Изготовление стропильной системы: Изготовление стропильной системы своими руками
видео-инструкция по монтажу своими руками, как изготовить стропильную систему Эркера, Шале, аттиковую, фото
Стропильная конструкция – основа для любой скатной крыши, ее «скелет». Она воспринимает на себя весьма серьезные нагрузки, особенно в зимнее время, и является несущей для кровли. Это значит, что защита дома от осадков и ветрового воздействия в значительной степени зависит от нее.
Поэтому в индивидуальном строительстве изготовление стропил на завершающем этапе – важная операция, которой уделяется особое внимание. Какова последовательность действий при устройстве стропильной системы, какие особенности имеют различные виды стропил – далее в статье.
Начальный этап монтажа висячих стропилУчитывая исключительную важность стропильной системы, ее тип, материал для изготовления и прочие важные детали определяются на этапе проектирования. Стропильные фермы обычно выполняются из дерева или металла (в уникальных случаях в частном домостроении – из железобетона).
Металлические фермы обычно изготавливаются заводским способом, доставляются в готовом виде на стройку и устанавливаются при помощи крана, закрепляются сваркой.
Деревянные стропила могут:
- Также изготавливаться заводским способом (висячие стропила)
- Заводским способом могут изготавливаться отдельные элементы конструкции и собираться на стройке
- Вся стропильная система раскраивается и монтируется непосредственно на объекте
Использование заводских полуфабрикатов предполагает предельную точность в соблюдении проекта при производстве строительных работ, поскольку переделка готовых ферм или изменение размеров их деталей связаны с большими сложностями, а иногда – просто невозможны.
Но плюсом такого решения является то, что если стены выведены правильно, то установка стропильной системы равносильна сборке детского конструктора.
Элементы стропильных системЧасто заводские изделия используют при возведении сложных кровель, например, если требуется стропильная система над эркером, и в обязательном порядке – при строительстве быстровозводимых зданий, поставляемых в комплекте.
Совет!!
Перед самостоятельным изготовлением и сборкой стропил следует изучить все термины, связанные с крышей.Путаница в понятиях может в ходе работ привести к непредсказуемым последствиям
В процессе устройства стропильной конструкции можно выделить следующие этапы:
Изготовление шаблонов, раскрой, изготовление ферм
Лекала и распиловка
Конечно, важнейшим в подготовке лекал будет изготовление шаблонов стропильных ног. Особенно строго следует подойти к этой операции на крышах сложной конфигурации, например, когда устанавливаются аттиковые стропила.
Оно может быть выполнено следующими способами:
- Берется рейка, длина которой равна вертикальному расстоянию от верха опорной стены до конька (конькового бруса или стыка стропил)
Перпендикулярно ей набивается по краю доска, длина которой равна расстоянию между внешними стенами здания.
Конструкцию следует сразу проверить «по месту», установив ее на стенах и повторив промеры.
Если геометрия соблюдена – можно изготавливать шаблон для стропила по верху вертикальной рейки и краю одной из боковых.Необходимо сразу учитывать запас на узлы соединений, свесы крыши и т.п.
Стропильные фермы раскроены и собраны на землеСовет!
Когда шаблон отмерен по длине, на него лучше сразу нанести все врубки, врезки, места крепления соединительных элементов.
Можно изготовить для всего этого отдельные шаблоны, и наносить их на раскроенные стропила самостоятельной операцией, однако при этом растет риск погрешностей
- Этот способ является подвидом первого, но перпендикулярная доска набивается не по обрезу вертикальной, а посредине .
Затем при помощи дополнительных реек или шнура определяются необходимые уклоны и расстояния до стен, после чего алгоритм действий – тот же.
Этот способ применяют чаще на домах с большим пролетом, где использование «полноразмерной» горизонтальной рейки затруднено. - Можно взять две планки, шарнирно соединить их по одному из краев одним гвоздем, и, установив на стены, отмерить нужную длину каждой, проверить геометрию конструкции, после чего закрепить соединение 3-4 саморезами.
Этот способ хотя и весьма прост, но считается наименее надежным.
Совет!
В шаблонах с вертикальной планкой последняя может быть сама использована в качестве шаблона для опорных элементов, если таковые предусмотрены конструкцией стропильной системы (например, стоек или бабок)
Раскрой стропильных ног и прочих элементов может проводиться как на земле, так и на перекрытии здания. Каждый из вариантов имеет свои преимущества и недостатки: на земле удобней работать, и можно собрать готовые фермы (впрочем, они редко имеют для этого достаточную прочность), на крыше – можно сразу примерить готовую деталь, и при необходимости – поправить огрехи.
А, например, стропильная система эркера просто требует сборки на месте, поскольку может иметь достаточно сложную конфигурацию, и стропила легче разметить сразу, чем тратить время и силы на отдельные шаблоны.
Сборка ферм
Фермы, во всяком случае, торцевые, лучше предварительно собрать «наживую», не делая капитальных соединений – ведь именно стропила, располагаемые над фронтонами, будут играть решающую роль в правильности геометрии крыши, поэтому вымерять и устанавливать их следует особенно тщательно.
Прежде всего, эти конструкции должны быть установлены строго параллельно стене, на которую устанавливаются, а также – иметь строго вертикальное положение. Это проверяется следующим способом: фермы временно закрепляются, от каждого из нижних углов каждой фермы протягиваются бечевки к вершине противоположного.
В результате получаются диагонали на каждом из скатов. Если крыша ломаная, угловая или имеет иную сложную форму – промеры необходимо произвести для всех ее ровных плоскостей.
Схема промера фермВ результате, если геометрия ската правильная, должны получиться следующие результаты:
- В месте пересечения бечевки должны слегка касаться друг друга
- Место их пересечения должно приходиться на середину длины крыши
- Пересекаться они должны на половине длины противоположных стропильных ног
Если какое-то из этих условий не соблюдается, ферму-«нарушителя» следует скорректировать соответствующим образом до устранения проблемы. После этого элементы можно крепить к подстропильному брусу капитально – при помощи скруток или скоб.
После этого в случае с наслонными конструкциями, если это предусмотрено проектом – следует установить между фермами коньковый брус. Если используется стропильная система шале, где предусмотрены фронтонные стены «под конек», следует те же операции выполнить для самих стен перед установкой крайних стропил, поскольку они будут опираться на стены.
В этом случае возможные несоответствия ликвидируются выравнивающей стяжкой. Для выравнивания последующих стропил используют бечевку, натянутую по коньку.
Технические подробности
Для соединения стропил с подстропильным брусом (мауэрлатом) и прочими деталями системы применяют различные виды плотницких «замков»: зуб, двойной зуб, шип и т.п. Выбор конкретного способа зависит от формы крыши, планируемой нагрузки на нее, особенностей работы конкретного узла (на сжатие, растяжение, изгиб, излом).
В последнее время практически любые виды соединений дублируются специальными металлическими накладками.
Совет!
В большинстве случаев при установке наслонных стропил стоит устроить шарнирное соединение хотя бы в одном из узлов: крепление к мауэрлату (специальная скользящая металлическая конструкция), связь с коньковым брусом, стык стропил (если коньковый брус отсутствует)
youtube.com/embed/Wa8Q92c5K8M» frameborder=»0″ allowfullscreen=»allowfullscreen»/>
Следует обратить внимание, что в наслонных стропилах при наличии конькового бруса допускается установка стропильных ног не строго напротив друг друга, а со смещением – таким образом, чтобы стропильные ноги соприкасались боковинами. В висячих стропилах это недопустимо, поскольку их принцип действия основан как раз на упоре стропил торцами.
Но, какая бы система ни была выбрана, перед тем, как изготовить стропила, следует хорошенько изучить теорию, и попробовать на практике свои плотницкие навыки. Если в порядке и то и другое – готовая крыша прослужит долго и никуда не съедет.
Стропильная система крыши — понятие и способы изготовления
Прочность крыши зависит от основы её конструкции — несущих элементов. Традиционно ими являются стропила. Стропильная система крыши держит на себе вес всей кровельной конструкции, которая в свою очередь должна удерживать дополнительные виды нагрузок – ветровую и нагрузку накапливающегося на крыше зимой снежного покрова. Поэтому строительство крыши — это вопрос к которому требуется подойти с особой внимательностью и точностью.
Стропильная система крыши
Стропильная система крыши частного дома состоит из следующих элементов:
Мауэрлат
Длинный брусок из смолистого ствола любого хвойного дерева. Его укладывают вдоль наружной несущей стенки по периметру дома, закрепив анкерами или особыми резьбовыми стержнями. Мауэрлат служит для равномерного распределения нагрузки и передачи её от стропил несущим стенам.
Стропильная нога
Деревянные брусья из которых возводиться контур скатной кровли характерной треугольной формы. Кровля должна выдерживать сильнейшее воздействие ветра, снега и прочих атмосферных аномалий.
Чтобы максимально её укрепить стропильные ноги равномерно распределяют вдоль кровли с шагом, не превышающим 1.2 метра. В зависимости от веса кровли шаг стропил может еще более снижаться.
Лежень
Брусок из дерева, подобно мауэрлату помогает перераспределять нагрузку он кровельных стоек на стены здания. Укладывается над внутренней несущей стеной дома.
Затяжка
Важнейший узел висячей стропильной системы. Брусок, уложенный таким образом, чтобы служить основой треугольника кровли. Этот элемент не позволяет скатам крыши разъезжаться под действием своего веса.
Стойки
Элемент кровли, представляющий собой вертикально установленный брусок квадратного сечения. Этот брусок принимает нагрузку от конька крыши и передает её внутренней несущей стене. Так же, как опоры могут устанавливаться и под стропильные ноги.
Подкос
Элемент, служащий для укрепления конструкции кровли. Подкосы соединяют кровельные ноги с лежнем, образуя конструкцию в форме ромба. Совокупность затяжки и подкосов с обеих сторон называется фермой. Такая конструкция способна выдержать вес кровли даже в том случае, если проем очень большой.
Обрешётка
По длине всей крыше поперек ног стропил своеобразными ступеньками закрепляются тонкие гладкие доски. Они скрепляют в единую конструкцию стропильные ноги. На обрешётку монтируется облицовка крыши – кровельное покрытие. Если предполагается покрывать крышу мягкой кровлей обрешётку нужно делать практически сплошной. Лучшим материалом для этого считаются листы фанеры.
Конек крыши
Верхняя часть треугольника кровельной конструкции. Вверху в месте соединения двух противоположных стропильных ног вдоль всей крыши крепится деревянный брус квадратного сечения. Таким образом, получается мощный узел, который не позволяет крыше разрушиться.
Свес крыши
Это нижняя часть скатной крыши, выступающая примерно на полметра от периметра здания. Это делается для того, чтобы дождевые потоки, стекающие по кровле, не попадали на внешние несущие стены и не разрушали их.
Кобылки
Эти элементы крыши применяются лишь тогда, когда длины стропильных ног не хватает для обустройства свеса. В этом случае их удлиняют, соединяя с досками меньшего сечения.
Стропильная система крыши — кобылки
Перед возведением кровли серьезные подрядчики всегда проводят анализ преобладающих показателей силы ветра в районе застройки и средней высоты снежного покрова. Такие исследования позволяют создать необходимый запас прочности для будущей крыши.Для достижения нужной прочности конструкции, необходимо надежное скрепление стропил друг с другом и фасадом здания.
Деревянные стропила, благодаря простоте изготовления и несложному монтажу, используются при постройке загородных домов малоэтажек. Поверхность таких стропил легко обрабатывается.
Это позволяет быстро и без использования сложного оборудования подогнать систему стропил под габариты уже возведенного здания, исправив небольшой брак, допущенный каменщиками при кладке стен. Подобная процедура практически невозможна при возведении крыши с использованием металлических стропил или железобетонных конструкций.
Стропильная система крыши
Для скрепления стропил применяются такие соединительные детали как хомуты и скобы. Тем не менее, наиболее часто в качестве соединения по старинке применяют гвозди. Такое соединение имеет существенный изъян. Когда спустя несколько лет древесина высыхает, оно утрачивает свою прочность.
Куда более надежным является метод болтового соединения. Но и здесь, каналы, просверливаемые для вворачивания болтов, вызывают частичное ослабление стропильной конструкции. Практика показывает, что наибольшей прочностью обладает крепеж металлическими скобами или хомутами.
Менее гибкий, но куда более надежный способ изготовления системы деревянных стропил является их промышленное производство. Отдельные стропила изготавливаются серией в условиях заводского цеха, с использованием точного оборудования и хорошо подобранной древесиной, отвечающей жестким стандартам. Изготовленные деревянные стропила соединяются стыковыми планками в крупные конструкции – фермы.
Упакованные фермы доставляют на место строительства. Затем, как в увеличенном в несколько раз детском конструкторе из отдельных ферм собирается полная кровельная система. Такая технология обеспечивает быстрое возведение стропильной системы. Дополнительными опциями при изготовлении ферм промышленным способом является пропитка ферм антисептиками и растворами, повышающими устойчивость древесины к возгоранию. Данные процедуры обеспечивают безопасность и долговечность как кровли, так и всего здания.
Стропильная система крыши — готовые фермы для крыши
Технология соединения гарантирует высокую прочность всей конструкции и невозможность смещения отдельных узлов системы стропил в процессе естественного усыхания древесины. О видах и особенностях стропильной системы вы сможете познакомиться также в этом видео:
Материалы для стропил
Любая крыша держится на специальной опорной конструкции – стропильной системе. Она может быть разной: это зависит от формы крыши, материала, применяющегося для обшивки кровли, и прочего.
Так как стропильная система одна из самых важных в общей конструкции крыши, то и материалы для стропил должны выбираться только качественные и надежные. В этой статье предлагаем узнать в целом про стропильную систему, ее виды, а также про материалы для стропил, которые рекомендуется использовать.
Общее описание стропильной системы для крыши
Для чего служит стропильная система? Отметим, что на стропила крепится обрешетка, по которой уже покрывают крышу кровельным материалом (предварительно также может быть уложена паро- или гидроизоляция, утеплитель и прочее).
Главная задача стропил – это передача нагрузки, получаемой крышей от ветра, на стены здания и внутренние опоры. Также стропила передают нагрузку, оказываемую весом крыши, сугробами снега и пр.
Что представляет собой конструкция стропильной системы? Основная геометрическая фигура, которая применяется в здесь, – это треугольник. По сути, практически любая система стропил – это сочетание разнообразных треугольников. Эта фигура была положена в основу стропильной системы из-за своей жесткой геометрии.
Отметим, что главным элементом стропильной системы являются стропильные ноги, или просто стропила. Они укладываются вдоль ската кровли, по ним строители дальше крепят обрешетку.
Виды стропил
При строительстве стропильной системы могут использоваться два вида стропил:
Висячие стропила опираются только на две опоры – это могут быть, к примеру, стены здания. Такие стропила устанавливаются без дополнительных промежуточных опор. Ноги таких стропил переносят напряжение сжатия и изгиба, а также передают стенам распирающее усилие, которое сами и создают. Для компенсации этого явления строителями обычно используются специальные затяжки горизонтальные либо наклонные, которые соединяют стропильные ноги.
Наслонные стропила обычно используются, когда между наружными стенами есть большой пролет. При их установке ноги опирают о наружные стены, а среднюю часть стропил на промежуточные опоры (это могут колоны, стены) с помощью специальных вертикальных стоек. Эти стойки могут соединяться с затяжками, что позволяет увеличить жесткость стропильной фермы.
Отметим, что часто висячие и наслонные стропила чередуются, все зависит от того, есть ли возможность установить дополнительные промежуточные опоры.
Какие материалы используются для стропил?
Основной материал, который используется для стропильных систем – это дерево. Специалисты отмечают, что деревянные стропила будут пользоваться популярностью еще долгое время.
Еще недавно для стропильной системы в основном применяли бревна и полубревна. Но этот материал требовал значительной подготовки, чтобы придать ему нужные размеры. Более простой в обработке материал – прямоугольный брус. Обычно стропила делают из хвойных пород дерева таких, как лиственница, сосна или ель. Для этих целей используют доску, которая имеет сечение 50х150 или 50х200 мм, иногда большее.
У дерева есть существенный недостаток – со временем от больших нагрузок оно деформируется. Поэтому часто применяют комбинированные стропильные системы из дерева и металла. Последний обычно используется для изготовления опор и площадок под них, разных накладок для усиления ног стропил и пр. Металл с одной стороны позволяет увеличить показатель жесткости всей стропильной системы. Но с другой стороны осложняется эксплуатация такой комбинированной системы из-за оседающего на металле конденсата, что может привести к загниванию деревянных частей, которые соприкасаются с металлом.
Для того чтобы избежать такой ситуации, необходимо проводить тщательную обработку деталей стропильной системы влагозащитными средствами. Может также применяться и пленочная изоляция, которая позволит исключить контакт дерева и металла. Также советуют оборудовать вентиляцию подстропильного пространства. Тем не менее, даже при всех этих мерах, стропила требуют постоянного контроля и ухода.
Существуют и стропильные системы, полностью выполненные из металла. Для этих целей чаще всего применяют стальной прокат, а именно тавра, швеллера, уголок, двутавра и прочее. Такая конструкция отличается большей компактностью, чем деревянные стропила. Недостатки такой системы связанны со свойствами металла – он имеет высокую теплопроводность, и очень быстро остывает и нагревается. Решение этой проблемы – тщательное утепление кровли.
Выбор материала для стропильной системы дома зависит от конструкционных особенностей здания. Оптимально, принимая решение по этому вопросу, посоветоваться с профессионалами.
Автоматизированные производственные системы
Обзор
Программируемые логические контроллеры (ПЛК) являются преобладающим инструментом управления производственными и специальными системы.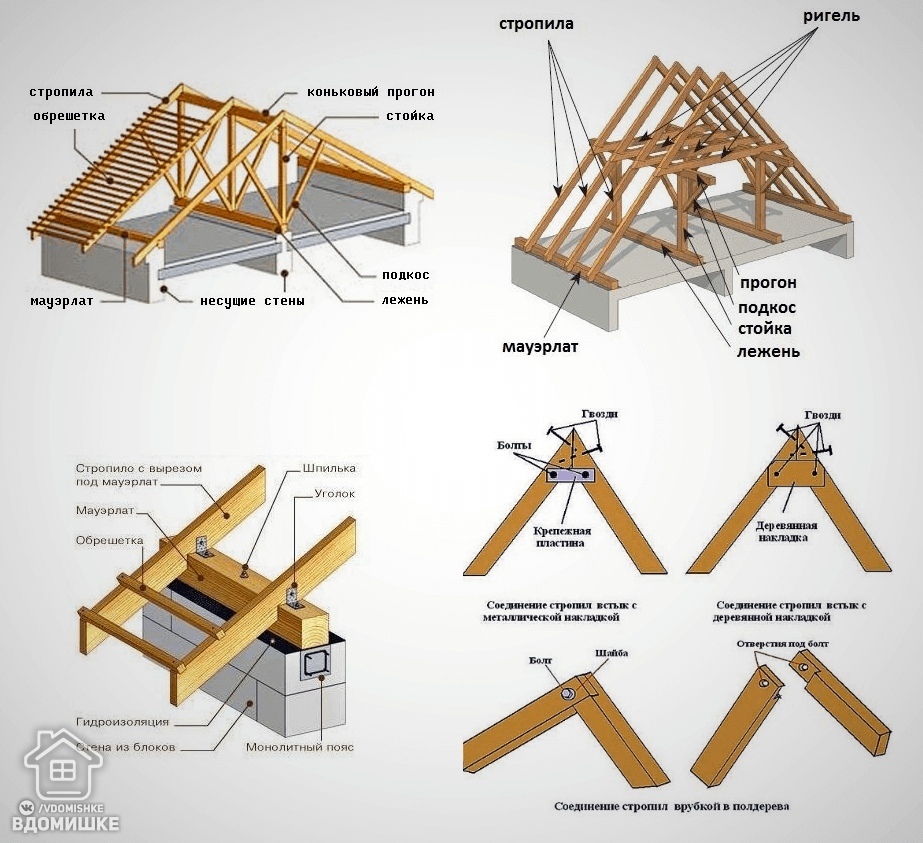
В настоящее время автор использует эту книгу для преподавания на бакалавриате контрольного курса EGR 450 — Manufacturing Controls.
Автор
Доктор Хью Джек, P.Eng. профессор
и председатель отдела дизайна и производства в Grand Valley State
Университет в Гранд-Рапидсе, штат Мичиган, США.
Функции книги
- Подробные главы, посвященные разнообразному оборудованию Allen Bradley
- Многочисленные проблемы, включая онлайн-решения для поддержки обучения
- Краткое содержание главы
- Отрывки и примечания для важной информации
- Книга находится под лицензией GFDL и распространяется бесплатно.
- Сосредоточение внимания на методах проектирования приводит читателя к разработке надежных систем
- Сотни фигур и примеров
(Необязательно) Купить
Хотя книга доступна для скачать бесплатно, у меня были запросы на печатные версии книги.Вы можете приобрести копии книги за 85 долларов на Lulu.com.Ресурсы
Руководства Аллена Брэдли MicrologixControl Logix [1] [2]
Карты ввода / вывода
Panelview [1]
Программирование
Веб-ресурсы, ориентированные на ПЛК
Управляющее программное обеспечение (бесплатное или закрытое)
OAT — Пакет программирования на основе IEC 61131TaskScript — Пакет программирования на основе IEC 61131
Демо-версия RSLogix
Программа Autocad Electrical Wiring
Коммерческое оборудование / программное обеспечение управления
Tek Supply — Продавцы со скидкой AB и другого оборудованияWire + Arc Additive Manufacturing — WAAMMat
AM — это технология, которая обещает снизить стоимость деталей за счет сокращения отходов материала и времени выхода на рынок. Кроме того, AM может также обеспечить большую свободу проектирования, что потенциально приводит к снижению веса, а также упрощает производство сложных узлов, которые ранее состояли из множества подкомпонентов.
Базовая система AM состоит из комбинации системы движения, источника тепла и сырья. Благодаря своим внутренним характеристикам каждый процесс, естественно, подходит для определенных приложений. Например, селективное лазерное плавление позволяет получать компоненты формы сетки с высоким разрешением; однако, как и при электронно-лучевой плавке, скорость осаждения относительно невысока, а размер детали ограничен закрытой рабочей зоной.Следовательно, этот класс процессов лучше всего подходит для небольших компонентов с высокой сложностью. Основными бизнес-факторами их внедрения являются свобода проектирования, настройки и, возможно, сокращение времени вывода на рынок. Выгода, связанная с сокращением количества отходов, ограничена; масса компонентов и так мала изначально. Хотя возможность топологической оптимизации некоторых компонентов важна, растет потребность в большем сокращении отходов материалов. В аэрокосмической промышленности существует острая необходимость в разработке процесса, который мог бы заменить существующий метод производства крупных конструкций, таких как крестообразные конструкции, усиленные панели, нервюры крыла и т. Д., которые изготавливаются из заготовок или крупногабаритных поковок, с высоким соотношением закупок и продаж (BTF) . Эта метрика представляет собой отношение массы исходной заготовки к массе готового изделия; в аэрокосмическом секторе значения 10 или даже 20 не являются чем-то необычным.
Сочетание электрической дуги в качестве источника тепла и проволоки в качестве сырья называется WAAM и исследуется для целей AM с 1990-х годов, хотя первый патент был подан в 1925 году. В настоящее время в оборудовании WAAM используется стандартное готовое сварочное оборудование. : источники сварочного тока, горелки и системы подачи проволоки.Движение может обеспечиваться роботизированными системами или портальными станциями с числовым программным управлением. По возможности предпочтительным методом является MIG: проволока является расходуемым электродом, а ее соосность со сварочной горелкой обеспечивает более легкий путь инструмента. MIG идеально подходит для таких материалов, как алюминий и сталь, но, к сожалению, с титаном на этот процесс влияет блуждание дуги. Следовательно, в настоящее время для осаждения титана используется вольфрамовый инертный газ или плазменная дуговая сварка.
Аддитивное производство в авиакосмической промышленности> ИНЖИНИРИНГ.com
Топливная форсункаCFM International, напечатанная на 3D-принтере. (Изображение любезно предоставлено GE.)
Аэрокосмическая промышленность продолжает находить новые применения для аддитивного производства.Используется ли она для изготовления прототипов и деталей с меньшими затратами или для создания конструкций, недостижимых при традиционном производстве, 3D-печати некуда идти, кроме как вверх.
Одной из сфер деятельности, которую разделяют многие аэрокосмические компании, является создание двигателей с использованием технологий 3D-печати, от реактивных турбин до ракетных двигателей.
Начиная от акцента НАСА на создании полностью 3D-печатного ракетного двигателя до GE, увеличивающего использование 3D-печати в производстве деталей реактивных двигателей. Даже ВВС заключили контракт с SpaceX с акцентом на более широкое использование 3D-печати при производстве ракетных двигателей.
Использование 3D-печати в двигателях рассматривается всеми этими компаниями и государственными учреждениями как ценное вложение. Во всех этих ситуациях лазерное спекание является наиболее популярным методом 3D-печати для создания прочных металлических деталей для авиационно-космических двигателей.
Струйные двигатели для 3D-печати
GE имеет один из самых известных случаев внедрения 3D-печати в производство реактивных двигателей. В 2016 году компания создала топливные форсунки для своего нового семейства двигателей LEAP, используя прямое лазерное плавление металла. Это превращает тонкие слои металлического порошка в полностью твердые металлические детали, используя лазер для плавления порошка там, где конструкторы хотят, чтобы детали застыли.
LEAP A1. (Изображение любезно предоставлено GE.)
3D-печать позволила снизить вес сопел на 25 процентов, количество деталей, используемых для создания сопла, было уменьшено с 18 до 1, а также более сложные пути охлаждения и опоры, что дало сопло пятикратное увеличение. в прочности.Эти форсунки не являются прототипами. В апреле 2016 года GE отправила Airbus первые два серийных двигателя LEAP-1A с 19 соплами, напечатанными на 3D-принтере. Двигатели LEAP, использующие эти форсунки, примерно на 15 процентов более экономичны, чем их аналоги.
Промышленность была чрезвычайно восприимчива к этим двигателям: уже выполнено более 10 000 заказов на сумму около 145 миллиардов долларов.
В конце декабря 2016 года был сделан еще один важный шаг вперед для двигателей LEAP и их сопел, напечатанных на 3D-принтере.Реактивный двигатель LEAP-1C был одобрен Федеральным авиационным управлением (FAA) и Европейской ассоциацией авиационной безопасности (EASA).
Аддитивное производство в НАСА
В прошлом году НАСА объявило о достижении важной вехи в создании полностью напечатанного на 3D-принтере ракетного двигателя. В Центре космических полетов имени Маршалла в Хантсвилле, штат Алабама, была успешно проведена серия из 12 испытательных запусков нового прототипа ракетного двигателя, напечатанного на 3D-принтере НАСА.
Грэм Нельсон (справа) и Эндрю Хэнкс исследуют камеру сгорания, разработанную инженерами Центра космических полетов им. Маршалла НАСА в Хантсвилле, штат Алабама, для проекта демонстрационного двигателя аддитивного производства. (Изображение любезно предоставлено NASA / MSFC / Charles Beason.)
Турбонасос, топливная форсунка, клапаны и несколько других основных компонентов двигателя были напечатаны на 3D-принтере. Однако проект создания полностью 3D-печатного двигателя не завершен, основным препятствием является главная камера сгорания.Еще в 2015 году НАСА завершило разработку прототипа двигателя, 75 процентов которого было сделано из деталей, напечатанных на 3D-принтере, а также первую часть полномасштабного медного ракетного двигателя.
При испытании прототипа двигателя использовалась камера сгорания, которая разрушается во время горения. Эта эрозия изменяет внутреннее давление в двигателе, позволяя запускать только 10 секунд. Однако, используя новую (не напечатанную на 3D-принтере) камеру сгорания в более поздних тестах, двигатель смог проработать 30 секунд, а при необходимости — и дольше.
«Система — это не просто сумма частей, соединенных вместе. Это продукт взаимодействия частей. Мы пытаемся понять и управлять этими взаимодействиями», — сказал Ник Кейс, ведущий системный аналитик проекта. «В то же время мы должны понимать характеристики отдельных деталей, напечатанных на 3D-принтере. Это то, что нам позволил сделать этот тест ».
Это недавнее испытание основано на предыдущих достижениях команды и приближает их к конечной цели — полностью напечатанному на 3D-принтере ракетному двигателю.Этот последний двигатель сократит время и затраты на разработку по сравнению с двигателями, производимыми традиционным способом, и будет включать в себя некоторые детали, которые невозможно было изготовить в традиционных условиях.
«С нашей новой камерой и более длинными обжигами мы можем создать тестовую среду, которая намного ближе к нашей проектной точке для этого проекта», — сказал Эндрю Хэнкс, руководитель тестирования проекта.
В этом году команда надеется протестировать почти 100-процентную систему 3D-печати. Этот двигатель будет служить прототипом, который будет влиять на коммерческий дизайн.
Следующим важным шагом к достижению этой цели станет добавление напечатанного на 3D-принтере турбонасоса окислителя, который изготавливается в рамках совместной разработки с программой Game Changing Development Управления космических технологий НАСА.
Эта же программа также финансирует разработку 3D-печатной камеры сгорания.
Данные о характеристиках материалов и характеристиках 3D-печатных деталей будут доступны в Системе технической информации НАСА по материалам и процессам (MAPTIS) для утвержденных пользователей.
3D-печать в SpaceX
Использование 3D-печати при разработке и производстве двигателей не менее распространено в коммерческом космическом секторе.
В 2015 году ВВС США выделили Orbital ATK и SpaceX совместные контракты на 241 миллион долларов на разработку прототипов ракетных двигателей. SpaceX, в свою очередь, инвестирует 67 миллионов долларов с целью разработки прототипа многоразовой силовой установки Raptor.
Пробный пуск двигателя Raptor. (Изображение любезно предоставлено SpaceX.)
Система Raptor — самый мощный двигатель SpaceX, в котором используется множество деталей, напечатанных на 3D-принтере, в том числе турбонасос. Один из двигателей Raptor, протестированных SpaceX в прошлом году, состоял из более чем 40 процентов деталей, напечатанных на 3D-принтере.Эта силовая установка используется в верхней ступени ракет Falcon 9 и Falcon Heavy и, вероятно, будет использоваться в будущих миссиях SpaceX на Марс.
Все эти мощные аэрокосмические компании, а также государственные программы, сфокусированные на продвижении 3D-печати металлом для применения в авиакосмических двигателях, намекают на то, что 2017 год станет большим годом для аддитивного производства.