Керамогранит теплопроводность: вес, толщина, плотность, теплопроводность, размеры
вес, толщина, плотность, теплопроводность, размеры
У любого человека, впервые услышавшего название такого отделочного материала как керамогранит, возникает двоякое чувство: с одной стороны – керамика означает что-то искусственное, с другой – гранит это гарантия природной прочности. Оба понятия совершенно справедливы по отношению к керамическому граниту.
Всё дело в том, что этот материал изготавливается по тому же принципу, по которому формируется натуральный камень. Разница в том, что природный процесс неуправляем и долог, а технические характеристики керамогранита обусловлены контролем за процессом производства.
Структура синтетического камня
Его состав практически идентичен структуре натурального гранита, т.е. в нем присутствуют полевые шпаты, каолиновые глины, есть кварцевые включения. Образование природного и искусственного камня происходит в одних и тех же условиях высокого давления. Но в чем же разница?
Натуральный гранит имеет неоднородную структуру.
Керамогранит обладает множеством уникальных характеристик
Производство керамогранита подразумевает полностью управляемый процесс. При этом используются только отфильтрованные исходные материалы. Искусственный камень не может иметь трещин, полостей, что обуславливает его высокую стойкость к статистическим и динамическим нагрузкам. Керамогранит имеет нулевое водопоглощение и полностью безопасен в экологическом плане.
Технические характеристики керамогранита
Они являются одним из определяющих факторов при выборе любого строительного материала. Средняя толщина керамогранита находится в пределах 8-14 мм. С 1984 года в Европе существует стандарт EN, «отвечающий» за качество любой керамической плитки. Ниже приведены наиболее важные показатели, характеризующие керамогранит.
- Износоустойчивость. Сюда включается сразу 3 понятия. Это сопротивляемость глубокому износу, «терпимость» к поверхностному износу, стойкость. У разных типов синтетического камня износоустойчивость может быть разной. По шкале EN максимальное значение (наименее прочный камень) составляет 205 мм куб.
- Стойкость к истиранию. Этот показатель важен, если отбирается плитка для пола. Существует 5 классов, один из которых и присваивается определённой партии продукции.
Комната, с покрытием из матового керамогранита
- Морозоустойчивость. Один из важнейших показателей, определяющих возможность применения материала вне помещений. Любая разновидность керамогранита способна выдержать до 50-ти циклов, предусматривающих замораживание и последующее размораживание.
- Водопоглощение. У керамогранита оно крайне низкое. Стандарт EN определяет значение не более 3%. Однако в реальности цифра в среднем составляет 0,05-0.
5%. Невозможность глубокого проникновения влаги в плитку гарантирует её защиту от разрыва при морозах.
- Удельный вес керамогранита составляет около 2400 кг/куб.м. Это примерно соответствует удельному весу стекла.
- Устойчивость к механическому воздействию. Здесь EN выделяет две позиции:
– сопротивляемость царапинам: >6 Моос;
– устойчивость к образованию разлома: >27 N/mm кв.
Помимо этих значений, существует такое понятие, как «прочность на изгиб». Керамогранит по этой характеристике прочнее природного камня в три раза, обычной напольной керамической плитки в полтора раза, а настенной – в два. Получаемая при производстве плотность керамогранита достигает 1400 кг/куб.м. - Стойкость цвета, его чистота. EN определяет эту характеристику, как «без изменений». Действительно, керамогранит не взаимодействует с химическими веществами, не реагирует на длительное солнечное излучение. Однако стоит помнить; чем сложнее фактура камня, тем сильнее он «притягивает» загрязнения.
- Длина, ширина. Самый популярные размеры керамогранита – 600 на 600 мм. Для малых помещений используют меньшие размеры, например, 300 на 300 мм. Производители же «держат» общий диапазон от 200 на 200 мм до 1200 на 1800 мм.
- Шероховатость (сопротивляемость скольжению). Это свойство имеет существенное значение при выборе плитки для напольного покрытия. Для определения класса проводятся испытания. При этом для частного жилья рекомендуется один тип камня, для общественных мест – другой. Производитель в любом случае выпускает плитку для пола с выраженной рельефностью, что позволяет исключить скольжение и избежать травматизма.
- Теплопроводность. Нормативные документы не отражают эту характеристику. Но постоянное использование искусственного камня для вентфасадов и в качестве напольного покрытия теплых полов свидетельствует, что коэффициент теплопроводности керамогранита меньше, чем у природного гранита.
Разновидности керамогранита
Они определяются поверхностью плитки, которая обрабатывается разными способами, ведущими к изменению свойств материала. Плитка может быть:
- матовой: после обжига камень не обрабатывают механически;
- полированной: необработанная сторона срезается, обрабатывается;
Пол, отделанный полированным керамогранитом
- полуполированной: срезается часть поверхности и полируется, что создаёт эффект фактуры;
- сатинированной: на плитку перед обжигом наносят минеральные кристаллы;
- глазурованной: на основу наносят эмаль и всё вместе подвергают обжигу;
- ректифицированной: готовые плитки обрабатываются дополнительно для унификации размеров;
- структурированная: при прессовании имитируется фактура дерева, камня.
Технология производства керамического гранита
1.Подготовка исходной глиняной смеси. В её состав входит:
- каолиновая глина;
- монтмореллонитовая глина;
- полевой шпат;
- кварцевый песок;
- красящие минеральные пигменты (окислы железа).
2.Формовка. Может происходить посредством экструзии, литья или прессования. Первые два метода пригодны только для получения декоративных элементов. Для производства керамогранитной плитки необходим последний способ.
Смесь предварительно просушивают и подвергают давлению в 500 кг/кв.см. Если плитка должна иметь пару слоёв, то прессование повторяют. На подготовленную к обжигу смесь наносят рельефный рисунок.
Процесс производства керамогранитной плитки
3.Обжиг. Он происходит в печах тоннельного типа. Температура доводится до +1200-1300С. Чтобы обжиг был более равномерным, материал всё время движется в печи, а колебания температуры заранее программируются. Высокие характеристики керамогранита достигаются за счёт процесса реструктуризации (полного внутреннего изменения свойств входящих в состав смеси материалов, их глубокого проникновения друг в друга).
Применение
Благодаря высокой степени износоустойчивости одной из самых популярных областей применения керамогранита стало обустройство пола, особенно в общественных помещениях (вокзалы, магазины, кафе и т.
Синтетический камень также очень часто используют при монтаже вентфасадов. Однако следует помнить, что вес керамогранита накладывает определённые требования к подготовке каркаса.
толщина пола, технические характеристики и теплопроводность, удельный вес и водопоглощение
Достаточно популярным и востребованным материалом для отделки пола является керамогранит
Отличие керамогранитной плитки лежит в технологическом процессе производства. Для керамогранитной плитки используется прессование под давлением не менее 450 кг/см2 в отличие от керамической плитки. Керамическую плитку прессуют под давлением не более 300 кг/см2. Вторым отличием в технологии является температура обжига: для керамогранита применяется не менее 1300 ᵒС, для керамической плитки – 500-900 ᵒС. Ниже узнаем о керамогранитной плитке подробнее.Содержание материала:
Керамогранит и его технические характеристики
При всей схожести названия, керамогранитная плитка не имеет никакого отношения к граниту, разве что, можно сказать прочная, как гранит. Керамогранитную плитку можно отнести к особому виду керамической плиты. Описание технологического процесса строится так: перемешивается масса глины, песка, шпатов и минеральных красителей до однородной гомогенной массы, затем прессуется на гидравлическом прессе под давление не менее 450 кг/см2, чем давление будет выше, тем масса будет плотнее без мельчайших воздушных камер, затем эти плитки сушат и только после этого полуфабрикаты обжигают при температуре не меньше 1300 оС в тоннельной печи.
Ознакомиться с техническими характеристиками керамогранита можно самостоятельно в интернете или в магазине
Уникальные эксплуатационные качества керамогранитной плитки можно сгруппировать по следующим критериям:
- Особая прочность к механическим повреждениям, устойчивость к ежедневной нагрузочной шлифуемости, как от оборудования, так и от любых движущихся объектов, незаурядная износоустойчивость;
- Предел прочности на изгибе регламентируется ГОСТом;
- Низкая способность к абсорбции воды, т.
е. поглощение воды намного меньше, чем у натурального гранита;
- Абсолютная невосприимчивость к действию агрессивных химических растворов;
- Прекрасная адаптивность к резким перепадам температуры;
- Устойчивость по отношению действия внешней среды на цветовую гамму и глубину рисунка;
- Высокая устойчивость на изгиб;
- Нескользящая поверхностью при намокании.
Особые технические характеристики керамогранитной плитки делают ее довольно востребованным строительным материалом для широкого спектра использования. Многоцветный керамогранит группируется по типу получения внешнего окраса. Гомогенный, технический, производится в соответствии со стандартами без какой-либо дополнительной обработки поверхности, шершавый, имеет однородную структуру, внешне похож на натуральный гранит или керамический камень, имеет увеличенную толщину и небольшой размер плитки, считается наиболее прочным.
В состав керамогранита входят только природные материалы, что определяет его экологичность.
Глазурованный – до обжига в печи на полуфабрикат наносится тонкий слой глазури, после процедуры запекания, глазурь впекается в поверхность плитки. Двойная засыпка или частично-окрашенный, когда в верхний слой примешаны окрашивающие пигменты, а нижний слой из исходного сырья. Окрашенный в массе – до вымешивания смеси, добавляются красящие пигменты, которые вмешиваются во всю массу плитки, после обжига плитка приобретает равномерный окрас по всей толщине.
Состав керамогранита
Керамогранит можно систематизировать по типам поверхности (из Вики). Матовая или натуральная, присуща техническому (гомогенному) керамограниту, получается на выходе после обжига без какой-либо дополнительной обработки. Шлифованная, обработанная специальными абразивными щетками с алмазным напылением, имеет красивый ненавязчивый глянец, приятный на ощупь. Полированная шлифуется алмазными дисками до зеркального вида, на ощупь очень гладкая, скользящая. Структурированная имитирует любой вид рельефной поверхности, например, дерево, кожу, любой натуральный камень и т. д. Сатинированная производится путем нанесения на готовые полуфабрикаты минеральных солей, после обжига получается легкий глянец. Лаппатированная или полуполированная, получается путем частичного срезания верхнего матового слоя на специальном оборудовании, образуется поверхность с чередованием гладкой и матовой структуры с ощущением объемности.
Производят также керамогранитную плитку с рустичными, антибактериальными, светящимися, противоскользящими поверхностями. Как говорится, на вкус и цвет, был бы любитель.
Для изготовления керамогранита, как правило, используется кварцевый песок, полевой шпат и каолиновая глина
Неполированный, технический керамогранит используется в промышленных учреждениях, складах, рельефный объемный керамогранит легко вписывается в любой интерьер помещения, полированный керамогранит применяется часто для облицовки фасада зданий. Легче перечислить, где не используется керамогранит. Уникальные свойства керамогранита формируются его составом и технологическим процессом и проверяются в процессе эксплуатации.
Для изготовления керамогранита, требуется следующий состав сырья:
- Каолиновая глина тугоплавких сортов;
- Чистый кварцевый песок;
- Полевой шпат;
- Натуральные красящие пигменты, как правило, окиси металлов.
Все составляющие сырья для производства керамогранитной плитки имеют природное происхождение. Технология проверки на химический состав, радионуклиды обязательно применяется к сырью керамогранита в соответствии с ГОСТом.
Правильная толщина керамогранитной плитки для пола
Находясь в любом месте, стоит просто оглянуться вокруг себя и, обязательно, взглядом натолкнешься на керамогранит. Керамогранитом выложены стены, пол, фасады, дорожки и т.д. Используют его и на мебели, вместо подоконников, столешниц. Керамогранит производится разных размеров, в том числе и толщины.
При выборе керамогранитной плитки для пола, настоятельно рекомендуется обращать внимание на толщину плитки.
От толщины выбирается схема укладки, учитывать при определении нагрузки на истираемость участка, высота, на которую есть возможность приподнять пол. Толщина керамогранитной плитки для пола варьируется от 3 мм до 30 мм и неразрывно связана с форматом плитки.
Выбирая керамогранитную плитку для отделки пола, специалисты рекомендуют обращать внимание на ее толщину
Востребованным размером выпускаемой плитки считается (мм):
- 600х600;
- 600х600х10;
- 400х400х9;
- 300х300х8;
- 1200х300;
- 450х450
- 300х600.
Толстый керамогранит имеет высокое значение сопротивляемости на изгибе и большой срок службы. Чем толще плитка, тем она прочнее, тем не менее, толщину надо соотносить с необходимостью к механической нагрузке, чтобы не переплачивать за нее.
Для чего знать удельный вес керамогранита
Удельный вес керамогранита, еще один критерий, по которому можно определить качество плитки. Существует ГОСТ, которым руководствуются производители, и согласно которому удельный вес керамогранита должен быть в пределах 2400/м3. Исходя из удельного веса и произведя не сложный расчет, квадратный метр керамогранита должен весить в пределах 18,5-19 кг.
При расчете веса плитки нужно учитывать также ее плотность и пористость
На вес плитки влияет:
- Плотность плитки;
- Пористость плитки;
- Процент водопоглощения.
Вес можно рассчитать путем умножения объема на его плотность. Применение значения удельного веса на практике поможет сделать вывод о качестве керамогранита.
Каково водопоглощение и плотность керамогранита
Водопоглащение напольного керамогранита регламентируется стандартами. Водопоглощение определяет способность керамогранитной плитки впитывать и удерживать в своих порах влагу. Чтобы определить процент водопоглащения, образец керамогранита подвергают манипуляциям.
Водопоглощение и плотность керамогранита должны соответствовать принятым стандартам
А именно:
- Высушивают до состояния постоянного веса и взвешивают;
- Помещают в горячую влажную среду;
- Кипятят в течение 1 ч;
- Взвешивают и находят процент изменения объема и веса.
Для керамогранита процент водопоглощения не должен превышать 0,05%. Этот коэффициент учитывается при использовании цементных растворов или клеевых основ при укладке керамогранитной плитки.
Что такое теплопроводность керамогранита
Теплопроводность керамогранита определяется его способностью передавать тепло от основания на поверхность плитки. Теплопроводность керамогранита зависит от следующих факторов – наличия пористости плитки, степени кристаллизации, состава. Теплопроводность необходимо учитывать при монтировании теплого пола или объектов на улице.
Если вы собрались устанавливать теплый пол, в таком случае необходимо учитывать теплопроводность керамогранитной плитки
Чтобы определить плотность керамогранита, необходимо для образца измерить длину, ширину, толщину, вычислить объем по формуле, взвесить, поделить массу на объем. Плотность позволяет рассчитать нагрузку на плитку. В некоторых случаях, это бывает необходимо.
Классификация керамогранитной плитки (видео)
youtube.com/embed/5l8qiS1jSik» frameborder=»0″/>
Производители учитывают потребности покупателей и выпускают не только керамогранитную плитку, но и декоративные и отделочные дополнения в одном стиле с керамогранитной плиткой. Используя их при укладке плитки, получается законченный красивый вид. Все это делает керамогранитную плитку абсолютно универсальным материалом для облицовки объектов.
водопоглощение, морозостойкость, теплопроводность и термическая стойкость. Статьи компании «ЛенКерам»
Физические свойства плитки — это свойства, которые не зависят от механического или химического воздействия. Изменение в состоянии материала при повышении влажности, температуре ниже 0 градусов, теплопроводность и термическая стойкость.
Водопоглощение
Данный параметр показывает пористость плитки, что непосредственно влияет на плотность изделия, и соответственно на прочность. Чем более пористая плитка, тем менее она прочная, в соответствии с чем классифицируется по соответствующему стандарту EN 14411.
Показатель водопоглощения зависит от количества жидкости, которое она впитывает в соотношении к массе сухой плитки. В случае с глазурованными плитками, данный показатель не затрагивает глазурь, так как у глазури отсутствует пористость.
Водопоглощение определяется двумя методами: кипячения (плитку на 2 часа опускают в кипящую воду) и вакуумным методом (водонасыщение происходит в вакуумной камере с пониженным давлением). При испытаниях, плитку взвешивают в сухом состоянии, после чего производят погружение в воду, и после извлечения снова взвешивают, на основании чего рассчитывают водопоглощение.
Морозостойкость
Показатель, отражающий способность плитки выдерживать температуры ниже ноля градусов, это особенно важно для плитки, которую планируется использовать в экстерьере.
Замораживание происходит в 2 этапа: проникновение воды внутрь плитки;замораживание её и соответственно расширение. Показатель морозостойкости определяется по двум параметрам: возможность попадания воды внутрь плитки; размер и форма пор — которые определяют степень нагрузки, которую материал будет испытывать в процессе замерзания.
Соответственно, можно сделать вывод, что данное качество напрямую связанно со свойством водопоглощения плитки, чем оно выше, тем ниже морозоустойчивость. Чем отличается технический керамогранит от обычного? Узнайте в статье по ссылке
Теплопроводность и термическая стойкость
Теплопроводность — коэффициент теплопроводности плитки варьируется обычно от 0,5 у более пористых материалов, до 0,9 у более плотных (клинкер, керамогранит).
Керамическая плитка как и натуральный камень может аккумулировать тепло, то есть плитка долго нагревается, но нагревшись — долго остывает. Все эти свойства необходимо учитывать при проектировании облицовочных поверхностей, а так же при устройстве теплых полов.
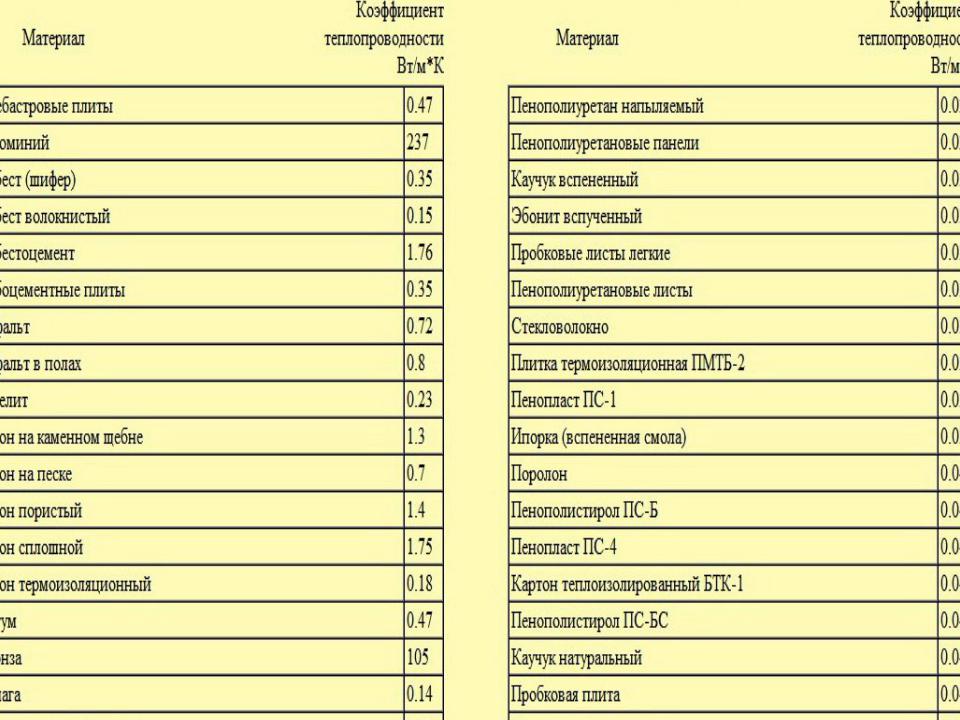
Конечно вряд ли в каком-либо магазине вы в описании увидите все эти показатели, да и если спросите у консультанта, нельзя быть уверенным, что он знает ответы, поэтому правила простые: керамогранит и клинкер могут находиться в суровых условиях перепадов температуры, и замерзания, а вот керамическая плитка скорее всего потрескается.
Керамогранит Estima Iron IR 02 600х600 мм в Саратове за 1 141.68 руб. в наличии
Керамогранит Iron — новинка 2016 года!
Модели коллекции керамогранита Estima Iron имеют оригинальный дизайн поверхности.
Керамогранит коллекции Estima Iron IR 02 — максимально реалистично создает имитацию рисунка и фактуры металла.
Покрытие выпускается в стандартном размере 600х600 мм и имеет высокие эксплуатационные характеристики, устойчиво к механическим повреждениям, благодаря чему может использоваться в жилой и коммерческой недвижимости: ресторанах, кафе, офисных центрах и пр. помещениях с большой проходимостью, а также на улице.
У каждого цвета плиток 600×600 мм — 8 варианта графических рисунков.
Натуральная матовая поверхность Iron идеально впишется как в ультрасовременный интерьер индастриал, в сверхмодный стиль лофт, так и хороша будет в качестве фона для классической мебели.
Керамогранит Estimа Iron обладает всеми свойствами натурального природного камня, но значительно превосходит его по техническим характеристикам. Используется для внутренней и внешней отделки помещений.
Iron не имеет глазурованного декоративного слоя на поверхности плитки и тем самым обладает наилучшими эксплуатационными свойствами.
Матовая поверхность — наиболее прочный и недорогой тип материала, он не подвергается обработке, что гарантирует целостность текстуры.
Благодаря высокой теплопроводности плитка может укладываться поверх системы «теплый пол».
Низкое водопоглощение делает покрытие морозостойким, пригодным для использования облицовки террас.
Преимущества керамогранита Estima Iron IR 02:
- износоустойчивость;
- способность выдерживать воздействие повышенной и пониженной температуры и её изменение;
- стойкость к химически агрессивным веществам;
- твёрдость и механическая прочность;
- однородная окраска по всей толщине материала;
- морозоустойчивость.
На сегодняшний день он широко используется как для отделки жилых, так и коммерческих помещений. Можно сказать даже больше – этот вид отделочного материала является универсальным и подходит для облицовки любых поверхностей.
Выбирая керамогранит Estimа для гостиной, для ванной или для кухни, вы выбираете качество, надежность и долговечность.
Керамогранит Estima обладает настоящим итальянским качеством, поскольку производство оснащено оборудованием от ведущих итальянских производителей.
Это особый вид высококачественной керамической плитки, который имеет превосходные эксплуатационные, технические и функциональные характеристики. Тщательный отбор сырья и многократный контроль качества дополняют этот процесс, а автоматизация производства гарантирует соблюдение технологий.
Технические характеристики керамогранита Estima:
Технические характеристики | Международные стандарты | Средние показатели Estima | |||
UNI EN 14413 | ASTM | ||||
Линейность (кривизна) | ± 0,5% | — | ± 0,1% | ||
Трапецеидальность (косоугольность) | ± 0,6% | ≤ ± 1% | ± 0,3% | ||
Кривизна поверхности | ± 0,5% | ≤ ± 0,75% diagonal | 0,2% | ||
Водопоглощение | < 0,5% | < 0,5% | < 0,07% | ||
Предел прочности при изгибе | > 27 мРа | ≥ 250 Lbs | > 45 мРа | ≥ 440 Lbs | |
Твердость по шкале Мооса | > 6 | — | <7 | ||
Морозостойкость | Без повреждений | Без повреждений | > 200 циклов без повреждений | ||
Химическая стойкость | Без повреждений | Без повреждений | Без повреждений |
Компания Estima Ceramica в 2001 г. первой в России освоила выпуск керамического гранита. Сегодня Estima Ceramica — крупнейший в России производитель керамогранитной плитки с производственной мощностью 15 млн кв.м в год. Керамогранит торговой марки Estima украшает многие архитектурные объекты, появившиеся в России за последние 15 лет.
Керамогранит TM Estima ® — это:
- современный дизайн;
- широкий ассортимент;
- внедрению передовых технологий;
- экологическая и гигиеническая безопасность;
- высокие эксплуатационно-технические показатели;
- срок службы — более 50 лет.
На данный момент Estima – лидер в своей отрасли, а керамика предприятия – продукт высочайшего качества, который успешно конкурирует на рынке с известными зарубежными брендами.
Как выбрать плитку по тех. характеристикам
Средняя толщина керамогранита составляет 8-14 мм.Минимальная – 7 мм, максимальная – 30 мм.
Керамический гранит большей толщины применяют для изготовления напольных покрытий, где предполагается повышенная нагрузка.

Удельный вес керамогранита
DIN 51057 по европейским нормам составляет в примерно 2400 кг/м3. Исходя из значения удельного веса керамического гранита, нетрудно рассчитать вес одной плитки заданного размера и толщины. Удельный вес керамогранита примерно соответствует удельному весу стекла, что делает его удобным в монтаже совместно со стеклом, часто применяемом при строительстве вентилируемых фасадов зданий.Плотность керамогранита
Понятие плотности керамогранита не отражается в нормативных документах. Существует норматив «веса на единицу объёма» (DIN 51065 по европейским нормам), что, собственно говоря, и есть плотность. Для транспортных и иных расчётов чаще оперируют понятием «удельный вес». Высокая плотность керамогранита имеет своё логическое следствие – низкое водопоглощение.Водопоглощение керамогранита
Водопоглощение керамогранита (EN 99 или ISO PROJECT 10545/3 по европейским стандартам) из меряется в процентах и в зависимости от марки и производителя керамогранита доходит до 0,05% и ниже.
Важным свойством керамогранита является его оптимальная теплопроводность для многих строительных задач. В нормативных документах по керамограниту эта характеристика так же не отражается, но практическое использование керамогранита, как строительного материала и для тёплых полов и для вентилируемых фасадов, говорит о том, что его теплопроводность выгодно отличается от теплопроводности натурального камня (намного меньше, чем у камня).
Напольная плитка под дерево в ванную, кухню или прихожую
Плитка под паркет: все за и против
Плитка с имитацией деревянного пола — прекрасный способ сделать интерьер более теплым и уютным (коллекция Laparet HillWood)
Издавна древесина считается одним из лучших отделочных материалов. Привлекая экологичностью, красотой структуры и доступной стоимостью, она обладает необходимыми эксплуатационными свойствами – хорошей тепло- и звукоизолирующей способностью, долговечностью, простотой обработки и монтажа. Но иногда паркетный или дощатый пол лучше заменить имитацией. И в этом случае лучше всего подходит керамическая плитка, стилизованная под натуральное дерево. По сравнению с оригиналом такое покрытие имеет ряд достоинств:
- Более высокая прочность. В этом плане современные марки керамогранита выигрывают даже у натурального камня. Отделанный строительной керамикой пол никогда не продавится ножками мебели и легко справится с другими физическими воздействиями.
- Широкая цветовая палитра. Вы можете выбрать плитку с рисунком определенной породы дерева или же найти искусственно созданные фактуры и оттенки, которые лучше всего подойдут к обстановке.
- Предельная износостойкость. Поверхность керамики намного лучше противостоит истирающим нагрузкам, поэтому та же плитка под паркет будет блестеть и радовать отсутствием царапин даже после многолетней эксплуатации. В большинстве случаев деревянный пол приходится периодически шпаклевать, перекрашивать или лакировать.
- Простота ухода.
Керамику не придется покрывать мастикой, натирать и шлифовать. Все, что понадобится, чтобы вернуть ее к первоначальному виду, – это простая влажная уборка с минимальным количеством моющих средств.
- Устойчивость к любым внешним воздействиям. Плитка и керамогранит под дерево не боится огня и влаги, отлично справляется с химическими и бактериальными загрязнениями, не выгорает на солнце и при нагревании не выделяет вредных токсичных веществ.
Как можно видеть, керамика превосходит древесину по целому ряду параметров. Единственное, в чем она проигрывает – это высокая теплопроводность. Там, где деревянный пол будет манить мягким, «ламповым» теплом и домашним комфортом, керамика будет отталкивать холодом. Но это неудивительно, ведь мы имеем дело с материалом, чьи характеристики максимально приближены к природным минералам.
Важно! Низкая теплоизолирующая способность керамической отделки является минусом ровно до той поры, пока речь не заходит о системе теплого пола. Если вы планируете обустраивать в своем доме нижний подогрев, то лучшего облицовочного материала, чем керамогранит, просто не существует. Благодаря высокой плотности и теплопроводности этот материал быстро и равномерно прогревается, делая напольный обогрев максимально комфортным и экономичным.
Керамический паркет: критерии выбора
Практичность и простота уборки являются существенными преимуществами плитки под паркет или палубную доску, особенно если речь идет об отделке санузла или ванной комнаты (коллекция Meissen (Mei) Love You Navy)
В ассортименте продукции заводов строительной керамики присутствует несколько видов плитки, которая отличается как дизайном и ценой, так и техническими и эксплуатационными характеристиками. Последние выходят на первый план, когда заходит речь о прочности и долговечности материала, поэтому в зависимости от целевого назначения при выборе облицовочной керамики следует внимательно отнестись к следующим параметрам:
- Износостойкость.
В зависимости от устойчивости материала к истирающим нагрузкам различают 5 классов износостойкости PEI I-V. Максимальными характеристиками обладает керамический паркет PEI-V, который можно использовать даже в таких нагруженных местах, как залы аэропортов, вокзалы, торговые залы супермаркетов и т.д. Разумеется, цена подобной плитки под дерево достигает максимума. Для офисных помещений рекомендуется использовать более дешевый керамогранит IV класса. Он же будет дольше всего служить и в таких помещениях, как кухня, ванная или прихожая. Плитку PEI-III можно использовать в большинстве помещений в доме. Ее выбор позволит избежать ненужных трат и получить качественное, долговечное покрытие. Что касается материалов I и II класса износостойкости, то они лучше всего подходят для мест, где предполагается ходить в мягкой обуви или босиком.
- Химическая устойчивость влияет на стабильность цвета и покрытия при воздействии агрессивных веществ. На этот параметр следует обратить внимание, выбирая напольное покрытие для кухни или ванной.
Лучше всего для этих целей подойдет плитка, маркированная «А» или «АА».
- Сопротивление скольжению. От этого параметра зависит, насколько удобно и безопасно можно будет передвигаться по поверхности из керамогранита. Коэффициент трения обозначается литерой R и цифрами от 1 до 11 – чем выше этот показатель, тем менее скользкой будет плитка. Для ванной лучше всего подойдет керамический паркет с обозначением R 11.
Выбирая материал по техническим характеристикам, следует обязательно учитывать и другие факторы. Например, сопротивление скольжению зависит от формата плитки и способа укладки. Многочисленные швы повышают коэффициент трения, поэтому в определенных условиях можно сэкономить, покупая отделку более низкого класса.
Нескользящий керамогранит под дерево: формат и фактура
Плитка под паркет Atlas Concorde Russia Verity является прекрасным доказательством тому, что в коллекциях известных производителей всегда найдется материал, который идеально впишется в интерьер, выполненный в любом стиле
Дизайн плитки с имитацией деревянной поверхности включает множество рисунков и фактур, которые способствуют уменьшению скольжения напольного покрытия. Для этого производители используют несколько технологических приемов:
- делают фактуру материала рельефной;
- наносят на поверхность плитки специальные риски, борозды и насечки, способствующие увеличению сцепления;
- покрывают керамогранит химическими веществами, образующими пленку с повышенными фрикционными способностями.
Кроме того, не следует забывать о возможности увеличить коэффициент сцепления с полом за счет многочисленных межплиточных швов. Выбирая мелкоформатные материалы типа октагональной плитки или мозаики, можно сделать пол более безопасным и эффектным.
Нескользящая плитка не требует монтажа резиновых лент при обустройстве ступеней и входных зон, а в ванной или санузле можно обойтись без дополнительных ковриков с резиновым основанием.
С другой стороны, необходимость сделать поверхность рельефной способствует разнообразию дизайна плитки под дерево. Сегодня производители предлагают качественную имитацию рисунков древесины любой породы – от привычной всем лиственницы или сосны до таких экзотических сортов, как бокота, амарант, эбен и бакаут. Что касается цветового ряда, то потребителям предоставлен выбор из десятков оттенков. Наиболее популярным в настоящее время можно считать напольный керамогранит с имитацией фактуры серого или выбеленного дуба и состаренной палубной доски. Формат материала может быть разным, но в тренде всегда остается напольная плитка под ламинат и паркет. Благодаря современным технологиям нанесения рисунка керамический пол визуально очень похож на деревянный. Если же говорить о практичности, то последний проигрывает искусственным материалам практически по всем параметрам.
Плитка под дерево: выбор и укладка
Испанские и итальянские заводы отделочной керамики уже много лет доминируют на рынке строительных материалов. Плитка и керамогранит под дерево для облицовки пола не является исключением и широко представлена в каталогах самых известных и популярных европейских брендов (коллекция испанской плитки Venis Starwood)
Дерево, как и его качественная имитация, отлично выглядит в любом интерьере – от строгой классики до развязного модерна. Очень часто оригинальную фактуру натурального материала применяют для того, чтобы подчеркнуть теплоту и домашний уют таких направлений в интерьерном дизайне, как прованс, кантри или этно.
В продаже сегодня представлена плитка любого оттенка – от беленого дерева до практически черного венге, поэтому чтобы выбрать идеальный вариант, ищите соответствия в особенностях отделываемых помещений. Так, материалы темных оттенков лучше всего подходят для просторных помещений, поэтому керамогранит с фактурой мореного дуба, вишни, ореха или зебрано будет органично выглядеть в большом холле, зале или на террассе. А вот светлые текстуры таких сортов древесины, как сосна, береза или тик способны сделать пространство более широким, поэтому такой плиткой можно украсить небольшую комнату. Для ванной дизайнеры рекомендуют выбирать испанский или итальянский керамогранит, имитирующий срез карельской березы, клена или ясеня, а для кухни – более насыщенную имитацию вьетнамского дуба, груши или экзотического амаранта.
Внимание! Плитка, изготовленная с применением технологии браширования (искусственное старение), очень часто имеет неравномерную окраску, которая является особенностью дизайна, но никак не браком. Кафель этого типа лучше всего сочетается с отделкой текстильными материалами или мебелью в винтажном стиле.
Выбор плитки под дерево – это всего лишь половина дела. Чтобы подчеркнуть красивую текстуру отделки, необходимо правильно уложить дорогостоящую керамику. В этом случае прибегают к нескольким схемам укладки:
- палубная;
- паркетная;
- в шахматном порядке;
- паркетное плетение;
- ромбическая (шереметьевская) укладка.
В зависимости от выбранного способа укладки может понадобиться чередование отличающихся по оттенку материалов, поэтому перед покупкой материала необходимо сделать дизайн проект и точно рассчитать количество той или иной плитки с учетом отходов на ее подрезку.
Керамогранит – технические характеристики | Свойства материала, характеристики плитки для пола и фасадов: гост, толщина, вес, теплопроводность, водопоглощение, прочность
Для подтверждения технических характеристик керамогранита производители регулярно испытывают его на прочность. Технологии совершенствуются и в 2015 году керамогранит ГОСТ 6787-2001 превосходит требования стандартов практически в два раза.
Технические характеристики керамогранита ГОСТ 6787-2001 и фактических показателей тестов производителей.
Технические характеристики керамогранита | Евростандарт UNI EN 14411 |
ГОСТ 6787-2001 |
Нормативы |
Средние показатели плитки |
|
Соответствие размеров сторон (мм) | (± 1,8 мм) | ± 1,5 | ± 0,5 | ± 0,5 | |
Толщина (мм) | (± 0,4) | ± 0,5 | ± 0,5 | ± 0,2 | |
Кривизна (%) | ± 0,5 | ± 1,5 | ± 0,6 | ± 0,1 | |
Косоугольность (%) | ± 0,6 | ± 0,5 | ± 0,5 | ± 0,3 | |
Кривизна поверхности (%) | ± 0,5 | ± 0,5 | ± 0,5 | ± 0,2 | |
Водопоглощение (%) | < 3 | < 3,5 | < 0,5 | < 0,07 | |
Предел прочности при изгибе (МПа) | > 27 | > 28 | > 35 | > 45 | |
Твердость по шкале Мооса | > 6 | — | — | 7 | |
Устойчивость к истиранию по кварцевому песку (г/см2) |
— | < 0,18 | < 0,18 | 0,08 | |
Износоустойчивость мм3 | <205 | — | — | 190 | |
Морозостойкость (циклов без повреждений) | без повреждений | > 25 | > 50 | > 200 |
Износостойкость
На испытаниях при продолжительном абразивном воздействии керамогранит теряет в толщине от 120 до 200 мм3, меньше чем натуральный гранит. Класс износостойкости керамогранита 4 (PEI Ⅳ) и 5 (PEI Ⅴ).
Водопоглощение
Определяется отношением массы воды в образце при полном насыщении, к его сухой массе. Этот показатель важно учитывать при наружной облицовке. Водопоглощение керамогранита составляет не более 0,05 % — ниже других облицовочных материалов. Он останется без повреждений при температурных перепадах минимум 30 лет.
Стойкость к кислотам и щелочам
Согласно европейским стандарту ISO 10545-13 керамогранит кислотостойкая плитка класса ULA, потеря массы не более 1,36%. По ГОСТ 961-89 плитки вида ТКД и ТКГ предназначение для защиты от концентрированных кислот.
Предел прочности при изгибе и разрушающая нагрузка
Это основные строительные характеристики прочности облицовочных материалов. Предел прочности керамогранита составляет 45 МПа при максимальной разрушающей нагрузке на тестируемый образец 2000 ньютонов. Показания могут незначительно отличатся в зависимости от типа и толщины плитки керамогранита.
Теплопроводность керамики
Керамика находит все большее применение в корпусах и печатных платах, так как имеет ряд преимуществ перед пластиком: гораздо более высокая теплопроводность, возможность согласования коэффициента теплового расширения, герметичность. К сожалению, стоимость керамики все еще намного выше стоимости пластмасс, что не позволяет использовать их в недорогих крупносерийных продуктах. Тем не менее, их использование в будущих продуктах кажется неизбежным, учитывая тенденции в полупроводниковой промышленности, связанные с ожидаемым гораздо более низким тепловым сопротивлением корпусов и одновременной конструкцией корпусов и плат для облегчения отвода тепла.
Проблема с теплопроводностью керамики заключается в зависимости от состава, размера зерна и технологии изготовления, что затрудняет получение достоверного значения только по литературным данным. Глядя на значения, указанные в различных справочниках, документах и таблицах данных, можно заметить две вещи. 1) существуют большие вариации, и 2) многие авторы, кажется, копируют значения из одних и тех же, но неотслеживаемых источников.
Интригующим примером является нитрид алюминия (AIN), все более популярная керамика.Наиболее часто упоминаемое значение составляет около 180 Вт/мК. Однако в Ссылке 1 можно найти некоторые интересные данные в виде графика, на котором значения теплопроводности от семи производителей отображаются в зависимости от температуры. Максимальное значение, найденное при комнатной температуре, составляет 200 Вт/мК; самый низкий — 80 Вт/мК. Кроме того, эти значения падают более чем на 30% при переходе от 20° к 100° С. Такое же падение, кстати, наблюдается и для других керамик, таких как BeO и Al 2 0 3 . (См. также раздел «Технические данные» предыдущего выпуска.)
Теплопроводность (Вт/мК) при 20°C | ||
АИН | Нитрид алюминия | 80-200, 180, 260 |
А1 2 0 3 | Оксид алюминия | 18-36 |
ВеО | Оксид бериллия | 184, 200, 220, 242, 250, 300 |
БН | Нитрид Бора | 15-40, 250-300, 600 |
карбид кремния | Карбид кремния | 90-160, 70-200, 80, 210 |
В таблице показан диапазон значений при комнатной температуре для ряда часто используемых керамических изделий из различных источников. Обратите внимание, что большой разброс значений
Таким образом, опубликованные значения теплопроводности керамики идеально подходят для сопоставления экспериментальных результатов с численным моделированием, и я боюсь, что именно это и происходит на практике. Измерения на месте с использованием хорошо разработанных экспериментальных эталонов являются предпочтительным способом получения точных значений.
Артикул1. R. Dindwiddie, Advanced Electronic Packaging Materials, Vo1.167, Бостон, 1989.
Исследования теплопроводности керамической напольной плитки | Интернет-исследования в области здравоохранения и окружающей среды (HERO)
ID ГЕРОЯ
1739202
Тип ссылки
Журнальная статья
Заголовок
Исследования теплопроводности керамической напольной плитки
Авторы)
Гарсия, Э; де Паблос, А; Бенгочеа, Массачусетс; Гуайта, Л; Осенди, Мичиган; Миранцо, П.
Год
2011
Рецензируется ли эксперт?
1
Журнал
Ceramics International
ISSN: 0272-8842
EISSN: 1873-3956
Объем
37
Проблема
1
Номера страниц
369-375
DOI
10.1016/ж.керамит.2010.09.023Идентификатор Web of Science
WOS:000285853500051Абстрактный
Температуропроводность, теплопроводность и удельная теплоемкость нескольких материалов, используемых в качестве напольной плитки, были измерены методом лазерной вспышки. Природные камни, особенно гранит, керамогранит и красный керамогранит с низким водопоглощением, являются более эффективными теплопроводниками, чем белый керамогранит и винил, теплопроводность которых ниже 1 Вт·м(-1)·К(-1).Следовательно, последние два не следует рекомендовать для применения в системах лучистого обогрева пола. Повышение теплопроводности красного и керамогранита достигается добавлением в керамическую массу Al(2)O(3) определенных характеристик. Таким образом, при добавлении 20 мас.% частиц Al(2)O(3) было получено увеличение температуропроводности до 50%. (C) 2010 Elsevier Ltd и Techna Group S.r.l. Все права защищены.
Ключевые слова
Тепловые свойства; Теплопроводность; Керамическая плитка; Традиционная керамика; Ал(2)О(3)
Керамика с высокой теплопроводностью и их композиты для управления температурой интегрированных электронных корпусов
2.Керамика с высокой теплопроводностью и композиты на их основе
2.1. Керамика и композиты на основе нитрида алюминия (AlN)
2.1.1. Керамика AlN со спекающими добавками
Нитрид алюминия (AlN) имеет структуру вюрцита с высокой ковалентной связью, высокую теплопроводность и низкий коэффициент теплового расширения (КТР) 4,5 ppm/°C, что хорошо сочетается с кремниевыми устройствами. Типичная теплопроводность AlN составляет 140–180 Вт/мК, но варьируется в диапазоне 18–285 Вт/мК в поликристаллической керамике AlN в зависимости от условий процесса, чистоты исходных материалов и микроструктуры [1].AlN стабилен при 700–1000°C в атмосфере кислорода. Он также обладает превосходными диэлектрическими свойствами: низкая диэлектрическая проницаемость (ε r ) = 9 и низкие потери (tan δ) = 0,0003 при 1 МГц. Благодаря этим выдающимся физическим и термическим свойствам керамика AlN часто выбирается в качестве материала-кандидата для изолирующей подложки (прямая ширина запрещенной зоны ~6,015 эВ) для устройств и корпусов силовой электроники. Однако спекание AlN с высокой плотностью для эффективной теплопередачи и высокой механической прочности является сложной задачей из-за его высококовалентной и низкой диффузионной природы, что требует очень высоких температур спекания свыше 1900°C в восстановительной атмосфере при приложенном давлении, хотя он стабилен при температуре около 1000°С на воздухе.
Кроме того, ухудшение теплопроводности из-за включения кислорода является еще одной проблемой при изготовлении подложек из AlN с высокой теплопроводностью.
Много работ по продвижению уплотнения керамических тел AlN с использованием различных видов спекающих добавок, таких как CeO, Sm 2 O 3 , Y 2 O 3 , CaO, CaZrO 3 , и их кратные коприсоединения были исследованы [2, 3, 4, 5]. Некоторые из недавних результатов, показывающие теплопроводность, полученную в поликристаллических телах, составляют 90–156 Вт/мК, как показано в таблице 1, что намного ниже теоретического значения и сильно отличается друг от друга.AlN, легированный церием (CeO), продемонстрировал резкое увеличение теплопроводности и значительное увеличение механической прочности при небольшом количестве добавки (~ 1,5 мас.%) по сравнению с добавкой иттрия (Y 2 O 3 ) [2] . Метод высокоэнергетического спекания, такой как искровое плазменное спекание (ИПС), применялся [3, 4], а также традиционный метод твердофазной реакции (ТТР) [2] для эффективного процесса низкотемпературного уплотнения. Метод двухэтапного спекания также применялся с использованием разных температур для минимизации роста зерен и очистки зерен AlN [5] (рис. 1).
Химический состав | Разведающие добавки | Тепловая проводимость | Теплопроводность (W / MK) | Механические свойства | Темп спекания | Ref. | |
---|---|---|---|---|---|---|---|
ALN | 1.5 WT% CEO | 156 | 72,46 кг / мм | 2 | 1900 ° C / SSR | [2] | |
ALN | 2 WT% SM 2 O 3 | 120 | — | 1700 ° C / SPS | [3] | ||
ALN | Y 2 O 3 -CAO-B | 90 | — | 1650 ° C / SPS | [4] | [4] | |
ALN | CAZRO 3 -Y 2 O 3 | 156 | 560 MPA | 1550 ° C / Двухступенчатые | [5 ] |
Таблица 1.

Физические свойства керамики AlN с добавлением спекающих добавок и методы уплотнения.
Рис. 1.
Влияние легирования Ce и Y на теплопроводность и твердость керамики AlN [2].
2.1.2. Композиты AlN с GNP/GNS/rGO: электропроводящие
Наноструктурированные материалы на основе углерода, такие как графеновые нанопластинки (GNP) или нанолисты (GNS), были добавлены в матрицу AlN для улучшения физических свойств (таблица 2). Электропроводность увеличилась при добавлении многослойного графена, как и ожидалось, но теплопроводность уменьшилась при добавлении как в плоскости, так и в направлении сквозь плоскость, что противоречит другим данным по композитам керамика/графен.Такое резкое снижение теплопроводности в обоих направлениях, по-видимому, связано с большим термическим сопротивлением в тонкой зоне взаимодействия, существующей на границе между AlN и ЗНЧ [6]. Высокая направленность в плоскости и сквозной плоскости композитов AlN/GNP, 74 Вт/мК для плоскости и 37 Вт/мК для сквозной плоскости, приписывается тепловому контактному сопротивлению, существующему на обеих границах раздела фаз, которое сильное в перпендикулярном направлении теплопередачи графеновых нанопластинок [7]. Эту сильную направленность теплопередачи, теплопроводность, можно легко обнаружить в системе нитрид бора (BN)/полимерный композит, в которой используются наполнители BN с двумерной морфологией [9, 10, 11, 12, 13, 14, 15, 16].В случае восстановленного оксида графена (rGO) с добавлением AlN теплопроводность резко снизилась с 92,5 до 37,4 Вт/мК при добавлении 2 % масс. rGO, хотя наблюдается незначительное увеличение прочности на изгиб и вязкости разрушения при ≤1 % масс. rGO, что обусловлено низкой кристалличностью, большим количеством вакансионных дефектов в rGO и повышенным межфазным термическим сопротивлением [8]. Снижение теплопроводности композитов AlN с этими тремя двумерными наполнителями на основе углерода показало почти одинаковые результаты, поскольку GNP, GNS и rGO в основном имели одинаковую морфологию и физические свойства.
Материалы с высокой теплопроводностью и высокой направленностью теплопередачи могут использоваться в специальных приложениях для направленного рассеяния тепла в качестве материалов теплового интерфейса (TIM) (рис. 2 и 3).
Химический состав | Добавки | Добавки | Термальная проводимость (W / MK) | Механические свойства | Темп спекания | . 01OL% | 74 (в самолете) | 37 (через самолет) | — | 17001550 / SPS | [6] | ||
---|---|---|---|---|---|---|---|---|---|---|---|---|---|
ALN-2WT% Y 2 O 3 | GNS 1.49 Vol% | — | FS = 441 MPA | FT = 441 MPA FT = 441 MPA 1/2 | 1850 / Hot Press | [7] | |||||||
ALN | RGO 1 WT% | 92,5 — > 37,4 (2 мас. %) | FS = 375 МПа | 1550/SPS | [8] |
Таблица 2.

Физические свойства AlN с добавками углеродных наноматериалов.
FS: прочность на изгиб; FT: вязкость разрушения; SPS: Искровое плазменное спекание
Рис. 2.
Данные электропроводности (а) и теплопроводности переменного тока (б) с содержанием ЗНЧ в композитах AlN [6].
Рис. 3.
Вязкость разрушения и прочность на изгиб композитов AlN/GNS [7].
2.1.3. Si
3 N 4 базовая керамика Нитрид кремния (Si 3 N 4 ) керамика вызывает большой интерес в качестве диэлектрического материала с высокой теплопроводностью, используемого в изолированной металлической подложке (IMS) для силовой электроники. схемные модули. Теплопроводность композитов AlN–BN. Si 3 N 4 имеют ряд преимуществ: высокие механические свойства (прочность на изгиб >800 МПа, твердость по Виккерсу >10 ГПа), высокое удельное электрическое сопротивление и превосходные тепловые свойства с термостойкостью, высокая теплопроводность 70–180 Вт/ мК. Однако в действительности изготовление Si 3 N 4 с высокой теплопроводностью и высокой механической прочностью затруднено из-за трудностей уплотнения и морфологического контроля в микроструктуре. Типичными подходами для получения таких высокоэффективных Si 3 N 4 являются: (i) использование сырья с низким содержанием кислорода для удаления вакансий Si, вызывающих рассеяние фононов, (ii) изготовление керамики Si 3 N 4 с текстурированной микроструктурой для использования термической анизотропии в кристаллах Si 3 N 4 , (iii) использование неоксидных спекающих добавок с низким содержанием кислорода, чтобы избежать содержания кислорода в оксидной фазе, и (iv) выбор оптимальных добавок, которые могут минимизировать вакансии Si [9].
Некоторые из выбранных результатов, основанных на этих подходах, обобщены в таблице 4. Когда неоксидные добавки, такие как YF 3 , были добавлены к Si 3 N 4 с MgO вместо Y 2 O 3 , механические прочность и теплопроводность улучшены с 40 до 52; она была дополнительно увеличена до 75 Вт/мК после обработки отжигом при 1850°C. Однако твердость по Виккерсу несколько снизилась из-за большего размера частиц, чем при добавлении Y 2 O 3 [9].Теплопроводность Si 3 N 4 увеличилась до 100 Вт/мК при добавлении Yb 2 O 3 /SiO 2 и уменьшении диэлектрических потерь с 11,5 × 10 −4 9020 1,4 × 10 −4 (2 ГГц), регулируя соотношение от 0,33 до 1,3 [10]. Влияние условий азотирования и спекания на механические и термические свойства спеченного реакционно-связанного Si 3 N 4 (SRBSN) с добавками Y 2 O 3 -MgO, укрупнение размера и внешнего вида зерен Соотношение снижает твердость и вязкость разрушения при одновременном увеличении теплопроводности.
Твердость по Виккерсу 17,32 ГПа, вязкость разрушения 8,36 МПа·м 1/2 и теплопроводность 98,52 Вт/м·К были получены путем подбора азотирования и спекания под давлением газа (GPS) [11]. Проведено сравнительное исследование влияния оксидных и неоксидных добавок на микроструктуру, содержание кислорода в решетке и теплопроводность керамики Si 3 N 4 . Неоксидные добавки, такие как MgSiN 2 , YF 3 , YbF 3 , вызывали уменьшение количества вторичных фаз и содержания кислорода в решетке, тем самым увеличивая теплопроводность с 65 до 101.5 Вт/мК, в то время как прочность на изгиб существенно не изменилась [12].
Добавки Теплопроводность (Вт/мК) ALN-BN SM 2 O 3 -CAF 2 40-85 1800 / SPS [17] [17] ALN-BN (15%) Y 2 O 3 5 141 1800 / SPS [18] ALN-BN CAF 2 110 1850 / Hot-Press [19 ] (Ал-ОН)–БН ⊥14, //42. 5
1900/горячий пресс [20] Таблица 3.
Главный элемент 0 Сущному элементу Тепловая проводимость Теплопроводность (W / MK) Механические свойства Состояние спекания Ref. Si 3 N 4 YF 3 , MgO 52–75 4.7 9008 GPA 1750-1850 ° C / 20 MPA [9] Si 3 N 4 YB 2 O 3 , SIO 2 46-100 — 1900 ° C / 0.9 MPA [10] Si 3 N 4 Y 2 O 3 , MgO 98.52 — / 17. 52 GPA
1950 ° C / GPS [11] [11] [12] Si 3 N 4 MgO-Y 2 O 3 , MGSIN 2 -Y 2 O 3 , MGSIN 2 -YF 3 , MgO-YB 2 O 3 , MGSIN 2 , MGSIN 2 -YB 2 O 3 и MGSIN 2 -YBF 3 101.5 862 MPA 1800 ° C / 250 1800 ° C / 250 MPA [12] 9
2.1.4. Композиты на основе AlN-BN: электроизоляционные
Нитрид бора (BN) был введен в матрицу AlN для достижения низкой диэлектрической проницаемости и умеренной теплопроводности [17]. Нитрид бора (h-BN) имеет гексагональную структуру с хорошей устойчивостью к тепловому удару и высокой теплопроводностью, а также с предпочтительным направлением теплопередачи, т.е.е., анизотропия теплопроводности в плоскости и в плоскости подложки из-за двумерной формы чешуек BN или нанолистов BN. Плоскостная и сквозная теплопроводность составляет около 300 и 30 Вт/мК, а среднее кажущееся значение составляет 33 Вт/мК. h-BN имеет низкую диэлектрическую проницаемость и тангенс угла потерь, ε r = 4–4,6, тангенс δ = 0,0012–0,0017 на частоте 8,8 ГГц и диэлектрическую прочность при переменном токе = 67–95 кВ, которая варьируется в зависимости от чистоты. BN использовался во многих приложениях благодаря этим превосходным свойствам, например, в корпусах микроэлектроники, особенно в компонентах управления температурой, таких как радиаторы и подложки силовой электроники и т. д.Добавление BN к AlN также может улучшить химическую стойкость и влагостойкость, поскольку AlN может медленно гидролизоваться в воде (таблица 3).
В композитах AlN–BN с 8 мас.% Sm 2 O 3 -CaF 2 в качестве спекающей добавки самая высокая теплопроводность 85 Вт/мК и самый низкий тангенс угла потерь 4 × 10 −3 были достигнуты при температуре спекания 1800°С методом ИПС. Полученная теплопроводность была ниже, чем у чистого AlN, поскольку пластинчатые частицы BN, случайно распределенные по матрице AlN, препятствуют прямому контакту AlN, в результате чего рассеяние фононов подавляется [17].При добавлении оксида иттрия (Y 2 O 3 ) от 3 до 8 мас.% в композиты AlN–15%BN коэффициент теплопроводности увеличился со 110 до 140 Вт/мК, что связано со значительным снижением в остаточной зернограничной фазе, содержащей иттрий, методом ИПС [18]. Добавление CaF 2 и повышение температуры также улучшили уплотнение, теплопроводность и очистку границ зерен в системе AlN–BN. В результате была получена высокая теплопроводность 110 Вт/мК при добавлении 3 % масс. CaF 2 и спекании при 1850°C [19].В системе оксинитрид алюминия (γ-AlON)–BN, полученной методом самораспространяющегося высокотемпературного синтеза (СВС), зерна h-BN пластинчатой формы переориентируются в процессе горячего прессования, что приводит к анизотропии теплопроводность.
Теплопроводность композитов (γ-AlON)–BN составляла 14 Вт/мК для направления зерен BN в плоскости и 42,5 Вт/мК для направления в плоскости, которое перпендикулярно силе горячего прессования [20] (рис. 4). ).
Рис. 4.
Композиционная зависимость теплопроводности композитов в системе (γ-AlON)–BN, определенная перпендикулярно (а) и параллельно (б) силе прессования [20].
2.2. Композиты на полимерной матрице с керамическими наполнителями с высокой теплопроводностью
Композиты на полимерной матрице для упаковки с контролем температуры обычно наполняются керамикой с высокой теплопроводностью, такой как AlN, h-BN, и наполнителями на основе углерода, такими как углеродные нановолокна (УНТ), графитовые или графеновые нанолисты (GNS) и восстановленный оксид графена (rGO). Полимеры с системами керамического наполнителя AlN и h-BN в основном предпочтительны для высокой теплопроводности с электроизолирующими подложками теплопередачи или материалами теплового интерфейса (TIM) из-за высокой теплопроводности, низкой диэлектрической проницаемости и низких характеристик потерь керамики AlN и BN. С другой стороны, наполнители на основе углерода предпочтительнее в ТИМ, где разрешены электропроводящие характеристики.
2.2.1. Полимер: Композиты BN
В полимерных композитах, наполненных гексагональным нитридом бора (h-BN), основными проблемами, связанными с улучшением свойств теплопередачи, являются обработка поверхности пластинчатых частиц h-BN для улучшения дисперсии частиц наполнителя в полимерной матрице. ; снизить тепловое сопротивление интерфейса; и увеличить ориентирование частиц h-BN в предпочтительную ориентацию для достижения высокой направленной теплопроводности в композитах.В таблице 5 приведены некоторые технические усилия по улучшению теплопередающих свойств композитов полимер-BN [13, 14, 15, 16, 21, 22, 23, 24].
Состав | BN % | Теплопроводность (Вт/мК) | Метод выравнивания BN | Ref. | ||||||||||||||||||||||||||||||||||||||||||||||||||||||||||||||||||||||||||||||||||||||||||||||||||||||||||||||||||||||||||||||||||||||||||||||||||||||||||||||||||||||||||||||||||||||||||||||||||||||||||||||||||||||||||||||||||||||||||||||||||||||||||||||||||||||||||||||||||||||
---|---|---|---|---|---|---|---|---|---|---|---|---|---|---|---|---|---|---|---|---|---|---|---|---|---|---|---|---|---|---|---|---|---|---|---|---|---|---|---|---|---|---|---|---|---|---|---|---|---|---|---|---|---|---|---|---|---|---|---|---|---|---|---|---|---|---|---|---|---|---|---|---|---|---|---|---|---|---|---|---|---|---|---|---|---|---|---|---|---|---|---|---|---|---|---|---|---|---|---|---|---|---|---|---|---|---|---|---|---|---|---|---|---|---|---|---|---|---|---|---|---|---|---|---|---|---|---|---|---|---|---|---|---|---|---|---|---|---|---|---|---|---|---|---|---|---|---|---|---|---|---|---|---|---|---|---|---|---|---|---|---|---|---|---|---|---|---|---|---|---|---|---|---|---|---|---|---|---|---|---|---|---|---|---|---|---|---|---|---|---|---|---|---|---|---|---|---|---|---|---|---|---|---|---|---|---|---|---|---|---|---|---|---|---|---|---|---|---|---|---|---|---|---|---|---|---|---|---|---|---|---|---|---|---|---|---|---|---|---|---|---|---|---|---|---|---|---|---|---|---|---|---|---|---|---|---|---|---|---|---|---|---|---|---|---|---|---|---|---|---|---|---|---|---|---|---|---|---|---|---|---|---|
BN-Epoxy | 10-20 | 74% ↑ | Механические и магнитные | [13] | ||||||||||||||||||||||||||||||||||||||||||||||||||||||||||||||||||||||||||||||||||||||||||||||||||||||||||||||||||||||||||||||||||||||||||||||||||||||||||||||||||||||||||||||||||||||||||||||||||||||||||||||||||||||||||||||||||||||||||||||||||||||||||||||||||||||||||||||||||||||
BN-силиконовые | 20 | 250% ↑ | E-поле ( AC, DC) | [14] | ||||||||||||||||||||||||||||||||||||||||||||||||||||||||||||||||||||||||||||||||||||||||||||||||||||||||||||||||||||||||||||||||||||||||||||||||||||||||||||||||||||||||||||||||||||||||||||||||||||||||||||||||||||||||||||||||||||||||||||||||||||||||||||||||||||||||||||||||||||||
BN-Polysiloxane | 15 Vol% | 400% ↑ | AC / переключение DC | [15] | ||||||||||||||||||||||||||||||||||||||||||||||||||||||||||||||||||||||||||||||||||||||||||||||||||||||||||||||||||||||||||||||||||||||||||||||||||||||||||||||||||||||||||||||||||||||||||||||||||||||||||||||||||||||||||||||||||||||||||||||||||||||||||||||||||||||||||||||||||||||
BN-PVA | 27 об.![]() | 1.63 Вт/мК ⊥/8,44 Вт/мК// | Инфильтрация раствором ПВС | [16] | ||||||||||||||||||||||||||||||||||||||||||||||||||||||||||||||||||||||||||||||||||||||||||||||||||||||||||||||||||||||||||||||||||||||||||||||||||||||||||||||||||||||||||||||||||||||||||||||||||||||||||||||||||||||||||||||||||||||||||||||||||||||||||||||||||||||||||||||||||||||
БН-полиуретан-акрилат (ПУА) | 30 об.% 7 9 дюйм ≥ 7 плоскость | %↓(через плоскость) | е-поле (TiO 2 BN с покрытием) | [21] | ||||||||||||||||||||||||||||||||||||||||||||||||||||||||||||||||||||||||||||||||||||||||||||||||||||||||||||||||||||||||||||||||||||||||||||||||||||||||||||||||||||||||||||||||||||||||||||||||||||||||||||||||||||||||||||||||||||||||||||||||||||||||||||||||||||||||||||||||||||||
BN-PEN(поли(нитрид ариленового эфира)) 1005 9 9 9 9 9 9 9 9 9 0 1 9 % | Магнетик + комбинированная модификация, вдохновленная мидией (Fe 3 O 4 /PDA + KH550) | [22] | ||||||||||||||||||||||||||||||||||||||||||||||||||||||||||||||||||||||||||||||||||||||||||||||||||||||||||||||||||||||||||||||||||||||||||||||||||||||||||||||||||||||||||||||||||||||||||||||||||||||||||||||||||||||||||||||||||||||||||||||||||||||||||||||||||||||||||||||||||||||||
BN | 3,00125
49 Вт/мК(45,4%) | Силановые аппреты с различной углеродной цепью | [23] | |
БН-ПВА | 50% об. | 1,1 Вт/мК 900м/16 Вт/13 Механическое расслоение, сжатие | [24] |
Таблица 5.
Примеры теплопроводности композитов полимер-BN.
Комбинированный метод, использующий механическую вибрацию и вращающееся магнитное поле, индуцированное высокой степенью выравнивания композита с 10 % наполнителем, показал улучшение теплопроводности на 74 % по сравнению с невыровненным образцом за счет образования проводящей сети и снижения теплового граничного сопротивления. .Снижение теплового граничного сопротивления между h-BN и смолой на основе бисфенола-А было вызвано высокой степенью выравнивания пластинок h-BN посредством комбинированного процесса [13].
Исследовано влияние электрических полей переменного и постоянного тока на анизотропно выровненную микроструктуру в композитах силиконового каучука, наполненных h-BN. Было обнаружено, что степень переориентации h-BN была более эффективной в условиях переменного, чем постоянного поля, в процессе отверждения композита h-BN-силикон (рис. 5), а теплопроводность е-поля композит с вспомогательным отверждением был примерно на 250% выше, чем у композита, отвержденного без E -поля [14].В недавнем исследовании наибольшее общее количество линейных плотно упакованных нанолистов BN (LDPBN) было сформировано при приложении поля переменного тока, а утолщение LDPBN и сужение промежутков между частицами были достигнуты за счет применения переключающего поля постоянного тока (рис. 6). В результате теплопроводность увеличилась в четыре раза по сравнению с композитом без структуры LDPBN [15].
Рис. 5.
Теплопроводность композитов BN/силикон при различных объемных долях [14].
Рис. 6.
Схематическая модель генерации путей более высокой проводимости через LDPBN с использованием различных приложений электрических полей [15].
Гибкая композитная лента h-BN/поли(виниловый спирт) была изготовлена путем пропитки раствора поли(винилового спирта) (ПВС) в пакет h-BN с вакуумной фильтрацией для уменьшения зазора между частицами h-BN и для повышения степени выравнивания h-BN тромбоцитов. Плоскостная и сквозная теплопроводность полученных таким образом композитов h-BN/PVA составила 1.63 и 8,44 Вт/мК соответственно [16]. В той же системе h-BN/ПВС степень ориентации пластинчатых частиц h-BN может быть улучшена литьем под давлением [24], где степень ориентации частиц h-BN можно наблюдать по характерным пикам в данных рентгеновской дифракции (XRD). Чтобы улучшить выравнивание частиц h-BN, также исследуется покрытие чувствительными к электрическому или магнитному полю материалами, такими как керамика TiO 2 или Fe 3 O 4 , на частицы h-BN для улучшения теплопроводность [21, 23].Частицы h-BN, покрытые TiO 2 золь-гель процессом, были выровнены в вертикальном направлении по отношению к приложенному полю, так что теплопроводность композита h-BN/полиуретан-акрилат (PUA) в сквозной плоскости увеличилась на 190 %, а плоскостная теплопроводность композита снизилась на 72% по сравнению с необработанным композитом h-BN [21]. Композиты h-BN/поли(ариленэфирнитрил) (PEN) с высокой диэлектрической проницаемостью и высокой теплопроводностью были разработаны путем магнитного выравнивания h-BN через покрытие из магнитных частиц Fe 3 O 4 вместе с дополнительной модификацией поверхности. полидофамином (PDA) и функциональным мономером KH550: (3-аминопропил)триэтоксисилан).Эти модификации поверхности улучшили дисперсию наполнителей h-BN в матрице PEN и межфазную адгезию.
В композитной системе BN/Fe 3 O 4 /PDA + KH550/PEN как диэлектрическая проницаемость, так и тангенс угла потерь были значительно увеличены с количеством BN/Fe 3 O 4 /PDA + KH550, и теплопроводность увеличилась на 140% по сравнению с чистой пленкой ПЭН [22]. Было исследовано повышение теплопроводности в композитах h-BN/эпоксидная смола за счет модификации поверхности частиц h-BN с помощью силановых связующих агентов с различной углеродной цепью.Теплопроводность композита h-BN/эпоксидная смола улучшилась на 45,4 % благодаря лучшему диспергированию h-BN в эпоксидной смоле по сравнению с необработанным h-BN, что связано с более высоким межфазным сродством композита, полученного при использовании более длинной углеродной цепи силана. на поверхности h-BN [23] (рис. 7, 8, 9).
Рис. 7.
Теплопроводность композита h-BN/PUA и композита h-BN/PUA с покрытием TiO 2 с покрытием h-BN/PUA до и после выравнивания электрического поля: (a) сквозная и (b) плоскостная теплопроводность [21].
Рис. 8.
Теплопроводность чистого ПЭН и BN/Fe 3 O 4 /ПДА + КХ550/ПЭН композиционных пленок с различным содержанием наполнителя [22].
Рис. 9.
Теплопроводность композитов h-BN/эпоксид с необработанным BN, MPCB (Al 2 O 3 /эпоксид), силан (C3)/BN и силан (C16)/BN [23 ].
Исследовано влияние размеров частиц h-BN, расслоения частиц BN и сжатия композитов h-BN/ПВС на поведение теплопроводности [24].На рис. 10(а) показано, что теплопроводность композитов h-BN/PVA увеличилась почти в два раза, когда исходные хлопья h-BN расслаиваются в тонкий нанолист h-BN. Кроме того, частицы h-BN меньшего размера проявляли более высокую теплопроводность в композитах h-BN/PVA, как показано на рисунке 10(b). Дальнейшее повышение теплопроводности композитов h-BN/ПВС было реализовано за счет одноосного термического сжатия после литья из раствора композитной пленки h-BN/ПВС при температуре 90°С, что выше температуры стеклования полимера ПВС.На рисунке 11 показаны микрофотографии FE-SEM поперечных сечений композитов 30 об.% h-BN/ПВС до (а) и после сжатия, которые ясно показывают выравнивание частиц h-BN перпендикулярно направлению прессования (b). Сквозная (поперечная) плоскость и плоскостная теплопроводность, измеренная методом лазерной вспышки, показаны вместе с теоретическим моделированием на рисунке 12. Две модели, арифметическая и модель Винера, используются для расчета двухфазной композитной системы со следующими уравнения.
Рис. 10.
Влияние механического расслоения (а) и размеров частиц h-BN (b) на теплопроводность композитов h-BN/ПВС в сквозной плоскости [24].
Рис. 11.
Виды в поперечном сечении композитных пленок 30 об.% h-BN/ПВС, полученные с помощью FE-SEM: (а) несжатые и (б) сжатые [24].
Рис. 12.
Влияние одноосного сжатия на поперечную и плоскостную теплопроводность композиционных пленок h-BN/ПВС: (а) несжатый и (б) сжатый образцы [24].
арифметическая модель:
λ = Cλ1 + 1-Cλ2e1
, где C = доля компонента 1.
1 -C = доля компонента 2
λ 1 , λ 2 = теплопроводность компонента 1, 2.
Модель Винера:
λ/λ2=1−c1−λ1/λ2/1+αλ1/λ2/1+αc1−λ1/λ2/1+αλ1/λ2E2
, где , α = 0,5 для дисперсионной модели, λ 1 < λ 2 .
В этом расчете теплопроводность ПВС и h-BN была принята равной 0.2 и 33 Вт/мК соответственно. Плоскостные, перпендикулярные направлению сжатия теплопроводности были в 5 раз выше, чем сквозные у несжатых образцов, и имели значения в 10 раз выше у сжатых образцов. Наибольшая теплопроводность, полученная при наполнении композита ПВС 50 об.% h-BN, составила 13 Вт/мК в плоскостном режиме, а теплопроводность сквозного режима составила около 1,1 Вт/мК, что ниже, чем у несжатого образца [ 24]. Уменьшение теплопроводности в сквозной моде в композитах h-BN/PVA связано с уменьшением контакта частиц в сквозной плоскости за счет выравнивания пластин h-BN параллельно направлению в плоскости, что приводит к увеличению плоскостные теплопроводящие пути и уменьшающиеся сквозные теплопроводящие пути.Модель Винера кажется более близкой к экспериментальным данным, чем арифметическая модель, но разрыв между этими теоретическими и экспериментальными данными велик, что указывает на то, что все еще остается много факторов, которые необходимо улучшить для достижения оптимальных условий при изготовлении полимерно-керамических композитов. высокая теплопроводность.
Таким образом, было исследовано несколько методов повышения теплопроводности композитов h-BN/полимер. Примерами являются (i) модификация поверхности частиц h-BN функциональными органическими соединениями для улучшения сродства и дисперсии раствора h-BN/PVA, (ii) покрытие частиц h-BN диэлектрическими и феррокерамическими материалами для повышения эффективности выравнивания. с приложением электрического и магнитного поля, (iii) расслоение хлопьев h-BN в тонкие нанолисты h-BN для лучшего соединения частиц при заданной загрузке наполнителя и (iv) механическое сжатие для обеспечения выравнивания частиц и межчастичного контакта.
2.2.2. Полимер: композиты AlN
Нитрид алюминия (AlN) является приоритетным выбором в качестве наполнителя в полимерно-керамических композитах с высокой теплопроводностью, поскольку он обладает высокой теплопроводностью (320 Вт/мК, теоретическая), хорошими изоляционными свойствами (удельное электрическое сопротивление > 10 14 Ом·см), низкой диэлектрической проницаемостью (2,2–3,7 при 1 МГц) и низким КТР (4,4 ppm/°C), близким к кремнию. В горячепрессованных композитах AlN/ПММА (полиметилметакрилат) теплопроводность 1.87 Вт/мК было получено при наполнении композита 70 об.% AlN, что примерно в 10 раз выше, чем у смолы ПММА (0,18 Вт/мК), как показано на рисунке 13(а). Диэлектрическая проницаемость и потери композита составляли 4,4 (рис. 13(b)) и 0,017 на частоте 1 МГц [25]. В композитах полипропилен (ПП)/AlN с трехмерной сегрегированной структурой, изготовленных путем механического измельчения смеси ПП и AlN с последующим горячим прессованием при 190°С, были получены композиты ПП/AlN со структурой ядро-оболочка. Сравнительные результаты этого композита с трехмерной структурой сердцевина-оболочка с обычными композитами, смешанными в растворе и расплаве, показали, что этот механически измельченный композит с 10 об.% AlN показал теплопроводность на 23 % выше, чем другие [26].Теплопроводность насыщенного нитридом алюминия жидкого раствора поли(пропиленгликоля) (ППГ) также была изучена, и результаты показали, что теплопроводность жидкостей AlN/ППГ зависела от содержания твердых частиц AlN и молекулярной массы ППГ [27].
Рис. 13.
Экспериментальные и расчетные данные теплопроводности композитов ПММА/AlN с варьированием наполнителей AlN [25].
Таким образом, несмотря на усилия по увеличению теплопроводности в полимерно-керамических композитах, теплопроводность, полученная в композитах с керамическим наполнителем на полимерной матрице, все еще намного ниже, чем у полностью керамических базовых материалов из-за низкой теплопроводности в полимерной матрице. что ограничено в улучшении теплопроводности, когда они являются электроизоляционными.Таким образом, требуется дальнейшая разработка полимеров с высокой теплопроводностью с электроизоляцией для получения максимально высокой теплопроводности в полимерно-керамических композитах, поскольку теплопроводность керамики-наполнителя, скорее всего, зависит от их собственной природы и вряд ли изменено материаловедением и инженерными манипуляциями.
2.3. Керамика LTCC с высокой теплопроводностью
Низкотемпературная керамика совместного обжига (LTCC) имеет ряд преимуществ при использовании в корпусах микроэлектроники.Типичная температура спекания LTCC ниже 1000°C, поэтому их можно обжигать совместно с электродами с высокой проводимостью, такими как серебро (Ag) или медь (Cu). Большинство современных материалов LTCC состоят из низкотемпературной плавящейся стеклянной матрицы и керамических наполнителей для функциональной регулировки, таких как электрические, механические и термические свойства, в зависимости от требований применения. Следовательно, LTCC иногда называют стеклокерамикой, но технически LTCC является частью стеклокерамических композитов. Например, в области высокочастотных (РЧ, микроволновых и миллиметровых волн) устройств и упаковочных подложек керамический порошок с низкими потерями и низкой диэлектрической проницаемостью, такой как порошок оксида алюминия (Al 2 O 3 ), добавляется к низкому стеклянная матрица с потерями. В результате в процессе термообработки выделяются вторичные фазы из-за того, что часть частиц алюмооксидного наполнителя вступает в реакцию со стеклянной матрицей. Интересно, что эти вторичные фазы способствуют улучшению диэлектрических свойств и механической прочности при правильном выборе частиц наполнителя и состава матрицы. LTCC использовался во многих приложениях благодаря экономии энергии в процессе низкотемпературного спекания, отличным диэлектрическим свойствам и простоте интеграции и миниатюризации в 3D.Примерами являются модуль радиочастотной системы в корпусе (RF-SiP), пакеты светодиодов, высокотемпературные датчики, корпус микроэлектромеханической системы (MEMS), микронагреватели, микрофлюидика и т. д. [28, 29, 30, 31, 32, 33, 34, 35, 36, 37, 38].
2.3.1. Система LTCC со стеклокерамическим основанием
В последнее время использование высокой теплопроводности с изолирующей керамической подложкой быстро расширяется для улучшения свойств теплопередачи встроенных электронных устройств и корпусов. Поскольку обычные LTCC основаны на системе стекломатричного керамического композита (GMC) с низкой теплопроводностью стеклофазы (1–2 Вт/м·К), теплопроводность большинства LTCC составляет всего 2–5 Вт/м·К, а показано в таблице 6 [38, 39, 40, 41, 42, 43, 44], что все еще выше, чем FR-4 (обычно 0.1–0,2 Вт/мК), но намного ниже, чем у объемной керамики с высокой теплопроводностью, такой как оксид алюминия, AlN или Si 3 N 4 .
9 Состав Chimatic Композиция | Температура спекания | Темп (° C) | Термальная проводимость (W / MK) | CTE (PPM / ° C CTE ) | Диэлектрическая проницаемость | Диэлектрические потери | Ref. | |
---|---|---|---|---|---|---|---|---|
Коммерческие продукты | ESL41110-70C | — | 2.![]() | 6.4 | 4.3 | 0.004 | [37, 38] | |
850 | 850 | 3 | 5.6 | 9.1 | 0.002 | [37, 39] | ||
DuPont 951 | 850 | 3.2-3.9 | 5.8 | 70016 | [37, 40] | [37, 40] | ||
Dupont 9K7 | 850 | 4.6 | 4.4 | 7.1 | 0.001 | [37, 41] | ||
Дюпон 943 | 850 | 4.4 | 6 | 70015 | 0.002 | [37, 42] | ||
Ferro A6 | 850 | 2 | 7 | 5.9 | 0,002 | [37, 43] | ||
Murata | 850 | 2.5 | 5.5 | 70015 | — | [37, 44] | ||
Научно-исследовательские работы | MgO-Cao-Al 2 O 3 -Sio 2 | 900 | 1.![]() | 8 | — | — | [33, 45] | |
AL2O 3 -BBSZ Стекло | 850 | 7.2 | 6.9 | 10.9 | 0,009 | [46] | ||
ZNTIO 3 -B 2 O 3 | 6.6 | — | 20 | 0,001 | [47] | |||
ABS-MWCNT | — | 2.2 | — | — | — | [48] | ||
CAS + β-Si 3 N 4 5 15016 80016 | 9— | 7.1 | 0,006 | [49] | ||||
LZT-LMZBS | 900 | 5.8 | 5.8 | — | [50] | |||
STALL-DIRAME | 750 | 9.01 | 4.35 | — | — | [51] | ||
AL 24 AL 2 O 3 / Стекло + ALN Усы / из углеродного волокна / из медного волокна | 850 | 38. | ![]() 4.6-6 .1 | 6.6-7.4 | — | [52] | | |
Borosilicate Glass-Aln-β-Si 3 N 4 | 850 | 18.8 | 4.2-4.4 | 6.5 | 0.0016 | [53] |
Таблица 6.
Физические свойства коммерческих LTCC систем и некоторые из последних исследований стеклокерамики с высокой теплопроводностью.
BBSZ: BI 2 O 3 -ZNO-B 2 O 3 -SIO 2 , ABS: AL 2 O 3 -B 2 O 3 -Sio 2 , CAS: CaO-AL 2 O 3 , LZIO 2 , LZT: LI 2 ZNTI 3 O 8 , LMZBS: LI 2 O-MgO-Zno-B 2 O 3 –SiO 2
Повышение теплопроводности в стеклокерамической системе может быть реализовано рекристаллизацией, добавлением наполнителей с высокой теплопроводностью, таких как Al 2 O 3 , AlN и Si 3 N 4 частиц. Различные типы морфологии частиц наполнителя, такие как пластинчатые и волокнистые типы, используются для улучшения межчастичных контактов, снижения межфазного теплового сопротивления и адаптации направленности теплопередачи в подложке. Также исследуются микроструктурные манипуляции, такие как переориентация частиц наполнителя, низкая теплопроводность, удаление вторичной фазы и контроль границ зерен. Среди них некоторые ключевые исследовательские работы приведены в таблице 6 [33, 45, 46, 47, 48, 49, 50, 51, 52, 53].
В наполненной оксидом алюминия (Al 2 O 3 ) стеклокерамической системе MgO–CaO–Al 2 O 3 –SiO 2 добавка оксида алюминия снижала теплопроводность стекла – керамика, где фаза диопсида или анортита является основной рекристаллизованной вторичной фазой, как показано на рисунке 14.Теплопроводность стеклокерамики на основе диопсида и анортита, спеченной при температуре <1000 °С, составляет 2,37 и 2,35 Вт/мК соответственно. Установлено, что кристалличность является более важным фактором, чем соотношение диопозида и анортита, так что наибольшая прочность на изгиб и теплопроводность получены у образцов с высокой кристалличностью, поскольку основные пиковые интенсивности на рентгенограммах стеклокерамики линейно пропорциональна [33, 45]. В системе стекла 40 % оксида алюминия–60 % масс. BSSZ (Bi 2 O 3 –ZnO–B 2 O 3 –SiO 2 ) [46] теплопроводность составляет 7.2 Вт/мК необычно высока по сравнению с ранее известной стеклокерамикой [38, 39, 40, 41, 42, 43, 44] с высокой диэлектрической проницаемостью 10,9 и низкими потерями 0,009 на спеченной ленте.
Рис. 14.
Зависимости теплопроводности для MgO–CaO–SiO 2 –Al 2 O 3 стеклокерамическая система на Al 2 O 3 добавка 4s [, ].
Алюмоборосиликатная (АБС) стеклокерамика, содержащая ≤15% масс. многостенных углеродных нанотрубок (МУНТ), показала улучшение электропроводности на ~10 6 и теплопроводность на ~70%.Максимальная электропроводность 2,1 См/см была получена при добавлении 15 % масс. МУНТ к LTCC на основе АБС, в то время как у чистого АБС она составляла всего ~10 90 202 -6 90 203 См/см. Порог перколяции существует в области добавления 2,5–5% масс. МУНТ из-за равномерного рассеивания МУНТ до 10% масс., что является относительно более высокой скоростью загрузки, чем другие [48] (рис. 15).
Рис. 15.
Тепло- и электропроводность с содержанием МУНТ для нанокомпозитов АБС–МУНТ [48].
В системе стекла из алюмосиликата кальция (CAS) теплопроводность была увеличена с 1.от 6 до 7,9 Вт/мК при добавлении 35 об.% β-Si 3 N 4 вискеров, добавленных к композитам CAS–Si 3 N 4 , спеченным при 775–850°C на воздухе (рис. 16 ) . Эта теплопроводность намного выше, чем у других систем LTCC, о которых сообщалось [38, 39, 40, 41, 42, 43, 44, 46, 47, 50]. Однако теплопроводность снижалась, когда загрузка нитевидных кристаллов β-Si 3 N 4 превышала 35% масс. Диэлектрическая проницаемость и потери, измеренные на частоте 1 МГц, составили 7,1 и 0.006 соответственно [49].
Рис. 16.
Экспериментальные данные и теоретическая кривая теплопроводности композитов CAS–Si 3 N 4 в зависимости от содержания β-Si 3 N 4 [49].
LI 2 ZNTI 3 O 8 (LZT) Система с 1 мас.% LMZBS (LI 2 O: MgO: ZnO: B 2 O 3 : SIO 2 = 1:1:1:1:1) в качестве добавки для спекания, теплопроводность 5.8 Вт/мК и КТР 11,97 частей на миллион/°C были получены на образцах, спеченных при 875°C. Высокая диэлектрическая проницаемость и потери системы ЛЗТ-ЛМЗБС на частоте 1 МГц составили 24,14 и 5,1 × 10 -4 соответственно. Микроволновые диэлектрические свойства спеченной ленты, измеренные с помощью метода разделенного диэлектрического резонатора (SPDR), составили ε r = 21,9, тангенс δ = 6 × 10 −4 при 5 ГГц и τ ε при −29 ppm/°. С [50] (рис. 17).
Рис. 17.
Данные измерения теплопроводности LZT + LMZBS, объемно спеченного при 900°C [50].
Исследована стеклокерамика, наполненная частицами монокристаллического алмаза размером 3–40 мкм, и результаты показали наибольшую теплопроводность стеклоалмазных композитов с алмазами размером 30 мкм, которые спекались при 750 °С и показали самый низкий КТР, самый высокий теплопроводность и прочность на изгиб: 4,35 ppm/°C, 9,01 Вт/мK и 108,25 МПа [51] (рис. 18).
Рис. 18.
Теплопроводность (а), КТР (б) и прочность на изгиб (в) стеклоалмазных НТПК, спеченных при 750°С [51].
Было изучено добавление одномерных материалов, таких как нитевидные кристаллы AlN, углеродные волокна и медные волокна, к композитам оксид алюминия/30 об.% стекла. Добавление нитевидных кристаллов AlN не улучшало теплопроводность по сравнению с добавлением порошка AlN, а волокнистые наполнители более эффективно увеличивали теплопроводность композитов. Самая высокая теплопроводность, полученная в этих композитах, была Al 2 O 3 /стекло с 30 об.% медных волокон, которые спекались при 850 °C, как показано на рисунке 19 [52].Удельное сопротивление Al 2 O 3 /30 % стекла и Al 2 O 3 /30 % стекла/30 %AlN-вискеров составляет 2,0–2,1 × 10 12 Ом·см, а у Композиты с добавлением 30 % углеродного волокна и 30 % медного волокна имели 8,7 × 10 90 202 -3 90 203 и 3,4 × 10 90 202 -6 90 203 Ом·см соответственно. Следовательно, эти два электропроводящих композита не применимы в качестве электроизоляционного терморегулирующего материала, или они могут быть покрыты слоем изолирующего стекла на поверхности для улучшения удельного электрического сопротивления [52].
Рис. 19.
Изменение теплопроводности композитов Al 2 O 3 /стекло с добавлением одномерного наполнителя [52].
В композите боросиликатного стекла и AlN LTCC теплопроводность была увеличена с 11,9 до 18,8 Вт/мК за счет добавления 14 об.% β-Si 3 N 4 вискеров, как показано на рисунке 20. проводимость может быть связана с образованием пути теплопроводности за счет мостиков изолированных частиц AlN через β-Si 3 N 4 вискеры.Диэлектрические свойства этих композитов составляют ε r = 6,5 и тангенс δ = 0,0016 на частоте 1 МГц, и значения существенно не изменяются с количеством нитевидных кристаллов из-за сходства их диэлектрических свойств между AlN и Si 3 N 4 [53].
Рис. 20.
(а) Экспериментальные данные и теоретическая кривая теплопроводности керамических композитов CMBS–AlN–Si 3 N 4 в зависимости от β-Si 3 N 4 вискер объемная доля и (б) относительная диэлектрическая проницаемость и диэлектрические потери керамических композитов CMBS-AlN-Si 3 N 4 в зависимости от объемной доли β-Si 3 N 4 [53].
2.3.2. Система LTCC без стекла
Системы LTCC без стекла или без стекла были исследованы для снижения сложности систем LTCC из-за включения нескольких фаз, таких как стекло, частицы наполнителя и дополнительные добавки для спекания. Из-за их сложности возникло несколько проблем при подготовке схем LTCC и устройств в интегральном электронном модуле. Чтобы преодолеть эту сложность химического взаимодействия, неоднородные диэлектрические свойства и трудности диспергирования суспензии, были разработаны системы LTCC с простыми фазовыми компонентами [54, 55, 56, 57, 58, 59, 60] (табл. 7).
Химический состав | Темп спекания (° C) | Термальная проводимость (W / MK) | CTE (PPM / ° C) | Диэлектрическая постоянная | Tan | δ/ Q-фактор | Реактивность с электродом | Ref. | |
---|---|---|---|---|---|---|---|---|---|
CAO- (GEO 2 , SIO 2 , TEO 2 ) | 780-1200 | — | — | 6.5 ~ 19.3 | 2,4 × 10 | ~ 1 × 10 -4 3 (MHZ) | N (AG: Германизы, силикат) | [54] | |
AMPO 2 O 7 (a = ca, sr., m = zn, cu) | 950 | — | — | 7.06 | 52871 | 52 871 | y (ГГц) | y (AG) N (CU) ) | [55] |
LiMgPO 4 | 950 | 7,1 | 10,5 | 6.![]() | 0,0002 | — | [56] | ||
BI 4 (SIO 4 ) 3 | 900 | 2,82 | 70015 | 13.3 | 0,0007 | (15 ГГц) | — | [57] | |
LI 2 мг 2 Ti 3 O 8 | 925 | — | 0,45 (τf) | 27 | 58 480 | ||||
N(Ag) | [58] | ||||||||
Li 2.08 TIO 3 -lif 16 | 4.75 | 22.4 | 22.4 | 35 490 | (GHZ) | N (AG) | [59] | | |
11ZNO-10MOO 3 | 850 | 1.3 | 4,7 | 11.1 | — | — | [60] |
Таблица 70077
Композиции и физические свойства стеклянных систем LTCC.
В традиционной системе LTCC стекло использовалось в качестве матричной фазы для снижения температуры спекания ниже 1000°C, поскольку функциональные диэлектрические керамические материалы в основном полностью уплотнялись при высоких температурах спекания, выше 1200°C, когда металлы с высокой электропроводностью такие как Ag или Cu, нельзя использовать в качестве согласующего электрода. LTCC, содержащие стеклофазную матрицу, как правило, проявляли низкую теплопроводность, как мы видели в таблице 6. В LTCC без стекла основным требованием является снижение температуры спекания ниже 1000°C без введения вторичных фаз, за исключением небольшого содержания спекающего агента. Поиск низкотемпературного синтеза и низкотемпературного плавления керамического соединения с кристаллической фазой является ключевым моментом для разработки LTCC, не содержащих стекла. Композиции LTCC, не содержащие стекла, применимые в промышленности с доказанными механическими свойствами и надежностью, почти не встречаются, несмотря на то, что сообщалось о нескольких первичных результатах исследований, показывающих отличные диэлектрические свойства [54, 55, 56, 57, 58, 59, 60].Существенными проблемами, обнаруженными в предыдущих системах LTCC без стекла, являются низкая механическая прочность, реактивность с соответствующими электродными материалами во время термообработки и уязвимость во влажной среде.
В системе проростков кальция и силикатов диэлектрические проницаемости составляли 6,5–10,8, добротность (Q × f) = 16 000–39 000 (при частоте 10 ГГц), температурные коэффициенты диэлектрической проницаемости составляли 70–140 миллионных долей/°C для образцов. спекаются при 1180–1200°C, что несколько выше температуры для обработки LTCC.Эти системы не проявляли никакой химической реакции с Ag-электродом. С другой стороны, в системе теллуратов кальция диэлектрические проницаемости составляли 15,5–23,6, Q × f = 13 400–49 300 (~10 ГГц), температурные коэффициенты диэлектрической проницаемости составляли 130–140 м.д./°С для образцов, спеченных при 780 –840°С; но эта система была уязвима на Ag-электроде. Высокотемпературные коэффициенты диэлектрической проницаемости подавляли добавлением 10 мол.% CaTiO 3 [54].
Для AMP 2 O 7 (A = Ca, Sr.; B = Zn, Cu), все соединения реагировали с Ag, но могут быть подвергнуты совместному обжигу с Cu в пониженной атмосфере. Среди них SrZnP 2 O 7 , спеченный при 950 °C, показал диэлектрическую проницаемость 7,06, Q × f = 52 781 ГГц и температурный коэффициент резонансной частоты (τ f ) = -70 млн/°C; следовательно, это соединение может быть преобразовано в термостабильную композицию, если к нему смешать соответствующий противодиэлектрический материал с отрицательным температурным коэффициентом. Теплопроводность этой системы не приводилась [55].
В ленте LiMgPO 4 , спеченной при 950 °C, микроволновые диэлектрические свойства составили: ε r = 6,4, tan δ = 0,0002, КТР = 10,5 млн/°C, а теплопроводность составила 7,1 Вт/м·К. , что в 2 раза выше, чем у обычных LTCC на стеклокерамической основе. Микроволновые диэлектрические свойства спеченной ленты измерялись с использованием метода расщепленного диэлектрического резонатора (SPDR), соединенного с векторным анализатором цепей [56].
Bi 4 (SiO 4 ) 3 Ленточная система LTCC без стекла показала диэлектрическую проницаемость 13. 3, потери (тангенс δ) 0,0007 на частоте 15 ГГц и теплопроводность 2,82 Вт/мК [57]. Не содержащая стекла керамика Li 2 MgTi 3 O 8 , спеченная при 925 °C, показала диэлектрическую проницаемость 27, значение Q × f 58 480 ГГц (при 5,8 ГГц) и очень стабильный температурный коэффициент резонансной частоты. τ f = 0,45 млн/°C. Эта система совместима с серебряным электродом [58]. Другой LTCC без стекла на основе лития представляет собой систему Li 2,08 TiO 3 –LiF, где микроволновые диэлектрические свойства ε r = 22.4, Q × f = 35 490 ГГц были получены при спекании ленты при 900 °C. КТР и теплопроводность системы составляли 22,4 ppm/°C и 4,75 Вт/мK соответственно. Система также совместима с серебряным электродом и имеет высокий коэффициент изоляции 50 кВ/мм, что имеет потенциал в приложениях большой мощности. Для вышеупомянутой системы без стекла полученные значения теплопроводности составляют 2,28–7,1 Вт/мК, что значительно выше, чем у большинства обычных LTCC на основе стеклокерамики [59].
Молибдат цинка с 1 % В 2 О 3 , спеченный при 850–900°С, имел диэлектрическую проницаемость 11.1 КТР 4,7 ppm/°C и напряжение пробоя 17,6 кВ/мм. Однако теплопроводность была относительно низкой, 1,4 Вт/мК, по сравнению с другими LTCC без стекла. Эта система может быть применима к высокотемпературным изолирующим диэлектрикам из-за низкого КТР и высокого напряжения пробоя [60].
Однако, несмотря на превосходные диэлектрические и термические свойства, некоторые не содержащие стекла соединения LTCC, содержащие элемент лития, имеют проблемы с растворимостью в воде, что ограничивает их применение. Поэтому им может потребоваться защитный слой покрытия, чтобы противостоять атмосферным воздействиям.
3. Резюме и перспективы на будущее
В этой главе кратко рассматриваются последние исследования и разработки в области керамики с высокой теплопроводностью и их композитов для терморегуляции интегрированных электронных блоков. Ключевые уроки, извлеченные из этих предыдущих работ, можно резюмировать следующим образом:
3.

Наиболее часто встречающаяся керамика с высокой теплопроводностью на основе HTCC представляет собой глиноземную и нитридную керамику, такую как материалы AlN, BN и Si 3 N 4 .Среди них керамика на основе нитрида кремния кажется наиболее часто используемой в силовой электронике в наши дни. В нитридах и композитах с керамической матрицей ключевыми параметрами, которые контролируют термические свойства, являются уплотнение, включая удаление пор, размер зерна и контроль границ зерен, примеси и контроль вторичной фазы. Среди них уплотнение является основным фактором для достижения высокой теплопроводности благодаря высокому термическому сопротивлению пор. Эту нитридную керамику трудно спекать с высокой плотностью, поэтому для достижения высокой плотности следует применять методы искрового плазменного спекания и двухстадийного спекания вместе с добавлением небольшого количества спекающих добавок.В нитридной керамике контроль содержания кислорода является очень важным фактором в дополнение к параметрам, требуемым для оксидных материалов.
В материалах на основе LTCC имеется много исследовательских работ по разработке материалов LTCC с высокой механической прочностью, но мало работ по улучшению теплопроводности LTCC. Некоторые работы, найденные в литературе, в основном касаются перекристаллизации и фазового контроля в матрице и показывают лишь незначительное улучшение термических свойств по сравнению с заметным улучшением механических свойств.Основная причина этого незначительного изменения тепловых свойств в обычном стеклокерамическом LTCC связана со стеклянной матрицей, которая составляет более половины объема спеченного тела. Объемная доля новообразованных нанокристаллических фаз в процессе термообработки настолько мала, что общая кажущаяся теплопроводность может существенно не измениться, в то время как механическая прочность может быть легко повышена за счет включения нанокристаллической фазы в матрицу.
В теплопроводных и электропроводных керамических композитах электропроводность была улучшена за счет добавления двумерных аллотропов углерода, таких как графеновые нанолисты/пластинки; однако теплопроводность снижалась при участии графена в матрице AlN, что может быть связано с наличием тонкого слоя взаимодействия на границе раздела AlN–GNS/GNP, вызывающего термическое сопротивление. Наблюдалась большая разница между плоскостной и сквозной теплопроводностью композитов, которую можно наблюдать в композитах полимер/графен.
3.2. Композиты с полимерной матрицей с высокой теплопроводностью
Композиты с полимерной матрицей с высокой теплопроводностью и электроизоляционными керамическими наполнителями в основном используются для диэлектрических изоляционных слоев в подложке упаковки светодиодов для эффективного отвода тепла к металлическим теплораспределяющим панелям.Наиболее часто используемыми изолирующими керамическими наполнителями являются порошки оксида алюминия, BN и AlN. Среди них предпочтительны пластинчатые порошки BN из-за анизотропного поведения теплопроводности в двумерной структуре кристалла BN. Многие исследования были сосредоточены на индивидуальной переориентации нанолистов BN в растворе BN/полимер в плоскость или сквозь плоскость композиционной ленты BN/полимер с использованием магнитного и электрического поля в процессе литья. Кроме того, предпринимаются некоторые усилия по нанесению наночастиц железа или диэлектрика на частицы тромбоцитов BN, чтобы способствовать легкому выравниванию частиц тромбоцитов BN в заданном направлении. Модификация поверхности частиц BN функциональными органическими соединениями, такими как силановый связующий агент, дофамин и вторичные функциональные мономеры, применяется для повышения теплопроводности композитов за счет улучшения сродства BN/полимера и межфазной адгезии, тем самым снижая межфазную термостойкость.
Композиты на полимерной матрице с неорганическими наполнителями с высокой теплопроводностью, такими как УНТ, чешуйки графита и графеновые нанолисты, продемонстрировали значительное улучшение теплопроводности при небольшом количестве добавок.Однако они в основном электропроводны, поэтому их нельзя использовать в качестве подложек для электрических цепей. Вместо этого эти композиты в основном используются для материалов теплового интерфейса. Эти полимерно-углеродные аллотропные базовые композиты также могут использоваться для применения в гибких устройствах, а также в качестве жестких подложек, поскольку морфология частиц карбонатного наполнителя является одномерной или двумерной.
3.3. Керамика с высокой теплопроводностью для корпусов светодиодов и IGBT
Керамические материалы, используемые для применения в корпусах светодиодов, обычно бывают двух типов: диэлектрические изолирующие подложки для формирующего слоя и наполнители с высокой теплопроводностью для материала теплового интерфейса.В изолирующих керамических подложках для модулей IGBT в основном используется глинозем, керамика AlN, но в последнее время разработка переместилась на Si 3 N 4 и LTCC для устройств высокой мощности из-за надежности или низкой стоимости.
3.4. Перспективы на будущее
Несмотря на вышеупомянутые успехи в разработке и коммерциализации керамики, существует несколько проблем, связанных с теплопередающими материалами на основе керамики с высокой теплопроводностью: высокая теплопроводность требуется в химии материалов и инновационных технологиях обработки.По сравнению с керамикой с высокой теплопроводностью на основе HTCC, LTCC по-прежнему требуют дальнейшего улучшения как тепловых, так и механических характеристик, чтобы их можно было использовать в приложениях для управления температурой. Поскольку большая часть обычного состава LTCC состоит из стекла, максимальная теплопроводность полученных таким образом композитов стеклокерамического наполнителя ограничена и намного ниже, чем у керамики с высокой теплопроводностью на основе HTCC. Поэтому, во-первых, необходимо исследовать пути улучшения теплопроводности самой стеклофазы, как это делается во многих композитах с полимерной матрицей.Во-вторых, механическая прочность LTCC должна быть дополнительно улучшена, даже несмотря на то, что некоторые результаты показали повышенную механическую прочность за счет процесса рекристаллизации посредством межфазной реакции и зародышеобразования между стеклофазой и фазой кристаллического наполнителя. Другими проблемами в области LTCC с высокой теплопроводностью может быть разработка LTCC на нестеклянной основе, которые уже предпринимались ранее в качестве приложений в радиочастотных и микроволновых диэлектрических материалах. LTCC на нестеклянной основе освобождаются от использования фазы стеклянной матрицы с низкой теплопроводностью; они будут демонстрировать более высокую теплопроводность, чем обычный тип.
Имеется много сообщений, в которых говорится о достижении высокой теплопроводности в композитах с полимерной матрицей с использованием керамических наполнителей с высокой теплопроводностью. Однако с практической точки зрения простое увеличение теплопроводности полимерных композитов с керамическим наполнителем не обеспечивает потенциального использования в приложениях управления температурой, особенно когда они используются в качестве материалов теплового интерфейса. Другие факторы, такие как прочность сцепления с подложками или материалами радиатора для применения TIM и прочность на растяжение термолент или гибких подложек устройств, также следует учитывать в дополнение к тепловым и электрическим свойствам, поскольку чем больше наполнителя, тем меньше адгезия и прочность на растяжение. сила обеспечена.
Для изолированных металлических подложек (IMS) с использованием керамики с высокой теплопроводностью по-прежнему требуется надежное решение для несоответствия КТР между керамическим и металлическим соединением, вызывающего расслаивание и образование трещин в суровых условиях, таких как среда с циклическими температурами. Кроме того, для высокоэффективных характеристик теплопередачи IMS может потребоваться ультратонкий изоляционный слой с высоким напряжением пробоя диэлектрика в сочетании с высокой механической прочностью, что обеспечивает как низкое тепловое сопротивление, так и низкий профиль корпуса устройства и модуля большой мощности.
Благодарности
Эта работа была поддержана программой конвергенции НИОКР MSIP (Министерство науки, ИКТ и планирования будущего) и NST (Национальный исследовательский совет по науке и технологиям) Республики Корея (грант № CAP-13- 02-ЭТРИ).
1. Введение
Напитки на растительной основе представляют собой группу продуктов, которые с каждым годом вызывают значительный интерес на рынке продуктов питания. Эти продукты становятся популярными по многим причинам. Они в основном используются в качестве веганского заменителя коровьего молока потребителями, которые ограничивают или исключают продукты животного происхождения из своего рациона.Это связано с растущей осведомленностью общества о влиянии интенсивного животноводства на климат, а также о пользе для здоровья от использования растительных диет. Кроме того, напитки, приготовленные из растений, употребляют люди, имеющие пищевую аллергию и непереносимость определенных компонентов молока. Они также вносят большое разнообразие в ежедневный рацион.
Одним из менее ценимых среди потребителей растительных напитков является пшенный напиток. Просо — это крупа, которая имеет такую же питательную ценность, как и самые популярные культуры, такие как пшеница и рожь.Обладает высокой устойчивостью к высоким температурам, засухе и вредителям. Продукты из проса не содержат глютена и, следовательно, подходят для употребления людьми, страдающими аллергией или непереносимостью глютена.
Просо богато полезными для здоровья ингредиентами, такими как клетчатка, полифенолы, минералы (включая медь, фосфор, железо) и витамины группы В. Употребление этого продукта может оказать положительное влияние на здоровье человека. Напитки из проса еще не стали популярными среди потребителей из-за их низкой органолептической приемлемости.Постоянный рост ассортимента напитков на растительной основе и повышение их доступности привели к необходимости разработки новых и усовершенствования существующих продуктов для удовлетворения потребностей и ожиданий потребителей.
2. Напиток из проса и его признание потребителями
2.1 Характеристика проса и продуктов из него
Просо ( Panicum L.) – растение, принадлежащее к семейству злаковых, состоящему из нескольких видов однолетних и многолетних растений. Это одно из древнейших злаковых растений, происходящее из районов Индии и Средней Азии.Наиболее культивируемым сортом проса является просо обыкновенное ( Panicum miliaceum L.). Посевы проса были известны и использовались, вероятно, еще в 7000 или 6000 г. С этого времени известны их преимущества, такие как устойчивость к засухе и относительно короткий период созревания, несмотря на высокую возделываемость их конкурентов, пшеницы и ячменя. Первоначально выращиваемое в северном Китае или на Кавказе, просо распространилось во всех направлениях и даже достигло Европы.Просо является основным продуктом питания для нескольких людей, живущих в жарких и засушливых районах по всему миру. В основном его выращивают в маргинальных сельскохозяйственных районах, где урожайность основных культур, таких как пшеница и кукуруза, низкая из-за плохого количества осадков. Кроме того, просо является важным источником углеводов и белков для миллионов людей, живущих в Африке. Это шестое место среди самых выращиваемых зерновых с точки зрения мирового сельскохозяйственного производства. Крупнейшими производителями проса являются Индия, Нигерия, Нигер и Китай. Кроме того, просо устойчиво к вредителям и имеет короткий период выращивания по сравнению с основными злаками [1, 2].
Благодаря своим технологическим преимуществам и пользе для здоровья, зерна проса с каждым годом вызывают все больший интерес среди пищевых технологов и диетологов. Блюда, напитки и закуски на основе проса известны во всем мире; однако зерно по-прежнему преобладает только в африканских странах. Просо имеет высокую питательную ценность, сравнимую с содержанием макроэлементов в семенах основных злаков, таких как пшеница, кукуруза или рис. В таблице 1 сравнивается пищевая ценность различных видов зерновых культур.Эти значения варьируются в зависимости от сорта зерновых. Белки проса являются хорошим источником незаменимых аминокислот, за исключением лизина и треонина; однако они относительно богаты метионином [1, 2, 3].
Тип зерновых | ||||||
---|---|---|---|---|---|---|
Угленные изделия [G / 100 G] | Белок [G / 100 G] | FAT [G / 100 G] | ||||
Грубый крахмал и сахар0 | ||||||
Пшеница | 60.0-75.0 | 2.0-3.0 | 10.0-25.0 | 2.0-2.6 | ||
RYE | ||||||
RYE | 65.0-73.2 | 1.6-2.7 | 7.2-16.0 | 1.5-2.3 | ||
Barley | 68.0-78.0 | 4.5-7.2 | 10.5-16.3 | 1.9-2.6 | ||
Oat | OAT | 31.1-51.0 | 7.7-19.2 | 9.0-19.0 | 3.1-6.6 | |
Maize | 68,0–78,0 | 2.0-3.0 | 9.0-13.0 | 4.0-6.0 | ||
Millet | 58.0-82.0 | 3.![]() | 9.8-17.2 | 9,8-17.2 | 1.9-4.8 | |
Rice | 65.0-80.0 | 7,8–12,5 | 7,0–10,8 | 1,2–2,5 |
Таблица 1.
Сравнение пищевой ценности зерна злаков [2, 3].
Распределение макроэлементов в просе такое же, как и в основных злаках; поэтому просо признано подходящим сырьем для использования в промышленном производстве закусок, диетических продуктов или детского питания.Зерна проса требуют соответствующей обработки перед употреблением. Наиболее популярными методами его обработки являются шелушение, измельчение, шелушение, полировка, ферментация и замачивание. Эти методы улучшают питательные и органолептические свойства проса, что включает повышение биодоступности микронутриентов и снижение содержания антипитательных веществ, таких как фитиновая кислота. В таблице 2 приведено сравнение средней пищевой ценности проса и продуктов из него. Однако промышленная переработка малоэффективна, что зачастую негативно сказывается на свойствах этого злака (т. г. снижение содержания питательных веществ в продукте по сравнению с его сырьем) [2].
Тип товара0 | Углеводы [G / 100 G] | Белок [G / 100 G] | FAT [G / 100 G] | ||
---|---|---|---|---|---|
Крахмал и сахар | |||||
Просо | 70,0 | 7,3 | 13,5 | 3,3 | Мука 57 | 5.9 | 5.9 | 12.1 | 3.6 |
80015 | 3.8 | 3.8 | 32 | ||
просо крупные | 71.6 | 3.2 | 11.3 | 2.9 |
Таблица 2.
Сравнение средней пищевой ценности проса и продуктов из него [3, 4].
Одним из способов переработки проса является шелушение. Зерна проса мелкие по сравнению с другими злаками; поэтому для облегчения шелушения просо сначала подвергают гидротермической обработке. Эта обработка способствует затвердению его эндосперма, внутренней ткани семени, содержащей запасы питательных веществ. Очищенное просо можно приготовить, чтобы за короткое время получить мягкую и съедобную структуру. Однако шелушение снижает количество некоторых питательных веществ в продукте, таких как пищевые волокна, минералы и полифенолы [1, 2].
Для получения пшенной муки цельное или предварительно очищенное от шелухи зерно проса подвергают процессу помола. Более раннее шелушение удаляет отруби, что одновременно снижает количество клетчатки, минералов и антиоксидантов в муке, что приводит к общему снижению пищевой ценности продукта.Таким образом, использование цельного зерна для производства муки более полезно для здоровья [2].
Просяные хлопья представляют собой еще один продукт, получаемый путем переработки. Сначала зерна проса увлажняют и направляют в испаритель, где в течение нескольких минут подвергают воздействию пара под давлением. После выпаривания зерна оставляют для созревания, а затем направляют на вальцовую мельницу. Дробилка измельчает зерна до тонких хлопьев с определенной влажностью (обычно 17–18%). Полученные хлопья сушат на ленточной сушилке при температуре около 50 градусов Цельсия.Затем высушенные хлопья охлаждают и надлежащим образом сортируют [5].
Для получения крупы из проса с зерна удаляют оболочку, а затем обрушенные зерна шлифуют. Просяная крупа известна не только своими сенсорными свойствами и широким спектром применения, но и пищевой ценностью. Крупа является прекрасным источником энергии (крахмал составляет 65 % массы продукта), растительных белков, магния, цинка, витаминов группы В (преимущественно тиамина и рибофлавина) [5, 6].
Ферментация широко используется в некоторых частях Африки, в основном из-за низкой популярности других методов сохранения пищевых продуктов.Этот процесс не только продлевает срок годности продукта, но также повышает его пищевую ценность и расширяет ассортимент доступных продуктов. Ферментированные продукты потребляются во всем мире из-за их пользы для здоровья, но, к сожалению, продукты из ферментированного проса не популярны в Европе. Такие продукты получают путем заселения растений специфической бактериальной микрофлорой, ферменты которой (в том числе амилазы, протеазы, липазы) гидролизуют углеводы, белки и жиры до нетоксичных ароматизаторов и ароматизаторов.Ферментация улучшает органолептические свойства продукта и обогащает его полезными микроорганизмами, присутствующими в желудочно-кишечном тракте, а также биоактивными веществами, вырабатываемыми этими микроорганизмами. Кроме того, ферментация уменьшает количество антипитательных веществ в продукте, таких как фитаты или ингибиторы протеазы. Следовательно, повышается содержание лизина, триптофана, витамина В2 и усвояемость белка. Повышение усвояемости белка происходит за счет деградации дубильных веществ и фитиновой кислоты ферментами, вырабатываемыми микроорганизмами при брожении.Примером продукта из ферментированного проса является ферментированный хлеб из Саудовской Аравии, известный как лаах. Хотя ферментация является очень эффективным методом переработки проса, ее использование в промышленных масштабах ограничено, так как эта технология до сих пор использовалась только в домашних и лабораторных условиях.
Промышленное использование данной технологии переработки проса требует адаптации оборудования и определения соответствующих технологических режимов [2, 7].
В дополнение к ранее описанным методам обработки проса зерно может быть приготовлено к употреблению, просто замачивая его в воде и подвергая термической обработке.Замачивание приводит к снижению содержания антипитательных соединений, тем самым повышая биодоступность минералов, присутствующих в зернах проса, таких как железо и цинк [2].
Просо — это безглютеновая крупа, поэтому продукты на основе проса идеально подходят для потребителей, страдающих глютеновой болезнью или непереносимостью глютена. Однако это также является ограничивающим фактором с технологической точки зрения. Глютен — это растительный белок, который помогает зерновым продуктам поглощать воду и проявлять консистенцию, липкость и эластичность.Следовательно, отсутствие этого белка в просе снижает его применение в хлебопекарной промышленности, где в результате его обычно комбинируют с другими злаками, такими как пшеница. Однако просо можно использовать в больших масштабах для производства напитков на растительной основе или сухих завтраков и круп [2, 8].
2.2 Характеристика и технология производства пшенных напитков
Пшенные напитки в наибольшем количестве потребляются в традиционных формах, таких как ферментированные продукты. Процесс ферментации повышает пищевую ценность напитка, а также обеспечивает его микробиологическую безопасность, без необходимости использования дополнительных консервантов.Эти типы продуктов составляют значительную часть рациона, главным образом, в Индии и африканских странах, поскольку они считаются очень питательными и безопасными продуктами питания. Например, Jandh — один из ферментированных напитков из проса. Это тип пива, полученный путем брожения с использованием молочнокислых бактерий, дрожжей и плесени [9, 10].
Производство пшенного напитка без процесса брожения включает процедуры, используемые при производстве большинства видов растительных напитков. Он также включает необходимые элементы, исходя из характеристик сырья.Стадии производства пшенного напитка показаны на рисунке 1. Пшенный напиток обычно получают из цельных зерен проса или крупы. Когда используются цельные зерна, они должным образом подготавливаются путем замачивания в течение как минимум 12 часов с последующим проращиванием и сушкой. При использовании круп сырье тщательно промывают для устранения горького привкуса [9, 11, 12].
Рисунок 1.
Этапы производства пшенного напитка [собственное исследование автора на основе 9–11, 19].
Правильно подготовленное сырье следует варить до получения жидкой консистенции. После предварительной обработки проводят мокрое измельчение. Замачивание и отжим водой позволяют подготовить сырье к дальнейшим стадиям обработки и способствуют высвобождению питательных веществ. Воздействие воды приводит к инактивации некоторых ингибиторов и уменьшению количества фитиновой кислоты, что, следовательно, увеличивает абсорбцию и биодоступность питательных веществ. Полученную жидкость дополнительно нагревают, чтобы вызвать термогидролиз крахмала.На этом этапе также добавляют ферменты, чтобы вызвать гидролиз крахмала. Примером используемого фермента является альфа-амилаза, которая гидролизует α-1,4-гликозидную связь амилозы и амилопектина в крахмале с образованием соединений с более короткой цепью, в основном в форме декстринов. Использование протеолитических ферментов повышает усвояемость белков и эффективность экстракции, а также повышает стабильность суспензии [9, 12, 13].
Следующим этапом производства пшенного напитка является отделение твердой фракции от жидкой путем фильтрации или центрифугирования полученной суспензии.В результате предыдущих этапов получается основа растительного напитка. Полученную основу подвергают процессу стандартизации для получения продукта с заранее предполагаемым составом. Стандартизация включает добавление воды, растительных масел, витаминов и минералов, а также подсластителей, ароматизаторов, солей и стабилизаторов. Витамины и минералы добавляются для повышения пищевой ценности напитка и приближения его к коровьему молоку. Отбираемые для напитка обогащающие вещества должны обладать высокой биодоступностью и стабильностью, не вызывать чрезмерных изменений качества конечного продукта [9, 14, 15].
Напитки из проса характеризуются низкой устойчивостью суспензии из-за присутствия твердых частиц, в том числе белка, крахмала, клетчатки и других остатков растительного сырья. Эти частицы имеют более высокую плотность по сравнению с водой и поэтому оседают на дне напитка, делая продукт нестабильным. С целью повышения стабильности пшенных напитков проводят процесс гомогенизации, заключающийся в одновременном измельчении и перемешивании частиц дисперсной фазы с одновременным продавливанием гетерогенной жидкой системы под высоким давлением (15–25 МПа) через гомогенизирующую щель.Эта операция делается для уменьшения диаметра и однородности формы жировых частиц, содержащихся в продукте. В результате полученный продукт характеризуется повышенной кремообразностью и однородностью по сравнению с негомогенизированными продуктами. Гомогенизация обычно поддерживается за счет использования стабилизаторов, загустителей и эмульгаторов (например, целлюлозы, тапиоки, каррагинана, пектина, камеди рожкового дерева или лецитина), которые увеличивают вязкость непрерывной фазы, что приводит к однородной структуре продукта. 9, 15].
В целях обеспечения микробиологической безопасности и продления сроков хранения растительных напитков применяются методы термического консервирования, к которым в основном относятся пастеризация и ультравысокотемпературная (УВТ) обработка. Пастеризацию проводят при температуре ниже 100°С, в результате чего получается продукт со сроком годности около 1 недели при температуре охлаждения. Такая обработка уничтожает патогенные микроорганизмы и инактивирует вегетативные формы других микроорганизмов. При УВТ-обработке продукт нагревается в потоке до 135–150°C в течение нескольких секунд для получения коммерчески стерильного продукта.Этот процесс уничтожает бактериальную микрофлору, сохраняя вкус и аромат продукта. Полученный микробиологически безопасный продукт разливают в порционные упаковки, хранят и распределяют до конца [9, 15].
2.3 Принятие потребителем пшенного напитка в различных формах
Принятие потребителем пищевых продуктов зависит от многих факторов, включая характеристики предлагаемого продукта, потребительские характеристики и социальные условия. Такие характеристики пищевого продукта, как цена, удобство, вкус, внешний вид и полезные для здоровья свойства, играют важную роль в его принятии потребителем.Кроме того, потребительские характеристики, такие как подход к инновациям, предпочтения по отношению к определенным группам продуктов питания или неофобия питания, в значительной степени определяют принятие пищи. Пищевые предпочтения различаются среди потребителей разных возрастных групп с точки зрения знаний о еде, взглядов на пользу для здоровья определенных групп продуктов питания и отношения к еде. На принятие потребителями также влияют социальные условия, такие как экономика страны, политические условия или общепринятые социальные нормы. Культурные факторы и происхождение потребителей имеют большое значение в принятии пищевого продукта. Другим важным фактором является доверие населения к пищевой промышленности в целом, а также существующие различия в доверии потребителей к традиционным и инновационным продуктам питания [16, 17, 18].
Приемлемость пшенного напитка потребителем оценивалась посредством органолептического анализа напитков, произведенных в различных типах. Основу пшенного напитка получали путем смешивания 100 г проса с 1000 г водопроводной воды.Сухое просо сначала промывали горячей водой для устранения горького привкуса, а затем добавляли в кипящую воду и варили под крышкой в течение 40 минут. По истечении установленного времени полученную крупу смешивали с водой, прессовали в однородную кашицу и снова нагревали в течение 5 минут. Приготовленную суспензию просеяли, получив 1000 г основы пшенного напитка и 20 г отвара. Напиток-основа из проса характеризовался высокой плотностью, после чего его подвергали двум разбавлениям для приготовления напитков из натурального проса: 1:2 (1 часть напитка-основы смешивали с 2 частями воды) и 1:3 (1 часть напитка-основы проса). смешивали с 3 частями воды).Затем готовили ароматизированные пшенные напитки путем смешивания с фруктовыми пюре (яблочным и банановым), яблочным соком и банановым нектаром. Таким образом, в качестве исследовательского материала использовали восемь вариантов пшенных напитков трех видов:
пшенный напиток в разведении 1:2,
пшенный напиток в разведении 1:3,
пшенная основа напиток в сочетании с яблочным соком,
пшенный напиток в сочетании с банановым нектаром,
пшенный напиток в разведении 1:2 в сочетании с яблочным пюре,
пшенный напиток в разведении 1:3 в сочетании с яблочным пюре,
пшенный напиток в разведении 1:2 в сочетании с банановым пюре,
пшенный напиток в разведении 1:3 в сочетании с банановым пюре.
Органолептический анализ полученных пшенных напитков проводился с использованием оригинальной анкеты, подготовленной для органолептической оценки. Оценка была проведена группой из 15 студентов факультета диетологии факультета питания человека Варшавского университета наук о жизни (SGGW-WULS), которые ранее заявили о своем желании употреблять напитки на растительной основе. Напитки готовили за 4 дня и охлаждали в холодильнике при температуре 8 градусов Цельсия до оценки. Охлажденные напитки подавались в виде образцов объемом 30 мл в кодированных одноразовых стаканчиках объемом 200 см3 в случайном порядке для органолептической оценки.Для статистической обработки результатов использовали программу Statistica 13.1. Используемые статистические методы: дисперсионный анализ — простые разделы ANOVA и апостериорный анализ — тест LSD (последние значимые различия) [19].
При органолептической оценке испытуемых пшенных напитков различных видов проверяли их вкус, запах, цвет и консистенцию. Каждая из характеристик оценивалась по 5-балльной шкале, где оценка 5 означала, что напиток был очень благоприятным, тогда как 1 означала, что напиток был очень неблагоприятным. Пшенный напиток в сочетании с яблочным соком (средний балл 4,33), пшенный напиток в разведении 1:2 в сочетании с банановым пюре (средний рейтинг 4,53), пшенный напиток в разведении 1:3 в сочетании с банановым пюре ( средняя оценка 4,33) были признаны наиболее благоприятными по вкусовым качествам. Наименее благоприятным по вкусовым качествам был признан натуральный пшенный напиток в разведении 1:2. Что касается цвета, все протестированные напитки были оценены на одинаковом уровне, а средние оценки были между 3 и 4.Пшенные напитки в обоих разведениях в сочетании с банановым пюре были оценены как напитки с наиболее благоприятным вкусом (средний балл 4,60). Наименее благоприятными по аромату были признаны пшенные напитки в натуральном виде в разведениях 1:2 (средняя оценка 2,53) и 1:3 (средняя оценка 2,73). Пшенный напиток в сочетании с яблочным соком (средняя оценка 3,80), пшенный напиток в разведении 1:2 в сочетании с банановым пюре (средний рейтинг 3,80) и пшенный напиток в разведении 1:3 в сочетании с банановым пюре (средняя оценка 3.
87) были оценены как наиболее благоприятные с точки зрения согласованности. Результаты дисперсионного анализа средних значений органолептических признаков оцениваемых напитков из проса разных типов представлены в виде графика органолептического профиля на рис. 2 [19].
Рис. 2.
Органолептические профили исследуемых напитков из проса разных типов [19]. Легенда: Цвет. Запах. Вкус. Консистенция.1 — пшенный напиток в разведении 1:2, 2 — пшенный напиток в разведении 1:3, 3 — пшенная основа в сочетании с яблочным соком, 4 — пшенная основа в сочетании с банановым нектаром, 5 — пшенный напиток в разведении 1:2 в сочетании с пюре яблочным, 6 — напиток пшенный в разведении 1:3 в сочетании с пюре яблочным, 7 — напиток пшенный в разведении 1:2 в сочетании с пюре банановым, 8 — напиток пшенный в разведении 1:3 в сочетании с банановым пюре.
Тест LSD использовался для сравнения результатов, полученных при органолептической оценке испытуемых напитков из проса в парах, и для оценки статистической значимости рассчитанных различий. Испытывались следующие пары:
натуральный пшенный напиток в разведении 1:2 и натуральный пшенный напиток в разведении 1:3,
пшенный напиток в сочетании с яблочным соком и пшенный напиток в сочетании с банановым нектаром. ,
пшенный напиток в разведении 1:2 с яблочным пюре и пшенный напиток в разведении 1:3 с яблочным пюре, и
пшенный напиток в разведении 1:2 с банановым пюре и пшенным напитком в Разведение 1:3 с банановым пюре.
Во вкусе существенных различий между натуральными пшенными напитками в обоих разведениях, пшенными напитками в сочетании с яблочным пюре в обоих разведениях и пшенными напитками в сочетании с банановым пюре в обоих разведениях обнаружено не было. Напиток из проса в сочетании с яблочным соком оказался значительно лучше, чем напиток из проса в сочетании с банановым нектаром. Результаты теста LSD для признака «вкус» оцениваемых напитков из проса представлены на рисунке 3 [19].
Рис. 3.
Категоризированная диаграмма «ящик-ус» для признака ВКУС оцененных напитков из проса [19]. Обозначения те же, что и на рис. 2.
По цвету существенные различия обнаружены только в случае напитков из натурального проса. Напиток из натурального проса в разведении 1:3 оказался значительно лучше, чем напиток из натурального проса в разведении 1:2. Статистически значимых различий между остальными парами пшенных напитков обнаружено не было.Результаты теста LSD для признака «цвет» оцениваемых напитков из проса представлены на рисунке 4 [19].
Рис. 4.
Классифицированная диаграмма «ящик-ус» для признака ЦВЕТ оцениваемых напитков из проса [19]. Обозначения те же, что и на рис. 2.
По запаху статистически значимых различий между сравниваемыми парами напитков обнаружено не было. Результаты теста LSD на признак «запах» оцениваемых пшенных напитков представлены на рисунке 5 [19].
Рис. 5.
Категоризированная диаграмма «прямоугольник-ус» для признака ЗАПАХ оцениваемых напитков из проса [19]. Обозначения те же, что и на рис. 2.
С точки зрения консистенции статистически значимых различий между сравниваемыми парами напитков обнаружено не было. Результаты теста LSD на признак «консистенция» оцениваемых напитков из проса представлены на рисунке 6 [19].
Рис. 6.
Классифицированная диаграмма с квадратными усами для признака ПОСЛЕДОВАТЕЛЬНОСТЬ оцененных напитков из проса [19]. Обозначения те же, что и на рис. 2.
В проведенных исследованиях вкус, запах, цвет и консистенция рассматривались как одни из основных характеристик, которыми потребители руководствуются при покупке продуктов питания [20].
По мнению людей, проводивших сенсорную оценку, пшенные напитки со вкусом яблока и банана были лучшими по вкусовым качествам. Банановые нектары и пюре характеризуются высокой интенсивностью вкуса и сладостью, что могло повлиять на органолептические оценщики на положительную оценку содержащих их напитков.Оценщики оценили напиток из натурального пшена в разведении 1:2 как самый плохой по вкусовым качествам. Такая оценка могла быть обусловлена растительным послевкусием напитков в натуральном виде, что может быть приемлемо не всеми потребителями, а также его высокой мутностью, вызванной низким разбавлением [19].
Цветовые характеристики всех протестированных пшенных напитков остались на одном уровне. Каждый тип напитка имел определенный цвет, что могло побудить оценщиков дать одинаковые оценки. Единственная существенная разница в оценках цвета была обнаружена между натуральными напитками из проса. Натуральный пшенный напиток в разведении 1:3 был оценен лучше, чем в разведении 1:2. Более высокое разбавление давало напитку менее «молочный» цвет, который больше похож на цвет напитков на растительной основе, доступных на рынке, и может быть причиной более высоких оценок, полученных сильно разбавленным натуральным напитком из проса [19].
Запах натурального пшенного напитка оказался наименее благоприятным для оценщиков и получил самую низкую оценку.Банановое пюре в наибольшей степени маскировало «пшенный» запах, что в сочетании с пшенным напитком придавало ему специфический запах. Таким образом, напитки в сочетании с банановым пюре в обоих разведениях оказались наиболее выгодными с точки зрения аромата для оценщиков и, следовательно, получили наивысшую оценку [19].
Наиболее благоприятные результаты с точки зрения консистенции наблюдались для пшенного напитка в сочетании с яблочным соком и пшенного напитка в сочетании с банановым пюре в обоих разведениях. Пшенный напиток в сочетании с яблочным соком и пшенный напиток в разведении 1:3 в сочетании с банановым пюре показали аналогичную консистенцию, характерную для освежающих напитков. Высокие оценки, присвоенные этим видам напитков, свидетельствуют о заинтересованности потребителей в имеющихся на рынке альтернативах. Пшенный напиток в разведении 1:2 в сочетании с банановым пюре консистенции смузи также получил высокие оценки [19].
Вы успешно отписались.
Влияние различной температуры обжига на теплопроводность керамической плитки
[1] Н.Т. Селли, Разработка составов плитки из белого керамогранита на основе анортита, Ceram. Междунар. 41 (2015) 7790–7795.
DOI: 10. 1016/j.ceramint.2015.02.112
[2] С.Эффтинг, С. Гутс, О.Э. Аларкон, Оценка теплового комфорта керамической напольной плитки, Матер. Рез. 10 (2007) 301–307.
DOI: 10.1590/s1516-143000300016
[3]
Э. Энрикес, В. Фуэртес, М. Дж. Кабрера, Дж. Сеорес, Д. Муньос, Дж. Ф. Фернандес, Новая стратегия смягчения эффекта городского теплового острова: энергосбережение за счет сочетания высокого альбедо и низкой температуропроводности в стеклокерамических материалах, Sol. Энергия. 149 (2017) 114–124.
DOI: 10.1016/j.solener.2017.04.011
[4]
Л.М. Шаббах, Д.Л. Мариноски, С. Гутс, А.М. Бернардин, М.К. Фредель, Пигментированная глазурованная керамическая черепица в Бразилии: тепловые и оптические свойства, связанные с коэффициентом солнечного отражения, Sol. Энергия. 159 (2018) 113–124.
DOI: 10.1016/j.solener.2017.10.076
[5] М.Sutcu, Влияние вспученного вермикулита на физические свойства и теплопроводность глиняных кирпичей, Ceram. Междунар. 41 (2015) 2819–2827.
DOI: 10.1016/j.ceramint.2014.10.102
[6]
М. Гуалтьери Л., Гуалтьери А.Ф., Гальярди С., Руффини П., Феррари Р., Ханушкова М. Теплопроводность обожженных глин: влияние минералогических и физических свойств сырья, Appl. Глина наук. 49 (2010) 269–275.
DOI: 10.1016/j.clay.2010.06.002
[7] Я.Аллегретта, Г. Эрамо, Д. Пинто, А. Хайн, Влияние минералогии, микроструктуры и температуры обжига на эффективную теплопроводность традиционной керамики горячей обработки, Appl. Глина наук. 135 (2017) 260–270.
DOI: 10. 1016/j.clay.2016.10.001
[8] У.Берарди, Разработка систем остекления с аэрогелем кремнезема, Energy Procedia. 78 (2015) 394–399.
DOI: 10.1016/j.egypro.2015.11.682
[9]
В. Бао, В. Донг, Дж. Чжоу, К. Лю, Т. Чжао, Влияние кальцита на микроструктуру и свойства спекания керамогранита, стр. 88, (2017) 881–886.
DOI: 10.2109/jcersj2.17105
[10] Ф.Контартези, Ф.Г. Мельхиадес, А.О. Boschi, Предполагаемый перегрев керамогранита: влияние цикла обжига и объемной плотности неспеченного материала, Bol. Ла Сок. особ. Керам. Y Видр. (2018) 1–8.
DOI: 10. 1016/j.bsecv.2018.07.001
[11] А.Павезе, Л. Пальяри, И. Адамо, В. Диелла, Ф. Франческон, Влияние распределения частиц по размерам и состава исходной фазы в системе натриевый полевой шпат/каолинит при высокой температуре, J. Eur. Керам. соц. 35 (2014) 1327–1335.
DOI: 10.1016/j.jeurceramsoc.2014.10.035
[12]
Э. Эрен Гюльтекин, Влияние скорости нагрева и температуры спекания на модуль упругости керамогранита, Ультразвук. 83 (2018) 120–125.
DOI: 10.1016/j.ultras.2017.06.005
[13] Дж.Гарсия-Тен, М. Дж. Ортс, А. Сабурит, Г. Силва, Теплопроводность традиционной керамики: Часть II: Влияние минералогического состава, Ceram. Междунар. 36 (2010) 2017–(2024).
DOI: 10. 1016/j.ceramint.2010.05.013
[14] С.Китуни, Хараби, Спекание и механические свойства фарфора, приготовленного из алжирского сырья (Sinterização e proprieades mecânicas de porcelanas, Cerâmica. 57 (2011) 453–460.
DOI: 10.1590/s0366-611000400013
[15]
Ю. Кобаяши, О. Охира, Ю. Охаси, Э. Като, Влияние температуры обжига на прочность на изгиб фарфора для посуды, J. Am. Керам. соц. 75 (1992) 1801–1806.
DOI: 10.1111/j.1151-2916.1992.tb07200.x
[16] Дж.Г. Тен, М. Дж. Ортс, А. Сабурит, Г. Сильва, теплопроводность традиционной керамики. Часть I: Влияние насыпной плотности и температуры обжига, Ceram. Междунар. 36 (2010) 1951–(1959).
DOI: 10. 1016/j.ceramint.2010.05.012
[17] ЧАС.Махрафи, Г. Лебон, Влияние размера и пористости на теплопроводность нанопористого материала с распространением на нанопористые частицы, встроенные в матрицу-хозяин, Phys. лат. Разд. Генерал В. Физика твердого тела. 379 (2015) 968–973.
DOI: 10.1016/j.physleta.2015.01.027
[18]
К. Алмадхони, С. Хан, Теплофизические свойства ячеистого алюминия и керамических частиц / алюминиевых композитов Теплофизические свойства ячеистого алюминия и керамических частиц / алюминиевых композитов, 5 (2015) 17–27.
Теплопроводность металлокерамики
H.O. Пирсон, Справочник по тугоплавким карбидам и нитридам (Вествуд, Нью-Джерси: Noyes Publications, 1996).
Google Scholar
Р.Е. Тейлор, Дж. Ам. Керам. соц. , 44 (1961), с. 525.
Артикул КАС Google Scholar
Р.Е. Тейлор, Дж. Ам. Керам. соц. , 45 (1962), стр. 353–354.
Артикул КАС Google Scholar
В.С. Уильямс, , Дж. Ам. Керам. соц. , 49 (1966), стр. 156–159.
Артикул КАС Google Scholar
В.С. Уильямс, Phys. Rev. , 135 (1964), стр. A505-A510.
Артикул Google Scholar
П.Г. Клеменс, Phys. Rev. , 119 (1960), стр. 507.
Статья КАС Google Scholar
Дж.Бетин и В.С. Уильямс, , Дж. Ам. Керам. соц. , 60 (1977), стр. 424–427.
Артикул КАС Google Scholar
РЭ. Тейлор и Дж. Морреале, J. Am. Керам. соц. , 47 (1964), стр. 69–73.
Артикул КАС Google Scholar
Л.Г. Радосевич и В.С. Уильямс, Phys. Rev. , 181 (1969), стр. 111–1117.
Артикул Google Scholar
л.Г. Радосевич и В.С. Уильямс, , Дж. Ам. Керам. соц. , 53 (1970), стр. 30–33.
Артикул КАС Google Scholar
А.Б. Пиппард, Фил. Маг. , 46 (1955), стр. 1104–1114 и JM Ziman, Electrons and Phonons (Oxford, UK: Clarendon Press, 1960).
КАС Google Scholar
Д. Т. Морелли, Phys. Rev. B , 44 (1991), с.5453–5458.
Артикул КАС Google Scholar
Л.Г. Радосевич и В.С. Уильямс, Phys. Rev. , 188 (1969), стр. 77–773.
Артикул Google Scholar
Дж. Бардин, Г. Рикайзен и Т.Л. Tewordt, Phys. Rev. , 113 (1959), стр. 982.
Статья КАС Google Scholar
С.Уэр, Дж. Суперконд. , 3 (1990), стр. 337.
Статья КАС Google Scholar
В.С. Несфор и С.С. Орданьян, Неог Матер. , 1 (1996), стр. 480. См. также G.S. Upadhaya, Nature of Properties of Refractory Carbides (Commack, NY: Nova Science Publishers, 1996), p. 286.
Google Scholar
Б. Чакраборти и П.Б. Аллен, Phys. Преподобный Летт. , 42 (1979), стр. 736–738.
Артикул КАС Google Scholar
GS Upadhaya, Природа свойств тугоплавких карбидов (Commack, NY: Nova Science Publishers, 1996), p. 285.
Google Scholar
М.В. Франдсен и В.С. Williams, J. of Hard Materials , 1 (1990), стр. 159–167.
КАС Google Scholar
М.В. Франдсен и В.С. Уильямс, , Дж. Ам. Керам. соц. , 76 (1991), стр. 1411–1416.
Артикул Google Scholar
А Перечерла и В.С. Уильямс, , Дж. Ам. Керам. соц. , 71 (1988), стр. 1130–1133.
Артикул КАС Google Scholar
К. Бахман и В.С. Уильямс, J. Appl. физ. , 42 (1971), с. 4407.
Google Scholar
Сохранение теплого напитка
В нашей серии статей о теплопроводности мы представляем различные контексты, в которых теплопроводность играет роль при выполнении наших повседневных задач.Количество раз, когда средний человек размышляет о влиянии теплопроводности в своем ежедневном принятии решений, практически равно нулю. Хотите верьте, хотите нет, но теплопроводность имеет большее отношение к вашей повседневной жизни, чем вы думаете, особенно когда речь идет о вашей кофейной кружке. Некоторые люди предпочитают керамическую кружку стеклянной, а другие предпочитают стальную. В чем причина? Скорее всего, этот выбор кружек основан на эстетических предпочтениях, а не на научной основе.
Рисунок 1 .Какая из трех кружек сохранит тепло вашего кофе: нержавеющая сталь, керамика или стекло?
Теплопередача, особенно теплопроводность, является важной идеологией среди производителей кружек, поскольку они стремятся производить качественный материал, привлекательный для покупателей. Существует три различных способа передачи тепла: теплопроводность, излучение и конвекция. Процесс теплопроводности — это способность тепла перемещаться из среды с более высокой температурой (жидкость) в среду с более низкой температурой (кружка) до тех пор, пока не будет достигнуто температурное равновесие между двумя материалами. Итак, какой из трех предложенных материалов для кружек больше всего замедлит этот процесс равновесия и дольше сохранит более теплую жидкость?
Рисунок 2 . Три способа передачи тепла: теплопроводность, конвекция и излучение.
Стальная кружка имеет самую высокую теплопроводность из трех предложенных материалов, 14,3 Вт/мК. Эта высокая теплопроводность связана с относительно быстрым температурным равновесием между кружкой и жидкостью, что означает, что жидкость довольно быстро остывает.Теплопроводность керамической кружки составляет примерно 3,8 Вт/мК, а теплопроводность стеклянной кружки — примерно 1,1 Вт/мК. Из-за относительно низкой теплопроводности стеклянной кружки жидкость должна сохранять более теплую температуру в течение самого длительного периода времени.
Основываясь на знаниях о теплопроводности, упомянутых выше, следует использовать стеклянную кружку, чтобы жидкости дольше оставались теплыми, за ней следует керамическая, а затем стальная кружка. Низкая теплопроводность стеклянной кружки предотвращает быстрое проникновение и рассеивание тепла жидкости в кружке.Благодаря высокой теплопроводности стали тепло от жидкости быстро передается кружке, а затем и ладоням.
Хотя, основываясь на знаниях о теплоемкости, керамическая кружка получает награду за теплый напиток. Теплоемкость – это способность материала удерживать тепло на единицу объема. Из-за меньшей плотности керамики, благодаря маленьким порам в материале, тепло может накапливаться внутри самой кружки, а не выделяться в окружающую кружку область, т.е.е. ладони ваших рук. Пока тепло остается внутри барьера кружки, поддерживается равновесная реакция между кружкой и жидкостью, что предотвращает слишком быстрое охлаждение жидкости.
В следующий раз, когда вы пойдете покупать свою новую любимую кружку, помните, как теплопроводность и теплоемкость могут повлиять на теплоту вашего напитка, и выбирайте с умом!
Сталь, стекло, керамика? — Бариста Хастл
Какой самый термостабильный материал для пивоварения?
Короткий ответ: лучше всего использовать пластиковые конусы. Они медленнее поглощают тепло из воды для заваривания, поглощают меньше тепла в целом и медленнее отдают это тепло воздуху. Чтобы действительно понять, почему пластик — лучший выбор материалов с точки зрения пивоварения, нам нужно немного углубиться в физику. Есть три вещи, которые влияют на то, сколько тепла вы теряете через конус:
- Проводимость – измеряет скорость прохождения тепла в конус и через него
- Удельная теплоемкость – сколько тепловой энергии требуется для изменения температуры конуса
- Потери тепла на поверхности – насколько быстро конус отдает тепло в атмосферу
Проводимость
Вы, наверное, помните из школьных уроков естествознания, что пластик — хороший изолятор, а металл — хороший проводник.Стекло и керамика находятся где-то посередине. Это говорит нам о том, что пластик выигрывает по проводимости, по крайней мере, но насколько?
Материал | Акрил | Стекло | Фарфор | Нержавеющая сталь |
Электропроводность (Вт/мК) | 0,2 | 1 | 4-5 | 16 |
(Источник: engineeringtoolbox. com)
Как видите, фарфор в 20–25 раз лучше проводит электричество, чем акрил (обычный пластик).Это означает, что тепло будет намного быстрее передаваться из вашего напитка в конус.
Удельная теплоемкость
Далее мы рассматриваем, сколько энергии конус способен поглотить. Это называется удельной теплоемкостью и измеряется в джоулях на кг на градус — другими словами, сколько джоулей энергии требуется для изменения температуры одного килограмма материала на один градус.
Итак, пластику требуется больше тепловой энергии на килограмм, чтобы увеличить температуру на заданную величину.Однако типичный керамический конус весит в четыре раза больше, чем пластиковый конус, поэтому он будет поглощать примерно в 3,5 раза больше тепла в целом при том же изменении температуры.
Это часто сбивает людей с толку: бариста часто говорят, что предпочитают керамические рожки, «потому что они лучше сохраняют тепло». Однако на самом деле это плохо, так как это означает, что из воды для заваривания уходит больше тепла.
Тепловые потери на поверхности
Наконец, тепло уходит из конуса в атмосферу либо конвекцией, либо излучением.Скорость конвекции зависит от температуры поверхности. Более проводящие материалы быстрее передают тепловую энергию на поверхность. Как только тепло достигает поверхности, материалы с более низкой удельной теплоемкостью становятся более горячими при заданном количестве теплопередачи. Таким образом, пластик с его более низкой проводимостью и более высокой удельной теплоемкостью будет терять значительно меньше энергии на конвекцию, чем другие материалы.
Скорость потери тепла излучением зависит не только от материала, но и от его структуры, в том числе от степени полировки, а также от температуры поверхности, поэтому ее трудно оценить расчетным путем.Стекло, фарфор и пластик излучают одинаковое количество тепла при заданной температуре. Сталь излучает гораздо меньше, но это компенсируется тем фактом, что высокая проводимость и низкая удельная теплоемкость означают, что температура поверхности нагревается намного быстрее. Кроме того, максимальная потеря тепла за счет излучения примерно вдвое меньше, чем за счет конвекции.
Как насчет изолированных конусов?
Воздух является лучшим изолятором, чем любой из этих материалов, с проводимостью около 0.02 Вт/мК. Существуют некоторые конструкции конусов, которые используют это преимущество, используя либо двойную стенку для улавливания слоя воздуха, либо открытую структуру сетчатого типа, чтобы минимизировать количество материала, контактирующего с фильтром, оставляя его открытым для воздуха. Эти конструкции могут в некоторой степени удерживать тепло, однако даже в этих случаях лучшим материалом для их изготовления по-прежнему остается пластик.
В стеклянных конусах с двойными стенками стеклянная масса по-прежнему будет поглощать много тепла до того, как вступит в действие воздушная прослойка.Пластиковый конус с двойными стенками будет работать намного лучше.
В конусах металлического сетчатого типа площадь поверхности металла по-прежнему значительна, что означает, что он по-прежнему будет отводить некоторое количество тепла от напитка и рассеивать его в атмосферу. Также будут дополнительные потери тепла на внешней поверхности фильтра из-за испарения, которое является высокоэффективным способом передачи тепла в атмосферу. В конечном счете, использование материала, близкого к пенополистиролу, сделает ту же работу намного лучше и дешевле.
Заключение
Таким образом, исходя из этих трех факторов, пластиковые конусы каждый раз выигрывают — они медленнее поглощают тепло из воды для заваривания, поглощают меньше тепла в целом и медленнее отдают это тепло воздуху. Дизайн конуса, особенно его вес и площадь поверхности, играют определенную роль, но какой бы дизайн ни был сделан, пластик является логичным материалом для использования. Этот вывод может показаться тревожным для некоторых читателей, которые сосредоточены на растущей проблеме пластикового загрязнения.Для решения этой важной темы мы начали работу над курсом под названием «Дерево решений ». Кроме того, рост BH Unlimited означает, что наши подписчики помогают сделать этот важный курс открытым.