Блок из щепы и цемента: Арболитовые блоки — недостатки, технические характеристики, размеры, состав
Арболитовые блоки — недостатки, технические характеристики, размеры, состав
Арболит в большинстве источников описывается, как материал, обладающий чудесными свойствами. Рекламные статьи превозносят арболитовые блоки, недостатки материала скромно умалчиваются. Но чудес не бывает, недостатки тоже есть. Чтобы по максимуму использовать положительные качества и нивелировать отрицательные, стоит хорошенько разобраться со свойствами арболита, его характеристиками и особенностями применения.
Состав и производство арболиттовых блоков
Начнем наш материал именно с состава и процесса производства. Все дело в том, что от качества выполнения определенных процессов зависит наличие или отсутствие определенных недостатков материала. А это является очень важным. Арболит позиционируется, как одна из разновидностей крупноячеистых легких бетонов. В качестве наполнителя в нем используется древесная щепа. Щепа связывается в монолитную структуру цементным тестом.
Материал используется в строительстве в нескольких видах:
- крупноформатные кладочные блоки;
- пустотелые блоки;
- теплоизоляционные плиты;
- смеси для заливки ограждающих конструкций по месту.
Кладочные блоки нашли наиболее широкое применение и под понятием «арболит» понимаются, прежде всего, они. Самым распространенным размером арболитовых блоков является 500×300×200 мм. Но в последние время производители стали расширять свои производственные линейки и предлагают арболит в других типоразмерах.
Технология изготовления блоков относительно проста, но как и везде, имеются свои тонкости. Качество будущих изделий зависит от соблюдения нескольких важных производственных моментов. Если производитель использует в наименовании своей продукции термин «арболит», он должен соблюдать требования нормативной документации на такие изделия, это:
- ГОСТ 19222-84 «Арболит и изделия из него. Общие технические условия».
- СН 549-82 «Инструкция по проектированию, изготовлению и применению конструкций и изделий из арболита».
Состав арболитовых блоков
Для изготовления арболитовых блоков используется:
- Древесная щепа;
- Химические добавки;
- Вода;
- Цемент.
#1. Древесная щепа. Итоговая прочность сильно зависит от калибра щепы. Чтобы на выходе был именно арболит, свойства которого строго нормированы, для производства должна использоваться именно щепа. Ее размеры регламентированы. ГОСТ рекомендует максимальный размер частиц 40×10×5 мм (длина/ширина/толщина).
Наилучшие показатели у блоков с размерами щепы из интервалов:
- длина – до 25 мм;
- ширина – 5..10 мм;
- толщина – 3..5 мм.
Опилки, стружки, тырса, костра, солома и все остальное, что пытаются смешивать с цементом для производства арболита, для его изготовления не подходит. Только чистая щепа без коры, листьев, грунта и прочих нежелательных примесей. Считается, что добавление до 10 % коры или 5 % листвы не оказывает серьезного влияния на характеристики арболита. Но лучше когда эти примеси отсутствуют.
Зачастую производства арболитовых блоков, организованы при лесопилках и других деревоперерабатывающих предприятиях. Для них арболит не является профильным направлением. В результате недобросовестные производители, для увеличения рентабельности производства, кроме самой щепы добавляют то, что имеется. Отсюда непредсказуемое качество продукции.
На специализированных предприятиях устанавливают производительные валковые дробилки, откалиброванные под нужный размер щепы.
Для конечного потребителя не имеет большого значения сорт древесины, из которой производится сырье, но технологи должны это учитывать для правильной дозировки минерализаторов и выбора степени уплотнения. Так, щепа лиственницы требует двойного количества добавок относительно других хвойных пород. Чаще других на производство щепы идут сосна, ель, реже лиственные породы.
#2. Химические добавки. Древесный наполнитель содержит сахара, которые препятствуют качественной адгезии цементного теста с поверхностью частичек дерева.
Для решения этой проблемы применяются 2 основные стратегии:
- 1.
Высушивание древесного сырья до применения в производстве в течение нескольких месяцев.
- 2. Минерализация поверхности щепы в растворе химических компонентов.
Наилучшие результаты достигаются при комплексном подходе к решению задачи. Снижение содержания сахаров и минерализация сырья позволяет решить и другие важные задачи:
- повышение биологической стойкости материала;
- снижение водопроницаемости при эксплуатации готового изделия.
Для решения всех этих задач, при производстве арболита могут использоваться следующие компоненты: хлорид кальция (ГОСТ 450–77), жидкое стекло (ГОСТ 13078–67), силикат-глыба (ГОСТ 13079–67), сернокислый глинозем (ГОСТ 5155–74), известь (ГОСТ 9179–77).
#3. Вода. Получать арболитовые блоки, характеристики которых соответствуют заданным, можно, следуя определенному порядку технологических операций. Вода с добавлением минерализаторов готовится заранее. Расход компонентов принимается в следующих соотношениях:
Добавка | CaCl2 | Al2(SO4)3 | Al2(SO4)3+ Ca(OH)2 |
---|---|---|---|
Расход на 1м3 арболита, кг | 12 | 12 | 8+4 |
Щепа засыпается в смеситель принудительного действия. Обычные гравитационные бетономешалки не обеспечивают достаточной гомогенизации. Вода с растворенным минерализатором перемешивается и равномерно распределяется по поверхности щепы. Перемешивание происходит на протяжении 20 секунд. На следующей стадии происходит добавление цемента. Перемешивание с цементом длится 3 минуты.
#4.Цемент. Достаточная для применения в строительстве прочность материала достигается только при применении цемента с маркой не ниже 400. Цемент имеет свойство быстро терять марку при хранении. Даже на выходе с завода цемент часто не соответствует заявленным характеристикам. Поэтому лучше когда, арболитовые блоки, технические характеристики которых должны соответствовать требованиям, предъявляемым к конструкционным материалам, изготавливаются из 500-го цемента.
Формование блоков
Формование необходимо завершить в течении ближайших 15 минут после перемешивания. В зависимости от степени механизации последующих процессов различают следующие способы формования:
- ручное формование без вибрирования;
- ручное формование с вибрированием;
- производство на вибростанке;
- производство на вибростанке с пригрузом.
Механизация процессов позволяет получать более высокие по качеству и стабильные по параметрам арболитовые блоки. При этом размеры, геометрия и плотность сохраняются от изделия к изделию.
Выдерживание изделия в опалубке применяют при кустарном производстве, когда снятию опалубки сразу после формования препятствует слишком жидкая консистенция раствора. В общем случае формы снимают без выдержки.
Сырые блоки остаются на съемном днище-поддоне или прямо на полу цеха.
Арболитовые блоки, состав которых одинаков, могут получать различные характеристики в зависимости от способа и степени их уплотнения. Основной целью прессования смеси в форме не является повышение ее плотности. Главная задача – это создание равномерно распределенной по объему структуры из произвольно ориентированной, полностью укрытой цементным тестом, щепы.
Вибрация при уплотнении применяется очень дозировано. Чрезмерное вибрирование приводит к осаждению цементного теста на дне формы. Важно сохранять его равномерное распределение по объему с полным укрытием зерен наполнителя. Даже в арболите высокой плотности щепа не плавает в растворе цемента с водой. Цементное тесто работает, как клей, покрывающий зерна наполнителя. Меняется только концентрация щепы в объеме и толщина покрывающего ее цементного камня.
Уплотнение блоков производится на значения, достаточные для взаимной переориентации зерен наполнителя и увеличения площади их соприкосновения. Сжатия и деформации самой щепы не происходит. Это обеспечивает сохранение размеров блока после снятия уплотняющего усилия.
Необходимость точной дозировки всех компонентов и соблюдения технологии
Точность дозирования компонентов регламентируется ГОСТом. Допустимые отклонения не могут превышать нескольких процентов. В условиях недостатка воды не происходит гидратация всего объема цемента. Ее избыток нежелателен по нескольким причинам:
- Превышение водоцементного соотношения снижает прочность.
- Избыточная пластичность препятствует выниманию сырого блока из формы непосредственно после формования.
- Увеличивается время хранения блока на поддоне до первичного схватывания.
Концентрация минерализаторов щепы, идущей в арболит, важна для прочности и долговечности материала. Дозировки компонентов, приводимые в нормативах, рассчитаны на определенный калибр заполнителя и его влажность на уровне 25 %. Оптимальную дозировку подбирают опытным путем на основе испытаний готовых образцов.
Для протекания процесса гидратации важна температура раствора воды с минерализаторами. Она не должна быть меньше 15 °С. Для набора необходимой температуры в холодное время года воду подогревают или выдерживают в отапливаемом помещении. Возможен также химический нагрев воды при применении в качестве минерализатора CaCl2.
Плотность арболита
По назначению материал условно делят на 2 типа:
- теплоизоляционный;
- конструкционный.
Определяющим фактором является плотность изделия. Считается, что блоки с плотностью до 500 кг/м3 не подходят для использования в составе несущих конструкций.
Типичными для конструкционных блоков являются значения плотности из интервала от 550 до 700 кг/м3. Но можно купить изделия и с плотностью до 850 кг/м3. Слишком высокие величины указывают на хорошую несущую способность элементов, но уступают более легким в теплоизоляционных качествах. Плотность материала замеряется при установившейся массе, когда блок прекращает терять влагу.
Стены из литого арболита могут иметь плотность порядка 300 кг/м3, но по несущей способности не уступают сложенным из камней с плотностью 550 кг/м3.
Прочность арболитовых блоков
Несущая способность блоков характеризуется их прочностью на сжатие. По результатам испытаний изделиям может присваиваться марка и класс по прочности на сжатие. В общем случае они связаны с плотностью материалов.
Плотность, кг/м3 | Марка | Класс |
---|---|---|
400 — 500 | М 5 | В 0,35 |
450 — 500 | М 10 | В 0,75 |
500 | М 15 | В 1,0 |
500 — 650 | — | В 1,5 |
500 — 700 | М 25 | В 2,0 |
600 — 750 | М 35 | В 2,5 |
700 — 850 | М 50 | В 3,5 |
Как и в случае изделий из тяжелого бетона, марка является средней величиной по результатам испытаний партии образцов. Класс характеризует гарантированную прочность, 95 % образцов должны соответствовать по классности.
Для реальных испытаний с хорошей выборкой зависимость между маркой и классом через переводные коэффициенты не является корректной. В этом случае разрыв между маркой и классом может рассказать о культуре производства на предприятии. Чем меньше разрыв, тем выше организация производства. В отечественной практике изготовления арболитовых блоков это учитывается с помощью коэффициентов вариации. Для изделий 1-ой категории качества допускается значение 18 %, для высшей – 15 %.
В кирпичной кладке мелкий размер изделий делает понятие классности бессмысленным. При покупке крупных кладочных камней, каковыми и являются арболитовые блоки, стоит отдавать предпочтение изделиям с присвоенным классом.
Для возведения несущих стен одноэтажных зданий высотой до 3 м допускается использовать блоки класса от B 1.0. Для более высоких стен нужны элементы класса от B 1.5. Для 2-х — 3-х этажных строений используют блоки классов B 2. 0 и B 2.5.
Прочность арболита на сжатие типична для ячеистых бетонов. Важным отличием является прочность блоков на изгиб, которая составляет от 0,7 до 1,0 МПа. Модуль упругости элементов может доходить до 2300 МПа. Такие величины делают арболит особенным среди ячеистых бетонов. Если для пенобетона и газобетона велика вероятность трещинообразования, то для арболита такая проблема не стоит.
Читайте также:
Теплопроводность арболита
Теплопроводность для арболита является одним из ключевых параметров.
Она растет с увеличением его плотности в следующей прогрессии:
Рекомендованная ГОСТом толщина ограждающих конструкций из арболита в умеренных широтах составляет 38 см. Но стены такой толщины возводятся редко. На практике для стен жилых домов блоки 500×300×200 мм кладут плашмя в один ряд. Вместе с внутренней и наружной отделкой этого достаточно для поддержания комфортной температуры в помещениях без появления проблем с выпадением конденсата.
Дополнительная теплоизоляция часто выполняется с помощью теплых штукатурных систем толщиной 1,5-2 см с добавкой перлита. Для не отапливаемых или периодически отапливаемых помещений (бани) нередко применяют кладку блоков на ребро.
Влагопоглощение арболита
В характеристиках арболита указывают величину водопоглощения до 85 % для теплоизоляционных блоков и до 75 % для конструкционных. Эти значения требуют осмысления. Структура блока представляет собой склеенные цементным камнем разрозненные зерна щепы. Они ориентированы относительно друг друга случайным образом.
Вода, наливаемая на поверхность блока, свободно протекает сквозь него. Естественно, что при окунании вода способна вытеснить большой объем содержащегося внутри блока воздуха. Если блок вытащить из воды, вода вытекает, а цементный камень быстро высыхает.
Арболитовые блоки находящиеся в естественной среде, например в стене дома, фактически не накапливают в себе влагу из окружающего воздуха.
Это происходит благодаря очень низкой сорбционной влажности материала, т. к. минерализованные щепа и цемент являются негигроскопичными и слабо смачивающимися материалами. Именно это стало причиной популярности использования материала для строительства бань.
Если поливать ничем не закрытую стену из арболита с внешней стороны водой, есть вероятность увидеть ее и внутри. Поэтому материал не используют без фасадной отделки. Для арболита рекомендуют отделку штукатурными растворами или устройство навесных фасадных систем.
Морозостойкость
Постепенное разрушение изделий при замораживании и размораживании происходит в результате расширения замерзающей в пустотах воды. Чем больше воды в них содержится, тем меньше циклов замораживания — размораживания способен выдержать материал без разрушения.
Низкое сорбционное влагопоглощение дает арболиту хорошую стойкость к промерзанию. Минимальное значение составляет F25 и доходит до F50. Защита арболита от прямого воздействия влаги, позволяет повысить реальную морозостойкость материала в конструкции. Кроме этого существуют реальные примеры эксплуатации зданий из арболита на протяжении 7 — 10 лет без повреждений для стен. Причем речь идет о стенах, которые ни чем не защищены от воздействия внешних факторов среды.
Усадка материала
Считается, что арболит совершенно не подвержен усадке. Но небольшие усадочные процессы в первые месяцы все же присутствуют. В основном они прекращаются еще на этапе созревания блока на производстве. Некритичное уменьшение размеров блока (на 0,4 — 0,8 %) возможно уже после укладки блоков в конструкцию.
Некоторое сокращение высоты блоков может происходить и под весом вышележащих элементов, перекрытий и конструкций кровли. Для предотвращения проблем с отделкой не рекомендуется выполнять штукатурные работы в первые 4 месяца после завершения основного комплекса работ.
Огнестойкость арболитовых блоков
По огнестойкости арболитовые блоки имеют следующие параметры:
- группа горючести — Г1, т. е. это трудногорючий материал;
- группа воспламеняемости — В1, трудновоспламеняемый материал;
- по дымообразующей способности — Д1, малодымообразующий материал.
Звукоизоляция
По шумопоглощению арболитовые блоки превосходят такие материалы как кирпич и древесина. Коэффициент шумопоглощения арболитовых блоков составляет 0,17 — 0,6 в акустическом диапазоне от 135 до 2000 Гц.
Паропроницаемость
Арболит это дышащий материал степень его паропроницаемости составляет до 35 %. Именно поэтому в домах построенных из данного материала не бывает сырости, а микроклимат комфортный как в холодное так и в теплое время года.
Недостатки арболитовых блоков
Как бы ни был хорош арболит, недостатки материала все же стоит знать и учитывать.
Поколебать решимость застройщика способны несколько сомнительных моментов:
— 1. Обилие на рынке блоков «гаражного» качества.
Их прочность, сопротивление теплопередаче неведомы даже производителю. Имеются трудности с приобретением заводского арболита в регионах. Выше мы писали про самые важные моменты производства арболитовых блоков. Как вы понимаете выполнить определенные задачи в кустарных условиях просто не возможно.
— 2. Недостаточная точность геометрии.
Точность геометрии арболитовых блоков уступает таковой у других легкобетонных кладочных камней (пенобетона, газобетона). Особенно это характерно для производств с большой долей ручного труда. Отклонения в размерах и взаимном расположении поверхностей заставляют увеличивать толщину швов до 10 — 15 мм. А это влечет промерзание кладки по швам, перерасход материала и снижение скорости кладочных работ.
Производители рекомендуют использовать для кладки теплые перлитовые растворы, но их приготовление обходится дороже. В последнее время для улучшения геометрии блоков начинают применять фрезерование поверхностей.
— 3. Необходимость защиты от прямого воздействия влаги.
Ничем не защищенная кладка в теории может быть проницаемой для больших напоров ветра, но реального подтверждения такого явления не получено. Нанесение на поверхность штукатурных покрытий решает проблемы с проницаемостью.
— 4. Высокая стоимость арболитовых блоков.
Это связано с недостаточными автоматизацией производственных процессов, степенью проработки технологии и скромными объемами производства. В итоге себестоимость пенобетонных и газобетонных блоков ниже в 1,5 раза.
— 5. Наличие ограничений в выборе отделочных материалов.
Для правильной эксплуатации важно сочетать с арболитовой кладкой только «дышащие» варианты отделки.
Достоинства арболитовых блоков
Тех, кто решается на строительство по арболитовой технологии, должны вдохновлять ее многочисленные достоинства:
+ 1. Экологичность материала.
Даже входящие в его состав минерализаторы не выделяют в атмосферу вредных веществ.
+ 2. Высочайшая паропроницаемость.
+ 3. Легкость материала.
Легкость материала и его упругость не требуют устройства мощного и жесткого фундамента. Дополнительным бонусом является сейсмостойкость.
+ 4. Легкость обработки.
+ 5. Простой монтаж крепежа.
В арболит можно вбивать гвозди и вкручивать саморезы, как в дерево.
+ 6. Низкая теплопроводность.
Отличное сопротивление теплопередаче при достаточной для малоэтажного строительства прочности позволяет обходиться без дополнительного утепления и получать однослойную структуру стены.
+ 7. Низкая звукопроницаемость.
+ 8. Отказ от армирования.
Возможность отказаться от армирования кладки и устройства монолитных поясов на небольших объектах.
+ 9. Биологическая стойкость.
+ 10. Негорючесть.
Если вы заметили ошибку, не рабочее видео или ссылку, пожалуйста, выделите фрагмент текста и нажмите Ctrl+Enter.
Блоки Арболита — как и из чего производится, возможно ли сделать самому?
Арболитом называют блоки, изготовленные из основных трех компонентов — это древесная щепа (она должна быть из хорошей древисины, без коры и гнили), из-за которой блок и получил название арболит, что означает от французского слова arbre в переводе — дерево, а также сульфат алюминия и цемент, это если арболит изготавливается в промышленных условиях.
В зависимости от назначения арболитового блока они могут быть как конструкционные для возведения стен в основном, также и теплоизоляционные.
Арболитовые блоки можно изготовить в домашних условиях, но для этого необходимо иметь некоторое оборудование и материал.
Самое главное для арболитовых блоков — это вибростанок, если данный станок отсутствует то любой процесс изготовления блоков уже будет отличаться от арболита.
Сам процесс состоит из нескольких этапов, для начала нужно древесную щепу замочить примерно на 3-4 часа в гашеной извести, в основном известь разводят в пропорции один к десяти, то есть одна часть извести и десять частей воды.
Далее древесную щепу откидывают на сито чтобы стекла лишняя вода с известью и загружают в бетономешалку.
В бетономешалке гашеная древесная щепа разводится с водой примерно на 3 массы (по весу) щепы на 4 объёма воды, бетономешалка включается на режим замеса и после смачивания дерева в водную массу добавляют примерно 1% жидкого стекла.
Хорошо перемешайте щепу, даже если не видите в этом смысла, и начинайте добавлять где-то 4 массы от объема щепы цемента, лучше всего М500 использовать. Мешайте достаточно хорошо чтобы вся масса стала тягучей липла в руках.
Далее эту масла надо залить в специально подготовленные формы и установить на вибростол примерно минут на 10-20 (в зависимости от силы вибрации.
Далее на 24 часа оставляйте форму с залитой массой в темном теплом помещении, через сутки блок вытаскиваете и оставляете для просушки ещё на неделю на открытой площадке, обдуваемый воздухом, но защищенном от прямых солнечных лучей. Между блоками обязательно должно быть расстояние не менее 10 сантиметров.
Форму для изготовления блоков лучше всего делать из дерева или пластмассы, стандартный размер длина 510 мм ширина 250 мм высота 215 мм, их можно также сделать с пустотами и без пустот со сквозными или половинчатыми.
Арболитовые блоки — недостатки, достоинства и характеристики | Статьи о строительных материалах
Арболит в большинстве источников описывается, как материал, обладающий чудесными свойствами. Рекламные статьи превозносят арболитовые блоки, недостатки материала скромно умалчиваются. Но чудес не бывает, недостатки тоже есть. Чтобы по максимуму использовать положительные качества и нивелировать отрицательные, стоит хорошенько разобраться со свойствами арболита, его характеристиками и особенностями применения.
Состав и производство арболитовых блоков.
Начнем наш материал именно с состава и процесса производства. Все дело в том, что от качества выполнения определенных процессов зависит наличие или отсутствие определенных недостатков материала. А это является очень важным. Арболит позиционируется, как одна из разновидностей крупноячеистых легких бетонов. В качестве наполнителя в нем используется древесная щепа. Щепа связывается в монолитную структуру цементным тестом.
Предлагаем напрямую с производства строительные материалы по ценам ниже рыночных. Делаем доставку, возможен самовывоз. Снабжаем строительные объекты, строительные рынки. Ищем партнеров для сотрудничества , снабженцев:
——————————————————————————
Материал используется в строительстве в нескольких видах:
крупноформатные кладочные блоки;
пустотелые блоки;
теплоизоляционные плиты;
смеси для заливки ограждающих конструкций по месту.
Кладочные блоки нашли наиболее широкое применение и под понятием «арболит» понимаются, прежде всего, они. Самым распространенным размером арболитовых блоков является 500х300х200 мм. Но в последние время производители стали расширять свои производственные линейки и предлагают арболит в других типоразмерах.
Технология изготовления блоков относительно проста, но как и везде, имеются свои тонкости. Качество будущих изделий зависит от соблюдения нескольких важных производственных моментов. Если производитель использует в наименовании своей продукции термин «арболит», он должен соблюдать требования нормативной документации на такие изделия, это:
1. ГОСТ 19222-84 «Арболит и изделия из него. Общие технические условия».
2. СН 549-82 «Инструкция по проектированию, изготовлению и применению конструкций и изделий из арболита».
Состав арболитовых блоков.
Для изготовления арболитовых блоков используется:
Древесная щепа;
Химические добавки ;
Вода;
Цемент .
Структура арболитовых блоков.
1. Древесная щепа.
Итоговая прочность сильно зависит от калибра щепы. Чтобы на выходе был именно арболит, свойства которого строго нормированы, для производства должна использоваться именно щепа. Ее размеры регламентированы. ГОСТ рекомендует максимальный размер частиц 40х10х5 мм (длина/ширина/толщина).
Наилучшие показатели у блоков с размерами щепы из интервалов:
длина – до 25 мм;
ширина – 5…10 мм;
толщина – 3…5 мм.
Опилки, стружки, тырса, костра, солома и все остальное, что пытаются смешивать с цементом для производства арболита, для его изготовления не подходит. Только чистая щепа без коры, листьев, грунта и прочих нежелательных примесей. Считается, что добавление до 10% коры или 5% листвы не оказывает серьезного влияния на характеристики арболита. Но лучше когда эти примеси отсутствуют.
Зачастую производства арболитовых блоков, организованы при лесопилках и других деревоперерабатывающих предприятиях. Для них арболит не является профильным направлением. В результате недобросовестные производители, для увеличения рентабельности производства, кроме самой щепы добавляют то, что имеется. Отсюда непредсказуемое качество продукции.
Щепа для арболитовых блоков.
На специализированных предприятиях устанавливают производительные валковые дробилки, откалиброванные под нужный размер щепы.
Для конечного потребителя не имеет большого значения сорт древесины, из которой производится сырье, но технологи должны это учитывать для правильной дозировки минерализаторов и выбора степени уплотнения. Так, щепа лиственницы требует двойного количества добавок относительно других хвойных пород. Чаще других на производство щепы идут сосна, ель, реже лиственные породы.
2. Химические добавки.
Древесный наполнитель содержит сахара, которые препятствуют качественной адгезии цементного теста с поверхностью частичек дерева.
Для решения этой проблемы применяются 2 основные стратегии:
1. Высушивание древесного сырья до применения в производстве в течение нескольких месяцев.
2. Минерализация поверхности щепы в растворе химических компонентов.
Наилучшие результаты достигаются при комплексном подходе к решению задачи. Снижение содержания сахаров и минерализация сырья позволяет решить и другие важные задачи:
повышение биологической стойкости материала;
снижение водопроницаемости при эксплуатации готового изделия.
Для решения всех этих задач, при производстве арболита могут использоваться следующие компоненты: хлорид кальция (ГОСТ 450–77), жидкое стекло (ГОСТ 13078–67), силикат-глыба (ГОСТ 13079–67), сернокислый глинозем (ГОСТ 5155–74), известь (ГОСТ 9179–77).
3. Вода.
Получать арболитовые блоки, характеристики которых соответствуют заданным, можно, следуя определенному порядку технологических операций. Вода с добавлением минерализаторов готовиться заранее. Расход компонентов принимается в следующих соотношениях:
ДОБАВКА CACL2 AL2(SO4)3 AL2(SO4)3+ CA(OH)2
Расход на 1м3 арболита, кг 12 12 8+4
Щепа засыпается в смеситель принудительного действия. Обычные гравитационные бетономешалки не обеспечивают достаточной гомогенизации. Вода с растворенным минерализатором перемешивается и равномерно распределяется по поверхности щепы. Перемешивание происходит на протяжении 20 секунд. На следующей стадии происходит добавление цемента. Перемешивание с цементом длится 3 минуты.
4. Цемент . Достаточная для применения в строительстве прочность материала достигается только при применении цемента с маркой не ниже 400. Цемент имеет свойство быстро терять марку при хранении. Даже на выходе с завода цемент часто не соответствует заявленным характеристикам. Поэтому лучше когда, арболитовые блоки, технические характеристики которых должны соответствовать требованиям, предъявляемым к конструкционным материалам, изготавливаются из 500-го цемента.
Формование блоков.
Формование необходимо завершить в течении ближайших 15 минут после перемешивания. В зависимости от степени механизации последующих процессов различают следующие способы формования:
ручное формование без вибрирования;
ручное формование с вибрированием;
производство на вибростанке;
производство на вибростанке с пригрузом.
Механизация процессов позволяет получать более высокие по качеству и стабильные по параметрам арболитовые блоки. При этом размеры, геометрия и плотность сохраняются от изделия к изделию.
Выдерживание изделия в опалубке применяют при кустарном производстве, когда снятию опалубки сразу после формования препятствует слишком жидкая консистенция раствора. В общем случае формы снимают без выдержки.
Блоки на поддоне.
Сырые блоки остаются на съемном днище-поддоне или прямо на полу цеха.
Арболитовые блоки, состав которых одинаков, могут получать различные характеристики в зависимости от способа и степени их уплотнения. Основной целью прессования смеси в форме не является повышение ее плотности. Главная задача – это создание равномерно распределенной по объему структуры из произвольно ориентированной, полностью укрытой цементным тестом, щепы.
Вибрация при уплотнении применяется очень дозировано. Чрезмерное вибрирование приводит к осаждению цементного теста на дне формы. Важно сохранять его равномерное распределение по объему с полным укрытием зерен наполнителя. Даже в арболите высокой плотности щепа не плавает в растворе цемента с водой. Цементное тесто работает, как клей, покрывающий зерна наполнителя. Меняется только концентрация щепы в объеме и толщина покрывающего ее цементного камня.
Уплотнение блоков производится на значения, достаточные для взаимной переориентации зерен наполнителя и увеличения площади их соприкосновения. Сжатия и деформации самой щепы не происходит. Это обеспечивает сохранение размеров блока после снятия уплотняющего усилия.
Необходимость точной дозировки всех компонентов и соблюдения технологии
Точность дозирования компонентов регламентируется ГОСТом. Допустимые отклонения не могут превышать нескольких процентов. В условиях недостатка воды не происходит гидратация всего объема цемента. Ее избыток нежелателен по нескольким причинам:
Превышение водоцементного соотношения снижает прочность.
Избыточная пластичность препятствует выниманию сырого блока из формы непосредственно после формования.
Увеличивается время хранения блока на поддоне до первичного схватывания.
Концентрация минерализаторов щепы, идущей в арболит, важна для прочности и долговечности материала. Дозировки компонентов, приводимые в нормативах, рассчитаны на определенный калибр заполнителя и его влажность на уровне 25%. Оптимальную дозировку подбирают опытным путем на основе испытаний готовых образцов.
Для протекания процесса гидратации важна температура раствора воды с минерализаторами. Она не должна быть меньше 15°С. Для набора необходимой температуры в холодное время года воду подогревают или выдерживают в отапливаемом помещении. Возможен также химический нагрев воды при применении в качестве минерализатора CaCl 2 .
Плотность арболита.
По назначению материал условно делят на 2 типа:
теплоизоляционный;
конструкционный.
Определяющим фактором является плотность изделия. Считается, что блоки с плотностью до 500 кг/м3 не подходят для использования в составе несущих конструкций. Но они могут применяться для теплоизоляции при возведении наружных стен в строениях, где нагрузка от кровли или перекрытий воспринимается колонами или другими элементами.
Типичными для конструкционных блоков являются значения плотности из интервала от 550 до 700 кг/м3. Но можно купить изделия и с плотностью до 850 кг/м3. Слишком высокие величины указывают на хорошую несущую способность элементов, но уступают более легким в теплоизоляционных качествах. Плотность материала замеряется при установившейся массе, когда блок прекращает терять влагу.
Стены из литого арболита могут иметь плотность порядка 300 кг/м3, но по несущей способности не уступают сложенным из камней с плотностью 550 кг/м3.
Сравнение плотности арболита и других материалов.
Прочность арболитовых блоков.
Несущая способность блоков характеризуется их прочностью на сжатие. По результатам испытаний изделиям может присваиваться марка и класс по прочности на сжатие. В общем случае они связаны с плотностью материалов.
ПЛОТНОСТЬ, КГ/М3 МАРКА КЛАСС
400 — 500 М 5 В 0,35
450 — 500 М 10 В 0,75
500 М 15 В 1,0
500 — 650 — В 1,5
500 — 700 М 25 В 2,0
600 — 750 М 35 В 2,5
700 — 850 М 50 В 3,5
Как и в случае изделий из тяжелого бетона, марка является средней величиной по результатам испытаний партии образцов. Класс характеризует гарантированную прочность, 95 % образцов должны соответствовать по классности.
Для реальных испытаний с хорошей выборкой зависимость между маркой и классом через переводные коэффициенты не является корректной. В этом случае разрыв между маркой и классом может рассказать о культуре производства на предприятии. Чем меньше разрыв, тем выше организация производства. В отечественной практике изготовления арболитовых блоков это учитывается с помощью коэффициентов вариации. Для изделий 1-ой категории качества допускается значение 18%, для высшей – 15%.
В кирпичной кладке мелкий размер изделий делает понятие классности бессмысленным. При покупке крупных кладочных камней, каковыми и являются арболитовые блоки, стоит отдавать предпочтение изделиям с присвоенным классом.
Для возведения несущих стен одноэтажных зданий высотой до 3 м допускается использовать блоки класса от B 1.0. Для более высоких стен нужны элементы класса от B 1. 5. Для 2-х — 3-х этажных строений используют блоки классов B 2.0 и B 2.5.
Прочность арболита на сжатие типична для ячеистых бетонов. Важным отличием является прочность блоков на изгиб, которая составляет от 0,7 до 1,0 МПа. Модуль упругости элементов может доходить до 2300 МПа. Такие величины делают арболит особенным среди ячеистых бетонов. Если для пенобетона и газобетона велика вероятность трещинообразования, то для арболита такая проблема не стоит.
Теплопроводность арболита.
Теплопроводность для арболита является одним из ключевых параметров.
Она растет с увеличением его плотности в следующей прогрессии:
Теплопроводность арболитовых блоков и ее зависимость от плотности
Рекомендованная ГОСТом толщина ограждающих конструкций из арболита в умеренных широтах составляет 38 см. Но стены такой толщины возводятся редко. На практике для стен жилых домов блоки 500х300х200 мм кладут плашмя в один ряд. Вместе с внутренней и наружной отделкой этого достаточно для поддержания комфортной температуры в помещениях без появления проблем с выпадением конденсата.
Дополнительная теплоизоляция часто выполняется с помощью теплых штукатурных систем толщиной 1,5-2 см с добавкой перлита. Для не отапливаемых или периодически отапливаемых помещений (бани) нередко применяют кладку блоков на ребро.
Сравнение теплопроводности арболита.
Влагопоглощение арболита.
В характеристиках арболита указывают величину водопоглощения до 85% для теплоизоляционных блоков и до 75% для конструкционных. Эти значения требуют осмысления. Структура блока представляет собой склеенные цементным камнем разрозненные зерна щепы. Они ориентированы относительно друг друга случайным образом.
Вода, наливаемая на поверхность блока, свободно протекает сквозь него. Естественно, что при окунании вода способна вытеснить большой объем содержащегося внутри блока воздуха. Если блок вытащить из воды, вода вытекает, а цементный камень быстро высыхает.
Арболитовые блоки находящиеся в естественной среде, например в стене дома, фактически не накапливают в себе влагу из окружающего воздуха. Это происходит благодаря очень низкой сорбционной влажности материала, т. к. минерализованные щепа и цемент являются негигроскопичными и слабо смачивающимися материалами. Именно это стало причиной популярности использования материала для строительства бань.
Если поливать ничем не закрытую стену из арболита с внешней стороны водой, есть вероятность увидеть ее и внутри. Поэтому материал не используют без фасадной отделки. Для арболита рекомендуют отделку штукатурными растворами или устройство навесных фасадных систем.
Морозостойкость.
Постепенное разрушение изделий при замораживании и размораживании происходит в результате расширения замерзающей в пустотах воды. Чем больше воды в них содержится, тем меньше циклов замораживания — размораживания способен выдержать материал без разрушения.
Низкое сорбционное влагопоглощение дает арболиту хорошую стойкость к промерзанию. Минимальное значение составляет F25 и доходит до F50. Защита арболита от прямого воздействия влаги, позволяет повысить реальную морозостойкость материала в конструкции. Кроме этого существуют реальные примеры эксплуатации зданий из арболита на протяжении 7 — 10 лет без повреждений для стен. Причем речь идет о стенах, которые ни чем не защищены от воздействия внешних факторов среды.
Сравнение морозостойкости арболита.
Усадка материала.
Считается, что арболит совершенно не подвержен усадке. Но небольшие усадочные процессы в первые месяцы все же присутствуют. В основном они прекращаются еще на этапе созревания блока на производстве. Некритичное уменьшение размеров блока (на 0,4 — 0,8%) возможно уже после укладки блоков в конструкцию.
Некоторое сокращение высоты блоков может происходить и под весом вышележащих элементов, перекрытий и конструкций кровли. Для предотвращения проблем с отделкой не рекомендуется выполнять штукатурные работы в первые 4 месяца после завершения основного комплекса работ.
Огнестойкость арболитовых блоков.
По огнестойкости арболитовые блоки имеют следующие параметры:
группа горючести — Г1, т. е. это трудногорючий материал;
группа воспламеняемости — В1, трудновоспламеняемый материал;
по дымообразующей способности — Д1, малодымообразующий материал.
————————— Р Е К Л А М А ——————————Предлагаем напрямую с производства строительные материалы по ценам ниже рыночных. Делаем доставку, возможен самовывоз. Снабжаем строительные объекты, строительные рынки. Ищем партнеров для сотрудничества , снабженцев:
——————————————————————————
Блок из арболита
Блоки из арболита имеют перед другими блоками ряд преимуществ. В первую очередь он прочный, не хрупкий. Его не так просто разрушить и, как следствие, трещин в стенах не бывает, если даже фундамент по каким — то причинам просел. Со штукатуркой стен можно не торопиться, он не разрушается от воды и поэтому отделкой можно заняться, когда сочтете нужным, даже через несколько лет
В качестве кладочной смеси хорошо подходит клей для блоков на основе перлита. Они позволят сделать шов наиболее тонким и сам обладает пониженными теплоизоляционными свойствами. Так же можно использовать строительный раствор и любые кладочные смеси.
Пилится арболит цепной электропилой или бензопилой. Цепь при этом, как правило,
используют с победитом.
Армирующую сетку между рядами использовать не нужно. Поверхность блоков шероховатая, а кладочная смесь и раствор схожие по составу с арболитовыми блоками. Эти обстоятельства создают благоприятные условия для склеивания и без использования дополнительных материалов, а так как блок из арболита обладает эластичностью, то трещины в стенах исключены. Сетка при штукатурке по тем же причинам не нужна.
При использовании готовых железобетонных плит в качестве межэтажных перекрытий делается армопояс. Для армопояса используются блоки с выемкой, которые служат несъемной теплой опалубкой. Если плита заливается на месте, то необходимость в армопоясе отпадает. При использовании деревянных перекрытий армопояс можно не делать. Блоки с выемкой так же используются при формировании балок над проемами.
В дополнительном утеплении и шумоизоляции арболит не нуждается. Особое значение необходимо уделить теплоизоляции пола и потолка.
Сложностей при работе с блоками из арболита не возникает, даже если кладка ведется самостоятельно, без привлечения квалифицированных каменщиков.
Блоки из арболита выбирают для строительства дома:
Из чего строить дом? Альтернатива блокам из арболита.
Рассмотрим наиболее популярные материалы.
Дома из бруса или сруба.
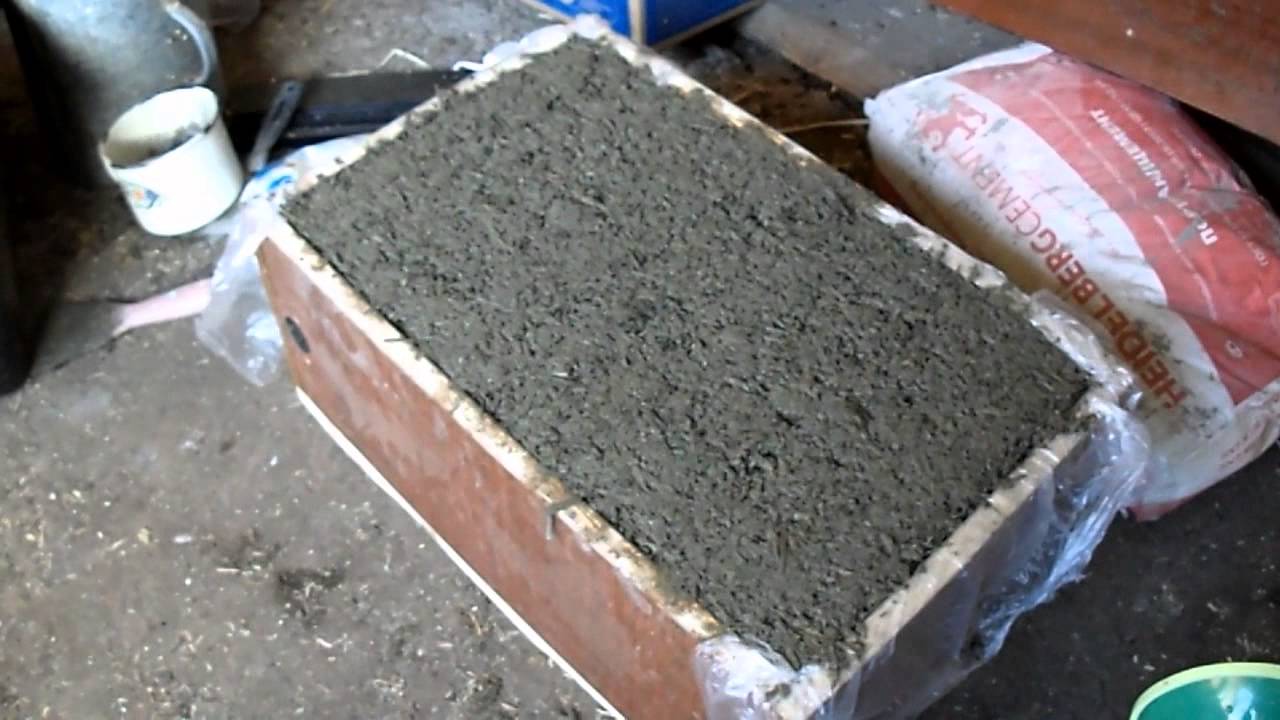
Но брус и сруб менее долговечный материал, горит, потдвержен биоразрушителям, необходимость периодической обработки.
Арболитовые блоки в основной свое массе то же состоят из древесины, цементный камень в готовых изделиях нейтрален.
Щитовые дома
Щитовые дома — горючие, менее долговечные. Если заведутся грызуны, избавиться от них будет очень трудно, для некоторых это стало настоящим бичом и при выборе материала они эту проблему ставят первоочередной.
Кирпич
Кирпичный дом обойдется намного дороже. Стены нужно делать гораздо толще, так как у кирпича более высокая теплопроводность, соответственно более массивный фундамент. Объем стен будет больше в разы, а значит и стоимость кладки будет выше.Кирпич с утеплителем.
Нужно подбирать паропроницаемый утеплитель. Утепленный пенопластом дом будет с эффектом термоса – не экологично. Возможность появления грызунов в утеплителе.Газобетон и газосиликат.
Схожие по характеристикам с арболитом материалы, но очень хрупкие. Повреждения могут получить уже при транспортировки, разгрузки – погрузки. На готовые стены трудно, что либо подвесить. Были контакты с людьми, которые в связи с этим обстоятельством, настолько огорчены, что готовы были продать дом и построить новый.
Не редкость трещины в стенах.
Критичны к прямому попаданию воды.
Можно распилить ручной пилой, это конечно удобно, но… не знаю.
Газобетон и газосиликат имеют замкнутую структуры воздушных пор, что затрудняет вывод влаги из блоков. В некоторых случаях будет значительно увеличиваться теплопроводность.
Логично было бы указать и на недостатки арболита, но что писать? Если Вы знаете – сообщите.
Интерес к арболиту со стороны застройщиков растет из года в год. Когда мы только начинали выпуск арболитовых блоков, приходилось объяснять что это за материал, его преимущества перед другими блоками для несущих стен. Сейчас застройщики по достоинству оценили арболитовые блоки его замечательные свойства.
Кто выбирает арболит для стен своего дома? Некоторая статистика:
Как не странно его экологичность отходит на второй план. В основном покупатели обращают внимания на неприхотливость к погодным условиям – когда дом стоит без отделки. Бывает, что дома без отделки стоят годами. Недавно один из покупателей рассказал, что был на Кольском полуострове на рыбалке и видел там дома без наружной отделки построенных в шестидесятых годах.
Так же от покупателя услышал, что он прежде чем решить из чего строить купил образцы различных блоков. В результате его испытания пережил, только арболит, который пролежал у него в бочке с водой три года.
Еще один рассказ от застройщика на тему, почему арболит: « на работе два гаража оба без отопления. Один из арболита другой из газосиликата. В арболитовом в мороз стоит плюсовая температура в отличие от газосиликатного». Про такое слышал и раньше. При ежедневном пользованием автомобилем, в гараже из арболита тепло без отопления. Видимо хватает до утра тепла мотора, поставленного на ночь автомобиля.. Почему так? Если посмотреть на результаты испытаний арболита на теплопроводность, то можно увидеть, что показатели у арболита выше но все — таки сравнимы с газо и пеноблоками. Но испытания проводятся на образцах без отделки. Пено и газоблоки имеют замкнутые воздушные поры, тогда как у арболита структура с открытыми воздушными порами. При отделки поры закрываются и теплопроводность значительно уменьшается. Тогда как у пено – газоблоков структура и так закрыта и отделка не оказывает существенного влияния.
Трещины в стенах. Еще один фактор побуждающих остановится на арболите. Кто — то из покупателей просто видел дома из пено и газоблоков с трещинами, кто то пережил это на себе. Стена из арболита не дает трещин благодаря определенной степени эластичности. данного материала.
Арболит не поддерживает горения. Это обстоятельство, в купе с другими положительными сторонами, повлияло на выбор в пользу арболита еще одну категорию покупателей. Это люди пережившие пожар.
Практичность – отмечают все из покупателей, с кем удалось побеседовать при оформлении заказа или после ввода в эксплуатацию дома. Действительно дом, по сути, из дерева, с хорошим микроклиматом, в стенах, которого можно легко и надежно закрепить все необходимые элементы интерьера и коммуникации, пожаробезопасный, теплый, долговечный – кому это не понравится.
Сырье для арболита
Внимание!
Принимаем заказы на изготовление блоков на строительный сезон 2021-2022 года.
1) Щепа
Арболит состоит из 90% щепы. Это основной компонент для изготовления арболитовых блоков. Лучше всего подходит щепа из хвойных пород деревьев, так как для обработки хвойной щепы требуется меньше количества сульфата алюминия, чем для лиственных. Сульфат алюминия нейтрализует сахароз в древесине и ускоряет схватывания цемента.
Форма щепы должна быть плоской и игольчатой, такая форма позволяет делать хорошую сцепку друг с другом, армируя блок.
Подробно о том, какие требования предъявляют к щепе для арболита, можно прочесть в нормативных документах:
- ГОСТ 19222-84 «Арболит и изделия из него. Общие технические условия»;
- ГОСТ Р 54854-2011 «Бетоны легкие на органических заполнителях растительного происхождения»;
- СН 549-82 «Инструкция по проектированию, изготовлению и применению конструкций и изделий из арболита».
2) Цемент
Компания АрболитСтройСмоленск использует свежий цемент марки М500Д0.
При реакции цементного раствора с сахарами древесной щепы образуются вещества, для живых существ безвредные, но замедляющие схватывание смеси. Чтобы избежать этого и получить прочный арболит, используется минерализатор – сульфат алюминия (один из видов соли, которым обрабатывают питьевую воду).
!!!!Очень важно знать что при изготовлении арболитового блока ни в коем случаи не добавляется песок. При покупке арболита необходимо это уточнять у производителей, а лучшим способом убедиться в этом самому, достаточно потереть пальцами и на коже должен остаться цемент, а не песок. Цвет блока – иссиня-серый.
3)Минерализатор: сульфат алюминия
Минерализатор – такой же ключевой компонент, как цемент и щепа.
Компания АрболитСтройСмоленск выбирает для минерализации сульфат алюминия, так как он полностью безопасен: его используют для очистки питьевой воды или в качестве пищевой добавки Е-520. Закупаем на прямую с завода в г.Казань
При взаимодействии древесных сахаров с раствором бетона замедляется процесс схватывания. Чтобы нейтрализовать сахара, нужны минерализаторы – соли. Самой эффективной и экономически выгодной считается сульфат алюминия.
В щепе лиственных деревьев сахаров больше, именно поэтому она не так хороша, как щепа сосновых пород. Если все же приходится использовать древесину лиственных – увеличится и количество сульфат алюминия.
Дома из арболита – Удачный Строитель
Арболит – это один из видов легкого бетона, в состав которого входит древесная дробленка (щепа), высокосортный цемент, химические добавки и вода. Необходимость химических добавок в составе арболита связана с тем, что в древесной щепе нужно нейтрализовать остаточный сахар, чтобы повысить сцепление щепы и цемента, а также улучшить такие свойства как пористость, ускорение твердения, бактерицидность и т. д.
Состав арболита
Минеральные вяжущие
В качестве основного компонента, связывающего органический заполнитель, в легком бетоне выступает портландцемент. Согласно требованиям ГОСТ 10178-85 и ГОСТ 31108-2003, марка используемого цемента должна быть не ниже М400. Но наиболее высокопрочный получается блок при использовании портландцемента марки ПЦ 500Д0.
Заполнители
Основным заполнителем для деревобетона является измельченные древесные отходы, полученные при переработке деревьев хвойных и лиственных пород. В качестве наполнителя применяется как один тип органического материала, так и комплексное совмещение разных наименований и фракций растительного сырья. Более качественный бетон получается при использовании деревянной щепы. Древесные заполнители должны соответствовать следующим требованиям: максимальный размер частиц калибруется в пределах 5 мм по толщине, 30 мм по длине и 10 мм по ширине; содержание полисахаридов в сырье не должно превышать 2%; допустимый процент примеси листьев и хвои (в сухой массе) должен находиться в пределах 5% — 10%. Органическое сырье не должно содержать плесени, гниющих частиц и инородных вкраплений (земля, металлические частицы, глина, лед и пр.).
Химические добавки
Поскольку в состав арболита входят органические заполнители, требуется добавление химических компонентов. Химикаты позволяют сохранить целостность биологического сырья и ускоряют адгезию с цементом, сокращая время твердения бетона. Они также регулируют пористость конечного продукта и способствуют предотвращению коррозии взаимодействующих стальных элементов. Для производства органической бетонной смеси требуются следующие вещества: сульфат алюминия; нитрат кальция; хлорид кальция; хлорид аммония; сернокислый глинозем; жидкое стекло. Критерии эффективности химических добавок регламентируются ГОСТ 24211-2008. Добавки смешиваются с водой, затем добавляются к цементно-древесной смеси. Эти добавки совершенно безопасны для здоровья.
Вода
Качество воды, используемой для производства деревобетона, указано в ГОСТ 23732-79. Она должна быть пресной, без содержания жиров и их производных, а также красящих примесей. Требуемое содержание ПАВ, фенолов и полисахаридов – не более 10 мг/л, ионов хлора – не более 300 мг/л. Вода и раствор химикатов проходят лабораторный контроль.
Основные технические характеристики
- Плотность (кг/м3). Для теплоизоляционного материала установлены марки D300-D500. Марки конструкционного арболита – от D500 до D900.
- Прочность на сжатие. Бетон соответствует разным классам прочности (В0,35, 0,75 – для одноэтажных зданий и В1,5, 2,5, 3,5 – для двухэтажных). Арболит имеет марки М2,5, М3,5, М5, М10. В зависимости от этого показателя определяется вид и функциональное назначение материала.
- Теплопроводность. Этот показатель позволяет определить необходимую толщину стен. Поскольку арболитовый материал имеет низкий коэффициент теплопроводности, это позволяет использовать его при строительстве в зонах с холодным климатом. В ГОСТ Р 54854-2011 установлены коэффициенты теплопроводности (Вт/(м·К)), в зависимости от марки бетона (D300 – 0,07, D500 – 0,95, D800 – 0,17).
- Влагопоглощение и паропроницаемость. Эти показатели регламентируются нормами ГОСТ 4.212-80. Коэффициент водопоглощения для арболита составляет 75 – 85%, паропроницаемость – до 35%.
- Морозостойкость. Этот коэффициент показывает устойчивость материала к воздействию переменных циклов заморозки и оттаивания. Для конструкционно-теплоизоляционного древобетона установлены марки по морозостойкости F15, F25, F35, F50.
- Усадка. Испытания показывают, что легкий органический бетон подвержен минимальной усадке, которая находится в пределах 0,8%.
- Огнестойкость. К этому показателю предъявляют несколько требований пожарной безопасности. Марки от D400 должны соответствовать группе горючести Г1, токсичности продуктов горения Т1, воспламеняемости В1 (ГОСТ 30244, 12.1.044, 30402). В соответствии с этими показателями, арболит является трудногорючим материалом, с малым количеством выделяемого дыма.
- Звукоизоляция. Теплоизоляционные арболитовые материалы имеют высокие звукоизоляционные свойства, с коэффициентом шумопоглощения до 0,6 ДБ. Свойства разных видов древобетона зависят от используемой марки цемента, химических добавок, технологии производства и материала, защищающего наружные части арболитовых блоков.
- Экологичность. Это безопасный для здоровья человека строительный материал. Состав и производство его также абсолютно безопасны, в том числе и для окружающей среды. Применяемые химические добавки давно используются во благо человечества и в пищевой промышленности. Например, такая добавка, как сернокислый алюминий, используется для эффективной очистки воды на водоочистительных станциях.
Достоинства арболита
- Повышенная тепло- и звукоизоляция, которые достигаются благодаря пористости материала, что позволяет отказаться от дополнительного утепления.
- Абсолютная огнестойкость – за счет того, что древесная щепа окружена толстым слоем бетона.
- Прочность. Технология производства дает арболиту высокие коэффициенты прочности на изгиб. Т. е. там, где другой материал треснет, арболит останется невредимым. Только при больших нагрузках этот материал может деформироваться, но также достаточно медленно, так как древесная щепа обладает связывающими функциями. Пластичность достигается опять же благодаря древесному наполнителю, поэтому арболиту не страшны повреждения при транспортировке, монтаже, а также воздействия природных факторов (колебания грунта, температурные скачки и т.д.)
- Легкость по сравнению с обычными материалами (кирпич, бетон), что облегчает работы по укладке блоков.
- Долговечность. Арболит не гниет, слабо поражается грибком, плесенью и химическими веществами. Легко изменять форму блока с помощью пилы, топора, а вбивание гвоздей, вкручивание саморезов даже без дюбелей не составит никаких трудностей.
Недостатки арболита
Специалисты выделяют недостаток данного материала, связанный с высоким водопоглощением, поэтому использование его в помещениях с высокой влажностью или в районах, где преобладают осадки, не рекомендуется. Это ни в коем случае не говорит о том, что строение разрушится после дождя, как карточный домик, но срок службы здания сократится в разы. Чтобы избежать этого, нужно предпринять некоторые меры по гидроизоляции строения еще на этапе возведения. Штукатурка или другая отделка защитят наружные блоки от воздействия дождя и снега.
Итак, из арболита можно построить дом, гараж, пристрой. При этом материал будет сохранять тепло и выводить лишнюю влагу из постройки, возможна любая внешняя отделка — облицовочный кирпич, декоративная штукатурка, сайдинг, дерево, камень и пр. Цена арболита и арболитовых блоков вполне доступная. Себестоимость дома будет снижена в 2 раза по сравнению с домом из кирпича. Единственным ограничением по использованию будет являться длительный контакт с влагой. В этом случае блоки нужно будет дополнительно защищать, о чем описано выше. Аналогов арболиту среди других строительных материалов по сочетанию свойств и технических характеристик нет!
Заказать арболитовый блок
Основные размеры блока:
200х300х500мм
200х400х500мм
U-блок для армопояса — 200х300х500мм
U-блок для армопояса — 200х400х500мм
Цену уточняйте по телефону — 8 904 8344250.
Скидки от объема.
Видео по теме:
Проекты домов из арболита
Вопросы и ответы — статьи на тему Блоки строительные
Насколько прочный арболитовый блок?
Наш завод производит арболитовый блоки с марочной прочностью М15(В1) и М25(В2).Данных показателей вполне достаточно для постройки жилого здания до трёх этажей. Другими словами конструктивный блок 500х300х200мм. способен выдержать нагрузку от 31500 до 40500 кг.
Нужно ли утеплять дом, построенный из арболитовых блоков?
Дом, построенный из арболитовых блоков, не нужно утеплять, так как он очень хорошо сохраняет тепло зимой и прохладу летом.
Арболит экологически чистый материал?
Арболитовые блоки изготовлены из древесной щепы игольчатой формы, цемента М500,воды и хлористого кальция. И не содержат пены, полистирола и прочих вредных веществ.
Арболит – это то же что и опилкобетон?
Нет. При изготовлении опилкобетона используется опилки и песок, в связи, с чем он тяжелее и менее прочнее арболита, хотя, к сожалению его, очень часто путают с опилкобетоном и саманом.
В арболитовых блоках заводятся насекомые или грызуны?
Нет. Так как при изготовлении арболитовых блоков, щепа пропитывается хлористым кальцием или сульфатом алюминия, и то и другое совершенно безвредно для человека. Но губительно для сахаров находящихся в древесине. Вследствие чего древесина обеззараживается и становится устойчива к насекомым, грибкам и бактериям. Не говоря уже о том, что щепа длительное время перемешивается с цементом М500, насекомое или грызун попросту не сможет прогрызть блок.
Какой фундамент нужен для дома, построенного из арболитовых блоков?
Это сугубо индивидуальный расчёт, который лучше доверить специалисту. Как правило, достаточно обычного – ленточного, так как арболитовые блоки относятся к лёгким ячеистым бетонам.
Какая гарантия, что дом, построенный из арболитовых блоков, простоит не одно десятилетие?
Дом, построенный из арболитовых блоков, будет радовать Ваших правнуков! Арболит – это не ноу-хау, а отечественная разработка 1960-х. годов. Доказательством его долговечности является станция «Молодёжная», построенная в Антарктиде в 1962 году, которая функционирует и по сегодняшний день. В Голландии и сейчас многие отдают предпочтение арболитовым блокам, только у них он называетсяDURISOL.
Арболит это горючий материал?
Нет. Арболит относится к группе Г1 слабо горючие, В1 трудновоспламеняемые, РП1 не распространяющие пламя.
Почему арболитовые блоки дороже других ячеистых блоков?
Всё очень просто:
В отличие от аналогичных ячеистых и пористых блоков, мы используем качественное, экологически чистое сырьё.
Изготовление арболитовых блоков – это очень трудоёмкий и долгий процесс.
На самом деле строя дом из арболитовых блоков Вы экономите, так как, нет необходимости утеплять стены, а это довольно затратное мероприятие, даже если это делать без найма рабочей силы. Как следствие на стенах не будет, появляется точка россы и стены не заплесневеют. Дом, построенный из арболита, очень хорошо сохраняет тепло зимой и прохладу летом, вследствие чего коммунальные платежи будут меньше, а если учесть, что они растут в геометрической прогрессией – это не маловажный фактор в пользу арболитового блока.
У вас есть сертификат качества на арболитовые блоки?
Да есть. Сертификат соответствует требованиям нормативных документов ГОСТ Р 54854-2011
Чем облицовывают дома из арболита?
Вариантов облицевать стены, построенные из арболитового блока бескрайнее множество, которое ограничивается только Вашей фантазией.
Например:
Внешняя отделка дома из арболитовых блоков:
Цементная штукатурка, Блок-хаус, все виды сайдинга, вагонка, кирпич.
Внутренняя отделка:
Цементная или гипсовая штукатурка, ламинированный ДСП, шпонированный МДФ, все виды обоев, гипсокартон.
Вы изготавливаете щепу из старых и отработанных поддонов и т.п. отходов?
Нет. Наш завод изготавливает арболитовые блоки из делового отхода берёзы.
Сколько весит один блок арболита?
Вес конструкционного блока не превышает 19кг., перегородочного около 10 кг., а U- образного армоблока 15кг.
Сколько блоков в поддоне, в одном кубическом и квадратном метре?
В одном поддоне:
Конструктивного блока (500х300х200мм.) – 53шт.
Перегородочного (500х150х200мм.) – 45шт.
U-образного блока (500х150х200мм.) – 53 шт.
В одном кубическом метре:
Конструктивного блока (500х300х200мм.) – 33,3м³
Перегородочного (500х150х200мм.) – 66,6м³
U-образного блока (500х300х200мм.) – 33,3м³
В одном квадратном метре:
Конструктивного блока (500х300х200мм.) –10 шт. (В пол блока 6,5шт.)
Перегородочного (500х150х200мм.) – 13,4шт.
U-образного блока (500х150х200мм.) – 10 шт.
Возможно, изготовить арболитовые блоки в домашних условиях?
Да возможно, но ввиду того что далеко не у каждого в гараже стоит щепорез который измельчит древесину до необходимой формы и размера и есть пресс с усилием 22 МПа. Не говоря уже о пропорциях и формах, в которых блок выдерживается 24 часа. Как следствие, качество готового арболитового блока будет не самым лучшим.
Какими метизами нужно крепить навесную мебель?
Любыми. В арболитовые блок можно вкрутить как обычный саморез по дереву, так и вбить обычный гвоздь. Как в первом, так и во втором случае этого будет достаточно чтобы не переживать за навесную мебель или телевизор.
Если Вы сомневаетесь в качестве арболитовых блоков…
Если у Вас остались сомнения посмотрите видео, где сотрудник нашего завода проводит разнообразные эксперименты над арболитовым блоком. Если и этого не достаточно приезжайте к нам на производство и убедитесь в качестве наших блоков сами!
Блоки цветут из древесных отходов
БОСТОН
КОГДА Джеймс Бэнкрофт показывает посетителям привлекательный новый амбар-студию, который он построил за своим домом в сельском округе Камберленд, штат Нью-Джерси, он любит говорить им, что это «самая красивая куча древесной щепы, которую вы когда-либо видели». Он также надеется, что это предшественник большого количества высококачественного и недорогого жилья по всей стране.
Это потому, что студия была построена из древесно-волокнистых бетонных блоков, настолько простых в использовании, что люди без строительных навыков могут легко возвести основную конструкцию.Фактически, цель Community Innovations, некоммерческой организации, которую он основал, состоит в том, чтобы привлечь неквалифицированную молодежь из городских районов к строительству недорогого жилья именно там, где это больше всего необходимо. Поскольку древесные отходы легко могут стать основным ингредиентом блоков, система может одновременно решить проблему утилизации твердых отходов.
Традиционно считается, что древесные волокна и бетон плохо смешиваются, потому что сахара, дубильные вещества и масла в древесине препятствуют ее правильному сцеплению с бетоном.Кроме того, древесные частицы разлагаются при длительном воздействии влаги.
Но несколько десятилетий назад швейцарские и австрийские ученые разработали процесс покрытия древесных частиц минерализующим слоем, благодаря чему они легко связываются с цементом, песком и камнем. Древесина в Европе дороже, чем в Северной Америке, и это послужило толчком к развитию. «Это было слишком дорого, чтобы просто выбросить или сжечь», — объясняет Хансруди Вальтер из Faswall Concrete Systems в Огасте, штат Джорджия, которая привезла систему в Соединенные Штаты.
Система, слегка адаптированная для учета повышенного содержания сахара в некоторых американских деревьях, для обработки древесины использует природные минералы, добытые в США. «Здесь нет агрессивных химикатов», — настаивает г-н Уолтер, утверждая, что «процесс действительно очень прост, если вы знаете, как это сделать».
«Экологически приемлемые» и продукт, и процесс, радует г-на Бэнкрофта, который возглавляет Community Innovations в Бриджитоне, штат Нью-Джерси. Но его в первую очередь привлекает древесно-волокнистый бетон, потому что он «настолько прост в использовании».«Помимо легкого веса (меньше половины веса обычного бетона), его можно« пилить, прибивать гвоздями или привинчивать, как любой кусок дерева », — говорит он. люди, не имеющие опыта кладки, «возводят четырехфутовую фундаментную стену по периметру всего за два часа».
В то время как на заводе Faswall Concrete Systems в Виндзоре, Южная Каролина, производятся различные строительные изделия из древесно-волокнистого бетона. Бэнкрофт использовал базовые блоки длиной 36 дюймов, высотой 12 дюймов и глубиной 9 дюймов.
При весе всего 39 фунтов, блокирующие блоки были сложены в сухом виде на высоту четырех футов, а затем жидкий бетон был залит в полые центры, чтобы связать конструкцию с твердой стеной. Другой вариант — нанести тонкий слой поверхностного склеивания на каждую сторону стены, что одновременно защитит стену от атмосферных воздействий.
Бэнкрофт отделал стены своей студии виниловым сайдингом, но «самый дешевый способ придать законченный вид — это нанести штукатурку», — говорит он.
Поскольку блоки состоят в основном из древесного волокна с небольшим количеством мелкого песка и цемента для обеспечения сцепления, блоки очень пористые.Фактически блоки примерно на 40 процентов состоят из воздуха, что дает им изоляционный показатель R11. Другими словами, они очень медленно выводят тепло из дома (или в него в жаркие летние дни). Это улучшается до R19, когда полые центры заполнены заливным бетоном с его высокой теплоемкостью.
Итак, «эти дома дешево отапливать и охлаждать», — говорит Бэнкрофт, и расходы на страхование будут относительно низкими, потому что «стены, построенные из этих блоков, имеют четырехчасовую огнестойкость». Другими словами, постоянно горящему огню потребуется четыре часа, прежде чем он сможет прожечь стену.Бетонные блоки сами по себе не поддерживают горение. Еще один плюс, стены делают здания «удивительно тихими и спокойными», — говорит Бэнкрофт. Фактически, одним из первых способов использования этой технологии в Соединенных Штатах было строительство шоссе и заграждений.
Испытания в нескольких тропических странах, включая Шри-Ланку, Конго и Марокко, показывают, что блоки не подвержены воздействию термитов и обладают высокой устойчивостью к гниению.
В настоящее время древесно-волокнистые блоки производятся только в одном месте. Но идея состоит в том, чтобы лицензировать эту технологию всем заинтересованным сторонам, хотя предприятия, уже работающие в отрасли сборного железобетона, будут в лучшем положении, чтобы воспользоваться этой технологией.
Хотя блоки, панели и другие формы могут быть изготовлены из первичной древесины и при этом оставаться конкурентоспособными, Уолтер надеется, что древесные отходы будут основным источником сырья, как и в Европе. По его словам, деревянные поддоны, часто сделанные из дуба, будут особенно хорошим источником волокна для промышленности. Он также отмечает, что «побочные продукты бумажной промышленности могут поставлять все необходимое нам древесное волокно».
Бэнкрофт узнал о строительных блоках из древесного волокна, когда посетил высотный проект в Канаде, построенный коммерческим подрядчиком.Очарованный возможностями, Бэнкрофт построил амбар-студию у себя на заднем дворе, чтобы испытать систему на себе и, в частности, посмотреть, можно ли ее построить с необученным трудом.
Проект подтвердил, что эту строительную систему можно легко использовать для создания прочного прочного жилья в районах с низким доходом. Теперь он надеется, что корпорации или фонды поддержат демонстрационные проекты в различных частях страны.
Для получения дополнительной информации пишите:
Faswal, Box 189,
Windsor, SC 29856
Телефон: (803) 642-9346
Бетонные блоки для оседания — блоки и кирпичи RCP
Бетонные блоки для осадки
Slump Block — это бетонный блок, который извлекается из формы до того, как он успеет полностью застыть.Это приводит к тому, что бетонный блок сохраняет обвисший вид, как сырцовый кирпич. Доступны как структурные, так и неструктурные бетонные блоки с противоскользящим покрытием. Бетонные блоки с противоскользящим блоком доступны как обычных, так и специальных размеров.
- Конструкционные элементы соответствуют ASTM C90, ACI 530, Калифорнийскому строительному кодексу (CBC), глава 21, и Международному строительному кодексу (CBC)
- Неконструкционные элементы соответствуют ASTM C129
- Доступны индивидуальные цвета, вес и особенности дизайна
- По вопросам, связанным с конкретным проектом, обращайтесь в RCP Block & Brick
Цвета опорных блоков
ПРИМЕЧАНИЕ. Цвета могут отличаться от отображаемых в Интернете.Чтобы убедиться в этом, запросите образцы цветных чипов, обратившись в RCP Block & Brick Architectural Support .
Цвета на складе:
Пользовательские цвета:
Размеры и формы опорных блоков
ПРИМЕЧАНИЕ: Все размеры являются номинальными
Характеристики продукции
- Конструкционные элементы: Соответствуют ASTM C90, Спецификации для несущих кирпичей, средний вес.Также соблюдайте последние редакции ACI 530 и главу 21 Строительного кодекса Калифорнии (CBC) и Международного строительного кодекса (IBC).
- Неструктурные блоки: Соответствуют ASTM C129, Спецификации для ненесущих бетонных блоков.
- Для достижения среднего веса промышленного стандарта, RCP Block производит из черного вулканического пепла, который соответствует ASTM C331, Спецификации для легких заполнителей для бетонных блоков.
- По специальному заказу доступны изделия разного веса и конструктивного исполнения.
- Стандартные блоки выполняются для каждого задания и доступны со сроком выполнения от четырех до шести недель.
- Пользовательские цвета и формы могут зависеть от: минимального количества заказа, увеличенного времени ожидания, платы за пресс-форму и соглашения о закупке всех единиц из производственного цикла.
Ресурсы для продукта
(PDF) ПРИГОДНОСТЬ БЕТОННЫХ БЛОКОВ РУЧНОЙ ФОРМОВКИ ДЛЯ ОДНОЭТАЖНЫХ ДОМОВ на
Исходя из значений, приведенных в Таблице 4, можно
предложить прочность блочной кладки равной 0.9 Нзмм? для стен
из блоков HMCC. В одноэтажных домах
расчетное напряжение стены будет в первую очередь состоять из вклада
из-за собственного веса, а оставшаяся часть
будет зависеть от веса крыши и потолка
(максимальное расчетное значение около l 0,0 кН / м
2
с
как статической, так и приложенной нагрузкой). Если стена поддерживает пролет крыши 4,0 м
, результирующее напряжение будет только 0.04 Н / мм «.
Как правило, высота стены в одиночном
-этажном доме среднего размера будет иметь максимальную высоту около 4,0 м.
Это даст напряжение около 0,092 Нз’мм + с плотностью
из 23 кН / м
3.
Когда введены частичные коэффициенты безопасности
, он составит около 0,49 Н / мм2 (0,092 x 1,4
x 3,5 +0,04). достаточный запас
при характеристической прочности 0,9 Н · мм », чтобы учесть
любых эффектов гибкости и эффектов отверстий.
Это может быть дополнительно поддержано за счет использования характеристической прочности
, необходимой для двухэтажных домов с несущими стенами
.
I
т было показано в подробном исследовании
, что прочность стены 1,5 Н / мм2 была достаточной
для двухэтажной несущей кирпичной стены с
монолитными железобетонными плитами (Jayasinghe, 1998).
Таким образом, можно предположить, что стены
, построенные из блоков HMCC (смесь 1: 8: 14) и цементно-песчаного раствора 1: 5
, будут иметь достаточную прочность для
одноэтажных конструкций.
7.0 Аспекты стоимости
Возможность производить вручную лепные бетонные блоки
имеет особое преимущество для определенного сектора
населения. Это группы с низким доходом на
, которым небольшие ссуды на сумму около рупий. 25,000 / = до 50,000 / =
предоставлены различными правительственными и не
правительственными организациями. Некоторые из этих кредитов
выдаются с небольшими взносами, что делает невыгодным
для получателей покупать блоки напрямую на рынке
.В таких случаях блоки HMCC предоставляют хорошую возможность
, поскольку для этого нужна только пресс-форма для изготовления блоков
, но не машина для изготовления блоков. Время, затрачиваемое на изготовление около 30 блоков
, составляет два часа, когда задействовано два человека
; один для производства щебеночной бетонной смеси
и другой для изготовления блоков. При такой скорости
потребуется менее двух месяцев, чтобы построить все блоки (около
1500-2000), необходимые для дома площадью около 50 м
2
,
, работая только 2 часа в день. на неполной ставке.
Таким образом, затраты рассчитываются на основе
неоплачиваемого труда и оплачиваемого труда.
Это
было установлено при реальных измерениях, что из мешка
цемента, можно сделать 67 штук блоков толщиной 125 мм
. Общая стоимость для этих 67 блоков была рассчитана
рупий. 812 / = с ценами на мешок цемента, 1 м «
песка или карьерной пыли и 1 рубль 6-8 мм стружки как
350 / =, 500 рупий / = и рупий.600 / = соответственно. Следовательно,
стоимость блока толщиной 125 мм составляет около рупий. 12 / = и рупий.
9,50 / = для блоков толщиной 100 мм.
Поскольку два неквалифицированных рабочих могут производить около
15 блоков в час, стоимость рабочей силы на блок рассчитывается на основе
рупий. 250 / = в день на одного работника. При восьми
часов рабочего времени в день стоимость рабочей силы может составить
рупий. 4,00 за блок. Следовательно, стоимость блока
с наемным трудом будет рупий.13,50 и рупий. 16.00 для 100
блоков толщиноймм и 125 мм соответственно. Это можно рассматривать как
как цену, сопоставимую с ценой на блоки из цементного песка
, доступные на рынке.
8.0 Выводы
В подробной программе испытаний показано, что
бетонных блоков из формованной стружкишириной 125 мм и 100
мм можно использовать для внешних и внутренних стен одноэтажных домов
, соответственно. Для любой конструкции конструкции
можно с уверенностью принять характеристическую прочность
0.9 Н / м »для стен из щебеночных блоков толщиной
100 или 125 мм. Рекомендуемая смесь:
1: 8: 14 цемент, мелкий заполнитель и щепа для блочной кладки
. Одно из основных преимуществ блоков из щебеночного бетона
состоит в том, что он может быть изготовлен на месте до требуемой толщины
. Это можно использовать, чтобы избежать штукатурки
, используя блоки толщиной 125 мм для внешних стен
. Для внутренних стен 100 Можно использовать блоки толщиной
мм.Исследование стоимости показало, что стоимость блоков HMCC
может быть сопоставима с теми, которые доступны на рынке
.
Благодарность
Автор хотел бы поблагодарить Сенатский исследовательский комитет
Университета Моратува за финансирование
этого исследования. Технический директор, г-н С.Л. Капуруге
успешно координировал исследовательскую работу с большой самоотдачей
. Особая благодарность за Research
Assistant Mr.У. К. Виданагамараччи и технический персонал
Помощник г-на У. С.
П.
Кумара.
Ссылки
BS 5628: Часть 1: 1992, Использование кирпичной кладки — Конструктивное использование неармированной кирпичной кладки
, 56 стр.
Строительные нормы (1985), «План развития города Коломбо
«, том
II,
Муниципальный совет Коломбо,
74p.
Chandrakeerthy, S.RDeS., Fonseka, M.C.M., Kodikara,
c.w.,
Jayawardane, S.JKLL, (1985), «Производство
блоков для многоэтажных несущих каменных конструкций»,
Труды Института инженеров, 1985.
29
Обломок старого блока: восстановление бетонных блоков
Криста Дж. Гаффиган, AIA, LEED-AP BD + C и Энн Э. Вебер, FAIA, FAPT
Бетонный блок, разработанный в начале 20 века как недорогой, но прочный материал для народного строительства. Он широко использовался в промышленном и коммерческом строительстве, а также широко продавался для сельскохозяйственного и жилищного строительства.К 1950-м годам блоки широко использовались в школах и подобных сооружениях и были доступны во многих размерах, отделках и формах.
Баня после ремонта. Предоставлено: Брайан Роуз
В 1920-е годы бетонные блоки были широко представлены на рынке товаров для самостоятельного изготовления, и многие публикации предлагали фермерам и домовладельцам инструкции по строительству сельскохозяйственных построек, гаражей и даже домов. Несколько компаний, включая Sears Roebuck , продавали миксеры и машины, которые позволяли людям изготавливать свои собственные блоки для небольших проектов, таких как гаражи или садовые стены.Многие из этих машин производили блоки с декоративными гранями. Известный бетонный дом № «Популярная механика» № 1949 года включал раздел о создании собственного блока. 1 Легкий блок был коммерчески разработан в 1930-х годах, двумя известными брендами были Haydite и Waylite . Производство блоков резко возросло во время и после Второй мировой войны: в США в 1951 году было произведено 1,6 миллиарда бетонных блоков (CMU), как их называют технически. 2 По мере роста производства стандарты ASTM C129-14a и C90-15 были разработан для покрытия ненесущих и несущих бетонных блоков.
Хотя консервация и реставрация этого материала осуществляется в соответствии с теми же процедурами, что и камень или другие каменные материалы, есть некоторые особенности, связанные с бетонным блоком, о которых следует знать. Реставрация двух современных сооружений, построенных из бетонных блоков — Trenton Bath House в Юинге, штат Нью-Джерси и Paepcke Memorial Building в Aspen Institute — иллюстрирует некоторые из этих проблем.
В 1955 году Еврейский общинный центр Трентона заказал Людовика I.Kahn спроектирует свой новый пригородный объект в Юинге, штат Нью-Джерси. Генеральный план включал бассейновый комплекс с двумя бассейнами и раздевалками; объект дневного лагеря; общественный центр; и игровые поля. Комплекс бассейнов, ныне известный как баня Трентон, был первым сооружением, которое было построено летом 1955 года. Кан выбрал экономичные материалы, включая CMU, деревянную конструкцию крыши и кровлю из асфальтовой черепицы для четырех конструкций в девятиквадратная сетка плана.
После 50 лет воздействия погодных условий в центре Нью-Джерси, CMU серьезно пострадал в нескольких местах.Монументальные пирамидальные крыши павильонов не имели желобов, а дождевая вода во многих местах стекала прямо по поверхности стен, вызывая эрозию поверхности блоков. Эта эрозия создала очень благоприятную поверхность для органического роста и накопления грязи. В двух местах карниз крыши находится прямо над единственной стеной CMU. Насыщение этой стенки вызвало растрескивание, смещение и сильную эрозию блока, а также чрезмерный органический рост. Во многих местах сквозь блочную конструкцию можно было видеть свет, а стены были сочтены командой дизайнеров несостоятельными.
Баня перед панно с обшивкой. Предоставлено: Брайан Роуз
Проблемы, с которыми пришлось столкнуться при реставрации, заключались в очистке и удалении краски, мастики и органических наростов на существующем CMU; и поиск блока замены. Заменяющий блок потребуется для восстановления двух структурно нарушенных стен, для строительства новых перегородок в раздевалках и для точечной замены поврежденных блоков.
Большинство загрязнений и органических наростов на CMU можно удалить с помощью биоцида и промывки под низким давлением.Было использовано низкое давление, потому что в некоторых местах блок стал довольно хрупким из-за эрозии поверхности. В других местах можно использовать более высокое давление для более стойкого окрашивания.
Краска и мастика были обнаружены на блоке после сноса закусочной, построенной в конце 1950-х годов. Испытания химических очистителей и растворителей дали неоднозначные результаты, поэтому были рассмотрены механические методы. На дробеструйной машине Torbo были испытаны различные взрывные среды, и скорлупа грецкого ореха была выбрана как эффективная, но минимально повреждающая блок.Различные другие средства массовой информации были более эффективными, особенно на мастике, но нанесли неприемлемый ущерб CMU. От мастики остались ореолы из-за проникновения черного материала в блок, и там, где это было особенно нежелательно, некоторые блоки были заменены.
Первый раунд образцов блока замены не дал хорошего совпадения. Новый блок имел гораздо более плотную и гладкую текстуру, чем практически не выветрившийся блок у стен, защищенных большими конструкциями крыши.Во время этого процесса Владелец обнаружил спецификации Кана в файлах Еврейского общинного центра, и блок был идентифицирован как Waylite, одна из наиболее широко используемых облегченных формул блока. Компания Trenton Block все еще производила Waylite в Трентоне, и их вторая серия образцов была гораздо более успешной. В третьем раунде был использован локальный агрегат, что привело к хорошему совпадению для необработанного блока. Новый блок был использован для восстановления двух стен внутреннего двора и для ремонта больших площадей.Неответренный оригинальный блок, добытый из водопроводных канавок, использовался для небольших участков засыпки.
Первоначальная высокопористая поверхность блока Waylite способствовала ухудшению состояния бани по прошествии 55 лет; материал был достаточно впитывающим, а на открытой поверхности было множество укромных уголков и трещин для загрязнения и органического роста, особенно когда блок был влажным. Каталог 1939 года для Waylite SuperPoke рекомендует гидроизолировать внешнюю поверхность несколькими слоями цементной краски, что, вероятно, улучшило бы долговечность поверхности, но не соответствовало бы философии Кана естественного выражения материалов. 3
Замена и восстановление CMU в бане прошли успешно, но для сохранения их внешнего вида потребуется постоянное обслуживание.
Баня после реставрации. Предоставлено: M + Sa Staff
Мемориальное здание Паепке , спроектированное Гербертом Байером , расположено на территории кампуса Института Аспена в Аспене, штат Колорадо. Здание оставалось практически неизменным спустя 40 с лишним лет после его завершения в 1962 году.Байер задумал здание простой формы с использованием несущих стен из бетонных блоков и крыш с деревянным каркасом. В здании расположены административные помещения и аудитория Института, в которой проводится ряд программ, включая научные лекции, фильмы, сольные концерты и детский театр.
На этапе проектирования проекта реставрации было определено, что бетонный блок наиболее пострадал от проникновения воды в зрительную часть здания. Вода из льда, снега и дождевальной системы весной и летом пропитывала стену.За краской скопилась влага, повредившая покрытие.
Команда дизайнеров, в которую входили консерваторы из The Collaborative Inc. (галочка) и Conservation Solutions Inc. (CSi), провела исследование консервации материалов, чтобы определить лучший метод удаления существующей краски как с внутренней стороны, так и с ее поверхности. наружные стены аудитории из бетонного блока. Микроабразивная очистка была протестирована вместе с тремя химическими средствами для удаления краски.
Тестирование показало, что микроабразивная техника с использованием стеклянной крошки является наиболее эффективным и комплексным методом удаления краски, и в результате существующий блок приобрел почти новый вид.Для химических очистителей Zip Strip обеспечила наилучшие результаты среди очистителей, удалив большую часть краски, не забивая поры бетонного блока.
Минеральная краска (Silin AZ) была затем нанесена на три области, чтобы оценить, насколько эффективно новая краска будет покрывать оставшуюся краску, сохраняя при этом открытые поры бетонного блока для акустических и паропроницаемых свойств. Затем эти области были протестированы с помощью трубок Rilem, чтобы определить влияние новой наложенной краски на коэффициент паропроницаемости как существующих окрашенных участков, так и необработанного бетонного блока.
Было установлено, что влага не могла проходить через только что покрытый внешний бетонный блок при нормальных погодных условиях, а внутренняя поверхность бетонного блока с новым покрытием не препятствовала прохождению влаги, что было желаемым результатом. Кроме того, минеральная краска на внешней стороне позволяет водяному пару выходить наружу, препятствуя проникновению влаги. Таким образом, цель предотвращения накопления влаги внутри бетонного блока может быть достигнута.
Изображение слева: Интерьер мемориального здания Пепке демонстрирует ухудшение состояния КМУ. Предоставлено: M + Sa Staff. Изображение справа: Интерьер мемориального здания Пепке с изображением КМУ после реставрации. Предоставлено: Майкл Брэндс
Во время строительства применяемые методы незначительно отличались от тех, которые были определены как наиболее эффективные при проектировании. Это было связано как со стоимостью, так и с удаленностью Аспена, что затрудняло поиск квалифицированных специалистов. Подрядчик использовал химический очиститель только для удаления большей части существующей наружной краски и не использовал микроабразивный метод.Внутри существующий одинарный слой краски был покрыт слегка нанесенным аэрозольным покрытием минеральной краски, что позволило обновить цвет без отрицательного воздействия ни на акустические свойства, ни на паропроницаемость стены. Подрядчик работал над тем, чтобы минеральная краска соответствовала цвету и блеску обычной латексной краски, нанесенной за пределами аудитории, как на наружных бетонных блоках, так и на внутренних стенах из гипсокартона.
Проект Мемориального здания Паепке привел к успешной реставрации оригинальных бетонных стен 1960-х годов этого культового здания с сохранением необходимых физических свойств стеновой конструкции.
Установленные принципы восстановления кладки, разработанные в основном для камня и кирпича, в настоящее время применяются к бетонным блокам, при этом в специальной литературе имеется мало специальной информации. Эти методы были успешно применены в Мемориальном здании Пепке и в банях Трентона. По мере того как наиболее значимые здания CMU второй половины двадцатого века реставрируются и документируются, литература и современное состояние искусства будут продолжать улучшаться.
Мемориальный комплекс Паепке после реставрации.Предоставлено: Майкл Брэндс
Около
Криста Дж. Гаффиган, AIA, LEED-AP BD + C, старший научный сотрудник Mills + Schnoering Architects, является архитектором по сохранению с опытом в различных институциональных, образовательных, и культурные проекты. Она была архитектором проекта реконструкции Мемориального здания Паепке и плана сохранения Трентонской бани и дневного лагеря.
Энн Е. Вебер, FAIA, FAPT, является партнером Mills + Schnoering Architects, где она специализируется на управлении крупномасштабными проектами по сохранению.В дополнение к реставрации Трентонских бань, она выполнила работы над Статуей Свободы, зданием суда округа Эссекс (Нью-Джерси) и аркой ворот.
Примечания
1. Уорд, Джеймс Р. Популярная механика Известный бетонный дом . Popular Mechanics Press, 1949.
2. Симпсон, Памела Х .; Хандерман, Гарри Дж .; и Слэйтон, Дебора, «Бетонный блок» в Строительные материалы двадцатого века: история и сохранение , Томас К.Шут, редактор. 2-е издание, Getty Conservation Institute, 2014.
3. Компания Waylite, Waylite-Superock: современный строительный материал: книга планов, 1939. стр. 5.
Как каратэ ломает бетонные блоки
Как может рыхлая рука смертного, уязвимая для заусениц, перегретых пакетов с попкорном и острых как бритва кусочков картофельных чипсов, зажатых между клавишами обычной компьютерной клавиатуры, идти? через бетонные блоки и деревянные доски?
Беглый просмотр интернета или музыкального тренинга из фильма о боевых искусствах восьмидесятых делает очевидным, что разбить бетон или дерево голыми руками возможно.На самом деле у некоторых читателей есть знакомые, которые из-за обширной подготовки или большого количества алкогольного опьянения попробовали это сами и добились успеха. Конечно, у этих читателей есть друзья, которые из-за сильного опьянения упали и сильно поранились о дерево или бетон. Главный вопрос: в чем разница между успехом и травмой? Какие факторы влияют на то, чтобы ударить по куску бетона и расколоть его надвое, вместо того, чтобы ударившая по нему рука взорвалась ливнем красной слизи, как перезрелый помидор?
Для начала важно нанести удар в нужную точку.Лучшая точка находится не только в узкой средней точке блока. Широкий удар отбрасывает много сил, так как нужно только сломать блок в одном месте, чтобы сломать его. Также важно быстро нанести удар по поверхности блока. Большинство ударов — это частично соединительный шлепок, а частично — толчок. Это наносит наибольший урон при борьбе с плотью, но помогает защитить бетон или дерево. Бетон и дерево обладают хорошим сочетанием жесткости и эластичности. Материалы будут изгибаться и даже изгибаться назад, как резинка, но пределы их пластичности намного ниже.Сгибание и резкое огибание могут нанести им больше вреда, чем вещи, которые сгибаются легче. Благодаря быстрому удару и оттягиванию ударник сильнее всего ударяет по блоку и позволяет материалу максимально изгибаться. Последующий толчок не даст материалу отломиться и защелкнуться.
Все в порядке, но редко можно увидеть, как кто-то пробивает здание пополам или выбивает трещины в тротуаре, даже если его форма идеальна. Посмотрите на картинку ниже.
Между каждой из бетонных плит небольшие перегородки. Редко можно найти разделители между слоями тротуара. Это то, что отделяет трещины от пятен. Пробить кусок бетона сложно, но пробить кусок бетона, лежащий на земле, практически невозможно. Материал должен дать трещину. То же свойство наблюдается и у более легких и гибких материалов. Держите лист бумаги за обе стороны в воздухе, и нож, приложенный к середине, прорежет его насквозь.Положите его на ровный бетонный пол, и будет намного сложнее разрезать лист бумаги тем же ножом.
Как и все остальное в жизни, ломка — это просто примитивная, выродившаяся форма изгиба. Бумага не сгибается и поэтому не поддается. Бетонный блок работает точно так же.
Так что помните, если вам необходимо пробить бетонный блок (вы не должны), убедитесь, что вы делаете это (не делайте этого) с блоком (максимум из пенополистирола), который удерживается в воздухе (кем-то, кто оторвет его, если вы сделаете что-то глупое, например, попытаетесь сломать его рукой), а не упадете на землю (как вы будете кататься взад и вперед в агонии, и это не будет моей ошибкой, черт возьми.Я тебя предупреждал).
Через Straight Dope and Discover.
Как делать бетонные блоки — производство цементных кирпичей, бетонных блоков, пустотелых цементных кирпичей, цементных кирпичей
Бетонные блоки, иногда называемые цементными кирпичами (или цементными кирпичами), широко используются в качестве строительного материала. Доступны автоматические или полуавтоматические машины для изготовления бетонных блоков, но их можно сделать на свободном доступном пространстве вашего дома. А если вы настроены серьезно, вы можете начать свой собственный бизнес по производству и продаже бетонных блоков на дому.
Найдите подходящее место **: ** Найдите широкое открытое пространство, даже лучше, если оно будет в тени, это сработает, если дождя в вашем доме не так уж и много. Пространство должно быть достаточно широким для смешивания бетона и заливки его в форму.
Сделайте форму: Используйте фанерные доски и гвозди, чтобы сделать односторонний открытый ящик с внутренней полостью 300 мм (длина) x 200 мм (ширина) x 150 мм (толщина). Это стандартный размер бетонного кирпича.
Приготовьте бетонную смесь: Возьмите большой контейнер, настолько большой, насколько вы можете разместить в своей рабочей зоне.Для приготовления бетонной смеси вам потребуются цемент, песок, гравий и вода. Насыпьте в емкость цемент, песок и гравий в соотношении 1: 2: 3. Начать смешивание воды в емкости и непрерывно перемешивать смесь палочкой. Налейте воду, пока бетонная смесь не станет достаточно податливой, чтобы ее можно было заливать в форму.
Изготовление необработанного бетонного блока: Залейте бетонную смесь в форму и перемешайте или встряхните форму так, чтобы бетон оседал в форме и достигал крайних углов.Зачерпните лишнюю бетонную смесь, используя фанерную доску с открытой стороны формы. Выровняйте открытую поверхность, проведя по ней фанерной доской.
Отверждение: Бетонный блок необходимо выдержать в форме в течение 24 часов для высыхания. Затем выньте бетонный блок из формы и поместите его в резервуар для воды для отверждения. Процесс отверждения обеспечит необходимую прочность на сжатие и займет около двух недель.
Реклама и продажа: Когда у вас будет достаточное количество бетонных блоков, вы можете разместить небольшое объявление в местной газете и создать веб-сайт, посвященный вашим услугам.
Заключение
Вы можете начать свой бизнес по производству цементного кирпича или бетонных блоков на начальном этапе, не вкладывая средства в оборудование. Вы даже можете попробовать изготовить пустотелый цементный кирпич по индивидуальному заказу, используя различные типы форм. Помните, что прочность цементного кирпича зависит от пропорции смеси и достаточного времени выдержки.
Изготовление глиняных кирпичей за 6 шагов: В этом руководстве по изготовлению глиняных кирпичей рассказывается, как сделать глиняные кирпичи за шесть шагов.
Лучший тип бетонных блоков настила
Вы, вероятно, мечтаете о том, как будете наслаждаться жизнью на вершине своей новой колоды, но сначала вам нужно подумать о том, что находится под ней — правильные бетонные блоки и опоры, которые будут поддерживать вашу колоду ровно, устойчиво и способно удерживать до любой вечеринки на открытом воздухе, которую вы устраиваете.
Если вы строите свою собственную террасу, первым делом необходимо проконсультироваться с местными строительными нормами и правилами, касающимися фундаментов террасы.Таким образом, вы будете знать, что собираете максимально безопасную колоду.
В большинстве регионов страны фундамент настила должен выходить ниже местной линии промерзания. Часто эта глубина составляет от 36 до 48 дюймов ниже уровня земли и может достигать 70 дюймов в далекой северно-центральной части страны.
Кроме того, основания настила должны быть соединены с конструкцией для предотвращения бокового смещения, вызываемого сильным ветром, землетрясениями и морозным пучком.В большинстве регионов страны это означает крепление опорных столбов к фундаменту с помощью утвержденных кодексом металлических соединителей или установку концов столбов на бетонные блоки настила, заглубленные как минимум на 12 дюймов ниже уровня земли (верхний слой почвы).
Сборные железобетонные настилы популярны для строительства настилов. Некоторые из них сделаны с выемками, предназначенными для размещения столбов, балок и балок стандартного размера.
Сборные блоки, доступные в центрах по благоустройству дома, обычно имеют квадрат 12 дюймов и высоту от 8 до 12 дюймов.Простого размещения их на земле или на залитой бетонной подушке глубиной в несколько дюймов обычно недостаточно для соблюдения правил — они должны быть установлены на глубине не менее 12 дюймов в ненарушенной почве. Однако бетонные блоки для настила можно использовать без ограничений для отдельно стоящей террасы, которая не прикреплена к вашему дому.
Некоторые блоки имеют отверстие в центре. Это позволяет вставить бетонный болт, предназначенный для крепления металлического анкера к блоку.
Сборные железобетонные блоки с выемками помогают остановить поперечное движение из стороны в сторону, но не обязательно должны быть одобрены кодексами во всех регионах страны — проконсультируйтесь с местными строительными органами, прежде чем планировать настил. В некоторых регионах страны может потребоваться использование шнековых креплений — металлических стержней, которые ввинчиваются в землю и прикрепляются к элементам каркаса палубы для предотвращения выхода столбов из сборных пазов.
Сборные опоры представляют собой длинные конические опоры фундамента, которые могут выступать ниже линии замерзания, поэтому они могут достигать нескольких футов в длину.Они удобны в использовании, потому что вам не нужно заливать фундамент (но вам все равно придется копать ямы для фундамента). И вам может понадобиться специальное оборудование для подъема сборных опор — они весят до 1000 фунтов каждая.
Хороший метод для домашнего мастера — вырыть ямы для фундамента, которые должны быть достаточно глубокими и широкими, чтобы соответствовать местным нормам. Вставьте картонные опорные трубы в отверстия, засыпьте вокруг трубы грязью, а затем заполните внутреннюю часть труб бетоном (Изображение 1).