Керамзит вес 1 м3 фракция 10 20: Ничего не найдено для d1 81 d0 ba d0 be d0 bb d1 8c d0 ba d0 be d0 b2 d0 b5 d1 81 d0 b8 d1 82 d0 ba d1 83 d0 b1 d0 ba d0 b5 d1 80 d0 b0 d0 bc d0 b7 d0 b8 d1 82 d0 b0 10 20
Сколько весит керамзит?
Одним из самых востребованных материалов является керамзит, который прекрасно подходит для теплоизоляционных работ. Но стоит иметь четкое представление о том, что керамзит бывает разной марки, что существенно влияет на вес.
Одним из важнейших показателей для керамзита является его насыпная плотность, которая влияет на удельный вес керамзита на один кубический метр. Существует ГОСТ за номером 9757-90, в нем определены все стандарты на различные марки, которых насчитывается около десятка. Самой меньшей насыпной плотностью обладает марка 250 кг/м3 (вес 1м3 керамзита составляет 250 кг).
Марка керамзита | Вес 1 куб. м. керамзита |
---|---|
М250 | 200-250 кг |
М450 | 400-450 кг |
Самым распространенным считается марка среднего показателя в 450 кг/м3 (вес 1 м3 керамзита составляет уже 450 кг).
Поэтому, при покупке керамзита стоит уделить внимание марке. Если возникнут проблемы с маркировкой, то стоит помнить, что вес 1 куба керамзита совпадает с его маркировкой.
Посмотрите, как производится керамзит:
Чтобы купить керамзит, звоните: +7 (499) 638-45-78
Сколько весит куб керамзита? Зависимость массы от фракции
Керамзит считается одним из наиболее востребованных строительных материалов, которые используются в качестве наполнителя. Благодаря небольшой массе и пористой структуре данный материал способен занимать большие объемы и выполнять роль хорошего теплоизолятора.
Фракции и их влияние на массу материала
Керамзитовый наполнитель имеет естественное происхождение и получается из глины, которую подвергают предварительному гранулированию и последующему обжигу. Вполне естественно, что спекшиеся частицы глины имеют неодинаковый размер в пределах до 40 мм. При этом окатыши, размеры которых составляют до 5 мм будут называться керамзитовым песком, частицы размером от 5 до 40 мм – гравием, а раздробленные окатыши – щебнем.
В данной ситуации масса керамзита будет напрямую зависеть от того, какой размер имеют частицы спекшейся глины. Чем мельче окатыши, тем они имеют меньшую пористость и большую массу.
Для определения массы керамзита в 1 куб. м важную роль будет иметь такой показатель, как насыпная плотность. Действует ГОСТ №9757-90, согласно которому к производителям выдвигаются определенные требования по маркировке керамзитовых наполнителей. На основании данного норматива определены конкретные марки материала.
Наименьшей насыпной плотностью, и соответственно массой, обладает керамзит марки М250, и вес 1 куб. м материала будет соответствовать 250 кг. В целом же, маркировка керамзита прямо указывает на массу материала в 1 куб. м. Если речь идет марке М450, то, следовательно, масса материала будет составлять 450 кг, если М1000 – то в 1 кубометре материала будет находится 1000 кг.
По сути, марка будет определять не прочность материала, а его массу. Впрочем, как утверждают аналитики, взаимосвязь между данными параметрами имеется. Материал с меньшим показателем пористости будет иметь более значительную массу. И, следовательно, из-за отсутствия воздушных прослоек его прочность будет в разы выше.
Если вы намерены приобрести керамзитовый наполнитель для строительных целей, приглашаем вас обратить внимание на предложение нашей компании. Мы сотрудничаем только с проверенными производителями, которые предлагают товар наивысшего качества. И потому вы всегда можете быть уверены не только в доступных и лояльных ценах, но и в высоком качестве товара.
Если у вас возникли вопросы относительно выбора керамзитового наполнителя, задать их вы можете нашим ведущим менеджерам в телефонном режиме по номеру +7 (343) 207-19-91 или же по электронному адресу [email protected].
Вес куба керамзита
Вес керамзита на метр кубический (насыпная плотность) – очень важный показатель. Он отвечает за допустимую нагрузку на основание, характеризует прочность изготавливаемого бетона, определяет уровень шумоизоляции, влияет на теплоизоляционные свойства материала. Для каждой марки керамзита насыпная плотность определятся простым способом: емкость, объем которой известен, предварительно взвешивается пустой, затем заполненной керамзитом. Разница веса (вес нетто) делится на объем емкости и получается значение кг/м3.
Вес куба керамзита в зависимости от марки
Данные о весе керамзита прописаны в его маркировке. При весе менее 250 кг/м3 – марка керамзита будет М250, вес 600-700 кг/м3 – марка М700 и так далее. Самая тяжелый керамзит М1000, его вес будет около одной тонны на 1 метр кубический. Керамзиты марки свыше М600 производятся по индивидуальным промышленным заказам, на регулярное основе выпускаются только марки М250-М600.
Соотношение марки керамзита и его веса представлено в таблице. Из нее можно сделать вывод, что вес керамзита примерно совпадает с его маркой.
Вес керамзита различной фракции
Вес 1м3 варьируется из-за фракции: чем меньше размер гранул (фракция) – тем выше вес материала в 1м3.
Правильный подбор фракции снижает расход цемента, показатели фракции учитываются в сфере работ (стяжка, стены, перегородки и др. ).
Если марку керамзита не идентифицировать, то примерный вес материала можно определить исходя из размера гранул.
Песок (менее 5мм) – 500 кг и больше Мелкий (5-10мм) — 400-500 кг Средний (10-20мм) – 350-400 кг Крупный (20-40мм) – 250-350 кг
Марка керамзита | Вес керамзита в 1 м3 |
---|---|
М250 | ≤ 250 кг |
М300 | 250-300 кг |
М350 | 300-350 кг |
М400 | 350-400 кг |
М450 | 400-450 кг |
М500 | 450-500 кг |
М600 | 500-600 кг |
М700 | 600-700 кг |
М800 | 700-800 кг |
Похожие материалы:
Объемный вес керамзита, плотность и удельный вес (кг / м3) – таблицы и описание
Объемный вес керамзита — один из основных технических показателей материала.
Рассмотрим детальнее важные технические характеристики стройматериала.
Удельный вес керамзита различных видов и фракций
Продукцию в основном классифицируют по диаметру зерен в составе. Как раз этот фактор влияет на стоимость. Фракции бывают следующими:
Фракция (мм) | Удельный вес (г/см3) | Вес (кг в 1м3) |
---|---|---|
0-0,5 | 0,55-0,6 | 550-600 |
5-10 | 400-450 | |
10-20 | 0,35-0,4 | 350-400 |
20-40 | 0,25 | 250-350 |
Чем крупнее зерна, тем меньше удельный вес и вес 1 кубометра. При заказе товара это стоит принимать во внимание.
Средний показатель удельного веса по марке прочности
Керамзит различают не только по размеру фракций. Имеет значение и марка прочности. Здесь наоборот: чем плотнее материал, тем он тяжелее. Следовательно, удельный вес будет расти с увеличением марки плотности:
- М250 — 0,2-0,25 г/см3;
- М300 — 0,25-0,3 г/см3;
- М350 — 0,3-0,35 г/см3;
- М400 — 0,35-0,4 г/см3.
Таким образом, если насыпная плотность составила 0,2-0,25 г/см3 (или 200-250 кг/м3), то марка стройматериала — М250. Продукт с весом 300-350 кг/м3 относится к марке М350. И дальше аналогично.
Удельная плотность – величина переменная. Она определяется типом стройматериала (то есть будет различаться для разных фракций керамзитового материала – гравия, песка и щебня). Истинная же плотность (Pu) — величина постоянная. Этот показатель как раз позволяет узнать средний удельный вес. Для расчета понадобится разделить вес сухого продукта на объем, без учета пор.
Формула такая:
Pu=m/Va.
Здесь Va — объем, m — масса.
Качественная продукция от «ТрансГруппСтрой»
В нашей компании продается сертифицированный керамзит разных марок и фракций. Выбирайте нужную продукцию с учетом планируемых рабочих задач. В прайс-листе указана цена при заказе определенного объема товара. Чем больше кубов, тем дешевле обходится продукт.
Оставляйте заявку на сайте для заказа продукции или пишите в чат и консультируйтесь.
Керамзит в мешках – сколько кубов понадобится? + Видео
Керамзит в мешках – универсальный утеплитель и наполнитель бетонных смесей, экологически чистый и безопасный для людей. Расфасовка по мешкам решает не только проблемы транспортировки небольшого количества материала, но и позволяет ускорить определенные строительные процессы.
Экологически чисто – назначение керамзита
Керамзит изготавливают уже не одно десятилетие, и хоть сегодня существует немало теплоизоляционных материалов, он по ряду характеристик остается уникальным. Изготавливают этот пористый гранулированный материал из специальных пород глины – благодаря высокому содержанию кварца они способны при высоких температурах вспучиваться и приобретать объем. Глина – самый главный компонент керамзита, что делает его абсолютно огнестойким и экологически чистым материалом. Готовый материал не содержит ни одного грамма токсичных веществ, а потому он до сих пор привлекает внимание строителей и заказчиков, которые ценят экологическую чистоту.
Пористый гранулированный материал
Чаще всего керамзит добавляют к бетону в качестве недорогого заполнителя. Готовая смесь имеет высокую прочность и относительно небольшой вес. Этот стройматериал также популярен и при утеплении перекрытий, кровли, фундаментов. Слой керамзита 10–15 см под полом значительно увеличивает теплоизоляцию напольных покрытий. Он не поддается воздействию агрессивных веществ и грибка.
Смесь бетона с керамзитом
Качество керамзита напрямую зависит от размеров гранул, объемного веса, насыпной плотности и прочности. Согласно ГОСТу, существует несколько фракций материала исходя из крупности гранул. Например, керамзит зернистостью менее 5 мм относят к керамзитовому песку, далее идут фракции 5–10 мм и 10–20 мм – их чаще всего и фасуют по мешкам, чтобы затем использовать для утепления или иных задач. Существует также классификация по маркам – в этом случае указывается его насыпная объемная масса. Чем мельче фракция, чем меньше поры, тем больше насыпная плотность и вес. Так, если на упаковке указана марка 300, то один метр кубический материала весит 300 кг.
Использование мешков для утепления пола
При утеплении пола важно понимать, что чем меньше насыпная плотность материала, тем меньший слой его нужен. Так, если вы приобрели керамзит марки 250, то для теплоизоляции будет достаточен слой в 25–30 см. Из марки 450 слой утепления должен быть не менее 40 см – чем больше вес, тем меньше пор в структуре гранул, и тем хуже их теплоизоляционные качества.
Керамзит марки 250 для утепления пола
При утеплении пола насыпается слой не меньше 10 см – в противном случае нужного эффекта не будет.
Насыпание 10-ти сантиметрового слоя утеплителя
Если материал расфасован по мешкам, то его так и укладывают на предварительно подготовленное основание. Мешки плотно подгоняют друг к другу и протыкают в нескольких местах ножом или отверткой, чтобы выпустить лишний воздух. Толщина упакованного материала составляет 15–17 см, поэтому сверху досыпают еще десять сантиметров, тщательно выравнивают и утрамбовывают. Поверх этой подушки производится традиционная стяжка.
Сколько керамзита в мешках – расчеты материала
Зачастую фасовкой керамзита в мешки занимаются сами строительные магазины – им так проще продать материал, а покупателям легче доставить на объект строительства. Фасуют чаще всего в полиэтиленовые или бумажные мешки объемом 50 литров – 1 кубометр керамзита помещается в 20 таких упаковок.
Мешки со строительным материалом объемом 50 литров
Реже бывает фасовка в упаковки побольше из расчета 16 мешков на 1 м3 или в упаковки поменьше – 30 мешков на куб. На всякий случай уточните, сколько литров в мешке. Рассчитать количество фасованного материала для стяжки очень легко. Например, если в комнате площадью 15 м2 вы хотите сделать стяжку поверх керамзитового слоя 15 см, вам понадобится:
15 м2 * 150 л (толщина, умноженная на 10) = 2250 литров или 45 мешков по 50 литров.
Оцените статью: Поделитесь с друзьями!Керамзит в Биг-Бэгах с доставкой в Москву и МО
Керамзит в биг-бегах

Применяется в качестве утеплителя, в домашнем цветоводстве для обеспечения водного баланса, для теплоизоляции грунтов и газонов. Керамзит активно закупают заводы для производства железобетонных конструкций. Применяют для звукоизоляции полов и стен домов.
Керамзит обладает хорошей морозостойкостью, влагоустойчив, огнеупорен, долговечен и экологичен, поэтому так востребован в строительстве.
Для удобства транспортировки керамзит продают в биг-бегах. Биг-бег – это мягкий контейнер с петлями (1-4), из полипропиленовой или капроновой ткани, отличающийся большими размерами и грузоподъемностью. Биг-беги могут быть в различных модификациях: с верхним или нижним клапаном, с раскрывающимся дном, с верхней сборкой, со специальными вкладышами. Содержимое биг-бега удобно высыпать, если развязать нижний клапан или просто разрезать дно. Насыпная плотность керамзита от 250 кг/м3.
У фасовки в биг-беги есть много преимуществ, среди которых: возможность переработки после использования, разнообразие моделей и модификаций, низкая стоимость, возможность хранения упакованного груза на открытых площадках. Биг-беги возможно транспортировать в любом автотранспорте, с использованием любого погрузочно-разгрузочного оборудования. Еще несомненными плюсами являются возможность хранения и транспортировки любых сыпучих материалов, экономия места на площадке, защита от влаги, грязи и повреждения материала.
Наша компания самостоятельно фасует керамзит в биг-беги и доставляет до заказчика по все Москве и Московской области.
Удельный вес керамзитобетона и вес 1 м3
Хозяева, планирующие возводить свой дом самостоятельно, должны знать все тонкости и основные параметры материала, с которым предстоит работать. Керамзитобетон является отличным выбором, особенно если покупать готовые блоки.
Когда вы уже определились с основным материалом стен, следует рассчитать его необходимое количество, а также вес. Эти данные используются для подбора фундамента и определения общей стоимости будущего строения.
Поэтому точно нужно знать сколько весит куб этого материала и какой его удельный вес.
Далее мы рассмотрим такие понятия, как:
- Объемный вес, кг/м3;
- Удельный вес, Н/м3;
Керамзитобетон ценится в строительстве за свою надежность и низкую стоимость. Он относится к легким бетонам. Основой этого материала является цемент с песком или гипс. Заполнителем здесь является керамзит — он имеет небольшой вес и плотность, за счет него эти блоки можно отнести к классу легких бетонов. Используется для частного и промышленного строительства.
Виды керамзитобетона и его назначение
Прежде чем рассматривать, сколько весит куб кермзитобетона и каков его удельный вес, необходимо разобраться в каких целях его можно применять.
Отличается материал по назначению:
- Конструкционный — используется для производства высокопрочных стеновых и дорожных плит.
- Теплоизоляционной — наносится на несущие стены с внутренней или внешний стороны для повышения теплоизоляционных характеристик и производства блоков используемых в малоэтажном строительстве.
- Конструкционно-теплоизоляционный — отличается от стандартного теплоизоляционного тем, что закладывается при возведении несущих конструкций.
Объемный вес или габаритный размер блоков
Под этим понятием подразумевается вес блоков, которые занимают определенный объем, например один кубический метр. В зависимости от плотности бетона, блоки имеют разный вес, поэтому один куб теплоизоляционного бетона значительно легче конструкционного. Блоки, которые используются для теплоизоляции, имеют наименьший объемный вес — он варьируется в диапазоне от 500 до 900 кг/м3. От этого типа не требуется высокой надежности и прочности, при этом он не создают излишнюю нагрузку на несущие стены и перегородки.
Что касается конструкционного типа, то его куб весит от 1400 до 1900 кг/м3. Показатели конструкционно-теплоизоляционного керамзитобетона должен варьироваться от 900 и до 1400 кг/м3. Обычно в промышленном строительстве выбирают блоки с оптимальным весом, который не будет делать конструкцию чересчур тяжелой, но при этом обеспечит достаточную прочность. К примеру, в панельных домах сегодня чаще всего используют 800 кг/м3.
Отдельно стоит рассмотреть конструкционный вид. Он обладает наиболее высокой прочностью, если сравнивать с другими видами, при этом его объемная масса достаточно низкая. Это связано с тем, что в строительстве этот вид применяют для облегчения несущей конструкции. Также стоит сказать и про прочность на сжатие, которая составляет от 200 до 400 кг/см2. При необходимости конструкционный керамзитобетон армируют, для этого используется как обычная арматура, так и напряженная. Второй тип можно применять с маркой М200 или выше. В некоторых ситуациях требуется повысить показатели упругости и прочности — для этого используют кварцевый песок, который добавляется при изготовлении раствора.
При выборе подходящего материала для возведения дома рекомендуется выполнить более прочные марки, так как частные дома обычно строятся на 2–3 этажа. В любом случае, оптимальной маркой будет 900–1200 кг/м3.
Удельный вес
Мы разобрали, сколько весит куб теплоизоляционного и строительного керамзитобетона. Удельный вес — отношение объема твердых частиц к их массе, очень часто этот параметр путают с плотностью. Расчет проводится при сухом состоянии материала. Есть ряд факторов, которые существенно влияют на удельную массу, наиболее важный из которых — это размер зерен.
В промышленном строительстве существует три фракции этого наполнителя:
- Песок — размер его фракций составляет 0–5 мм.
- Гравий — разделяется на 3 вида: 5–10, 10–20, 20–40 мм.
- Дробленая фракция — ее размер составляет 5–40 или 0–10 мм.
Почему же мы рассматриваем удельный и объемный вес? Дело в том, что от выбора фракции будет зависеть, сколько вест куб этого материала. По государственному стандарту 9757-90 выставляется марка, соответствующая плотности. К примеру, марка M250 имеет объемный вес 250 кг/м3.
Также будет полезно знать формулу, с помощью которой можно получить максимальную массу керамзитобетона:
gбс=Vк*gк+Vм*gм+1,15Ц
Где:
- gбс — max возможный объемный вес сухого керамзитобетона, кг/м3;
- gк и gм — объемный вес крупного и мелкого заполнителя, кг/м3;
- Vк и Vм — расход крупного и мелкого заполнителя на 1 м3 раствора, м3;
- Ц — расход вяжущего на 1 м3 замешенного керамзитобетона, кг.
Чтобы вычислить массу керамзитобетона, необходимо брать в расчет массу материалов, которые используются при создании раствора, форму и размер. Для примера можно взять стандартные блоки 200х200х400 мм, они могут быть от 6 до 30 кг. Их объемная масса будет около 300 кг на куб.
, удельный вес, теплопроводность. Общие свойства материала, его структура и виды
Подробно Создано 27 апреля 2012 г. 23:51 Обновлено 21 мая 2012 г. 04:25 автором
Керамзитовый гравий, щебень и песок — это искусственные пористые материалы с ячеистой структурой с преобладающим содержанием закрытых пор, получаемых путем набухания глинистые породы при ускоренном обжиге.
Керамзитовый щебень получают путем измельчения крупных кусков керамзитовой массы.Керамзитовый песок получают путем набухания мелко измельченного глиняного материала с отсеиванием мелких фракций, полученных измельчением более крупных кусков вспученной массы.
Наиболее рациональный вид керамзита — керамзитовый гравий и песок, получаемый набуханием глинистой массы и имеющий форму, приближающуюся к сферической. Характерной особенностью керамзитового гравия является его относительно высокая прочность при невысокой насыпной плотности. Это дает возможность получать легкий бетон и изделия из него с высоким коэффициентом конструктивного качества на основе керамзита
К.К. б = (Р комп / у об) = (450/1800) = 0,25
против 0,18 при такой же прочности для обычного бетона. Керамзит в России производится в основном в виде керамзитового гравия по ГОСТ 9759-65. В зависимости от крупности щебень подразделяется на следующие фракции: мелкий — 5-10, средний — 10-20 и крупный — 20-40 мм. Керамзитовый песок также подразделяется на фракции: до 1,2 мм — мелкие, 1,2-5 мм — крупные.
Зерновой состав каждой фракции гравия или смеси нескольких фракций должен иметь гранулы меньше нижнего предела, не более 10%, или больше, чем верхний предел этой фракции, не более 8%.Зерна в 2 раза крупнее самого большого размера этой фракции быть не должно вообще.
Насыпная плотность 1 м 3 керамзита по фракциям (мм) принимается для расчетов в следующих количествах (кг):
Фракции керамзитобетона — объемная масса
Керамзит несортированный
В зависимости от насыпной плотности (кг / м 3) керамзит подразделяется на особо легкий (до 300), легкий (300-500), средний (500-700) и тяжелый (более 700).
Коэффициент теплопроводности (ккал / м · ч · град) для керамзита этих категорий соответственно равен: 0,03-0,07, 0,07-0,12, 0,12-0,15 и 0,15-0,3. Для расчетной максимальной объемной плотности керамзита в смеси, предназначенной для конструкционного керамзитобетона, масса принимается равной 1000 кг / м 3.
Прочность такого керамзитового гравия при испытании в В зависимости от насыпной плотности этой фракции керамзит подразделяется на марки, и для каждой марки устанавливается минимальная прочность на разрыв (см. Таблицу ниже), средняя марка керамзита составляет 500 , а средняя прочность на сжатие в стандартном цилиндре — 26.3 кг / см 2.
В зависимости от насыпной плотности (кг / м 3) керамзит подразделяется на особо легкий (до 300), легкий (300-500), средний (500-700) и тяжелый (более 700). Коэффициент теплопроводности (ккал / м · ч · град) для керамзита этих категорий соответственно равен: 0,03-0,07, 0,07-0,12, 0,12-0,15 и 0,15-0,3.
За расчетную максимальную насыпную плотность керамзита в смеси, предназначенной для конструкционного керамзитобетона, масса принимается равной 1000 кг / м 3. Прочность такого керамзитового гравия при испытании в стандартном баллоне может составлять от 50 до 100 кг / см 2.
Сорта керамзитового песка также зависят от насыпной плотности. Объемный вес керамзита в куске может варьироваться от 150 до 1300 кг / м 3.
Керамзит должен выдерживать не менее 15 циклов попеременного замораживания и оттаивания с потерей веса не более 8%; имеют сферическую форму — средний коэффициент формы зерна не более 1.2-1,5, а количество зерен с коэффициентом формы 2,5 не должно превышать 20%; имеют мелкопористую ячеистую структуру в трещине; не должен содержать иловых включений, а серной кислоты и соединений серы в пересчете на SO 3 в керамзитовом гравии — не более 1%; иметь влажность не более 2%. Содержание колотых зерен в гравии не должно превышать 15% по весу.
Потеря массы щебня при кипячении не должна превышать 5%. Водопоглощение гравия (по весу) за 1 час (по ГОСТ 9758-61) должно быть не более: 25% для гравия марок до 400, 20% для марок от 450 до 600, 15% для марок 700 и 800. Размер пор в зернах керамзита обычно (98%) менее 1 мм, а общая пористость зерна достигает 70%. Поры преимущественно закрытые и равномерно распределены по сечению зерен.
Керамзит, помимо того, что он обладает достаточной прочностью и атмосферостойкостью, имеет хорошую адгезию к связующему и не содержит вредных примесей для связующего и арматуры, часто готовится из местного сырья. Эти преимущества керамзита предопределили его быстрое внедрение в строительство и развитие производства в ряде стран Европы и Америки.
В США, например, где производство керамзита впервые началось в 1918 году, к 1959 году его производили в количестве 4 млн м 3 в год, а в Советском Союзе темпы роста производства керамзита было даже выше. В 1970 г. на 110 предприятиях страны разной мощности было произведено около 16-17 млн. М 3. Предполагалось, что к 1975 г. потребность в керамзите увеличится до 37 млн. М 3. К 1975 г. планировалось поставить. введены в эксплуатацию предприятия по производству керамзитового щебня в объеме 22 млн м 3.
Капитальные вложения в создание мощностей по производству керамзитового гравия окупаются примерно за три года. В советский период в России доля керамзита в общем объеме произведенных искусственных пористых заполнителей составляла 85,3%.
Керамзит применяется как заполнитель для изготовления несущих строительных конструкций из бетона и железобетона (63,5%), для засыпки теплоизоляции (25,8%) и других целей (10.7%).
Характеристики керамзита по ГОСТ.
ГОСТ 9757-90 предусматривает следующие фракции керамзитового щебня по крупности: 5-10, 10-20 и 20-40 мм. и керамзитовый песок фр. 0-5. В каждой фракции допускается до 5% более мелких и до 5% более крупных зерен по сравнению с номинальными размерами. Из-за низкой эффективности просеивания материала на барабанных грохотах трудно добиться разделения керамзита на фракции в пределах установленных допусков.
По насыпной плотности керамзитовый гравий делится на 10 марок: от 250 до 800, к марке 250 относится керамзитовый гравий с насыпной плотностью до 250 кг / м3, к марке 300 — до 300 кг. / м3 и др. Насыпная плотность определяется по долям в мерных сосудах.
Чем больше фракция керамзитового гравия, тем, как правило, меньше насыпная плотность, так как более крупные фракции содержат больше всего вспученных гранул.
Для каждой марки по объемной плотности стандарт устанавливает требования к прочности керамзитового гравия при прессовании в цилиндре и соответствующие марки по прочности (таблица).Маркировка прочности позволяет сразу обозначить область рационального использования того или иного керамзита в бетоне соответствующих марок. Более точные данные получаются при испытании заполнителя в бетоне.
СОРТА НАСОСА ПЛОТНОСТЬ | ВЫСШАЯ КАТЕГОРИЯ КАЧЕСТВО | ПЕРВАЯ КАТЕГОРИЯ КАЧЕСТВО | ||
---|---|---|---|---|
Марка по прочности | Предел прочности при сжатии в цилиндре, МПа, не менее | Марка по прочности | Предел прочности при сжатии в цилиндре, МПа, не менее | |
250 | P35 | 0,8 | П25 | 0,6 |
300 | P50 | 1 | P35 | 0,8 |
350 | П75 | 1,5 | P50 | 1 |
400 | П75 | 1,8 | P50 | 1,2 |
450 | П100 | 2,1 | П75 | 1,5 |
500 | П125 | 2,5 | П75 | 1,8 |
550 | П150 | 3,3 | П100 | 2,1 |
600 | П150 | 3,5 | П125 | 2,5 |
700 | П200 | 4,5 | П150 | 3,3 |
800 | P250 | 5,5 | П200 | 4,5 |
Характеристики керамзита — прочность пористого заполнителя
Прочность пористого заполнителя является важным показателем его качества. Стандартизован только один метод определения прочности пористых заполнителей вне бетона — выдавливание зерен в цилиндре стальным штампом на заданную глубину. За условную прочность наполнителя принимается фиксированное значение напряжения. Этот метод имеет принципиальные недостатки, главный из которых — зависимость показателя прочности от формы зерен и пустотности смеси. Это настолько искажает фактическую прочность агрегата, что делает невозможным сравнение различных пористых агрегатов и даже агрегатов одного и того же типа, но с разных заводов.Метод определения прочности керамзитового гравия основан на испытании на одноосное сжатие на прессе отдельных гранул керамзита. Предварительно гранулу растирают с двух сторон для получения параллельных опорных плоскостей. При этом имеет форму ствола высотой 0,6-0,7 диаметра.
Чем больше количество испытанных таблеток, тем точнее будет средняя прочностная характеристика. Для получения более-менее достоверной характеристики средней прочности керамзита достаточно десятка гранул.

Испытание керамзитового гравия в баллоне дает лишь условную относительную характеристику его прочности, и она сильно занижена. Установлено, что фактическая прочность керамзита, определенная при испытаниях в бетоне, в 4-5 раз превышает нормативную характеристику. К такому же выводу на основании экспериментальных данных пришли В.Г. Довжик, В.А. Дорф, М.З. Вайнштейн и другие исследователи.
Стандартный метод заключается в засыпке керамзитового гравия в цилиндр, а затем его выдавливании для уменьшения первоначального объема на 20%.Под действием нагрузки, в первую очередь, происходит уплотнение гравия за счет некоторого смещения зерен и их более плотной упаковки. Исходя из экспериментальных данных, можно предположить, что за счет более плотной укладки керамзитового гравия достигается уменьшение объема свободной засыпки в среднем на 7%. Следовательно, оставшиеся 13% уменьшения объема приходятся на дробление зерен (рис. 1). Если исходная высота зерна D, то после измельчения она уменьшается на 13%.
Рисунок: 1. Схема выдавливания зерен керамзита при испытаниях
Рис. 2. Укладка зерен керамзита
, обладающего высокой прочностью, как правило, характеризуется относительно меньшими по размеру, закрытыми и равномерно распределенными порами. .
Он содержит достаточно стекла, чтобы связывать частицы в плотный и прочный материал, который образует стенки пор. При распиливании гранул края сохраняются, корочка хорошо видна. Поверхность реза из-за небольшого размера материала
Водопоглощение заполнителя выражается в процентах от веса сухого материала.Этот показатель для некоторых типов пористых заполнителей стандартизован (например, в ГОСТ 9757-90). Однако более наглядное представление структурных особенностей агрегатов дает показатель объемного водопоглощения.
Поверхностные расплавленные корки на зернах керамзита в начальный период (даже при более низкой объемной плотности зерна и более высокой пористости) имеют почти в два раза меньшее объемное водопоглощение, чем зерна гравия.
Следовательно, необходима технология гравийных агрегатов с поверхностной расплавленной коркой из перлитного сырья, шлаков и других побочных продуктов промышленности (золы ТЭС, отходы углеобогащения).
Поверхностная корка керамзита на первых порах способна задерживать проникновение воды вглубь зерна (это время сопоставимо со временем от изготовления легкой бетонной смеси до ее укладки). Наполнители, лишенные корки, сразу впитывают воду, и в дальнейшем ее количество мало меняется.
В некоторых случаях существует тесная корреляция между водопоглощением и прочностью зерна. Чем выше водопоглощение, тем ниже прочность пористых заполнителей.Это свидетельствует о дефектности конструкции материала. Например, для керамзитового гравия коэффициент корреляции равен 0,46. Эта связь проявляется более четко, чем зависимость прочности от насыпной плотности керамзита (коэффициент корреляции 0,29).
Для уменьшения водопоглощения делаются попытки предварительной гидрофобизации пористых заполнителей. Пока они не привели к существенным положительным результатам из-за невозможности получения не расслаивающейся бетонной смеси при сохранении эффекта гидрофобизации.
Характеристика керамзита — деформационные свойства.
Особенности деформативных свойств предопределены пористой структурой агрегатов. В первую очередь это относится к модулю упругости, который значительно ниже, чем у плотных заполнителей. Собственные деформации (усадка, набухание) искусственных пористых агрегатов, как правило, небольшие. Они на порядок ниже деформации цементного камня. При изучении деформаций керамзита все образцы при насыщении водой дают набухание, а при высыхании дают усадку, но величина деформаций разная.После первого цикла половина образцов показывает остаточное расширение, после второго — три четверти, что свидетельствует об изменении структуры керамзита. Среднее значение усадки после первого цикла составляет 0,14 мм / м, после второго — 0,15 мм / м. Учитывая, что гравий в бетоне менее насыщен и высушен, реальные деформации керамзита в бетоне составляют лишь часть этих значений. Пористые заполнители оказывают сдерживающее влияние на деформацию усадки (и ползучести) цементного камня в бетоне, в результате чего легкий бетон имеет меньшую деформируемость, чем цементный камень.
Другими важными свойствами пористых заполнителей, влияющими на качество легкого бетона, являются морозостойкость и устойчивость к гниению (силикатным и железным), а также содержание водорастворимых серы и соединений серной кислоты. Эти показатели регламентированы стандартами.
Морозостойкость (F, циклы) — ГОСТ нормирует, что этот показатель должен быть не менее 15 (F15), а потеря веса керамзитового гравия в% не должна превышать 8%. — Как правило, такую ставку производители поддерживают.
Искусственные пористые заполнители обычно морозостойки в пределах нормативных требований. Недостаточная морозостойкость некоторых видов заполнителей вне бетона не всегда свидетельствует о том, что легкий бетон на их основе также морозостойкий, особенно если речь идет о необходимом количестве циклов 25-35. Заполнители для легкого бетона, предназначенные для тяжелых условий эксплуатации, не всегда соответствуют требованиям по морозостойкости и поэтому требуют тщательного исследования.
Характеристика керамзита — теплопроводность.
На теплопроводность пористых агрегатов, как и других пористых тел, влияют количество и качество (размер) воздушных пор, а также влажность. Заметное влияние оказывает фазовый состав материала. Аномалия коэффициента теплопроводности связана с наличием стекловидной фазы. Чем больше стекло, тем меньше коэффициент теплопроводности у наполнителя такой же плотности.Для стимулирования выделения заполнителей с лучшими теплоизоляционными свойствами для бетона ограждающих конструкций предлагается нормировать содержание шлакового стекла (например, для качественной пемзы шлакового типа 60-80%).
В зависимости от технологии изготовления и свойств сырья показатель теплопроводности может быть разным у разных производителей, но в среднем он составляет 0,07 — 0,16 Вт / м oС, где соответственно меньшее значение соответствует плотности М250. оценка.(Здесь следует отметить, что марка М250 встречается редко и часто делается на заказ. Обычная плотность материала М350 — М600 соответственно, то К 0,1-0,14).
Искусственные пористые пески — это в основном продукты измельчения пористых кусковых материалов (шлакопемза, аглопорит) и гранул (керамзит). Специально изготовленный керамзит (перлит, керамзит) пока не занимает доминирующего положения.
Большим преимуществом песчаного щебня является возможность их производства в сочетании с производством щебня.Однако это обстоятельство также приводит к существенным недостаткам качества песка. Являясь побочным продуктом при измельчении материала в щебень, песок в некоторых случаях не соответствует требуемому гранулометрическому составу для производства легкого бетона. Очень часто песок слишком крупный, не содержит в достаточном количестве фракции размером менее 0,6 мм, наиболее ценной для обеспечения сцепления и подвижности бетонной смеси.
Насыпная плотность пористых песков в еще меньшей степени, чем крупных заполнителей, характеризует их истинную «легкость». Низкая насыпная плотность песка часто достигается за счет межкристаллитной, а не внутрикристаллитной пористости из-за особого гранулометрического состава (преобладание зерен одного размера).
При добавлении в бетонную смесь такой песок не осветляет бетон, а только увеличивает его водопотребность.
Очевидно, что для улучшения качества пористого песка требуется особое технологическое переделание измельчения материала в песок заданной гранулометрии, а не сопутствующее производство песка при измельчении в щебень.
Производство керамзитового песка, особенно с преобладанием в нем крупных фракций, нельзя считать рациональным. Крупные фракции (1,2-5 мм) измельченного песка незначительно улучшают удобоукладываемость смеси, но вызывают увеличение ее насыпной плотности за счет наличия открытых пор и повышенной пустотности. Керамзитовый песок (в печах с псевдоожиженным слоем) по-прежнему производится в небольших количествах. По физико-техническим показателям он лучше, чем щебень. Во-первых, его водопоглощение меньше.
Характеристики пенопластов и дробленых песков по фракциям:
Фракция 1,2-5 мм 50%. Поэтому в легком бетоне необходимо снизить расход керамзитового щебня, что нерационально (замена щебня на песок).
С уменьшением насыпной плотности пористых заполнителей (насыпных и зернистых) их пористость и водопоглощение увеличиваются. Однако водопоглощение, относящееся к пористости зерна, уменьшается, что указывает на увеличение «закрытой» пористости в более легких материалах.
Радиационное качество, Аэфф., (Бк / кг) — для керамзита этот показатель находится на уровне 200-240, что не превышает 370 Бк / кг, соответственно, ограничений по сфере его применения нет.
Вес одного куба этого материала зависит от показателей его насыпной плотности и фракции гранул. Отношение веса керамзита к его объему определяет марку керамзита. Самая распространенная марка керамзита М450 имеет вес от 400 до 450 кг на кубический метр.Наименьший вес у марки М250, вес одного куба составит 200-250 кг.
Вес керамзита на кубический метр (насыпная плотность) — очень важный показатель. Он отвечает за допустимую нагрузку на основание, характеризует прочность производимого бетона, определяет уровень звукоизоляции, влияет на теплоизоляционные свойства материала. Для каждой марки керамзита насыпная плотность определяется простым способом: емкость, объем которой известен, предварительно взвешивают пустой, затем заполняют керамзитом.Разница в весе (вес нетто) делится на объем контейнера, чтобы получить значение кг / м3.
Вес куба керамзита в зависимости от марки
В его маркировке фиксируются данные о весе керамзита. При массе менее 250 кг / м3 — марка керамзита М250, вес 600-700 кг / м3 — марка М700 и так далее. Самый тяжелый керамзит — М1000, его вес составит около одной тонны на 1 кубический метр. Керамзит марок свыше М600 изготавливается по индивидуальным производственным заказам, на постоянной основе выпускаются только марки М250-М600.
Соотношение марки керамзита и его веса представлено в таблице. Из него можно сделать вывод, что вес керамзита примерно совпадает с его маркой.
Масса керамзита различных фракций
Вес 1 м3 зависит от фракции: чем меньше размер (фракция) гранул, тем больше вес материала в 1 м3.
Правильный подбор фракции снижает расход цемента, показатели фракции учитываются в области работ (стяжка, стены, перегородки и т. Д.).
Если марка керамзита не идентифицирована, то примерный вес материала можно определить исходя из размера гранул.
Песок (менее 5 мм) — 500 кг и более Мелкий (5-10 мм) — 400-500 кг Средний (10-20 мм) — 350-400 кг Крупный (20-40 мм) — 250-350 кг
Керамзит марки | Масса керамзита в 1 м3 |
---|---|
M250 | ≤ 250 кг |
M300 | 250-300 кг |
M350 | 300-350 кг |
M400 | 350-400 кг |
M450 | 400-450 кг |
M500 | 450-500 кг |
M600 | 500-600 кг |
M700 | 600-700 кг |
M800 | 700-800 кг |
Какой удельный вес керамзита фракции 5-10 (фр 5-10 мм) в килограммах? Масса следующих видов насыпных материалов: керамзитовый камень, песок, керамзитовый утеплитель, керамзитовый щебень, керамзитовый заполнитель, гравий, керамзитовая галька, теплоизоляция, керамзитовая засыпка, щебень, керамзитовый утеплитель, дренаж, керамзит.![]() ![]() |
Удельный вес керамзита фракции 5-10 (фр. 5-10 мм) зависит от марки по насыпной плотности, марки по прочности и влажности сыпучего материала. Удельный вес керамзита фракции 5-10 в 1 кубометре, 1 кубометре, 1 кубометре, 1 м3 — насыпная или насыпная плотность. Одной из важных характеристик насыпного материала (гравия, песка, щебня, гальки, крошки, щебня) является насыпная плотность , которая определяет удельный вес керамзита фракции 5-10 в 1 м3 … Обычно для практических целей и для строительных работ он измеряется в таких единицах, как кг / м3 или т / м3. Удельный вес керамзита равен весу куба керамзита.Масса 1м3 керамзита и его плотностьг. Намного реже его нужно распознавать в таких единицах, как г / см3. Оказывается, что ГОСТ 9757-90 четко не регламентирует насыпную плотность по фракциям керамзитовых материалов , а требует ее соблюдения только для марок насыпной плотности керамзита.Нас это не совсем устраивает. Почему? Казалось бы, мы смотрим на маркировку на таре (пакете), если материал расфасован или узнаем марку по паспорту, сертификату и можем узнать точный удельный вес керамзита фракции 5-10. Теоретически это так, но на практике есть одна тонкость. Дело в том, что марка керамзитового материала дает нам достаточно точные характеристики объемной массы 1 куба для мелкой фракции, например: песок, крошка, крошка.А для средних и крупных фракций нужна дополнительная настройка. Чем крупнее фракция керамзита, тем легче насыпной материал, так как в объеме вместе с ним находится большее количество воздуха, что снижает массу 1 куба, при объемной плотности данной марки заявленной по ГОСТ 9757 -90. Узнать точный удельный вес керамзита фракции 5-10 для конкретной партии материала можно только путем контрольного взвешивания.Справочные данные дают нам лишь допустимый диапазон массы керамзита в объеме 1 м3 для каждой марки. В практике строителей и продавцов сыпучих керамзитовых материалов (утеплитель, смеси, дренаж, засыпка, щебень, галька, камень, подстилка, теплоизоляция, песок, крошка, утеплитель, гравий и щебень) часто используют средний удельный вес керамзит фракцией 5-10 мм. См. Таблицу 1 … Это удобно, в большинстве случаев вполне оправдано и дает более-менее реальное представление о массе объема материала.Однако, если вам нужны точные данные в килограммах для конкретной марки, вам придется взглянуть на большую таблицу, выписку из ГОСТ 9757-90. См. Таблицу 2: удельный вес керамзита фракции 5-10. Керамзит массой 5-10 и керамзит влажностью. Как и любой другой сыпучий материал, керамзит фракции 5-10 мм существенно меняет свою плотность в зависимости от влажности. Керамзит массой 5-10 и прочностью керамзита. Вес керамзита фракции 5-10 по ГОСТ 9757-90 не имеет прямого отношения к его прочности. Нет прямой аналогии между классами прочности и классами насыпной плотности по ГОСТу. Однако приблизительное совпадение найти можно. Но это настолько условно, что вес керамзита 5-10 лучше не определять только по классу прочности — это плохая практика. Какие марки керамзита фракции 5-10 крепостью можно найти в продаже? Обычно это: P 25, P 35, P 50, P 75 и P 100. Таблица 1. СРЕДНЯЯ СТОИМОСТЬ, ОБЫЧНО УКАЗАННАЯ В СПРАВОЧНОЙ ЛИТЕРАТУРЕ, ДАЕТ НАМ ПРИБЛИЗИТЕЛЬНУЮ ОЦЕНКУ ДЛЯ НАИБОЛЕЕ ПОПУЛЯРНЫХ БРЕНДОВ. Сколько составляет средний удельный вес керамзита фракции 5-10 в кг / м3 — объемный вес 1 м3 для керамзитового песка, гальки, щебня, щебня, утеплителя, смеси, засыпки, дренажа, крошки, утеплителя, теплоизоляции утеплитель, засыпка, камень, щебень. | ||
Что бьет. вес или какова насыпная плотность в г / см3 | Количество кубиков в тонне керамзита. |

Таблица 2. Сколько составляет удельный вес керамзита фракции 5-10 мм, точная масса материала в 1 кубе, насыпная плотность и насыпная плотность 1 м3, таблица составляется с учетом марки утеплителя. по плотности. Следующие классы насыпной плотности керамзита и крошки (песок, гравий, щебень) представлены как: M 250, M 300, M 350, M 400, M 450. Для каждой марки насыпной плотности указываются удельный вес и указывается масса некоторых объемов в килограммах.
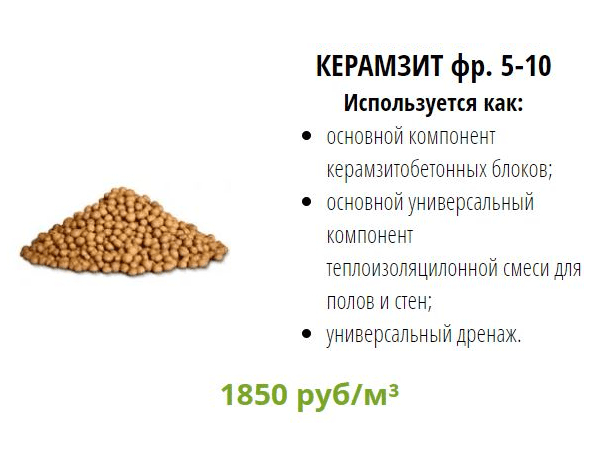
Керамзитовый гравий фракции 5-10 часто называют мелким керамзитовым гравием (керамический гравий, керамический гравий, легкий гравий), учитывая мелкий гравий фракции 5-10 мм.Судя по внешнему виду на фото, это довольно крупные зерна, гранулы, частицы округлой формы с оплавленной поверхностью и порами внутри, диаметром 5-10 мм. Округлый, сглаженный, без краев и острых углов по форме гравий напоминает натуральную гальку или натуральный камешек. С чем связано другое название (не ГОСТ, бытовой) керамзит — керамзитовая галька фракции 5-10. Таким образом, керамзитовая галька — это не отдельный особый вид камней, а просто обиходное или торговое название керамического гравия.
Керамзит фракции 5-10 на производственных предприятиях, на заводах по его производству изготавливается преимущественно в виде керамзитового гравия. Это самый распространенный в продаже материал. Большинство людей так думают об этом внешне, почти на всех фотографиях керамзита, опубликованных в Интернете, мы видим только гравий. Его зерна имеют округлую форму, поэтому их часто называют пеллетами, хотя с технологической точки зрения это не правильно, но очень похоже на фото керамзита.Структура керамзитового гравия 5-10 пористая, шероховатая, не совсем гладкая и воспринимается рукой как мелкоячеистая. На поверхности керамогранита 5-10 образуется более плотная корка, внутренняя часть напоминает пемзу. «Натуральный» цвет керамзитового гравия 5-10, изготовленного из глины, без нарушения технологии производства, обычно темно-коричневый, больше похож на коричневый.
Интересно, что цвет керамзитового гравия 5-10 меняется в трещине. Если поверхность керамзита коричневая, то внутри, на изломе, цвет более темный, без красноватого оттенка, почти черный или черновато-серый.Технология производства. Керамзитовый гравий фракции 5-10 производится на заводе и получается набуханием при обжиге легкоплавких глин во вращающихся печах. По свойствам и физическим характеристикам керамзитовый щебень с крупностью 5-10 мм морозоустойчив, имеет низкую теплопроводность и высокие теплоизоляционные качества, огнестойкий, не впитывает воду (низкое водопоглощение) и не содержит вредных для цемента примесей.
Керамзитовая галька и керамзитовый щебень фракции 5-10 используются в качестве утеплителя, теплоизолятора, изолятора, засыпки, засыпки, утеплителя, гипсового наполнителя, заполнителя при производстве легкого бетона (монолитных легких бетонных конструкций на основе цемента).
Керамзитовый щебень фракции 5-10 — это мелкий щебень. Название керамзитовый щебень основан на его характерной форме, с углами, краями, трещинами, пластинами, напоминающими натуральный камень — природный щебень, полученный путем дробления горных пород (гранит, мрамор, известняк). По цвету и характеристикам керамзитовый щебень фракции 5-10 мм не отличается от керамзитового гравия, но его форма визуально выглядит не так хорошо и не ассоциируется с натуральной галькой.Поэтому керамзитовый щебень фракции 5-10 не используется в декоративных целях, например: для засыпки дорожек, в ландшафтном дизайне. Основное применение керамзитового щебня фракции 5-10 связано с применением утеплителя в качестве засыпки под будущую стяжку. И конечно же керамзитовый щебень 5-10 также является наполнителем для легкого бетона. Его использование позволяет изготавливать легкие и «теплые» бетонные конструкции на основе цемента монолитным способом любой произвольной формы.Вес керамзита фракции 5-10 мм указан в таблице 1 и таблице 2.
Керамзит — один из самых востребованных строительных материалов, так как его используют не только для изготовления бетона, но и для теплоизоляции помещений. Основная проблема, с которой сталкиваются строители, — это правильное определение количества материала, которое понадобится для их целей.
Керамзит — это мелкие гранулы, обладающие высокой пористостью, что определяет его легкий вес. Керамзит изготавливается методом обжига глины.
В связи с тем, что керамзит очень легкий, его масса чаще всего указывается в кубах и литрах. Но иногда необходимо узнать, каков вес 1 куба керамзита в килограммах. Для этого необходимо учитывать определенные факторы, которые могут повлиять на вес керамзита.
Узнать цены на керамзит
Как рассчитать вес 1 куба керамзита
В среднем в 1 кубе керамзита содержится около 200-400 кг материала.Однако это значение не всегда верно, так как керамзит может быть крупнее / мельче, отличаться по плотности. Существуют различные таблицы, в которых дана уже рассчитанная масса керамзита разных марок и фракций, но даже они не всегда дают актуальную информацию. Самый простой способ узнать вес 1 куба керамзита — обратиться к продавцу, у которого есть все необходимые документы и который знает, какие условия хранения у его материала.
Однако недобросовестные продавцы могут обмануть покупателей и указать завышенные цифры.Поэтому не лишним будет знать, как самостоятельно рассчитать вес одного кубометра керамзита. Первое, что определяет вес керамзита, — это размер его зерна.
Сколько весит куб керамзита?
В зависимости от крупности фракции изменяется вес керамзита: с увеличением крупности вес уменьшается, а с уменьшением фракции — увеличивается. Всего ГОСТ выделяет три существующих вида керамзита: мелкий (5-10), средний (10-20) и крупный (10-20).
Немаловажное значение имеет плотность керамзита. Он зависит от его веса и выражается в отметке плотности (M), значение которой лежит в пределах 250-1200. Если значение плотности М450, то вес 1 куба керамзита будет 410-450 кг.
Масса керамзита в мешках
Для ремонта в доме или квартире часто не требуется большое количество керамзита. В этом случае вы можете сэкономить на покупке и доставке, купив керамзит в мешках, вес которых указан в литрах.
В этом случае многое зависит еще и от фракции и плотности вещества, если взять керамзит фракции 5-10 мм, то вес одного мешка составит порядка 23-38 кг.
Все эти расчеты очень приблизительны, чтобы узнать, сколько именно керамзита вам нужно для ваших нужд, позвоните по указанному на сайте номеру или оставьте заявку. Наши менеджеры свяжутся с вами и рассчитают для вас необходимый объем керамзита. Вы можете купить его у нас по доступным ценам с быстрой доставкой.
Вернуться к списку статей
Удельный вес керамзита 10-20 кг / м3. ГОСТ 9757-90 — насыпная плотность, насыпная плотность 1 куба насыпного материала.
Насыпной или насыпной вес керамзита 10-20 — это удельный вес керамзита (галька, гравий или щебень) с размером (фракцией) гранул от 10 мм до 20 мм. Профессионалы называют плотность в насыпи, навалом. Подразумевает неуплотненное состояние насыпного материала, сыпучий, рыхлый.А еще подразумевается нормальная влажность керамзита 10-20, равная двум процентам по ГОСТ 9757-90. Учтите, что влажность — важная характеристика любого насыпного материала, так как даже небольшое повышение влажности сразу вызовет заметное увеличение насыпной плотности в заливке. Нормальная влажность обеспечивается правильными условиями хранения и транспортировки сыпучих материалов.
Удельный вес керамзита 10-20 определяется маркой керамзитового материала по насыпной или насыпной плотности.Таких марок керамзита 10-20, предусмотренных ГОСТ 9757-90, очень много: М 250, М 300, М 350, М 400, М 450, М 500, М 600, М 700, М 800, М 900, М 1000, М 1100, М 1200. Поэтому вес 1 куба керамзита 10-20 может сильно варьироваться в зависимости от конкретной марки материала. См. Таблицу 1. Однако, если рассматривать не все марки, а только наиболее часто используемые для изготовления керамзитового щебня, гравия или гальки, то «вопрос с объемной массой керамзита 10-20 значительно упрощается. .«
См. Таблицу 3. Есть такое определение как средний удельный вес керамзита 10-20. Medium — не точное название, было бы неплохо заключить его в кавычки. Или замените слово «средний» на «популярный, распространенный, самый распространенный».
Плотность и масса 1 кубометра керамзита
Популярность керамзитового материала 10-20 «средней» плотности, по сути, сводится к области его применения в качестве утеплителя, подстилки, теплоизоляции, засыпки, шпатлевки или дренажной смеси.Другие варианты насыпной плотности керамзитового гравия, щебня или гальки имеют свои преимущества, но более узкое применение и более сложная технология изготовления материала. Поэтому в продаже они встречаются гораздо реже. Возможные варианты насыпной плотности керамзита 10-20 по сортам объемного веса см. В таблице 2. Для «расширения горизонтов» полезно знать, что насыпной вес керамзита 10-20 также зависит от класса прочности керамзита. керамзитовый гравий, щебень или галька.Более прочные марки или марки с высокой прочностью, естественно, также будут иметь более низкую пористость и, следовательно, более высокий удельный вес в 1 куб.
Таблица 1. Удельный вес керамзита 10-20 С УЧЕТОМ БРЕНДА. Насыпная плотность в г / см3. Сколько килограммов в кубе, тонн в 1 кубометре, кг в 1 кубометре, тонн в 1 м3.
Насыпная плотность керамзита 5-10 — это объемная масса керамзита (галька, гравий или щебень) с размером (фракцией) гранул от 5 мм до 10 мм.Давайте разберемся с названиями, чтобы не было путаницы. Такое красивое название, как керамзитовая галька — это не определение ГОСТа, а торговое название обычного искусственного легкого пористого керамического гравия. Керамзитовый гравий часто называют керамзитовой (легкой, керамической) галькой на том основании, что внешне керамзитовый гравий действительно очень похож на гальку из природного камня (морского или речного). Визуально отличается от него только характерным красновато-коричневым цветом поверхности и темно-серым, почти черным цветом излома.Оказалось, что торговое название — керамзитовая галька фракцией 5-10 мм — очень положительно воспринимается покупателями материала, желающими использовать его в декоративных целях. Например: для засыпки дорожек в саду, площадок для ровных участков, полов в беседках и других ландшафтных идей в частном доме, коттедже, загородном доме. Название керамзитовый гравий — ГОСТ, вполне официальное, правильное. Это говорит нам сразу о двух характеристиках искусственного камня. 1), что фракция состоит из довольно крупных камней — это явно не песок.2) форма зерен округлая, как бы прокатанная, без острых углов, краев и сколов. Такой, который содержится в натуральном каменном гравии. Название керамзитового щебня — ГОСТ. Также подразумеваются две характеристики: размер фракции и форма гранул. Щебень отличается более остроугольной, слоистой формой с более выраженными краями и краями, чем гравий. В целом керамзитовый щебень по внешнему виду напоминает щебень из природного камня, хотя и не является таким «битым камнем».Что касается керамзита фракции 5-10, то для гравия и щебня это минимально возможная фракция. Частицы размером менее 5 мм, независимо от их формы, называют песком. Керамзитовый гравий выпускается двух фракций: 5-10 и 10-20.
Реже в виде смеси фракций керамзита с размером гранул от 5 до 20 мм. Керамзитовый щебень 5-10 — мелкая фракция щебня, производится из керамзита в виде трех фракций: 5-10, 10-20 и 20-40.Возможны смеси керамзитового щебня, в том числе разной крупности: от 5 до 40 мм.
Насыпная плотность керамзита 5-10 — определяется маркой керамзитового материала по насыпной или насыпной плотности. Таких марок насыпной плотности для керамзита 5-10, предусмотренных ГОСТ 9757-90, очень много. Поэтому вес 1 куба 5-10 керамзита может сильно варьироваться в зависимости от конкретной марки материала. См. Таблицу 1. Однако, если рассматривать не все марки, а только наиболее часто используемые для изготовления керамзитового щебня, гравия или гальки, то «вопрос с плотностью керамзита 5-10 значительно упрощается.См. Таблицу 3. Есть такое определение, как средняя плотность керамзита 5-10. Это не совсем точное название, неплохо было бы заключить его в кавычки. Или слово «средний» заменить на «популярный». , самая распространенная ». Популярность керамзита 5-10« средней »плотности, по сути, сводится к его области применения в качестве утеплителя, подстилки, теплоизоляции, засыпки, шпатлевки или дренажной смеси. Насыпная плотность керамзитового гравия, щебня или гальки имеет свои преимущества, но более узкое применение и более сложная технология изготовления материала.Поэтому в продаже они встречаются гораздо реже. Возможные варианты насыпной плотности керамзита 5-10 по сортам объемной массы см. Таблицу 2.
Керамзитовый гравий — строительный материал, получаемый из глины путем обжига и представляющий собой фрагменты круглой формы с порами внутри и расплавленной поверхностью.
Документом, регулирующим требования к керамзитному щебню: технические параметры, правила приемки, методы испытаний, транспортировку и хранение, является Межгосударственный стандарт ГОСТ 32496-2013 «Заполнители пористые для легкого бетона.Технические условия ».
Производство керамзитового гравия осуществляется в специальных барабанных печах, где сырье — монтмориллонит и гидрослюдистые глины доводится до определенного структурного состояния, после чего охлаждается.
Производство
Производственный процесс разделен на несколько этапов:
- Подготовка сырья.
- Горение.
- Охлаждение.
Схематично производственный процесс выглядит так:
Требования к сырью, из которого изготавливается керамзитовый гравий, определяются тремя параметрами, это:
- Содержание кварца не более 30%, оксида кремния — не более 70% и минералы — не менее 12%.
- Низкая температура плавления — температура обжига не должна превышать 1250˚С;
- Интервал набухания — должен соответствовать требованиям.
Подготовка сырья может осуществляться по нескольким технологиям. Это сухой препарат — когда глиняная порода измельчается до необходимой крупности с последующим разделением на фракции. Пластическая подготовка — формирование зерен осуществляется замешиванием сырья в специальной машине (смеситель для глины) и лепкой гранул с последующей сушкой.Порошок — пластическая подготовка — процесс осуществляется аналогично приготовлению пластическим методом, с той лишь разницей, что в этом случае исходное сырье превращается в порошок. Мокрая (шликерная) подготовка — глина смешивается с водой в специальных устройствах (глиняных плитах), где получается глиняный раствор, называемый шликером, который подается в печь. По этой технологии печи оснащаются специальными завесами из цепей, которые нагреваются во время работы. Шликер подается на цепи, где разбивается на куски, которые затем обжигаются.
Обжиг происходит в специальных печах различной конструкции:
- Вращающиеся, одно- и двухбарабанные печи — при такой конструкции подготовленное сырье подается в верхнюю часть барабана, который расположен под определенным углом. наземь. В нижней части барабана находится сопло, обеспечивающее обогрев внутреннего пространства устройства. Гранулы глины скатываются по стенкам барабана и проходят термообработку, при которой глина вскипает и набухает, ее верхний слой плавится.
- Кольцо — производство керамзита осуществляется методом термического удара. Готовые гранулы на 25-40% легче, чем при обжиге в барабанах.
- Вертикальный, воздушный — керамзит получают в восходящем потоке горячих газов. При такой конструкции также возникает тепловой удар, который вызывает активное разбухание глины.
Охлаждение происходит в несколько этапов с постепенным снижением температуры: 1-я стадия — по окончании набухания глины — до температуры + 800-900 ° С, 2-я стадия — в течение 20 минут, до температуры +600-700. ° С и 3-я ступень — окончательное охлаждение.
В соответствии с ГОСТ 32496-2013 гравий выпускается трех фракций:
- Мелкая фракция — размер обломков (зерен) от 5,0 до 10,0 мм;
- Средняя фракция — крупность от 10,0 до 20,0 мм;
- Крупная фракция — размер зерна от 20,0 до 40,0 мм.
Основные технические параметры керамзитового гравия:
- Насыпная плотность (насыпная плотность).
Измеряется в кг на м3, выпускается 11 марок — от марок М150 до М800, наиболее востребованными являются М450, М500, М600.
Истинная плотность (насыпная плотность) в 1,5-2 раза больше насыпной плотности.
Прочность материала измеряется в МПа (Н / мм2), выпускается 13 классов прочности — от P15 до P400.
Между сортами керамзита существует связь по плотности и прочности — увеличение плотности приводит к увеличению прочности.
- Коэффициент уплотнения — значение (К = 1,15) используется для учета уплотнения массы материала при транспортировке или хранении.
- Звукоизоляция. Керамзит обладает повышенной звукоизоляцией.
- Морозостойкость.
Керамзит обладает достаточно высокими морозостойкими свойствами. Он характеризуется потерей массы материала, измеряемой в%.
- Самым важным показателем является теплопроводность.
Измеряется в Вт / м * К. Характеризует способность материала сохранять тепло. По мере увеличения плотности увеличивается коэффициент теплопроводности.
Измерено в мм. Определяет количество влаги, которое может впитать керамзит. Керамзит относится к относительно стойким к влаге материалам.
- Количество радионуклидов.
Удельная эффективная активность радионуклидов не должна превышать 370 Бк / кг.
По ГОСТ 32496-2013 марка керамзитового гравия должна быть:
- Прочность в зависимости от марки:
Марка гравия | Прочность, МПа | ||||||||
До 0.5 | 0,5 — 0,7 | 0,7 — 1,0 | 1,0 — 1,5 | 1,5 — 2,0 | 2,0 — 2,5 | 2,5 — 3,3 | 3,3 — 4,5 | 4,5 — 5,5 | |
По прочности | P15 | P25 | P35 | P50 | P75 | P100 | P125 | P150 | P200 |
- Насыпная плотность должна соответствовать марке прочности, а именно:
Марка гравия | |||||||||||
По насыпной плотности | M150 | M200 | M250 | M300 | M350 | M400 | M450 | M500 | M600 | M700 | M800 |
По прочности | P15 | P25 | P25 | P35 | P50 | P50 | P75 | P100 | P125 | P150 | P200 |
Морозостойкость материала также нормируется ГОСТом — потеря веса керамзитового щебня не должна превышать 8%.
Теплопроводность зависит от технологии подготовки и состава сырья, конструкции печи для обжига и условий охлаждения. В зависимости от плотности полученного материала и технологии изготовления удельная теплопроводность колеблется от 0,07 до 0,18 Вт / м * К.
Способность керамзита впитывать влагу (влагопоглощение) также является важным параметром, характеризующим его. строительный материал. Коэффициент влагопоглощения у разных марок колеблется от 8.От 0 до 20,0%. Способность впитывать влагу по отношению к массе материала в течение 1 часа должна быть не более, для марок:
- До М400 — 30%;
- M450 — M600 — 25%;
- M700 — M800 — 20%.
Общая влажность отгружаемой партии материала не должна превышать 5,0% от общей массы щебня.
После изготовления керамзита готовый материал отправляется на продажу в виде россыпи или в определенной упаковке, при этом количество поврежденных (расколотых) зерен не должно превышать 15% от общей массы материала. произведено.
Кроме того, при производстве керамзитового гравия регулируется форма зерен, которая определяется коэффициентом формы. Коэффициент формы должен быть не более 1,5, а количество зерен, превышающих этот показатель, также должно быть не более 15% от общего количества в партии материала.
При реализации наливом и тарой продавающая организация должна иметь сертификаты соответствия, результаты испытаний и накладные на материал. При продаже в таре (фасованной) продукция маркируется на упаковке.В маркировке указываются: наименование наполнителя, данные производителя, дата изготовления, значение теплопроводности, количество наполнителя, результаты испытаний и обозначение стандарта.
Для упаковки используются бумажные, полипропиленовые и тканевые мешки, которые должны соответствовать требованиям ГОСТ к таре данного типа. Маркировка наносится на каждую сумку в соответствии с требованиями к маркировке товаров, указанными выше.
Контроль качества материала осуществляется производителем, при этом контроль осуществляется с момента поступления сырья до окончания производственного процесса (входной, производственный и приемочный контроль), данные о котором имеются. заносятся в специальные журналы и оформляются протоколами.
При проведении приемочных испытаний определяются:
- зерновой состав в каждой партии;
- насыпная плотность;
- силы;
- коэффициент формы зерна;
- содержание дробленых зерен в щебне;
- влажность.
При длительном хранении готового материала проводятся периодические испытания, которые проводятся:
- 1 раз в две недели — проверяется потеря массы при прокаливании и содержание легкобожженных зерен;
- раз в квартал — проверяется потеря веса при кипячении;
- 1 раз в полгода — проверяется морозостойкость и коэффициент размягчения;
- 1 раз в год — проверяется удельная эффективная активность природных радионуклидов и теплопроводность.
В начале производства и при каждой смене сырья проводятся испытания для проверки на наличие радионуклидов и теплопроводности керамзита.
Керамзит, подготовленный к продаже, отгружается, при этом количество материала измеряется по объему или его массе с учетом коэффициента уплотнения (К = 1,15).
Достоинства и недостатки
Преимущества использования:
- Достаточная прочность материала.
- Низкая теплопроводность, а как следствие — хорошие теплоизоляционные свойства.
- Хороший звукоизолятор.
- Высокая огнеупорность, определяет этот материал как негорючий, пожаробезопасный. При воздействии внешнего источника огня не поддерживает горение, не выделяет вредных веществ в окружающее пространство.
- Морозостойкость.
- Низкий удельный вес — позволяет при необходимости использовать для уменьшения массы строящихся строительных конструкций.
- Не подвержен влиянию атмосферных факторов (влажность, перепады температур).
- Инертен к химическому воздействию.
- Не гниет и не разлагается.
- Длительный срок службы.
- Это экологически чистый материал.
- Легкость монтажных работ.
- Низкая стоимость по сравнению с другими теплоизоляционными материалами.
Недостатки:
- При горизонтальной укладке необходимо укладывать подоснову.
- При некачественном изготовлении или изготовлении без образования поверхностной корки впитывает влагу, после чего не может использоваться как теплоизолятор.
- При использовании в качестве обогревателя он занимает большой объем, тем самым уменьшая пространство в изолированном помещении.
Благодаря своим положительным свойствам керамзитовый гравий широко применяется в различных видах строительных работ, таких как:
- монолитное строительство — используется в качестве наполнителя;
- теплоизоляция — крыши, перекрытия и перекрытия зданий, сооружений и сооружений;
- теплоизоляция различных систем — «теплый пол», водопровод, трубы наружного отопления и др. Трубопроводные системы.
- защита от шума внутреннего пространства;
- производство бетона и строительных блоков;
- теплоизоляция фундамента — позволяет уменьшить глубину фундамента;
- дорожное строительство — используется для теплоизоляции и дренажа при строительстве насыпей для дорог и при строительстве на заболоченных территориях.
Керамзит также используется при создании ландшафтного дизайна участка (создание альпийских горок и террас), при необходимости утепления почвы (при выращивании растений) и в растениеводстве — для создания дренажа корневой системы растений.
При выборе керамического гравия необходимо руководствоваться следующими критериями выбора:
- Качество материала.
- Наличие сертификата соответствия.
- Условия хранения готового материала.
- Целостность фрагментов (зерен) материала.
- Цвет и наличие корки на зернах керамзита.
Керамзитовый гравий, благодаря своим положительным свойствам, широко используется в различных отраслях промышленности и народном хозяйстве, как в нашей стране, так и за рубежом.
Легкий наполнитель из вспененной глины — обзор
7.4.4.1 Технические характеристики
При вторичной переработке алюминия образуется шлак и шлак , оба обычно классифицируемые как опасные отходы, могут происходить через керамические изделия. Свойства побочного продукта алюминиевого шлака обсуждаются в главе 6.
Несмотря на его потенциально опасный характер, высокое содержание глинозема является привлекательным аспектом, способствующим его переработке. В основном изучаются две области повторного использования (Yoshimura et al., 2008): (i) огнеупоры и (ii) композиты (алюминиево-глиноземные композиты).
Легкие керамзитовые заполнители были произведены из природной пластичной глины и отходов переработки алюминиевого лома (ASRW), которые были получены в результате извлечения металлического алюминия из черного шлака с использованием обычного металлургического процесса (Bajare et al., 2012). ASRW содержит нитрид алюминия (AlN — в среднем 5 мас.%), Хлорид алюминия (AlCl 3 — в среднем 3 мас.%), Хлориды калия и натрия (всего 5 мас.%) И сульфит железа (FeSO 3 — на в среднем 1 мас.%).Его средний химический состав приведен в таблице 7.25, а элементный анализ — в таблице 7.26.
Таблица 7.25. Средний химический состав отходов переработки алюминиевого лома (мас.%) (Bajare et al., 2012)
LOI, 1000 ° C | Al 2 O 3 | SiO 2 | CaO | SO 3 | TiO 2 | Na 2 O | K 2 O | MgO | Fe 2 O 3 | Прочие 61 71 | 63,19 | 7,92 | 2,57 | 0,36 | 0,53 | 3,84 | 3,81 | 4,43 | 4,54 | & gt; 2,6 |
---|
Таблица 7.26. Элементный анализ отходов переработки алюминиевого лома (мас.%) (Bajare et al., 2012)
Al | Si | Ca | Mg | Fe | Na | K | Cl | S | Cu | Pb | Zn |
---|---|---|---|---|---|---|---|---|---|---|---|
34.4 | 4,4 | 1,32 | 2,44 | 3,60 | 1,69 | 2,31 | 4,23 | 0,07 | 0,99 | 0,14 | 0,6 |
Разложение летучих элементов, присутствующих в нитриде, сульфит и хлориды будут выделять газы при сжигании, а отходы переработки алюминиевого лома могут действовать как порообразователь. Керамические заполнители были изготовлены из смесей углеродистой глины и ASRW в различных пропорциях (ASRW от 9 до 37.5 мас.%). Подготовленные агрегаты сушили 3 ч при 105 ° C, а затем прокаливали 5 мин при различных температурах от 1150 ° C до 1270 ° C. Скорость нагрева поддерживалась постоянной (15 ° C / мин). Затем были оценены физические и микроструктурные свойства спеченных агрегатов.
Кажущаяся плотность агрегатов колебалась от 0,4 до 0,6 г / см 3 . Структура пор показана на рис. 7.7 и состоит из макропор со средним диаметром 1 мм и микропор (размер менее 0,2 мкм).
Фиг.7.7. Пористая структура агрегатов, полученных из смеси глины и отходов переработки молотого и алюминиевого лома (показаны мас.%) И обожженных при различных (заданных) температурах (Bajare et al., 2012).
Согласно Pereira et al. (2000a), солевой шлак, образующийся при плавке вторичного алюминия, можно использовать в огнеупорных кирпичах. Соблюдались типичные условия промышленной обработки. Добавление шлака улучшает физические и механические характеристики керамического материала из-за его флюсования.Допускаются более высокие уровни включения (около 10% масс.). Те же авторы протестировали включение солевого шлака, богатого алюминием, в огнеупоры бокситового типа (Pereira et al., 2000b). Сделан вывод о возможности включения промытых шлаков солей алюминия в бокситовые огнеупоры. В общем, физические свойства обожженного материала имеют тенденцию улучшаться с увеличением содержания шлака (например, более высокой прочности на изгиб). Этот эффект можно объяснить характеристиками флюсования шлака. С функциональной точки зрения допускаются значительные уровни включения (18 мас.%).
Процессы анодирования и порошкового покрытия поверхности требуют больших затрат воды не только для каждой последующей партии химикатов, но и для надлежащей промывки промежуточных деталей. Как прямое следствие, образуется огромное количество сточных вод, и после надлежащей очистки это приводит к чистой воде и большому количеству твердых отходов, называемых алюминиевым шламом (BREF, 2006; Magalhães et al., 2005).
Производство керамического кирпича из глиняного кирпича может стать интересной альтернативой утилизации осадка на суше.Marques et al. (2012) направлена на разработку термостойкого кирпича путем переработки алюминиевого шлама в производстве кирпича. Они использовали производственный цикл кирпичного завода и провели полномасштабные испытания кирпичной кладки, произведя 10 тонн настоящего кирпича. В заключение, добавление анодирующего шлама улучшает тепловые характеристики кирпича на 26% без увеличения стоимости производства кирпича, что приводит к значительному повышению теплового комфорта зданий. Остальные физико-механические свойства (водопоглощение и прочность на сжатие) кирпича по-прежнему имеют приемлемые значения (Marques et al., 2012).
Цель Khezri et al. (2010) заключалась в том, чтобы найти применение для использования осадка на установках анодирования алюминия для предотвращения загрязнения окружающей среды и получения экономической выгоды для заводов. Для этого были изготовлены кирпичи с различным сочетанием шлама, глины и песка, которые были испытаны в соответствии с имеющимися стандартами. Результат показал, что кирпичи, содержащие 40 мас.% Шлама, обладают лучшими и ближайшими стандартизованными параметрами качества обычных внутренних кирпичей. Эти кирпичи имеют меньший вес, чем кирпичи при такой же массе и более низкой цене, а также предотвращают распространение осадка в окружающей среде.
Ozturk (2014) изучил использование шлама анодирования, который производится в больших объемах на одной из алюминиевых компаний в Турции (Таблица 7.27). Целью исследования было производство муллитовой керамики из богатого алюминием шлама, содержащего 15–30 мас.% Твердого вещества (90 мас.% Твердого вещества составляет бемит (AlOOH), а остальное — тенардит (Na 2 SO 4). ) и барит (BaSO 4 )).
Таблица 7.27. Химический состав богатого алюминием анодирующего шлама (мас.%, XRF) (Ozturk, 2014)
Алюминиевый шлам | Al 2 O 3 | SiO 2 | Fe 2 O 3 | CaO | SO 3 | Na 2 O | K 2 O | MgO | BaO |
---|---|---|---|---|---|---|---|---|---|
70.9 | 0,78 | 0,31 | 2,06 | 20,2 | 2,95 | 0,03 | 0,97 | 1,20 |
Муллит — стабильная кристаллическая алюмосиликатная фаза в Al 2 O 3 — SiO 2 и способствует высокой прочности, сопротивлению ползучести, химической инертности и термической стабильности керамических материалов (Martins et al., 2004).
Озтурк (2014) применил процесс промывки, фильтрации и сушки анодированного шлама для удаления натрия перед производством муллитовой керамики.Цикл удаления натрия повторяли до полного удаления натрия из ила. Затем порошок без натрия прокаливают при 1400 ° C в течение 1 ч при скорости нагрева 5 ° C / мин для получения порошка с фазой альфа-оксида алюминия (α-Al 2 O 3 ). Полученный порошок α-Al 2 O 3 был смешан (42 мас.%) С каолином, диатомитом и глиной в пропорциях 15, 28 и 15 мас.% Соответственно. Смесь прессовали и спекали при 1450–1550 ° C в течение 1–5 ч (код образца M1).Результаты сравнивают с другой смесью, приготовленной с использованием коммерческого порошка Alcoa α-Al 2 O 3 (код образца M2). В результате работы было обнаружено, что при соответствующей обработке и смешивании с природными минеральными добавками анодирующий шлам может быть использован в производстве керамических материалов на основе муллита (таблица 7.28) (Ozturk, 2014).
Таблица 7.28. Физико-механические свойства спеченных образцов М1 и М2
Состав | Условия спекания | Прочность на изгиб (МПа) | Плотность (г / см ) | Пористость (%) | Водопоглощение (%) ) | Плотность (%) |
---|---|---|---|---|---|---|
M1 | 1450 ° C — 1 ч | 53 | 2.02 | 26,1 | 12,88 | 63,9 |
1500 ° C — 1 час | 54 | 2,27 | 13,1 | 5,76 | 71,8 | |
1550 ° C — 1 час | 80 | 2,47 | 0,72 | 0,29 | 78,2 | |
1550 ° C — 3 ч | 81 | 2,49 | 0,71 | 0,29 | 78,8 | |
1550 ° C — 5 ч | 84 | 2.49 | 0,72 | 0,29 | 78,8 | |
M2 | 1450 ° C — 1 ч | 72 | 2,15 | 0,81 | 0,81 | 70,3 |
1500 ° C — 1 ч | 80 | 2,13 | 1,02 | 1,02 | 68,7 | |
1550 ° C — 1 ч | 75 | 2,11 | 1,69 | 1,69 | 66,8 | |
1550 ° C — 3 ч | 72 | 2.11 | 1,75 | 1,75 | 66,8 | |
1550 ° C — 5 ч | 72 | 2,10 | 6,36 | 2,36 | 66,5 |
Рибейро и др. (2004a, b, 2006), Ribeiro и Labrincha (2008) и Labrincha et al. (2006) провели подробные исследования использования шламов анодирования алюминием в производстве огнеупорной и электроизоляционной керамики. Огнеупорные керамические материалы на основе муллита и кордиерита получали из составов, содержащих 42 и 25 мас.% Шлама соответственно.Каолин, шариковая глина, диатомит и тальк завершили составы. Цилиндрические образцы, обработанные методом одноосного сухого прессования, спекались при различных температурах. Были оценены свойства материалов после обжига (усадка при обжиге, водопоглощение, прочность на изгиб, коэффициент теплового расширения, огнеупорность и микроструктура на сканирующем электронном микроскопе) и продемонстрировано, что оптимальные свойства были получены при 1650 ° C для муллита и 1350 ° C для тел кордиерита (Ribeiro и Лабринча, 2008). Последние могут использоваться в качестве огнеупорных кирпичей при температуре до 1300 ° C.
Составы, полностью состоящие из ила, были также произведены и испытаны, что выявило образование α-оксида алюминия и β-оксида алюминия (NaAl 11 O 37 ) на образцах, спеченных при 1450 ° C или выше (Ribeiro et al., 2004a , б). Их электроизоляционные характеристики описаны в отдельных работах (Labrincha et al., 2006; Ribeiro et al., 2004a, b). Составы на основе муллита (содержащие 42 мас.% Шлама) демонстрируют электрическую проводимость примерно на четыре порядка выше, чем составы на основе оксида алюминия (100% шлама).Последние обладают изоляционными характеристиками, сопоставимыми с образцами глинозема чистотой 90%. На рис. 7.8 показаны тела, обработанные в ходе этих работ.
Рис. 7.8. Тела на основе алюминиевого шлама, обработанные экструзией и шликерным литьем (Ribeiro et al., 2004a).
Тот же самый шлам также исследовался в составе неорганических пигментов (Leite et al., 2009; Hajjaji et al., 2009), в некоторых случаях в сочетании с другими отходами (например, шламы при волочении проволоки Fe и шламы хромоникелевого покрытия , резка мрамора / полировка шламов / мелочи).Составы, полностью основанные на отходах, образуют стабильные структуры при более низких температурах, чем коммерческие (химически чистые реагенты) пигменты, и могут быть получены различные цвета, как показано на рис. 7.9 (Hajjaji et al., 2012; Costa et al., 2007).
Рис. 7.9. Отличительные пигменты, полученные из отходов (Hajjaji et al., 2012).
(PDF) Возможности использования пластиковых отходов в пенобетоне
WMCAUS 2018
IOP Conf. Серия: Материаловедение и инженерия 471 (2019) 032009 IOP Publishing
doi: 10.1088 / 1757-899X / 471/3/032009
10
получено. Для достижения рациональных свойств керамзитобетона предлагается использовать
5% отходов типа А вместо расчетного количества керамзита фракции 4/8. Затем плотность керамзитобетона
увеличивается примерно на 5%, а прочность на сжатие — на 70% по сравнению с контрольными образцами
, однако водопоглощение и капиллярность снижаются.Кроме того, повышается удобоукладываемость керамзитобетона
.
Заключена полиномиальная математическая зависимость второй степени. Он позволяет прогнозировать прочность керамзитобетона
на сжатие в зависимости от количества отходов. Определение
Коэффициентуравнения равен 0,845. По полученной зависимости видно, что прочность керамзитобетона
на сжатие увеличивается при определенном пределе количества отходов в смеси
, а затем уменьшается.
Анализ микроструктуры показывает, что существует достаточная адгезия между заполнителями, отходами и цементным камнем
. Микроструктура цементного камня при использовании разного количества отходов различается. Самая плотная структура
имеет образцы с 5% отходов типа А. В образцах из всех партий определены одни и те же минералы: портландит, эттрингит, кальцит
и гидросиликаты кальция.
Ссылки
[1] EUR-Lex Доступ к законодательству Европейского Союза http: // eur-lex.europa.eu/legal-
content / LT / TXT /? uri = CELEX: 52013DC0123 Зеленая книга Европейской стратегии по
Пластиковые отходы в окружающей среде
[2] Л. Гу, Т. Озбаккалоглу, «Использование переработанных пластмассы в бетоне: критический обзор, Waste
Management, 51, стр. 19–42, 2016.
[3] П. Лю, Р. Фарзана, Р. Раджарао, В. Сахайвалла, «Легкие вспученные заполнители из смесь отходов автомобильной пластмассы и глины
, Строительные материалы, 145,
с.283–291, 2017.
[4] Х.А. Булут, Р. Сахин, «Исследование механических свойств полимербетона, содержащего
электронных пластиковых отходов», Composite Structures, 178, pp. 50–62, 2017.
[5] В. Грегорова, М. Ледерерова, З. Стефункова, «Исследование влияния вторичного пластика
из отходов кабеля, этиленвинилацетата и полистирола на свойства легкого бетона»,
Engineering Engineering, 195, стр. 127– 133, 2017.
[6] Ф. Коланджело, Р. Чоффи, Б. Лигуори, Ф. Юколано, «Рециклированные полиолефиновые отходы в качестве заполнителей для легкого бетона
», Композиты, Часть B: Разработка, 106, стр. 234–241, 2016.
[7] Р. Шарма, П.П. Бансал, «Использование различных форм пластиковых отходов в бетоне — обзор»,
Journal of Cleaner Production, 112, стр. 473–482, 2016.
[8] A Бадаче, А.С. Беносман, Ю. Сенхаджи, М. Мули, «Теплофизические и механические характеристики
легких композиционных растворов на песчаной основе с переработанным полиэтиленом высокой плотности
(HDPE)», Строительные и строительные материалы, 163, стр. стр.40–52, 2018.
[9] С. Акчаозоглу, С.Д. Атиш, К. Акчаозоглу, «Исследование использования измельченных бутылок из ПЭТ
в качестве заполнителя в легком бетоне», Управление отходами, 30, стр. 285 –290, 2010.
[10] З. Ге, Р. Сун, К. Чжан, З. Гао, П. Ли, «Физико-механические свойства раствора с использованием
бутылок из отработанного полиэтилентерефталата», Строительство и строительные материалы , 44, pp. 81–
86, 2013.
[11] K.А. Джассим, «Переработка полиэтиленовых отходов для производства пластикового цемента», Процедура
Производство, 8, стр. 635–642, 2017.
[12] А. Аттаче, Р. Солтани, А. Махи, «Исследования для Улучшение свойств рециклированных строительных смесей PE
, армированных полимерными частицами, для ремонтных работ, Construction and Building
Materials, 146, pp. 603–614, 2017.
[13] Md. J. Islam, Md. S. Meherier , АКМ Ракинул Ислам, «Влияние отходов ПЭТ как грубого заполнителя
на свежие и твердые свойства бетона», Строительные и строительные материалы
, 125, стр.946–951, 2016.
[14] М.И. Никбин, Р.С. Рахими, Х. Аллахьяри, Ф. Фаллах, «Технико-экономическое обоснование отходов полиэтиленовых частиц
терефталата (ПЭТ) в качестве совокупной замены для кислотной эрозии устойчивых
IRJET -Запрошенная вами страница не найдена на нашем сайте
IRJET приглашает статьи из различных инженерных и технологических и научных дисциплин для Тома 8, выпуск 5 (май 2021 г.)
Отправить сейчас
IRJET Vol-8, выпуск 5, май 2021 г. Публикация продолжается…
Обзор статей
IRJET получил «Импакт-фактор научного журнала: 7,529» за 2020 год.
Проверить здесь
IRJET получил сертификат регистрации ISO 9001: 2008 для своей системы управления качеством.
IRJET приглашает специалистов по различным инженерным и технологическим дисциплинам, научным дисциплинам для Тома 8, выпуск 5 (май 2021 г.)
Отправить сейчас
IRJET Vol-8, выпуск 5, май 2021 г. Публикация продолжается…
Обзор статей
IRJET получил «Импакт-фактор научного журнала: 7,529» за 2020 год.
Проверить здесь
IRJET получил сертификат регистрации ISO 9001: 2008 для своей системы управления качеством.
IRJET приглашает специалистов по различным инженерным и технологическим дисциплинам, научным дисциплинам для Тома 8, выпуск 5 (май 2021 г.)
Отправить сейчас
IRJET Vol-8, выпуск 5, май 2021 г. Публикация продолжается…
Обзор статей
IRJET получил «Импакт-фактор научного журнала: 7,529» за 2020 год.
Проверить здесь
IRJET получил сертификат регистрации ISO 9001: 2008 для своей системы управления качеством.
IRJET приглашает специалистов по различным инженерным и технологическим дисциплинам, научным дисциплинам для Тома 8, выпуск 5 (май 2021 г.)
Отправить сейчас
IRJET Vol-8, выпуск 5, май 2021 г. Публикация продолжается…
Обзор статей
IRJET получил «Импакт-фактор научного журнала: 7,529» за 2020 год.
Проверить здесь
IRJET получил сертификат регистрации ISO 9001: 2008 для своей системы управления качеством.
IRJET приглашает специалистов по различным инженерным и технологическим дисциплинам, научным дисциплинам для Тома 8, выпуск 5 (май 2021 г.)
Отправить сейчас
IRJET Vol-8, выпуск 5, май 2021 г. Публикация продолжается…
Обзор статей
IRJET получил «Импакт-фактор научного журнала: 7,529» за 2020 год.
Проверить здесь
IRJET получил сертификат регистрации ISO 9001: 2008 для своей системы управления качеством.
IRJET приглашает специалистов по различным инженерным и технологическим дисциплинам, научным дисциплинам для Тома 8, выпуск 5 (май 2021 г.)
Отправить сейчас
IRJET Vol-8, выпуск 5, май 2021 г. Публикация продолжается…
Обзор статей
IRJET получил «Импакт-фактор научного журнала: 7,529» за 2020 год.
Проверить здесь
IRJET получил сертификат регистрации ISO 9001: 2008 для своей системы управления качеством.
IRJET приглашает специалистов по различным инженерным и технологическим дисциплинам, научным дисциплинам для Тома 8, выпуск 5 (май 2021 г.)
Отправить сейчас
IRJET Vol-8, выпуск 5, май 2021 г. Публикация продолжается…
Обзор статей
IRJET получил «Импакт-фактор научного журнала: 7,529» за 2020 год.
Проверить здесь
IRJET получил сертификат регистрации ISO 9001: 2008 для своей системы управления качеством.
IRJET приглашает специалистов по различным инженерным и технологическим дисциплинам, научным дисциплинам для Тома 8, выпуск 5 (май 2021 г.)
Отправить сейчас
IRJET Vol-8, выпуск 5, май 2021 г. Публикация продолжается…
Обзор статей
IRJET получил «Импакт-фактор научного журнала: 7,529» за 2020 год.
Проверить здесь
IRJET получил сертификат регистрации ISO 9001: 2008 для своей системы управления качеством.
Горячая продажа золотого концентрата Флотационная ячейка Золотой завод
1988 Год основания 1988
69+ Патенты и сертификаты
400+ Количество сотрудников
13350+ Обслуживаем клиентов
Звездные продукты
Системы дробильно-сортировочной установкипродуманы до мельчайших деталей, и весь процесс всегда находится в руднике.
Онлайн чатПолные квалификационные аттестаты
C&M Mining Machinery — частная китайская компания, занимающаяся проектированием, производством и поставкой мобильных решений для дробления и сортировки по всему миру для строительной, горнодобывающей, карьерной и перерабатывающей промышленности.
Передовые производственные технологии и оборудование
C&M Mining Machinery владеет более чем 50 запатентованным оборудованием собственной разработки, обеспечивающим оцифровку заготовок, автоматизацию сварки и сборочного формования, а также строгий контроль качества продукции на протяжении всего процесса.
Котельная по индивидуальному заказу
C&M Mining Machinery имеет сильную команду разработчиков котлов и построила полную систему исследований и разработок.
Комплексное и профессиональное послепродажное обслуживание
C&M Mining Machinery имеет профессиональные группы послепродажного обслуживания, которые предоставляют техническое руководство для всего процесса установки и бесплатное обучение для эксплуатационного и обслуживающего персонала..
Добро пожаловать в компанию
C&M Mining Machinery — высокотехнологичная инженерная группа. Мы специализируемся на исследованиях, разработке и производстве оборудования для промышленного дробления, измельчения порошков, обогащения полезных ископаемых и других сопутствующих устройств.
Учить больше[randpic] станки для обработки железа — tcfuwhrorg Читать дальше
[randpic] Статистика рынка камнедробильного оборудования — анализ размеров…Отраслевые тенденции. Объем рынка камнедробильного оборудования в 2018 году оценивался в более чем 4,5 миллиарда долларов США, и его среднегодовой темп роста превысит
. Читать дальше [рандпик] URBAN CRUSHER — jocurinJocuri online super tari si imbunatatite aici pe site-ul nostru plin de jocuri cu jocuri cu masini noi, pe care le poti juca la orice minut si poti sa te distrezi gratu
Читать дальше [randpic] шаровая мельница vertikal dalam Industri semenprofesional pabrik penggilingan semen, semen mesin pemasok dengan 58 dampak crusher, шариковая мельница для спермы Lifer, sistem pemanasan, semen вращающаяся печь proses
Читать дальше АКЦИОНЕРНОЕ ОБЩЕСТВО «ЗАВОД ГЛИНЯНЕГО ГРАВИНА НОВОЛУКОМЛЬ»
Дом »Компании »АКЦИОНЕРНОЕ ОБЩЕСТВО« ЗАВОД ГЛИНЯНОГО ГРАВИНА НОВОЛУКОМЛЬ »Беларусь
Количество сотрудников: 100+
Беларусь, 211162, Витебская область, г. Новолукомль, шоссе Крупское, 1
Напиши сообщениеОАО «Завод керамзитового гравия Новолукомль» производит керамзит следующих видов: керамзитовый гравий фракции 8/20 мм или 4/10 мм; песок керамзитовый фракции 0/4 мм.Продукция завода соответствует требованиям действующих стандартов — СТБ EN 13055-1-2003, СТБ EN 14063-1-2007, EN 13055-1, EN 14063-1; Имеет маркировку СЕ, дающую право на импорт и применение в строительстве в странах Европейского сообщества. Система менеджмента качества ОАО «Завод керамзитового гравия Новолукомль» сертифицирована международным сертификационным органом BVC (Bureau Veritas Certification) на соответствие требованиям ISO 9001: 2000, ISO 14001: 2004, OHSAS 18001: 1999.
СертификатыТоваров
Беларусь
Керамзитовый гравий фракции 10/16 мм насыпью
Беларусь
Керамзит — это спеченный материал с ячеистой структурой, полученный расширением и обжигом темно-коричневых глин.Обладая высокой прочностью, он обладает низкой насыпной плотностью и высокими теплоизоляционными характеристиками …
Беларусь
Керамзит применяется в гражданском и промышленном строительстве в качестве заполнителя для легкого бетона с объемной массой 500 кг / м3 и теплопроводностью 0,13 Вт / м · К, в качестве теплоизоляционного заполнителя с плотностью …
Беларусь
Керамзит применяется в гражданском и промышленном строительстве как заполнитель для легкого бетона с объемной массой 500 кг / м3 и теплопроводностью 0,13 Вт / м · К, как теплоизоляционный заполнитель с т…
Беларусь
Керамзит применяется в гражданском и промышленном строительстве в качестве заполнителя для легкого бетона с объемной массой 500 кг / м3 и теплопроводностью 0,13 Вт / м · К, в качестве теплоизоляционного заполнителя с плотностью …
Изготовлено LECA LWA
Простые идеи часто служат дольше.Leca® LWA производится из свежей глины и производится путем предварительной обработки и высоких температур. Из 1 м3 свежей глины получается 5 м3 прочного природного заполнителя, который можно использовать во всем, от цветочных горшков до конструкционных бетонных элементов мостов в суровых северных морях. Сосредоточенность на ресурсоэффективном производственном процессе всегда сохраняется с упором на производство как можно меньшего количества отходов в процессе. На всех производственных предприятиях Leca действует строгий контроль качества, чтобы поставлять высококачественные материалы с минимальным воздействием на окружающую среду.
Leca® Легкий заполнитель из вспененной глины подвергается ряду производственных процессов, начиная с момента сбора глины на глиняном поле и до производства готового продукта и его упаковки в мешки, грузовики и корабли для доставки заказчику. Ниже описаны 8 этапов производственного цикла. Также посмотрите видео выше, в котором показаны шаги один за другим.
- Добыча глины: Глина собирается с глиняного поля и вносится в глиняный амбар после отделения более крупных камней от глины.
- Заменители глины: глина смешивается с регенерированными отходами для сохранения природного сырья. Замещающие продукты состоят из избыточных продуктов / биоотходов других производств.
- Измельчение: более мелкие камни дробятся, а глина продавливается через небольшие отверстия.
- Замес: глину замешивают с небольшим количеством воды, чтобы облегчить процесс обработки.
- Сушка: Глина проходит через сушильную печь, где вода испаряется, а глина нагревается до 400 ⁰C.Именно здесь гранулы Leca приобретают свои особые размеры (0-4, 4-10 и 10-20 мм) по мере того, как глина раскалывается на более мелкие частицы.
- Горение: В следующей части печи, в горящей печи, глина нагревается до 1150 ⁰C, что вызывает процесс расширения, в результате чего образуются легкие круглые легкие глиняные агрегаты. Для осуществления этого процесса сжигания используется комбинация угля и отработанного топлива из других отраслей промышленности.
- Просеивание: когда гранулы глины из легкого заполнителя извлекаются из печи, они помещаются в систему сит, которая делит их на 9 различных фракций в зависимости от размера зерна.Эти размеры глины имеют различные свойства в зависимости от геотехнических требований.
- Упаковка: В последнем процессе легкие глиняные гранулы из заполнителя упаковываются в мешки или загружаются прямо на грузовики и корабли и доставляются непосредственно клиентам.
«Большинство наших промышленных проектов включают попытки заменить ископаемое топливо отработанным топливом или сырье в смеси Leca с остатками», — Йеспер Шмидт, руководитель проекта на фабрике шарниров, Дания.
Фабрика петель имеет 3 действующих печи, каждая из которых поставляет 200 000 м3 легких заполнителей в год. Конечно, для этого требуется много топлива, поскольку ротационные печи нагреваются до 400 ° C в сушильной части печи и до 1150 ° C в обжиговой печи. Обжиговые печи работают более или менее 24 часа в сутки, 7 дней в неделю, 365 дней в году. На большинстве заводов Leca биотопливо используется в дополнение к сжиганию угля, чтобы максимально снизить выбросы.
Leca® UK импортирует легкий керамзит с ряда наших наиболее удобно расположенных производственных предприятий, включая Данию, Португалию и Норвегию.Несмотря на то, что каждое предприятие управляется «Центральной командой Leca», они стремятся найти наиболее эффективные и экологически безопасные методы и материалы для производства, и постоянно стремятся улучшить нашу экологическую репутацию.
.