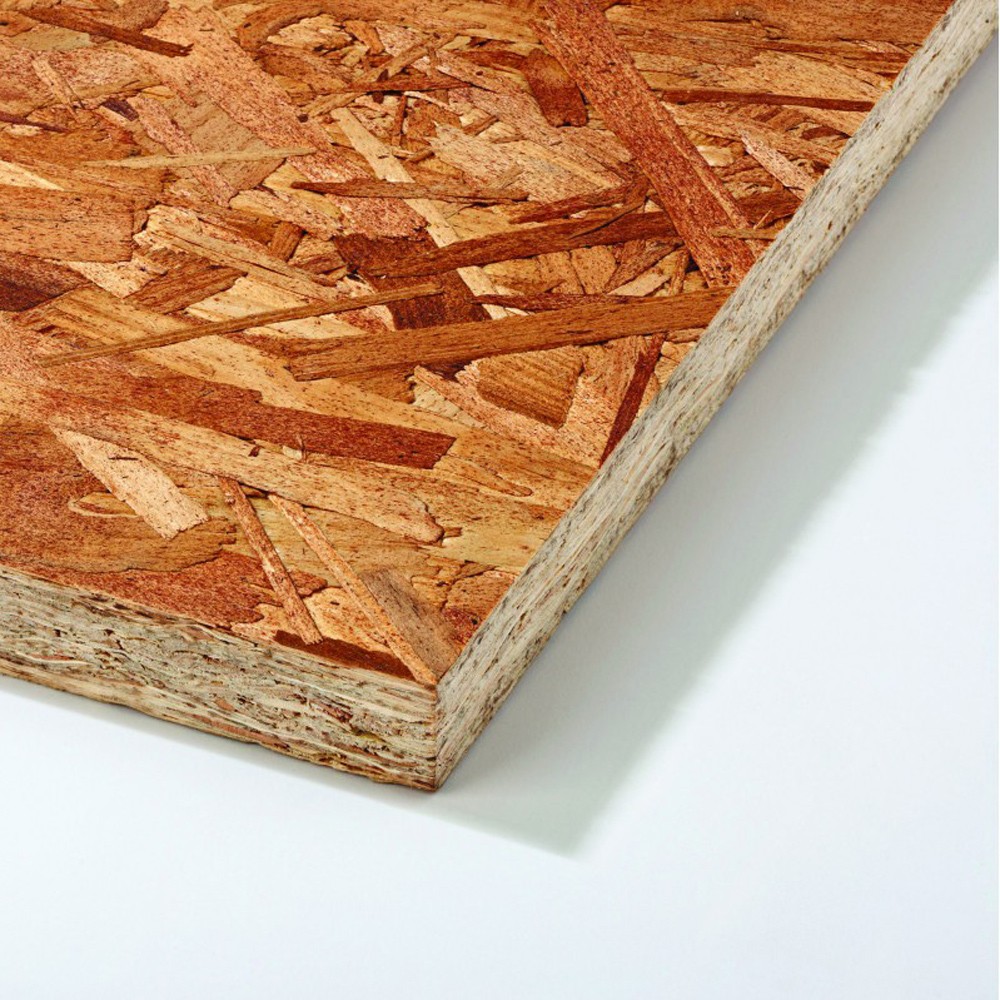
(PDF) Производство цельнодревесных древесностружечных плит на основе опилок с использованием процесса плавления с использованием ионной жидкости
348
Wood Science and Technology (2021) 55:331–349
1 3
Ссылки
9000 Келли А.Л., Вера-Соррош Дж. и др. (2014) Эффективность процесса экструзии полимеров: корреляция между потреблением энергии и термической стабильностью расплава.Appl Energy 135: 560–571. https://дои.org/10.1016/j.apene rgy.2014.08.086
Atalla RH, Vanderhart DL (1984) Натуральная целлюлоза: смесь двух различных кристаллических форм. Science
223:283–285
Cai Z, Ross RJ (2010) Механические свойства композитных материалов на основе древесины. Wood Handb wood as
an Eng Mater Chapter12 Centen ed Gen Tech Rep FPL; GTR-190 Madison, WI US Dept Agric For
Serv For Prod Lab 2010 p 121–1212 190:11–12
Croitoru C, Patachia S (2014) Биокомпозиты, полученные из древесных опилок с использованием ионных жидкостей. Acta
Chem Iasi 22:113–134
Eriksson K-EL, Blanchette RA, Ander P (2012) Микробное и ферментативное разложение древесины и компонентов древесины
, 1-е изд. Springer Science & Business Media, Heidelberg
Fan M, Dai D, Huang B (2012) Инфракрасная спектроскопия с преобразованием Фурье для натуральных волокон. В: Салих С.М.
(ред.) Анализ материалов с преобразованием Фурье. InTechOpen, Лондон, стр. 45–68
FAO (2017) 2016 г. Глобальные данные о лесных товарах, факты и цифры Арвидас Лебедис (редактор), FAO-Food and agricul- ture
Организация Объединенных Наций, Рим
Foston M (2014) Достижения в твердотельной ЯМР целлюлозы.Curr Opin Biotechnol 27:176–184
Голампур А., Озбаккалоглу Т. (2020) Обзор композитов из натуральных волокон: свойства, модификации
и методы обработки, характеристика, применение. J Mater Sci 55: 829–892. https://дои.
org/10.1007/s1085 3-019-03990 -y
Graenacher C (1934) Растворы целлюлозы. Пат. US1943176
Гровер П.Д., Мишра С.К. (1996) Брикетирование биомассы: технология и практика. Продовольствие и сельское хозяйство
Организация Объединенных Наций, Бангкок, Таиланд
Исогай А., Усуда М., Като Т., Урю Т., Аталла Р.Х. (1989) Твердотельное CP/MAS исследование углерода-13 ЯМР цел-
люлоза полиморфы.Макромолекулы 22: 3168–3172. https://doi.org/10.1021/ma001 97a04 5
Johnson DL (1969) Укрепление набухающего волокнистого материала оксидом амина. US US 3447956A 3 стр.
Khakalo A, Tanaka A, Korpela A, Hauru LKJ, Orelma H (2019) Композитный материал All-Wood путем частичного растворения поверхности волокна
ионной жидкостью. ACS Sustain Chem Eng 7:3195–3202. https://дои.
org/10.1021/acssu schem eng.8b050 59
Хакало А., Танака А., Корпела А., Орелма Х (2020) Делигнификация и обработка древесины ионными жидкостями
для получения многофункциональных высокоэффективных конструкционных материалов.Интерфейсы приложений ACS. https://
doi.org/10.1021/acsam i.0c022 21
Kilpeläinen I, Xie H, King A, Granstrom M, Heikkinen S, Argyropoulos DS (2007) Растворение древесины
в ионных жидкостях. J Agric Food Chem 55:9142–9148. https://doi.org/10.1021/jf071 692e
Lahaye M, Rondeau-Mouro C, Deniaud E, Buléon A (2003) Исследование твердотельной 13C ЯМР-спектроскопии
ксиланов в клеточной стенке Palmaria palmata (L , Кунце, Родофиты). Carbohydr Res 338:1559–
1569.https://doi.org/10.1016/S0008-6215(03)00241-6
Le KA, Rudaz C, Budtova T (2014) Фазовая диаграмма, предел растворимости и гидродинамические свойства целлозы
в бинарных растворителях с ионная жидкость. Карбогидр Полим 105: 237–243. https://doi.org/10.1016/j.
carbp ol.2014.01.085
Li W, Sun N, Stoner B, Jiang X, Lu X, Rogers RD (2011) Быстрое растворение лигноцеллюлозной биомассы
в ионных жидкостях с использованием температур выше температуры стеклования лигнина.Зеленая химия 13: 2038–2047.
https://doi.org/10.1039/C1GC1 5522A
McNatt JD (1973) Основные инженерные свойства древесно-стружечных плит. Лаборатория лесных товаров, Мэдисон,
Висконсин
Митчуал С.Дж., Фримпонг-Менса К., Дарква Н.А. (2013) Влияние видов, размера частиц и давления уплотнения на релаксированную плотность и прочность на сжатие топливных брикетов. Int J Energy Environ Eng
4:30. https://doi.org/10.1186/2251-6832-4-30
Nishino T, Arimoto N (2007) Полностью целлюлозный композит, полученный путем селективного растворения поверхности волокна.
Биомакромолекулы 8:2712–2716. https://doi.org/10.1021/bm070 3416
Нишино Т., Мацуда И., Хирао К. (2004) Цельноцеллюлозный композит. Макромолекулы 37: 7683–7687. https://
doi.org/10.1021/ma049 300h
Olsson A-M, Salmén L (1997) Влияние состава лигнина на вязкоупругие свойства древесины.
Nord Pulp Pap Res J 12:140–144
Содержание предоставлено Springer Nature, применяются условия использования. Права защищены.
101 Лучшее цепляющее название для опилок
Одной из вещей, которых в избытке при работе с деревом, являются опилки.Это пыль от распиливаемого дерева, обычно люди просто подметают ее и выбрасывают, но она становится все более ценной! Эта пыль может быть спрессована в доски, которые затем могут быть использованы для других целей, вывести предприятия по производству опилок на передний план строительства и пиломатериалов. Вот несколько замечательных названий существующих предприятий по производству опилок, которые вы можете использовать, чтобы вдохновить свои собственные.
84 Пиломатериалы
ABC South Lumber and Hardware
Almond Brothers Lumber Co.
American Lumber Co.
Опилки Artesia
Мельница Avana Grogans
Avondale Bark & Topsoil
BC Перевозка стружки
BC Wood Work
Bella Cera Wood Co. Company
Cherokee Wood Products
Clarks Lumber and Sawdust
Colton Enterprises
Cox Lumber and Supplies
Crossroad Sawmill
Crossroads Recycled Lumber
Crown Shavings
De Jong Sawdust & Shavings
Diamond Pacific
Dodge Grain Co.
Пиломатериалы Долана
Восточное побережье Пиломатериалы
East Coast Lumber
Экономичная лесозаборник
Дальнее West Forest
Фрэнк Пиломатериал
GI GANAHL
GI Shavings
Golden State Lumber
Griffis Saw Mill
Hancock Lumber
Herms Lumber Salumbs
High Sierra Lumber
Древесная стружка
Houston Wood Co.
Humboldt Redwood Company
Hunts Timber Inc
Jones Lumber Company
Justice & Sons Wood Shavings
Kelseyville Lumber & Supply
Kimal Saw Dust Removal
Kinder Sawmill
La Mesa Lumber 3 Hardwood
Lumbers Unlimited 3 Hardwood
Поставка пиломатериалов
Mason’s Mill
Строительные материалы McCoy’s
Meek’s Lumber & Hardware
Midwest Price Co.
Mount Storm Forest Product
National Sawdust
Neiman Reed Lumber
Nichols Lumber Co.
No Waste Grindings
NorCal Lumber Co.
Northridge Lumber Company
Notie Corporation
NW Dry Shavings
Paul Davis Lumber Co. Пиломатериалы и строительные материалы
Raymond Building Supply
Red Mill Lumber
Redwood Empire
Redwood Lumber Supply
Regus Tallahassee
Ron Lyons Trucking
Rosedale Mills
Rust and Sawdust
Salas & Son Sawdust & Shavings
Saroyan Hardwoods и
Stuff
Склад опилок
Sawdust Hill Alpaca Farm
Sawdust Sales
Sawdust Supply Co.
Sawmill Park
Shore Line Sawmill
Sierra Pacific Industries
South Florida Lumber
Southern Pine Lumber Company
Stall Master Co. Пиломатериалы
True American Grain
We Rock the Spectrim
Деревянный настил
Woodberry Farm
Вы будете поражены тем, что можно сделать с опилками и другими обрезками древесины в современном мире.Это удивительная технология, которая превращает опилки в пригодные для использования доски.
Древесностружечные плиты и ориентированно-стружечные плиты на основе клея, армированного наноцеллюлозой
Клеи на основе карбамидоформальдегидных (КФ) и меламино-карбамидоформальдегидных (МУФ) широко используются в производстве древесных плит . В настоящем исследовании была предпринята попытка улучшить механические свойства плит путем армирования этих клеев нановолокнами целлюлозы (УНВ).Последние были произведены из буковой целлюлозы растворимого сорта методом механической гомогенизации. Клеевые смеси с содержанием УНВ 0, 1 и 3 мас. % на основе твердой смолы готовили путем смешивания водной суспензии УНВ с клеями УФ и МУФ. Были изготовлены древесно-стружечные плиты и ориентированно-стружечные плиты (OSB) лабораторного масштаба, и были исследованы механические свойства и механические свойства на излом. Древесностружечные плиты, изготовленные с применением UF, содержащего 1 мас.% CNF, показали меньшее набухание по толщине, лучшую внутреннюю связь и прочность на изгиб, чем плиты, изготовленные с использованием чистого UF.Армирующий эффект УНВ был еще более очевиден для OSB, где было обнаружено значительное улучшение прочностных свойств на 16%. Как для древесно-стружечных плит, так и для OSB энергия разрушения в режиме I и вязкость разрушения были параметрами с наибольшим улучшением, указывающим на то, что клеевые соединения заметно упрочнялись при добавлении УНВ.
1. Введение
Спустя почти 80 лет после своего изобретения древесностружечные плиты по-прежнему представляют наиболее важную группу древесных плит в Европе.В 2010 г. доля стружечных плит в общем объеме производства древесно-стружечных плит составила около 63 % [1]. Помимо древесностружечных плит, ориентированно-стружечные плиты (OSB) приобретают все большее значение как в декоративных, так и в конструкционных целях. Для использования в качестве строительного материала механические свойства плит имеют жизненно важное значение. В связи с этим качество соединений между древесными частицами является ключевым фактором, который, в свою очередь, определяется количеством и типом используемого клея. В производстве древесных плит преобладают аминопластические клеи на основе карбамидоформальдегидных (КФ) и меламинокарбамидоформальдегидных (МУФ).Эти клеи имеют ряд преимуществ для промышленного применения; однако механические характеристики клеевых соединений UF и MUF для древесины ограничены. Поскольку модуль упругости отвержденных аминопластических линий склеивания высок, деформация клеевого слоя при механическом нагружении обычно невелика. В результате образуются концентрации напряжений по линии скрепления клеевого соединения древесины [2–4], снижающие общую прочность соединения.
В прошлом предпринимались различные попытки уменьшить хрупкость UF и, таким образом, улучшить его прочностные характеристики.Подходы варьируются от химической модификации UF-полимера или смешивания с другими полимерами (например, [5–11]) до армирования различными видами волокон. Поскольку известно, что UF-смолы обладают сильной адгезией к большинству целлюлозосодержащих материалов, волокна на основе целлюлозы, по-видимому, хорошо подходят для усиления UF. Это подтверждено экспериментально рядом работ (например, [12–17]). Поскольку при производстве древесно-стружечных плит клей распыляется на мелкие капли диаметром около 40–60 мкм мкм до связывания древесных частиц, армирующие элементы должны быть микро- или наноразмерными [18]. Следовательно, применение целлюлозных нановолокон (УНВ) для армирования клея представляется перспективным.
В то время как можно найти значительное количество публикаций по армированию полимеров нановолокнами из целлюлозы, литература по армированным целлюлозой клеям, подходящим для склеивания древесины, довольно скудна. Рихтер и др. [19] обсуждали применение УНВ для армирования однокомпонентных полиуретановых и поливинилацетатных (ПВА) латексных клеев для древесины на водной основе. Хотя оба клея, содержащие целлюлозу, хорошо показали себя в механических испытаниях, не удалось добиться значительного и последовательного улучшения характеристик линии склеивания по сравнению с эталонными продуктами.Авторы определили одинаковую полярность волокон и полимера, контролируемую по качеству морфологию волокон и тщательно сбалансированную загрузку волокон в диапазоне от 1 до 5% масс. как критические параметры, определяющие механические свойства клеев, армированных УНВ. В другом исследовании [20], выполненном той же исследовательской группой, изучалась пригодность использования УНВ для приготовления смесей ПВА-адгезив, дающих линии склеивания с повышенной термостойкостью. Значительно повышенный модуль упругости был обнаружен для пленок ПВА-латекс, армированных УНВ, с помощью динамического механического анализа.Кроме того, образцы соединений внахлестку, изготовленные с использованием клея, армированного целлюлозой, показали значительно повышенную термостойкость. В совсем недавнем исследовании Atta-Obeng [18] армировал фенолформальдегидный (PF) клей микрокристаллической целлюлозой при различной степени загрузки от 0 до 10 % масс. Испытания на сдвиг внахлест показали увеличение прочности при добавлении целлюлозы. С другой стороны, древесностружечные плиты, изготовленные из ПФ с наполнителем из целлюлозы, показали худшие механические свойства в испытаниях на статический изгиб и большее набухание по толщине, чем плиты, связанные с чистым ПФ.Это объясняется менее выраженным эффектом пружинения при горячем прессовании. Армирование целлюлозой, по-видимому, ограничивает пружинистость доски после того, как напряжение сжатия, вызванное горячим прессованием, снимается.
Автор пришел к выводу, что это приводит к отслоению древесных частиц и клея, что приводит к снижению эксплуатационных характеристик плиты.
Собственные исследования [21] показали, что добавление 5 % масс. CNF к обычно используемому клею UF позволяет выполнять клеевые соединения из массивной древесины со значительно повышенной прочностью на сдвиг внахлестку в соответствии с EN 302-1 [22].Поскольку деформация до разрушения была значительно выше для образцов, армированных CNF, был сделан вывод, что клей UF, возможно, был усилен добавлением фибриллированной целлюлозы. В последующем исследовании [23] изучалось влияние добавки УНВ на удельную энергию разрушения клеевых соединений твердой древесины. Энергия разрушения определялась для плоских образцов с двойной консольной балкой (DCB), как описано Гальяно и Фрейзером [24]. Поскольку энергия разрушения UF-связей, заполненных 2 % масс. CNF, была на 45% выше по сравнению с чистыми UF-связками, это исследование доказало возможность повышения ударной вязкости UF путем добавления CNF.
Целью настоящего исследования было выяснить, приводит ли добавление УНВ к клеям для древесины на основе формальдегида к улучшению механических свойств древесных плит, изготовленных с их использованием. Лабораторные древесно-стружечные плиты и плиты OSB были приготовлены с использованием коммерчески доступных клеев UF и MUF, которые были усилены добавлением небольшого количества CNF. Исследовано реологическое поведение клеевых смесей и механические свойства готовых плит.
2. Материалы и методы
2.1. Получение целлюлозных нановолокон
Исходным материалом, используемым для получения УНВ, была никогда не высушенная растворимая буковая пульпа (Lenzing AG, Ленцинг, Австрия) с содержанием сухого вещества около 50% масс. Пульпу предварительно замачивали в дистиллированной воде на 2 часа. После этого более крупные агрегаты волокон были разрушены с использованием смесителя Ultra-Turrax, работающего при 21500 мин -1 в течение 3 мин. Сухое содержание волокнистой суспензии было установлено на уровне 0,5% масс. Для получения нановолокон суспензию фибриллировали за 30 проходов через лабораторный гомогенизатор высокого давления (APV 1000, APV Manufacturing Sp.z o.o., Быдгощ, Польша) работали при давлении 700–800 бар. Гомогенизированную суспензию сушили на воздухе при 70–80°С до достижения содержания целлюлозы 1,5 ± 0,1 % масс. Суспензию впоследствии использовали для приготовления клеевых смесей с целлюлозным наполнителем.
Нановолокна были охарактеризованы с помощью атомно-силовой микроскопии (АСМ). Одну каплю 0,002%-ной суспензии УНВ наносили на слюдяной диск и оставляли сохнуть при комнатной температуре до испарения воды. Изображение АСМ было выполнено на АСМ Dimension Icon (Bruker Corp., Санта-Барбара, США). Изображения получали в режиме постукивания со скоростью сканирования 0,5-0,6 строк в секунду с использованием стандартного кремниевого кантилевера (TESPA, Bruker Corp., Санта-Барбара, США).
2.2. Приготовление и определение характеристик клеевых смесей
Для приготовления древесно-стружечных плит в лабораторных условиях применялся клей УФ, используемый в производстве древесно-стружечных плит (Prefere 10F102, Dynea Austria GmbH, Кремс, Австрия). Клеевые смеси с содержанием целлюлозы 1 и 3 % от массы твердой смолы готовили добавлением соответствующего количества 1.5% суспензии УНВ к клею. Наполненный целлюлозой клей перемешивали ручным блендером в течение 3 мин для достижения надлежащего распределения УНВ в УФ-матрице. В качестве отвердителя для UF-смолы использовали раствор 10 мас.% аммиачной селитры в воде. Панели OSB были изготовлены с использованием порошкообразного клея MUF (Prefere 4681, Dynea AS, Лиллестрём, Норвегия) без дополнительного отвердителя. Содержание целлюлозы составляло 1% от массы твердой смолы. Состав отдельных клеевых смесей приведен в таблице 1.
| |||||||||||||||||||||||||||||||||||||||||||||||||||||||||||||||||||||||||
строительство | мебели | ||||||||||||||||||||||||||||||||||||||||||||||||||||||||||||||||||||||||
инфраструктура | |||||||||||||||||||||||||||||||||||||||||||||||||||||||||||||||||||||||||
6 | |||||||||||||||||||||||||||||||||||||||||||||||||||||||||||||||||||||||||
6 | Другие приложения (упаковка, автомобиль) |
Северная Америка |
Соединенные Штаты Америки |
Канада |
Mexico |
Европа |
Германия |
Великобритания |
Италия |
Россия |
Франция |
Остальной Европы |
Read of Source America |
Ближний Восток и Африка |
Саудовская Аравия |
Южная Африка |
Остальная часть Ближнего Востока и Африки |

Ключевые тенденции рынка
Растущий спрос со стороны мебельной промышленности
- В связи с изменением образа жизни населения за последние годы резко изменились предпочтения в отношении стиля мебели. Современная мебель состоит из таких элементов, как простые линии, стулья с прямоугольными краями и различные сочетания цветов.
- В мебельной индустрии представления об интерьерах домов, офисов и квартир постоянно меняются.Это стимулирует инновации и развитие, в первую очередь с точки зрения дизайна, размера и цвета. Ожидается, что это увеличит объем производства мебели по всему миру.
- Увеличение спроса на новое офисное строительство, вероятно, приведет к росту изучаемого рынка, поскольку наблюдается увеличение спроса на напольные покрытия, кубические перегородки, стеновые панели, подвесные потолки, двери и мебель. Кроме того, ожидается, что реконструкция и реконструкция существующих офисных зданий поддержит спрос на продукцию в прогнозируемое время .
- Страны, включая Китай, США и Германию, занимают крупнейшие рынки мебельной промышленности.Китай является доминирующим экспортером деревянной мебели в ЕС.
- В Индии разрешены прямые иностранные инвестиции исключительно в строительные проекты в сфере туризма, включая развитие отелей, курортов и рекреационных объектов. Ожидается, что это повысит гостиничный сектор и окажет положительное влияние на спрос на мебель в этих структурах.
- Dream Hotel Group планирует инвестировать около 300 миллионов долларов США в течение следующих трех-пяти лет в развитие круизного сектора в Индии. Ibis, часть Accor Group, планирует инвестировать более 500 крор индийских рупий, чтобы добавить еще четыре объекта, предлагая 685 ключи к 2024 году.
- Ожидается, что все вышеупомянутые факторы будут влиять на мировой рынок в течение прогнозируемого периода.

Чтобы понять основные тенденции, загрузите образец Отчет
Азиатско-Тихоокеанский регион будет доминировать на рынке
- В Азиатско-Тихоокеанском регионе ожидается устойчивый рост рынка древесно-стружечных плит благодаря развитию строительной и мебельной промышленности в таких странах, как Китай, Индия.
- Китай является крупнейшей рыночной базой в Азиатско-Тихоокеанском регионе благодаря постоянно растущему населению, росту доходов и быстрой урбанизации.Он также является одним из основных производственных центров практически для всех отраслей промышленности. Следовательно, развитие инфраструктуры в стране будет постоянно расти.
- Строительная отрасль Китая быстро развивалась благодаря стремлению центрального правительства к инвестициям в инфраструктуру для поддержания экономического роста.
- Правительство Индии активно стимулирует жилищное строительство, стремясь обеспечить жильем около 1,3 миллиарда человек. Страна, вероятно, станет свидетелем около 1 доллара США.3 триллиона инвестиций в жилье в течение следующих семи лет и, вероятно, станет свидетелем строительства 60 миллионов новых домов в стране. Ожидается, что к 2022 году Индия внесет около 640 миллиардов долларов США в строительную отрасль благодаря правительственным инициативам в области доступного жилья, такого как жилье для всех планов.
- Растущая строительная деятельность в регионе и растущая тенденция использования инженерных изделий из дерева в интерьерах приводят к увеличению спроса на древесностружечные плиты, что, в свою очередь, стимулирует рост изучаемого рынка в Азиатско-Тихоокеанском регионе.
Чтобы понять тенденции в географии, загрузите образец Отчет
Конкурентная среда
Рынок древесно-стружечных плит по своей природе фрагментирован из-за присутствия нескольких крупных игроков в разных странах. Некоторые из основных игроков (не в каком-либо определенном порядке) на рынке включают West Fraser, Roseburg Forest Products, Georgia-Pacific, Wanhua Ecoboard Co. Ltd и Kastamonu Entegre.
Содержание
1.Введение
1.1 Учебные результаты
1.2 Учебные предположения
1,3 масштабы исследования
7
2.
Методология исследования
3. Представительское обеспечение
4. Рыночная динамика
4.1 Драйверы
4.1
4.1.1 Увеличение спроса из мебельной промышленности
4.1.2 Простая доступность сырья
4.2 Ограничения
4.2.1 Угроза джинги средней плотности в качестве замены
4.2.2 Неблагоприятные условия, возникающие из-за воздействия COVID-19
4.3 Анализ цепочки цепочки промышленности
4.4 Анализ пяти сил портера
4.4.1
64.4.1 Торговая мощность поставщиков
4.4.2 Торговая мощность потребителей
4.4.3 Угроза новых участников
4.4.4 Угроза подстановки продуктов и услуг
4,4,5 градусов конкуренции
5. Сегментация рынка
5.
1 Сырье
5.1.1 Wood
5.1. 1.1 Sawdust
5.1.1.2 Shavings
5.1.1.3 Flakes
5.1.1.4 Чипсы
5.1.2 Bagasse
5.1.3 другое сырье
- 7
5.2.4 Прочие приложения (упаковка, автомобиль)
5.3 География
5.3.1 Asia-Pacific
5.3.1.1 China
5.3.1.2 Индия
5.3.1.3 Япония
5.3.1.4 Южная Корея
5.3.1.5 Отдых Азиатско-Тихоокеанского океана
5.3.2 Северная Америка
5.3. 2.1 Соединенные Штаты
5.3.2.2 Canada
5.3.2.3 Mexica
5.3.3 Европа
5.3.3.1 Германия
5.3.3.2 Великобритания
5.3.3.3 ИТАЛИЯ
5.
3.3.4 Россия
5.3.3.5 Франция
5.3.3.6 Отдых Европы
5.3.4 Южная Америка
5.3.4.1 Бразилия
5.3.4.2 Argentina
5.3.4.3 Отдых Южной Америки
5.3.568
5.3.5.1 Саудовская Аравия
5.3.5.2 Южная Африка
5.3.5.3 Отдых на Ближнем Востоке и Африка
60 60677 9096
6. Конкурентный пейзаж
68
6.1 слияния и поглощения, совместные предприятия, совместные отношения и соглашения
6.2 Доля рынка **/Рейтинговый анализ
6.3 Стратегии, принятые ведущими игроками
6.4 Профили компаний
6.4.1 Associate Decor Ltd
5
2 6.4.1 Associate Decor Ltd
5
24,2 Boise Cascade
6.4.3 века PROWUD
6.
4.44 D & R HENDERSON PTY LTD
60677
6.4.5 EGGER
60677
6.4.6 Georgia-Pacific
6.4.7 Kastamonu Extegre
6.4.8 Krifor Industries Pvt. Ltd
6.4.9 Peter Benson (Plywood) Limited
6.4.10 Roseburg Forest Products
6.4.11 Shirdi Industries Ltd.(Asis India)
6.4.12
6.4.12 Siam Riso Wood Products Co. Ltd
6.4.13 Timber Products Company
6.4.14 Uniboard
6.4.15 West Fraser
6.4 .16 Wanhua Ecoboard Co. Ltd
* Список не исчерпывающих
7. Рыночные возможности и будущие тенденции
7.1 Разработка новых методов для производства досок частиц
** до наличия
Вы также можете приобрести части этого отчета.Вы хотите проверить раздел мудро прайс-лист?
Получить разбивку цен В настоящее времяЧасто задаваемые вопросы
Каков период изучения этого рынка?
Рынок ДСП изучается с 2017 по 2027 год.
Каковы темпы роста рынка ДСП?
Рынок ДСП будет расти со среднегодовым темпом роста более 5% в течение следующих 5 лет.
Какой регион имеет самые высокие темпы роста рынка ДСП?
Азиатско-Тихоокеанский регион демонстрирует самый высокий среднегодовой темп роста в 2021–2026 годах.
Какой регион имеет наибольшую долю рынка ДСП?
Северная Америка будет иметь самую высокую долю в 2021 году.
Кто является ключевыми игроками на рынке ДСП?
West Fraser, Roseburg Forest Products, Georgia-Pacific, Wanhua Ecoboard Co., Ltd, Kastamonu Entegre являются основными компаниями, работающими на рынке древесно-стружечных плит.
80% наших клиентов ищут отчеты на заказ. Как ты хотите, чтобы мы подогнали вашу?
Пожалуйста, введите действительный адрес электронной почты!
Пожалуйста, введите корректное сообщение!
ОТПРАВИТЬ Загрузка.